Why you may want to repair wheel-end systems now
The Commercial Vehicle Safety Alliance (CVSA) has announced that wheel ends will be the focus of this year’s International Roadcheck inspections initiative running from May 17-19. The goal of this annual inspection program is to check that truckers in the United States, Mexico, and Canada are up to date with maintenance work on their big rigs for the safety of drivers and nearby motor vehicles. During International Roadcheck, inspectors will examine large trucks and motorcoaches using CVSA’s North American Standard Inspection Program procedures as well as the driver’s credentials. If they successfully pass Level I or Level V inspections, they will receive a CVSA decal and avoid lectures from inspectors. Truck owners and operators should be proactive to repair wheel end systems now in preparation for May’s 72-hour blitz. Keep reading to learn what inspectors will check on heavy-duty vehicles, which truck parts to replace, and how to properly install them.
Why care about wheel ends?
According to the CVSA, about one quarter of historical commercial vehicle incidents involve components from faulty wheel end systems (wheels, rims, hubs, and tires) and remain common trucking violations declared by the Federal Motor Carrier Safety Administration (FMCSA). Since these components support heavy loads on big rigs and help to stabilize and control vehicles, failing to care for them can result in wheel-offs and crashes.
What should I repair?
Truckers should always perform pre-trip inspections before any long-haul trip; but to dodge citations from inspectors during International Roadcheck, truckers should fix leaks they see from wheel seals, hubs, and tires. They should also care for weak bearings, cracks in wheel rims, plus supporting wheel end parts like locking rings, studs, valve stems, and clamps. Finally, they should care for their tires by properly inflating them and inspecting them for tread wear.
Fixing failing wheel seals
The most common reason for wheel seal failure is due to improper installation and incorrect bearing alignments. If drivers rush the installation process, they may fail to see that the wheel seal is not properly on the spindle or within the hub—or even in the correct direction. Wheelco recommends lining up the seal and inspecting it for a snug fit prior to installing the part.
“If your seal is for a spindle mount, check this by gently sliding your seal onto the bare spindle shoulder and look for gaps between the inner diameter of the seal and the spindle. If your seal is a hub mount, place the seal over the hub and again check for any gaps between the seal and the hub. If it all lines up for a snug fit, you know you have the correct seal that should fit properly,” Wheelco stated.
Wheel seals should be installed with the lip facing the “wet/oil” side. Backwards installation can result in leaks.
Bearing adjustments
Loose wheel bearings can negatively affect the performance of tires and cause wobbling wheels and alignment issues. Technicians may be quick to grab an impact wrench to fasten bearings, however, this tool is not recommended as it can lead to over- or under-tightening of the wheel bearings. Instead, using a breaker bar and socket followed by a torque wrench to tighten the seal is the better approach. It is recommended to check manufacturer guidelines and follow the Technology and Maintenance Council’s RP-618 bearing adjustment procedure references for proper technique which advises the use of a wheel end dial indicator tool to display wheel bearing end play (.001 inches to .005 inches).
Weak wheel rims
Rim cracks are a common issue due to excessive weight from heavy loads. The location of the crack matters. A crack on the inboard side of the wheel, or the back, should be easy to repair. Cracks near the base of the spoke and the lug area are typically non-repairable.
Proper tire inflation
Low tire pressure can result in the reduction of braking distances, tire treads, and even fuel economy. The “right amount” of tire pressure will depend on the truck and the maximum load capacity. Other factors to consider include whether truckers are cruising on “steer” or “drive” tires and the size of the tires. Typically, heavy-duty steer tire pressure should be at approximately 110 psi while drive tire pressure can set around 85 psi. All tires’ psi will be different based on application. Check tire psi using a tire pressure gauge to determine under- or over-inflation.
While checking tire pressure, inspect for cracked valve stems by applying soapy water to the valve stem. If bubbles appear, there is a crack or leak that needs to be addressed. Luckily, valve stems are easy to replace on tires by removing lug nuts with a lug wrench and deflating the tire.
May the odds be in your favor
The CVSA has given truckers plenty of time to inspect their wheel end components prior to the 72-hour event. Now, it is up to drivers and fleets to make the necessary repairs prior to May’s International Roadcheck.
Information provided by: JIT Truck Parts
Author bio: Jennifer Smith is an e-Commerce Digital Content Specialist for JIT Truck Parts in Highland Park, Illinois.
About the Author
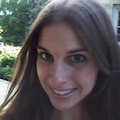
Jennifer Smith
e-Commerce Digital Content Strategist
Jennifer Smith is an e-Commerce Digital Content Strategist with JIT Truck Parts in Highland Park, Illinois. JIT Truck Parts is a national aftermarket truck parts distributor servicing national, regional, and local fleets. With distribution centers located throughout the U.S., JIT offers parts from leading manufacturers—delivered any place, on time, with a commitment to customer service.