Manufacturers of axles and other drivetrain components are making a bigger push into the electric vehicle (EV) market, and we’re not just talking about passenger vehicles anymore. From medium duty trucks all the way through Class 8, electrification can help fleets lower both emissions and operating costs – without adding complexity for drivers or technicians.
“Dana has been working on electrification for quite a while now,” says Harry Trost, senior manager of product planning for Dana’s Commercial Vehicle Group, a leading drivetrain and propulsion systems provider. The company put its first electric axle into production a little over a year ago in China, resulting from a joint venture with Dongfeng Dana Axle Co., Ltd. That factory is capable of producing 800,000 electric axles per year.
China is a great example of how a market for electrification can quickly evolve. According to Trost, the Chinese market started with the easiest way to integrate an electric propulsion system into a vehicle: a central-mount, direct-drive solution where a motor is connected to a traditional driveshaft and axle. Roughly 95 percent of the Chinese market continues to rely on that solution. However, the technology is evolving toward a more efficient, lighter-weight and lower-cost electric axle that is part of an integrated system.
Dana’s recent acquisition of controlling interest in TM4 Inc. gives Dana the capability of producing all core components of a fully integrated electric drive system:
- Electrified drivetrain components (including electric axles, which Dana refers to as e-Axles)
- Motors, power inverters, and controls components
- Thermal management components
In addition to TM4, Dana has acquired SME Group, a manufacturer of lower-voltage motors for accessory drive applications. Dana has also acquired Oerlikon Drive Systems, which gives Dana additional competency in precision helical gearing and planetary gearing, as well as transmissions.
“Many of these e-Axles will also incorporate multi-speed transmission approaches,” Trost says.
Speaking of transmissions, some major news broke in April when it was announced that Allison Transmission was acquiring the Electric Vehicle Systems division of AxleTech. Allison Transmission is a leading manufacturer of automatic transmissions for medium and heavy duty commercial vehicles, as well as hybrid propulsion systems for city buses. AxleTech’s CEO, Bill Gryzenia, says the integrated electrification solutions AxleTech has developed can now enter a new phase of development and commercialization with Allison Transmission.
“Allison recognized the benefit of these electric axle products by way of the space between the wheels for batteries and other system components, and believes this is a true differentiator,” says Mike Foster, chief technology officer for Allison Transmission. “We look forward to being a part of the big opportunity for the electrification of medium and heavy duty fleet vehicles. An OEM’s needs are based on weight and application, so central drive units, electric axles, or a combination of the two will be able to support the needs of many fleets.”
Another example of an integrated electric axle comes from Meritor, a supplier of drivetrain, mobility, braking, and aftermarket solutions for the commercial and industrial markets. The company is marketing its eAxle Integrated Electric Drivetrain under its Blue Horizon brand. The system comprises:
- Power Control & Accessory Subsystem (PCAS) – the brains of the operation that links all drive system components together
- Motor Drive System (MDS) – consists of an electric motor(s), automated manual transmission, EV-optimized drive axle and brakes, and shifting software
- Energy Storage System (ESS) – Nickel Manganese Cobalt (NMC) battery pack and battery management system packaged in a modular design
Meritor made news itself this spring when the company announced it would be supplying the Port of Long Beach and the Port of Oakland with electric drivetrain systems for 38 terminal trucks. T.J. Reed, Meritor’s vice president of front drivetrain and electrification, says the contract validates Meritor’s position as a leader in electric drivetrains as the company works toward the commercialization of battery-electric vehicles.
A startup company that is capitalizing on integrated electric axle technology is Hyliion. The company’s name is derived from its flagship product, a hybrid lithium-ion solution called the 6X4HE System. This system allows fleets to hybridize any Class 8 truck from any manufacturer. Featuring a modular design for easier installation and servicing, the 6X4HE System includes:
- Battery pack
- Control unit
- Thermal management system
- Electric axle
- Co-pilot display
- Aerodynamics
“We’ve been in development for a little over three years now,” says Thomas Healy, founder and CEO of Hyliion. “Over the past six months or so, we’ve begun shipping revenuable units to fleets. We had some beta test units with some fleets prior to that.”
Dana has been supplying Hyliion with conventional axles (the S23190) for use in the Hyliion system. Hyliion then acts as the total system integrator and software provider. But what started out as a routine buyer-seller relationship has blossomed into more. Dana has become the lead investor in Hyliion’s most recent round of financing.
“We’ve now been able to cement an even stronger relationship so we can partner on whatever future technologies exist with respect to the electric axle, motors, inverters, and other electric components,” Healy says.
In addition to Hyliion’s hybrid solution, Dana manufactures e-Axles for fully electric vehicles. Dana is currently working with leading truck manufacturers on future projects to incorporate Dana e-Axles into their own electric and hybrid solutions.
If you'd like more information and articles like this in your inbox, subscribe to the Fleet Maintenance Today newsletter.
Do electric axles make sense for fleets?
When a vehicle goes fully electric, it consumes zero fuel and produces zero emissions. Even when moving to a hybrid solution such as Hyliion’s, fleets can realize significant environmental and cost savings. Dana provides a Total Cost of Ownership Calculator to help fleets understand the financial benefits of electrification. Fleets can check it out at apps.dana.com/commercial-vehicles/tco/.
Dana’s Trost says fleets can also enjoy efficiency gains as a result of an electric axle configuration.
“On the classic Class 8 tractor-trailer, there is a 6x4 drive axle, meaning that both rear axles are driving with a connecting interaxle driveshaft,” Trost explains. “With an electric vehicle, an OEM can now use Dana’s S175 high-efficiency drive axle that supports 6x2. Instead of having a rear axle that is a non-powered tag axle, Dana’s new eS6200r e-Axle can be installed to provide the efficiency of a 6x2 with 6x4 tractive effort. This e-Axle fits into existing suspensions in the marketplace.”
Integrated electric axles can offer additional benefits for fleets. “One limitation with a conventional drive axle is that you can probably go up to the low 7:1 ratio, and then you can’t incorporate much more high-numerical gearing,” Trost points out. “With an integrated approach, you have more flexibility on ratio choices, which leads to the benefit of being able to select a more optimized motor and inverter for an integrated approach. So improved efficiency is an immediate benefit. Then, because of the smaller motor, there is the benefit of reduced weight.”
For fleets that still are a little skittish about relying solely on battery power, Hyliion’s Healy says hybridization is a good option – especially for long-haul trucks.
“For Class 8 long-haul trucking, you’re putting tremendous amounts of miles on every year,” Healy says. “With a passenger car, you’re typically making a 30-mile commute to work every day, and then parking in the garage and recharging every night. So full electrification is catching on more in the passenger vehicle industry. That said, we think it will still be quite a while before Class 8 trucks can go fully electric.”
In the meantime, the hybrid approach can make a lot of sense. According to Healy, an electric axle in a hybrid vehicle can help a fleet save 5 to 10 percent on fuel in rolling terrain areas, and 10 to 15 percent in more hilly areas. When a truck reaches an uphill climb, the electric axle kicks in and helps relieve some of the load placed on the engine. Then, when travelling downhill, that same axle can use regenerative braking to charge the battery pack. As a result, the truck never has to be plugged in to recharge, which is a big efficiency and convenience gain for fleets.
With an electric axle, electric power from the truck is transferred to a battery bank, control box, and cooler, and then to the rear axle with an integrated motor. Hyliion’s Healy says it is difficult to put a drive system on a steer axle, so the Hyliion system is not designed for that right now. Instead, it focuses on the two rear axles of the tractor.
Since the Hyliion system is a hybrid system, the truck still needs diesel power. Thus, a driveshaft is still needed to run from the transmission to the front axle. However, that is where the driveshaft stops. The electric axle is completely independent and located at the rear. Fleets must also mount a battery box, cooling system, and controls box to the frame of the truck.
“All of these components connect together and work in unison,” Healy says with respect to the Hyliion system. “When the truck accelerates, we are passively reading the CAN bus of the truck so we know how hard the engine is working and how much fuel is being consumed. We also have our own algorithm with our software that is analyzing the data coming off of the truck. Our system then determines when it is appropriate to kick in and supplement what the engine is already doing.”
A side benefit of the Hyliion hybrid system is that a driver can use the unit that cools the system batteries to function as an auxiliary power unit (APU) when the driver is sleeping in a rest area. That could potentially spare a fleet the need to invest in a separate APU.
In addition to long-haul, Trost says there are many other fleet applications where an integrated electric axle can be beneficial – from Class 4 all the way through the variants of Class 8. Dana is developing a full lineup of e-Axles for 6- to 12-meter buses, as well as medium duty vehicles such as city delivery vehicles, incorporating Dana’s eS9000r e-Axle for Class 4, 5, and 6. An e-Axle like the one put in the Hyliion solution can be leveraged for Classes 6 and 7. Dana is also developing a solution for Class 8 for severe-duty applications like refuse vehicles.
In other words, fleets of all shapes and sizes could see more electrification in coming years – perhaps sooner than later.
Maintenance made easier
Hyliion’s Healy says the nice thing with electric systems is that wear and tear is limited. There are no pistons or cylinders. There is an electric motor that spins, but then just a battery pack behind it.
“You just drive until the batteries run out of life,” Healy says. Any battery pack has a pre-determined life. Hyliion is using one of the more advanced on the market, generally providing a seven- to nine-year life.
“Very little maintenance is required beyond that,” Healy adds. “On the Hyliion system, you do need to swap out the ATF (automatic transmission fluid) in the motor once a year. Also, be sure to top off the antifreeze as needed.”
Dana’s Trost says most motors and inverters are relatively maintenance-free. “Some have bearings that are greased and are literally lubed for life,” he points out. “Some solutions in the market have oil-cooled motors, so fleets could see sharing of oil as well as lubricants for gears and bearings. Many solutions have traditional oil change maintenance procedures. One new thing to periodically check are the electrical cables to make sure everything is staying tight. Still, it’s a significant overall decrease in the amount of maintenance needed.”
An electrified drivetrain could dramatically change the industry, and that change has taken a big step forward in recent months. The benefits for a fleet are plenty, from reduced weight and fuel consumption to simplified maintenance and reduced emissions. As the technology evolves and more OEMs begin to adopt these types of integrated electric solutions, even bigger changes could be on the horizon.
“We expect that vehicles themselves are likely to change,” Trost says. “An electric axle opens up new possibilities with respect to vehicle design architectures. For example, maybe a delivery van would like to have a lower floor. Now you don’t have to restrain the vehicle architecture to the traditional frame rails or the traditional extended-nose cab. There are a lot of new possibilities that probably haven’t even been thought about yet – possibilities that these new integrated electric powertrains are going to enable.”
If you'd like more information and articles like this in your inbox, subscribe to the Fleet Maintenance Today newsletter.
About the Author
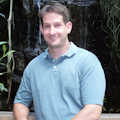
Gregg Wartgow
Gregg Wartgow is a freelancer who Fleet Maintenance has relied upon for many years, writing about virtually any trucking topic. He lives in Brodhead, Wisconsin.