As I get more entrenched in managerial duties, I’m starting to realize there’s more to planning than I previously thought. For example, do you know you have to plan time to even be able to plan? This probably comes naturally to all those perfectly organized enigmas who use color-coded binders and always know what day of the week it is. But for those of us who skew reactionary, people who attack problems as they come, planning ain’t easy.
Being proactive, though, is necessary for any manager, whether they edit a magazine or run a busy commercial vehicle repair shop. And this is likely more difficult—and important—for shop managers, as an editor’s job has always been: write, read, edit, repeat. In a modern service facility, the job and tools are always changing, getting more advanced, more technical. Simple body work now includes re- calibrating the ADAS cameras. A routine tire changeout might also now include installing and programming tire pressure monitoring system sensors as well. And if you think diagnosing electrical issues is a pain point now, wait until electric vehicles need service. Understanding those complexities takes a lot of training and a lot of planning.
You might think it’s easier to ignore all the newfangled tech and focus on the job at hand, but when all of these components become universally adopted and your team isn’t prepared, you might have to plan for a change of employment.
Now disaster planning is an area I am well versed in. Back in my old submarine days, that’s all we did. Nearly every day at sea, we’d pretend the reactor was melting down, or another sub was shooting a torpedo at us, or both at the same time. I used to think it was an exercise in sadism on the part of the officers, but now I realize it was so we’d have the muscle memory to handle business if something like that did go down. Shops also need to excel at disaster planning, like when when a barrel of engine oil spills over.
That piece coincidentally reminds me that you can’t plan for everything, like when a lube pump erupted hydraulic fluid all over the engine room once, shortly after diving. A few handpicked off-watch sailors including myself spent six hours sopping up the viscous mess with chem wipes, the Navy’s reinforced version of paper towels. I would’ve loved to have an actual spill kit, or at least a shop vac. Having the right tools to make jobs easier is far more important for shops than subs, because diesel technicians can leave the job without fear of the bends or sharks.
For shop managers, the technician shortage might actually be a more fearsome threat. Will that newly onboarded tech stick around, or will they depart for an easier job? Hobby Lobby recently raised its starting pay to $18.50 for full-time employees. The median pay for a diesel technician is a little over a dollar more, according to the U.S. Bureau of Labor Statistics.
Fleets and shops are starting to plan for the future via outreach programs at high schools and community colleges. That’s a great start, but probably futile if you’re not stocking the right tools to make PMs and repairs more efficient. These workers value fixing problems as best as possible, not just a paycheck.
We recently profiled a Dickinson Fleet Services technician named Josh Lawhorn, who said, “As much as I hate wasting a customer’s money, I really hate wasting their time.” Plan accordingly to keep folks like this.
Predictive maintenance might just be the digital tool to ensure smooth operations. Just as diagnostics tell you what’s wrong now, prognostics use historical data and algorithms to forecast what could go wrong. This allows shops to get ahead of catastrophic failures. Pitstop’s maintenance platform cut downtime by an average of 20% annually, time that can now be spent training on all that new technology. Noregon’s remote diagnostics tool TripVision Uptime is another good example, and will be a big part of the company’s future strategy. Scott Bolt, Noregon VP of product management (and fellow sub vet), explained that while the industry is now in a “fix-it-because-it’s-broke phase,” Noregon’s roadmap calls for predicting breakdowns and fixing them so they don’t break.
Sandeep Kar, Noregon’s newly appointed chief strategy officer, teased that even this isn’t the endgame: “The future is going to be prescriptive in nature, where you can prescribe a certain business outcome. That is where the real value lies.
“Through effective analysis of vehicle operation and service/maintenance data,” Kar continued, “optimal RPM ranges can be prescribed to fleets for delivering higher powertrain efficiency and safety, as well as lower TCO and environmental footprint.”
That’s a lot, and might even tempt some fleets to downgrade the role of the shop manager. To avoid obsolescence, maybe the plan should be to show where your real value lies: that’s likely more in predicting what your employees and customers want and need, not what some machine wants.
About the Author
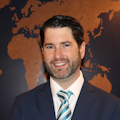
John Hitch
Editor-in-chief, Fleet Maintenance
John Hitch is the award-winning editor-in-chief of Fleet Maintenance, where his mission is to provide maintenance leaders and technicians with the the latest information on tools, strategies, and best practices to keep their fleets' commercial vehicles moving.
He is based out of Cleveland, Ohio, and has worked in the B2B journalism space for more than a decade. Hitch was previously senior editor for FleetOwner and before that was technology editor for IndustryWeek and and managing editor of New Equipment Digest.
Hitch graduated from Kent State University and was editor of the student magazine The Burr in 2009.
The former sonar technician served honorably aboard the fast-attack submarine USS Oklahoma City (SSN-723), where he participated in counter-drug ops, an under-ice expedition, and other missions he's not allowed to talk about for several more decades.