In the American sitcom “The Office,” Dwight Shrute once revealed he doesn’t tip for services he can do himself, like cutting his own hair. He grants gratuity to his urologist, though, for Dunder Mifflin Scranton’s assistant to the regional manager is “unable to pulverize [his] own kidney stones.” If that’s how life really operated, I would always give a healthy tip to the technicians who perform brake service on my car. Because I can write story after story about brakes and explain how they work (or quote people who can), but I’ll be damned if I ever change them myself. There’s just too much at stake, as one little oversight, or under-torqued bolt, could lead to my brakes failing and my family dying. For this type of work, someone more experienced and less neurotic should be securing my wife and children’s future.
It’s a crazy but essential burden we place on maintenance providers, when you think about it. If I miss a typo (and oh, how I hav), no one is hurt. If a truck technician fails to securely tighten a trailer tire wheel-end after a blowout, the vibrations from the road may rattle the 110-lb. wheel off the spindle and send it careening down the highway. High stakes, indeed.
Read more: A fresh approach to maintenanceEven a pickup’s tire can cause catastrophic damage. A viral video in March taken by Tesla driver Anoop Khatra’s dash cam caught a 2011 Chevy Silverado’s front drive tire rocketing off its axle and directly in front of the Kia Soul passing in the left lane. The compact car drove over the tire, which through a wicked act of physics, catapulted the Kia several feet in the air. It landed on its roof, then bounced and rolled right-side up again. Luckily, the driver was a Soul survivor, sustaining only minor injuries, according to police.
The true cause has yet to be determined, but whether the cause was faulty maintenance or lack of routine maintenance, this event shows how little things, like a fatigued bearing, can create big-time crashes. It’s an extreme example, of course, but illustrates how we as a road-faring society are all connected through this maintenance circle of life. It’s a huge responsibility, and one we in the commercial vehicle industry are so used to, that it could be taken for granted. Because of this, complacency remains one of the industry’s biggest threats.
It’s fortunately the easiest for management to take on. The correct steps to fix things, of course, are meticulously defined by the OEMs and industry sources such as the Technology & Maintenance Council’s Recommended Practices. The technician has to follow those instructions, though. If they don’t learn the right way, or choose to take shortcuts, that could trigger an avalanche of apathetic quick fixes when new technicians mimic their mentors. And like a game of telephone, the message could get more and more corrupted with each new batch of hires. Before you know it, wheels are flying off every vehicle and in every direction. Morning commutes will be like playing reverse Frogger. OK, maybe not that bad, but it won’t be good.
I mentioned before that maintenance folks deserve a tip, so here’s one: Kick the tires on augmented reality tools for the shop. They have proven to boost efficiency and accuracy. For instance, Peterbilt has reported its ARTech software can save 15 to 30 minutes per electrical repair.
And the RealWear Navigator 500, a high-tech wearable computer, allows technicians unfamiliar with a repair or troubleshooting task to call a remote expert for help. This expert can see exactly what the technician sees via a 48-megapixel camera, streamed over a wireless network. The Navigator has a small monocular display from which they can reference work instructions, or view relevant files and images sent from the remote expert’s computer. Unlike a tablet, they also never have to put it down to do the actual work. Very handy and hands-free.
RealWear defines this version of AR as assisted reality. I call it a complacency killer. A savvy shop will have their most experienced technicians don the voice-controlled headset, tell it to “record,” and then correctly perform preventive maintenance or part repairs. After a while, that company has created a complete library of training videos.
Each device costs about $2,500, comparable to many diagnostic tools. If you can use it to shave off a day of downtime for a truck by finding an issue faster, you’ve likely recouped most of your money right there. As a bonus, the digital natives you want to hire out of auto and diesel schools appreciate cool gadgets like these and will be more likely to want to work for you. Just remember innovation is a natural predator of complacency.
That’s half the battle. The other part is getting drivers to recognize issues during pre-trip inspections and have an easy way to promulgate that info to the shop. Using electronic driver inspection reports can help here.
“It’s really easy to get complacent,” noted Fred Fakkema, VP of safety and compliance at Zonar Systems to FleetOwner last year. “I always tie it into my law enforcement days when you see people have an ‘Oh no’ moment because they weren’t really paying attention. And it’s the same concept when driving a truck: You get comfortable. And once you’re comfortable, you get a little complacent and then that’s when mistakes can happen. That’s when you overlook something.”
And when bad things already happened, complacency makes it worse. The trucker who fatally struck NFL player Dwayne Haskins last year is getting sued, as are his employers, due to some maintenance issues found during the investigation. I doubt this particular case will have a nuclear verdict-style ending, but tens of thousands die on U.S. roads every year, and there are plenty of chances for lawyers to bleed the life out of fleets.
We might not ever know how many accidents on the road are truly avoidable. We do know, however, that maintenance leaders can and do save lives simply by ensuring things are done the right way on every vehicle, and striving to improve more tomorrow. It’s a tough job, but I trust you are all up to the challenge.
About the Author
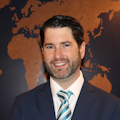
John Hitch
Editor-in-chief, Fleet Maintenance
John Hitch is the award-winning editor-in-chief of Fleet Maintenance, where his mission is to provide maintenance leaders and technicians with the the latest information on tools, strategies, and best practices to keep their fleets' commercial vehicles moving.
He is based out of Cleveland, Ohio, and has worked in the B2B journalism space for more than a decade. Hitch was previously senior editor for FleetOwner and before that was technology editor for IndustryWeek and and managing editor of New Equipment Digest.
Hitch graduated from Kent State University and was editor of the student magazine The Burr in 2009.
The former sonar technician served honorably aboard the fast-attack submarine USS Oklahoma City (SSN-723), where he participated in counter-drug ops, an under-ice expedition, and other missions he's not allowed to talk about for several more decades.