Maintenance strategies for commercial vehicle lighting
It’s long been established that lighting issues on commercial vehicles such as tractor-trailers are the cause of many violations and fines, not to mention a large portion of fleet maintenance expenses. According to Federal Motor Carrier Safety Administration Analysis & Information data, some of the most common roadside inspection violations in 2021 were related to not having required operable lamps, inoperative turn signals, and defective lighting devices.
One year earlier, during the 2020 International Roadcheck event, the Commercial Vehicle Safety Alliance’s (CVSA) annual high-volume, high-visibility inspection and enforcement initiative, out-of-service lighting issues in the U.S., Canada, and Mexico accounted for almost half of the overall violations.
Each year, CVSA highlights categories of violations during International Roadcheck to bring awareness to certain aspects of a routine roadside inspection, and in 2021 results on more than 40,000 commercial motor vehicle inspections painted a similar picture.
Last year, CVSA inspectors found 1,367 lighting issues, accounting for 14.1% of all vehicle out-of-service violations. The lighting violations, which ranked third after brake systems and tires, included headlamps, tail lamps, stop lamps, turn signals, and lamps on projecting loads.
To help fleet maintenance operations address this costly challenge, Fleet Maintenance assembled a panel of subject-matter experts from leading lighting manufacturers to discuss challenges on tractors and trailers, and the latest equipment trends to overcome them.
These experts also weighed in on how telematics technology helps detect broken and nonfunctioning lights. Finally, the group provided advice on ways that fleet maintenance operations can improve their lighting maintenance strategies.
Fleet Maintenance: What are the lighting challenges on tractor-trailers and the latest equipment trends to help address them?
Paul Sniegocki, Clarience: The environment is always demanding. Trucks and drivers face any and every condition, meaning their lights must stand up to just about anything; and so, robust designs and manufacturing methods can help overcome this.
Additionally, as we move to electric vehicles, customers are looking for low current draw. With Clarience Technologies’ A2Z for eMobility initiative, our team of companies is addressing this concern by developing low amp draw lighting solutions and adaptive response technologies.
Kyle O’Dell, Optronics: Rising cost is the biggest challenge that tractor and trailer owners are facing currently. This has caused fleets to take a more serious look at total ownership costs of lighting systems. The entire industry has embraced the conversion from incandescent to LED lighting because of all the LED systems’ advantages.
Drawing less power allows wire gauges to be reduced, and with copper prices almost doubling from a year ago, this helps offset the higher initial costs of LED lights. LED lights that are fully sealed and electronics with the latest SMD (surface mount diodes) can offer a lifetime of trouble-free service, which reduces downtime and service costs.
Mark Blackford, Grote: Traditionally, a major lighting challenge is the demanding environment in which commercial vehicles operate. On the road, vehicle lighting and wiring are frequently exposed to shock, vibration, corrosive chemicals, moisture, temperature extremes, and road hazards. In addition to these ever-present dangers, equipment availability has recently become a more critical concern for fleets, making downtime for maintenance or repairs more costly than ever.
The best solution is to ensure that tractors and trailers are outfitted with premium LED lights and harnesses that are designed to operate as a system. This will minimize downtime and allow a fleet to field road-ready equipment that can easily stand up to the challenges of the highway.
Kevin Koyle, TecNiq: If properly engineered, an LED light will outlast the life of the vehicle, so the focus needs to be on areas of concern like corrosion at the connection and physical damage. Using a properly sealed connector, made from the correct material, will reduce corrosion issues and lead to less failures on the road. Using quality components meant for harsh environments leads to less failures for both lights and grommets.
Lights and components engineered for the environments that tractors and trailers are used in should last the lifespan of the vehicle without any issues and help avoid any DOT violation fees. Although lights look the same, there are differences in construction that improve the quality of the components. Thermal management, proper high-quality circuit boards, precise sonic welds, and proper gasket material will all lead to lower fleet costs.
Al Anderson, Peterson Manufacturing: Corrosion is the number one reason trailer wiring harness and lighting systems fail and need to be replaced. Lights are always one of the top three CSA violations. Unplanned troubleshooting and replacement increase costs along with the associated unscheduled downtime, having an impact on every part of the fleet.
We designed our Defender and PetersonPATRIOT modular harness systems to provide a very strong defense against moisture intrusion and corrosion in trailers with a modular layout. These systems have a distribution module that connects all the lighting components to a small-footprint central hub. Additionally, an integrated moisture barrier feature of the wiring harnesses provides excellent corrosion resistance. The modular design of both systems allows efficient troubleshooting and repair, and easy installation when needed.
FM: How does telematics technology come into play to help detect broken or nonfunctioning lights?
Cliff Creech, Phillips Connect: Lights are the most frequently repaired item on a trailer, but when nonfunctioning, they can put your driver and fleet at risk for a CSA violation or even an accident on the road. Through telematics, the driver or fleet manager will receive an alert if a tail light is inoperative.
Our system, the Phillips Connect Lite Sentry, monitors resistance; if a light is broken, the resistance changes. We take it a step further by not just telling you the light is broken, but by pre-checking the light circuits on a parked trailer, indicating whether the light is broken before the driver dispatches. This gives the fleet the opportunity to safely replace the faulty light and eliminate unnecessary downtime.
Anderson: By alerting the driver and the fleet maintenance department to a nonfunctioning light, repairs can be made proactively. That limits costly over-the-road repairs, eliminates violations that might be found during CVSA inspections, and helps to keep a fleet’s equipment operating safely.
Koyle: Often when a light is out, the light is what gets blamed. Telematics can determine if there is another issue that is playing a role in that circuit. Being able to monitor each circuit and reference the data may show an issue with the wire or connector, as well as if there are electrical surges or ground issues causing the premature light failure. Being able to reference the data, in real time or recorded, can provide more detail into the problem than just a nonfunctioning light can.
Blackford: Outage detection systems, such as Grote Guardian, can detect light outages, short circuits, missing lamps, and even intermittent connections, and interface with a telematics system to communicate that information to the driver or the fleet maintenance office. This can greatly increase the efficiency of repair work and help minimize downtime and the risk of CSA violation exposure. In the near future, as technology advances and the utilization of telematics data develops, we envision detection systems with the ability to predict, not just report, lighting failures, leading to even greater safety, efficiency, and savings.
Sniegocki: Telematics technology enables connectivity of information and data. For example, our Road Ready Light-Out Detection System provides awareness to the back office. With its newest feature, Virtual Tether, information such as this can be communicated to the driver for proactive action. The system connects to the J-560 port and provides instantaneous data to the driver via edge computing.
O’Dell: The telematics technologies that are being incorporated into trucks and trailers aid in detecting issues with lights and wiring but still cannot fully replace an operator walkaround. With small 3/4” marker clearance LED lights drawing less than 0.05 amps, it is extremely hard for even the most advanced system to detect if one of these lights fails, so there is no substitute for the maintenance department performing routine inspections and for operators to perform daily walkarounds to inspect the lighting.
FM: How can fleets improve their lighting maintenance strategies?
Anderson: There are several things a fleet can do to ensure a good lighting system maintenance strategy. When spec’ing new equipment, be sure to ask the manufacturer to use the most moisture- and chemical-resistant connectors available on both the wiring harness and lighting components. Peterson believes that AMP-style connectors provide the best moisture exclusion available.
Be sure drivers do thorough pre- and post-trip inspections and report any problems to the maintenance department for attention. On 7-way trailer cords and J-560 connections, be sure the cord fits securely into both the tractor and trailer connection points. Also, be sure both connection points are free from corrosion and that the 7-way cord itself isn’t damaged or worn.
Train technicians not to use test light probes to check for current in a wiring harness when troubleshooting. The slightest intrusion into a wiring harness will allow moisture and corrosive chemicals to get into the insulation and cause almost immediate problems. And be sure to use a high-quality dielectric grease on connections where appropriate.
Connections should not be disconnected unless repair or replacement is required; there is no periodic PM needed. A light’s functionality can be determined by bench testing the light from a power source of the proper voltage or by replacing the light with a known-good unit. When working with LumenX lights, do not grease the silicon-sealed connectors. Greasing the terminals will prevent the silicone seal from seating properly and will lead to undo corrosion. Apply dielectric grease to 0.180 bullet connectors anytime they are disconnected or replaced.
Sniegocki: Choosing the light with the most robust design ensures your light has a long lifetime and can operate in any conditions. Additionally, using a light-out detection system enables maintenance departments to increase uptime. In most cases, problems and potential maintenance can be identified before they become major issues.
Ron Fay, Phillips Industries: Lighting maintenance strategies are not just about maintaining the lights alone. Lights need power to operate. When a light fails, it might not be because the light itself is bad; it often is due to corrosion in the electrical system, which is highly susceptible to corrosion.
Routine PMs should be performed every six months, or more frequently in highly corrosive environments, using a plug and socket brush with electrical cleaner to clean 7-way connectors at the front of the trailer. After every cleaning, reapply dielectric grease on the plug and socket pins to keep corrosion at bay.
When a faulty light needs to be replaced, clean the contacts on the pigtail with an electrical cleaner and use a blowgun to clear residual cleaner and old grease before installing a new light. When a lighting failure happens and it’s not the light, always start where the symptom first appears (for example, at the connection at the back of the lamp). Then move toward the front of the trailer with continuity or voltage drop testing along the electrical system to diagnose where the problem could be.
O’Dell: Coming out of the winter months, fleets should perform a thorough inspection of the lighting systems on their trailers. Throughout the winter months, drastic temperature changes, snow and ice buildup, and salt and chemicals used to treat roadways can cause connection points to fail. Roads treated with sand and salt can also cause physical damage to the face of lights that need to be checked for cracks and chips that can be potential moisture leak paths into sealed lamps. The chemicals being used to pretreat roadways today are particularly corrosive to copper wiring and unsealed connection points.
Maintenance departments should pay particular attention to these areas, as the warmer months will speed the rate of corrosion. If a connector is not fully seated, it should be fully disconnected, inspected for any corrosion, cleaned, and repacked with dielectric grease before reseating.
Blackford: Routine inspections by technicians trained to diagnose wiring and lighting issues can have an outsized impact on the amount of downtime a rig undergoes. Fleet maintenance departments can also make use of the failure data from telematics systems to help identify problem areas and take corrective or preventive steps.
Ultimately, a successful lighting maintenance strategy starts with the installation of a quality, branded lighting and harness system utilizing uniform terminations on all new equipment.
A robust system of premium, matching lighting and harnesses will require little or no maintenance and invariably cost less than systems that require routine maintenance and downtime.
Panelists
- Al Anderson, VP of sales and marketing, Peterson Manufacturing, is a recipient of the TMC Recognized Associate and Silver Spark Plug Awards, which recognize professional excellence in commercial vehicle maintenance.
- Mark Blackford, director of national fleet sales, Grote Industries, has over 35 years of experience in the heavy-duty vehicle industry and specializes in aftermarket consolidation and OE specification to maximize safety and profits.
- Cliff Creech, director of sales engineering, Phillips Connect, has 20 years of experience in fleet maintenance and evaluates new sensor solutions and helps design telematics solutions.
- Ron Fay, technical support specialist, Phillips Industries, has over four decades spent in the heavy-duty trucking commercial vehicle industry with varying positions in maintenance and product management.
- Kevin Koyle, technical sales director, TecNiq, has worked in the LED lighting sector since 2007. He is a graduate of Western Michigan University.
- Kyle O’Dell, director of engineering and product development at Optronics International, directs the new product development group and oversees the company’s FMVSS 108 compliance testing program.
- Paul Sniegocki, CTO and EVP for Clarience Technologies, joined Truck-Lite in 1992 and has served as VP of R&D, director of engineering, and in several other roles.
About the Author
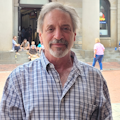
Seth Skydel
Seth Skydel, a veteran industry editor, has more than 36 years of experience in fleet management, trucking, and transportation and logistics publications. Today, in editorial and marketing roles, he writes about fleet, service, and transportation management, vehicle and information technology, and industry trends and issues.