Brake check-in: Latest update on commercial vehicle braking systems
If there’s one thing on commercial vehicles that operations and maintenance professionals need to understand, it’s braking systems. Not getting a truck to start rolling on time will cause delayed deliveries and missed work. Not getting it to stop will cause all that and a whole lot more, including property damage, injuries, and even death. Improper brake maintenance also will leave fleets and shops vulnerable to “nuclear” verdicts.
The good news is that fleets that keep up to date with the latest braking technology, as well as related preventive maintenance and inspections, shouldn’t lose any sleep over brake issues. And to ensure your rest, we’ve put together a comprehensive look at the current brakes on the market, along with some tips on how to avoid downtime caused by out-of-service violations and prevent or mitigate collisions.
Before getting into that, let’s revisit the proper braking standards for stopping. As a key element of safety, commercial vehicle stopping distances are codified in law. Specifically, FMVSS (Federal Motor Vehicle Safety Standard) 121 calls for air brake systems to fully stop tractor-trailers in no more than 250 ft. when loaded to their gross vehicle weight rating (GVWR) at 60 mph. This is true for commercial vehicles using either air disc brakes or S-cam drum brakes.
Drum or disc? Fleets weigh in
So which type of brake can better help you meet these FMVSS standards?
According to Bendix Commercial Vehicle Systems, a 6x4 tractor-trailer going 60 mph takes 200 ft. to stop with air disc brakes and 225 ft. with drum brakes. An independent test of Bendix ADB22X air disc brakes completed on a test track by Pitt Ohio revealed that at 55 mph, these ADBs stopped 15 ft. earlier than drums.
“Fifteen feet is the length of a car,” noted Jeff Mercadante, VP of safety at Pitt Ohio, a perennial fleet safety award winner. “When you get up to 70 mph, you’re talking closer to 50 to 60 ft.”
Drum brakes, though, make up the majority of systems in trucking, as they initially cost less. ADBs, however, have gained market share in the last decade. In 2015, ADB adoption was about 15%, while in 2020 it doubled to 30%. ADBs have fewer parts for quicker servicing, which can lead to higher uptime and a better total cost of ownership. But that hardly settles the debate.
Terrance Wall, senior manager of maintenance technical support at Ryder, pointed out that for decades, S-cam type drum brake systems have been the “go-to” standard for medium- and heavy-duty trucks and tractors.
“Drum brakes are a consistent economical solution that provides common components across multiple vehicle platforms as well as weight classes,” he said. “And since the implementation of reduced stopping distance regulations in 2013, drum brake lining manufacturers have improved materials to meet or exceed the stopping distance requirements.”
“Although air disc brakes do have a slightly shorter stopping distance, drum brakes still easily meet the requirements,” Wall continued. “Air disc brake systems do have an advantage when brakes heat up and brake fade becomes more evident, but with a multi-vocational fleet, a uniform and economical option becomes the primary focus second only to safety.”
For Ryder, that is where drum brake systems have an advantage. When operating a wide variety of vehicles and with multiple repair locations, standard practices that include uniform training, tooling, and maintenance procedures are paramount to maximizing the useful life of brake components while maintaining the safety and cost effectiveness of the brake system.
Penske Truck Leasing, meanwhile, mostly specs ADBs. “To capitalize on their full benefit, however, both the tractor and trailer need to be equipped with air disc brakes,” noted Chris Hough, Penske’s VP of maintenance, design, and engineering.
Air disc brakes benefit the Penske fleet in several ways. In the area of safety, Hough noted, they provide shorter stopping distances and reduced brake fade. From a maintenance standpoint, there are fewer moving parts and grease points, and no need to measure brake stroke. Also, pad replacements are a relatively quick and simple process. Penske shops also are stocked with brake vendor-specific tools, along with hub handlers and various gauges to measure the remaining brake pad life and to inspect the rotor condition.
Hough also pointed out that ADBs have helped reduce the number of units placed out of service for brake stroke compliance issues during roadside inspections. “When it comes to ROI, there are some segments that are hard to measure,” he explained. “In general, we have found that ADBs provide a lower brake maintenance [cost per mile], provide our customers with improved stopping distances, and increase uptime.”
The advent of new technologies such as lane departure, electronic stability, and adaptive cruise control, which are now being integrated with ABS systems, also contribute a great deal to extending the life of foundation brake systems, he added. ADB systems also offer electronic pad wear sensors, which can provide data via telematics to assist in PM interval planning and procedures.
“All brake component manufacturers provide specific maintenance procedures to ensure optimal performance and life from these components,” Hough said. “By integrating these procedures into your brake maintenance program, coupled with the utilization of the correct tools, the maximum useful life at the most economical cost can be realized.”
“ADB systems provide benefits such as less time required to replace lining material and fewer components to lubricate,” Hough continued. “However, even with these benefits, ADB systems typically cost more to maintain and are difficult to standardize across a multi-vocational fleet without maintaining a larger inventory to accommodate the different spec and lining requirements.”
For example, some operations with repeated stop-and-go applications, such as refuse and inner city routes with multiple deliveries, can realize cost savings from shorter maintenance times and extended pad life when ADB systems are equipped with the proper friction material.
However, he cautioned that the ease of getting an accurate measurement of the lining material on both the front and rear of the rotor is consistently a drawback on currently designed ADB systems. This, in turn, typically leads to less than full utilization of the lining material if the pads are being changed prematurely.
“It is important to carefully analyze the duty cycle and operation of the fleet to determine the optimal type of brake system that makes economic sense but also provides the maximum useful life while retaining maintenance efficiency for your technicians,” Hough stated.Avoiding OOS violations
No matter what types of brakes are employed by a fleet—and it may even be a mix of both on the same tractor-trailer—the driver and maintenance team must keep a close eye on their systems because the Commercial Vehicle Safety Alliance (CVSA) will be watching.
Unfortunately, not all fleets do. In the 2022 CVSA International Roadcheck commercial motor vehicle inspection and enforcement initiative, brake system issues resulted in the largest percentage of violations: 25.2% in the U.S., Canada, and Mexico combined. In fact, brakes were the top reason for out-of-service violations in both the U.S. (24%) and Canada (38%), and 26.1% of violations were second only to tires in Mexico.
According to FMCSA’s Motor Carrier Management Information System, common out-of-service violations for all of 2022 included: brake hose or tubing chafing and/or kinking (Violation code 393.45B2), inoperative/defective brakes (393.48A), brakes out of service (396.3A1BOS), and missing or defective parking brake system (393.95B).
It’s impossible to know all the different variables and events that led to all of these violations. What is known is that the last line of defense, the driver, likely missed something on their pre-trip inspection.
“Considering that a high percentage of violations for brake issues are air leaks and chafed air hoses, a big part—but not all, of course—of these could be avoided with a good pre-trip inspection,” noted Keith DiRuscia, manager of fleet maintenance at Pitt Ohio. “We still keep our preventive maintenance intervals at a point where we catch most brake thickness and cracked lining at the shop level.”
Drivers are the last line of defense, though, and former Washington State Patrol officer Fred Fakkema, currently VP of safety and compliance at Zonar Systems, offered some tips to help drivers avoid these types of brake violations.
“While conducting pre-trip inspections, listen for leaks and look at the hoses and valves,” he said. “It’s very easy to see chafing and check the connections. A visual check of slack adjusters and wheel ends is also important during the pre-trip. Many drivers believe that since there are automatic adjusters, there is no reason to look. But they are still mechanical and need to be maintained.”
Fakkema urged that drivers not get complacent. Issues such as pressure loss or an inoperable parking brake should be discovered during a proper pre-trip. It is important that fleets are proactive at all times.
“Once a fleet realizes they may have an issue with brake violations, it may be too late, and they will have already received numerous roadside inspections with brake violations,” he said. “A fleet should always have pre-trip inspections and identify brake violations in their ongoing in-service training. The training and reinforcement of these issues are vital—not only for the safety of the driver but also for all motorists on the road.”
Fakkema noted that seven of the top 20 CVSA violations were for brakes.
“If you stop and think about that, the mechanism that stops an 80,000-lb. truck is among the most noted violations,” he explained. “That alone should encourage the driver to do a proper pre-trip inspection to get in that safety mindset before leaving the yard.”
Better solutions for better braking
To help keep those 80,000-lb. tractor-trailers and all other commercial vehicles stopping as they should, manufacturers have continued to churn out continually better braking technologies that exceed FMVSS requirements.
“The OEMs have an additional 10% better than FMVSS requirement, and all production brakes must meet those requirements,” said Chuck Brodie, field service team leader at ZF Commercial Vehicle Solutions.
Because brake manufacturers all have the same basic stopping requirements, they have to set themselves apart in different ways. Here’s how several of the leading brake OEs have done that.
Meritor
In 2020, Meritor introduced the EX+ LS single piston air disc brake designed for linehaul, city pickup and delivery, and trailer applications. According to Alicia Wong, director of brakes at Meritor, the lighter mono-block air disc brake is the result of five years of development.“The EX+ LS brakes include features of our EX+ platform, such as the adjuster mechanism, and have new advantages such as an improved sealing system with fewer entry points for moisture, enhanced taper wear performance, and an approximately 20-lb. weight reduction on a 6x4 truck,” she said.
“Meritor continues developing and testing new technologies for overall brake health, such as positive pad retraction, a solution that improves brake drag and fuel efficiency, and enables longer pad life,” Wong continued. “We have also developed smart sensor-based products, such as a pad wear warning indicator that enables wear prediction and proactive maintenance planning.”
In addition, Meritor has in the works an equivalent solution in a lining wear indicator for drum brakes. “Collectively, these new technologies support fleet technology and information requirements for trucks and trailers, and contribute to TCO optimization, uptime, and reliability,” Wong said.
Meritor was acquired by Cummins this year, and time will tell how this will further push Meritor’s braking systems forward.
Bendix
Commercial vehicle safety technologies are increasingly complex, and full-stability systems are mandated for all new trucks, pointed out Mark Holley, Bendix director of marketing and customer solutions, wheel-end.“Ultimately, these systems depend on consistent stopping power at the wheel ends to work at their best,” he said. “That’s where air disc brakes shine—and it’s a big part of the reason that adoption rates for ADBs are now approaching 50% on trucks and tractors.
“Air disc brakes also provide shorter stopping distances than drum brakes,” Holley continued. “At 60 mph, a fully loaded tractor-trailer stops in about 225 ft. with drum brakes. In our testing, air disc brakes showed a 12% improvement by reducing the stopping distance to roughly 200 ft., and some of our testing showed up to an almost 75-ft. difference when drum brake fade becomes a factor.”
Brake fade can happen when heat friction on the drum causes it to expand away from the friction material. This lengthens the pushrod stroke needed for the brake to contact the drum frictional surface, weakening the stopping power.
Bendix also offers pad wear sensing on its ADB22X air disc brakes. The technology removes the guesswork from friction replacement because it uses a sensor to determine when the pad is nearing its end of life, then generates a diagnostic code that can either be sent to the fleet office via telematics or pulled by a technician using a diagnostic tool. This enables fleets to make sure they have friction available and proactively schedule maintenance while also protecting costly components like rotors from being damaged by worn-out friction.
Holley also pointed out that electric commercial vehicles will be spec’d with air disc brakes and that Bendix is actively engaged in numerous projects with commercial EV OEMs. The EVs will employ regenerative braking, which will reduce wear on any brakes by capturing that stopping energy in the motor and converting it to electrical energy that is stored in the battery.
ZF CV Solutions
ZF, which folded Wabco into its newly formed CV Solutions group, is also high on ADBs.“Air disc brakes really shine in conditions that heat the brakes up more than the defined test,” ZF’s Chuck Brodie explained. “Long downhill runs, stops from higher speeds, and multiple stops are where drum brake performance can be impacted more than on disc brakes.”
ZF’s latest foundation air disc brake offering, the MAXXUS L2.0, has been in production since 2020. And these will also help steer the future of higher degrees of autonomous driving.
“From a purely pneumatic and mechanical setup, brake system evolution led to stability control, increasing safety, and adding more SAE Level 1 and Level 2 functionality to enhance safe and efficient driving,” Brodie related. “Looking ahead, with fully integrated deceleration control, brakes will include regenerative braking capability and with that bring in efficiency and reduced friction brake maintenance.
“To put it simply, the driver tells the system how fast they want to decelerate by applying the brake pedal, and the system will use the most efficient combination of engine brake, retarder control, and regenerative braking when available to achieve the driver’s demanded deceleration,” he explained further. “That makes for an easy-to-operate system with optimized efficiency and brake friction material life.”
TSE Brakes
Air disc and drum brake systems technology continues to evolve, noted Patrick McNamara, VP of sales and marketing at TSE Brakes. Two key items that are available from the company are ADB brake pad sensors and, for drum brakes, the TSE-Sense system, which monitors not only brake stroke but also service and parking-brake status.“Those solutions assist fleets with planning preventive maintenance and provide fleets with real-time data with regard to the brake performance,” McNamara said. “The TSE-Sense system can also assist with early indication of when to service based on brake stroke. That not only keeps brakes operating at their optimum but also prevents out-of-service events as fleets are notified in advance that they are approaching out-of-stroke parameters.”
Haldex
In 2018, Haldex began offering the lightweight Gen II version of the ModulT ADB for trailers. This year, the Swedish brake maker came out with ADBs for trucks, based on the Gen II design, starting with medium-duty DBT22 MD.The ModulT product line also includes the DBT22LT caliper for 22” wheels. Design features include a single casting that reduces weight by avoiding the need for an extra interface and more bolts. Because the system employs a single tappet mechanism, rather than twin, fewer parts overall are needed.
In combination with its air disc brake, Haldex also offers the fully sealed LifeSeal+ spring brakes for all truck, tractor, and trailer applications equipped with air disc brakes.
“Standard spring brakes wear out quickly, usually from corrosion and contamination ingress through the vent holes,” said Denisse Pedraza, commercial product manager for disc brakes and actuators at Haldex. “That results in premature breakage of the power spring, which leads to unscheduled repair and replacement, costly downtime, roadside repairs, and even unsafe or inadequate braking performance. With LifeSeal+, the spring chamber is completely sealed, so contaminants cannot get in and the actuators last twice as long as traditional vented actuators.
“Braking systems are continuously evolving,” she continued. “In 2026, we will release the Haldex EMB, an electromechanical brake. The EMB is much simpler than existing pneumatic systems because it is electrically controlled and actuated from the brake pedal to the wheel end.”
She added these EMBs have about half as many components, so the entire system is lighter and simpler to produce and install.
“Because it does not need a compressor, the high-efficiency EMB offers a 90% energy savings compared to existing conventional pneumatic systems on trucks and buses,” Pedraza added. “The EMB is also quieter because there are no compressors or valves, which are typically noisy when charging and venting.”
EMB includes an electric parking brake function as part of an integrated wheel end design. According to Pedraza, the system delivers 15% reduced stopping distance thanks to better and more precise control of wheel speed compared to pneumatic systems. This actuator control precision results in a more stable clamp force on the rotor, increasing the life of pads and lowering brake dust emissions.
“EMB offers the level of diagnostics and redundancy in controls to support Level 5 autonomous commercial vehicles,” Pedraza added. “Over the next few years, Haldex will continue developing, testing, and validating the technology with simulations and physical units in readiness for EMB industrialization.”
Keeping with the trend of mergers and acquisitions, Haldex was acquired by SAF-Holland Group in August.
Brake tools in the shop
According to Kevin Pfost, coordinator, technical service at Bendix Commercial Vehicle Systems, these are the shop tools and equipment needed to properly maintain and repair air disc and drum brakes:
- Friction wear gauges
- Tape measures and micrometers
- Magnetic base and dial indicators
- Borescopes and inspection mirrors
- Disc brake hub and rotor jacks
- Drum dollies
- Torque wrenches
Additionally, he recommends that fleets and service providers use manufacturer training as well as reference Service Data Sheets and troubleshooting guides.
Product innovations also impact how brake system service and repairs are performed, related Denisse Pedraza at Haldex. “Haldex offers a complete toolbox with all required items for air disc brake service,” she explained. “Our toolbox is standard; the only unique tool necessary to remove ModulT pads is a Torx 55-bit for making brake adjustments, which is included.”
Shop tools and equipment for properly maintaining and repairing brakes is something to discuss with brake suppliers, noted Chuck Brodie at ZF. “With our MAXXUS L2.0 system, you can replace brake pads with basic tools, but ZF also has tool kits for deeper maintenance such as guide pin bushing replacements,” he said. “For ABS, you need our diagnostic software, TOOLBOX Plus, to go with your basic toolset.”
Making the right connections
Digital technology also is helping to prevent brake issues. To help fleets make more precise decisions about brake maintenance, the PreSet Plus SmartHub provides actionable insights on wheel end components from a sensor applied to the hub barrel and alerts fleets about issues with brakes, noted Isaac Otto, product manager at ConMet Digital.
ConMet Digital also offers SmartAir, which provides line pressure monitoring for visibility into trailer emergency-brake air pressure. Real-time data from the system is available on the ConMet Digital dashboard and soon through a driver mobile app, where users can set alerts for information during pre-trip or maintenance inspections as well as on-the-go.
“Line pressure monitoring gives drivers visibility to brake drag as a result of improperly connected air lines, debris in the pneumatic system, or forgetting to release the parking brake,” Otto explained. “Trailer applications are where SmartAir line pressure monitoring becomes crucial for identifying slow air leaks across one or more trailers.
“Fleets face mounting needs for efficiency and increased uptime, and inspections and violations can delay deliveries and sideline vehicles, causing costly downtime,” he continued. “Actively monitoring brake air pressure can help fleets and drivers take corrective action before hitting the road, reducing the chance of costly fines and violations.”
About the Author
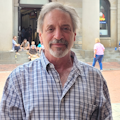
Seth Skydel
Seth Skydel, a veteran industry editor, has more than 36 years of experience in fleet management, trucking, and transportation and logistics publications. Today, in editorial and marketing roles, he writes about fleet, service, and transportation management, vehicle and information technology, and industry trends and issues.