How to maintain compliance with federal reduced stopping distance requirements
In August 2013, the National Highway Traffic Safety Administration (NHTSA) completed implementation of its reduced stopping distance (RSD) mandate for over-the-road Class 8 tractors. The amended Federal Motor Vehicle Safety Standard (FMVSS) 121 required a 30-percent reduction in stopping distance compared to the current standard.
That meant these vehicles had to stop from a speed of 60 mph in not more than 250’ when loaded to their gross vehicle weight rating. They were also required to stop within 235’ when loaded to their lightly loaded vehicle weight.
The purpose of the changes, NTHSA explained at the time, was to improve highway safety by reducing the number of fatalities and injuries associated with crashes involving tractor trailer combinations and other vehicles. Moreover, it anticipated the new standard would “prevent a substantial amount of property damage through averting or lessening the severity of crashes involving these vehicles.”
HEAT
During an emergency stop, heat is generated by the friction material contacting the brake drum faster than this heat can be dissipated into the drum and finally the atmosphere.
“This heat causes two types of brake fade,” explains Frank Gilboy, product manager, remanufactured wheel end products, Bendix Commercial Vehicle Systems. “First, the friction releases gases that interrupt the friction contact on the drum surface, reducing the available stopping force. Second, the drum expands as it rises in temperature, moving the braking surface away from the friction.”
Bendix (www.bendix.com) develops and supplies leading-edge active safety technologies, energy management solutions and air brake charging and control systems and components for medium and heavy duty trucks, tractors, trailers, buses and other commercial vehicles throughout North America.
The friction material and brake drum must have the capability of withstanding the heat until dissipated.
AIR DISC BRAKES
As a consequence of the RSD mandate, changes needed to be made to the braking systems on Class 8 tractors. One change was the increased use of disc brakes. Today’s air disc brakes (ADB) offer a shorter stopping distance than other brake designs.
However, RSD drum brakes “have significantly narrowed the gap to air disc brakes,” notes Joe Kay, director of engineering, brakes, North America, Meritor. The company’s data shows that during FMVSS 121 testing, drum brakes exceeded the stopping distance requirements by an additional 10 percent, stopping at 225’.
Meritor (www.meritor.com) is a leading global supplier of drivetrain, mobility, braking and aftermarket solutions for commercial vehicle and industrial markets.
“The difference in stopping distance between an all ADB RSD tractor and an all drum brake equipped RSD tractor is less than 10 feet,” adds Thomas E. Rogers, senior application engineer - commercial vehicle friction, Federal-Mogul Motorparts - Braking.
Federal-Mogul Motorparts (http://aftermarket.federalmogul.com) is a leading global automotive supplier offering a broad portfolio of products, brands and solutions to the automotive aftermarket, and serves OEMs with braking, chassis, wipers and other vehicle components.
SOME ADVANTAGES
ADB manufacturers say ADB have improved brake responsiveness and “drivability.”
“We’ve heard time and again from drivers who have come to prefer the passenger car-like feel and consistently straight, stable stops of ADB compared with drums,” says Bendix’s Gilboy.
ADB also provide better wear and virtually no brake fade for greater stability and capacity during stops, he adds.
Brake fade is a characteristic in which braking torque is reduced as temperature increases. Fade can be a concern where high brake temperatures are experienced, such as when heavy duty trucks are operating in mountainous regions, carrying heavy loads and are frequently using the brakes, as in city traffic.
ADB eliminated the fade created by an expanding drum, Gilboy says, but the friction is still subject to the same off-gassing seen in drum brakes, so higher-quality friction is still required.
There is also less labor and maintenance involved with ABD, say the manufacturers, which means maintenance costs and vehicle downtime can be reduced.
For one thing, ADB have fewer parts than drum brakes.
For another, there are longer service intervals because with disc brakes, brake pads normally last twice as long as drum linings and it takes less than half the time to perform lining change compared to drum brake, says Brent Fitch, director of fleet and trailer sales, WABCO North America.
WABCO (www.wabco-auto.com) is a leading global supplier of technologies and control systems for the safety and efficiency of commercial vehicles.
“Pad changes are much quicker and easier, typically taking about 15 minutes once the wheel is off, as compared to 60 minutes for a drum brake,” Gilboy of Bendix adds. “Uptime is also increased through longer life cycles and the lack of a need for regular lubrication.”
However, “if rotor replacement is involved, the situation is reversed,” points out Federal-Mogul Motorparts’ Rogers. “It takes less time to change shoes and drums than it does to replace pads and rotors.”
“If the rotor is in need of change, then the effort becomes much more significant as the hub must be removed,” adds Meritor’s Kay. This involves more costly parts and increased time for service.
FRICTION MATERIAL
At the same time, to meet the RSD standards, brake manufacturers designed upgraded foundation drum brake systems, including larger brakes and complementary friction material. In addition to meeting the stopping distance requirements, these new systems also perform better than their predecessors, with significantly less fade, due to a superior ability to handle high temperatures while maintaining torque.
These benefits, the manufacturers point out, extend to the OEM replacement linings designed for RSD-compliant braking systems. Prior generation OE and many aftermarket brake linings are not engineered to the RDS standards.
Interestingly, there is no federal mandate for RSD compliance after the purchase of a new vehicle. Once the tractor is placed into service, the owner can replace the brakes with non-RSD brake lining.
However, brake manufacturers strongly advise against this practice, stresses Dennis Griffin, product manager, CV friction, Federal-Mogul Motorparts - Braking.
Relining with non-RSD compliant aftermarket friction can reduce a vehicle’s stopping distance performance, leading to longer stopping distances and potentially compromising safety.
The issue, he says, is to maintain like new RSD stopping power (under 250 feet). This performance can be achieved with the OE brake lining that came on the tractor new, and also with certain aftermarket RSD brake linings.
RSD friction can be purchased through the OE, the brake manufacturer or from OE friction suppliers, says John Thompson, sales manager, CV, NAFTA, TMD Friction (www.tmdfriction.us), one of the world's leading manufacturers of brake friction materials for the automotive and brake industries.
To avoid such problems, brake manufacturers emphasize the importance of replacing brake friction material with the same friction originally spec’d on the vehicle and ensuring that the replacement friction is properly developed under the newly established performance guidelines.
This is the only way truck operators can maintain the same high level of safety mandated by the RSD standards on stopping performance, brake manufacturers say.
CERTIFICATION
“Vehicle manufacturers certify their vehicles by conducting FMVSS 121 vehicle stopping distance testing,” Federal-Mogul’s Rogers says. “However, vehicle manufacturers are not the only ones conducting such testing. Brake manufacturers and quality friction material suppliers similarly conduct vehicle stopping distance testing to demonstrate that their RSD solutions do meet RSD requirements.”
“For a friction material to be certified RSD compliant, it must not only be dynamometer certified to FMVSS 121 standards, it must also pass a more demanding vehicle test,” Gilboy of Bendix notes. “This means that official certification of RSD compliance comes only as part of an OE truck build or approval by a certified third-party vehicle test provider.
“We strongly advise customers to ask for evidence of compliance from their friction supplier when choosing friction for an RSD-equipped vehicle.”
Furthermore, brake manufacturers recommend that both wheels of a single axle be relined at the same time and to always install the same type of linings and drums on both wheels of an axle.
To eliminate any doubts about appropriate friction selection, TMD Friction’s Thompson says it is always best to consult with your brake supplier or an OE-certified lining supplier.
ENVIRONMENTAL ISSUES
Brake friction can consist of a highly-filled organic or semi-metallic material with formulations of 20 to 30 different materials, each with different functions. Whenever a driver applies the brakes, a small amount of brake wear – which includes copper and other metals – is released into the environment and deposited onto roadways.
This material can wash into waterways, negatively impacting them and adversely affecting aquatic life.
Both Washington and California now have laws that restrict the amount of certain constituents present in brake linings for on-highway vehicles. The objective is to reduce the impacts of brake friction materials to the environment and to technicians.
Washington was first, when in early 2010, it passed the Better Brakes Law. This legislation bans the use of asbestos, lead, cadmium, mercury, chromium and other heavy metals, plus provides for a phase-out for copper.
California’s legislation became law in September 2010.
COPPER
The two laws will effectively prohibit the manufacturing of brake pads using more than 0.5 percent copper by 2025, says Thompson of TMD Friction.
Other states are considering their own laws regulating copper and other substances in brake pads.
Copper is a key ingredient in brake pad formulations for several reasons, explain friction manufacturers. Among them: copper makes for a smooth braking experience, it transfers heat efficiently, it helps brakes' effectiveness in cold weather, and it has properties that help prevent brakes from squeaking and shuddering when used.
In some cases, copper makes up 5 to 20 percent of the mass used in friction materials.
As of Jan. 1, 2014, in California, brake pads that have more than 0.1 percent by weight of asbestiform, cadmium, chromium, lead and mercury may not be sold.
With both the Washington and California laws, copper must be limited to less than 5 percent by weight by 2021 and no more than 0.5 percent by 2025 in California.
The 0.5 percent rule may take effect as early as 2023 in Washington State, Thompson says.
Rather than wait for these deadlines, many brake friction manufacturers, to comply with environmental legislation without compromising brake pad performance, have been developing new formulations and selecting alternatives that pose less potential hazard to public health and the environment.
About the Author
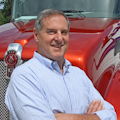