Arrival to start building batteries in U.S. and train technicians to service its electric vans
Electric delivery vehicle startup Arrival is creating a program to train and certify technicians to service its vehicles in the U.S. and Europe. As it prepares to launch its BEV products, the company plans to build a high-voltage battery module (HVBM) assembly plant in Charlotte, North Carolina, it announced this week.
The assembly plant would become Arrival’s third facility in Charlotte, joining its new North American headquarters and a van microfactory in the city. Arrival has proprietary battery modules that allow fleets to configure their battery requirements. The battery design goes with what Arrival calls its “plug-and-play hardware and software architecture,” allowing scalability.
See also: Jumping on the EV bandwagon
Arrival’s proprietary software runs across all of its in-house components, diagnosing potential issues and optimizing the fleet experience, intending to improve total cost of operations. Operators can replace just one module instead of a whole pack, saving costs and downtime. The modules manufactured in Charlotte will be used in the Arrival Bus and Van produced at nearby microfactories.
Arrival also recently announced a collaboration agreement with Li-Cycle, a leading lithium-ion battery recycler in North America, to create a closed-loop EV battery supply chain in the U.S. and Europe.
“By bringing the assembly of our proprietary high-voltage battery modules in-house, we’re striving to be as vertically integrated as possible,” said Mike Ableson, CEO of Arrival Automotive. “This will enable us to have even greater control over the functionality and cost of our products and pass those cost savings on to the customer while also working toward our goal of zero waste production.”Arrival partners with existing technician networks
Arrival plans to begin vehicle production in Rock Hill, South Carolina, in Q2 2022, Ableson said. To service those future fleet vehicles, the company is creating a service platform based on data from its vehicles and proprietary algorithms to enable existing service providers to repair and maintain its electric vans and buses.
The program looks to use existing networks of technicians and workshops, ensuring scalable coverage while helping maintenance and repair companies transition to electric vehicles. Arrival is starting with four initial partners in the U.S.: Amerit Fleet Solutions, Bridgestone Retail Operations, NAPA Auto Parts, and Valvoline. (It also has tapped four E.U. partners: ARC Europe Group, Kwik Fit, Rivus Fleet Solutions, and ZF.)
Together these partners will help form the Arrival Service Network, with more than 21,000 workshops and 60,000 mobile service units across the two markets. Powered by Arrival's service platform, partners will have access to repair and maintenance documentation, in-person and online training, predictive and automated diagnostics, and spare parts distribution.
“We’re aiming to fundamentally change the way that maintenance, service, and repair is performed using in-house software to create a next-generation experience for our customers,” said Serge Sulgin, CEO of Arrival Solutions. “The Arrival Service Platform will provide a marketplace to connect EV users with skilled and certified service providers, giving them an end-to-end solution for the newest and most advanced products in their fleet and allowing us to scale our service network quickly and on-demand to meet our customers wherever they are. It will also give our partners the opportunity to upskill their workforce for the future of mobility.”
How Arrival’s service network works
The service platform starts at the vehicle level, where onboard sensors and embedded software constantly analyze the state of the vehicle and its components. This vehicle-specific information is maintained in the cloud, creating a real-time picture of the vehicle that allows Arrival to remotely determine which component needs service, rather than requiring technicians to diagnose an issue in the field manually.
The platform considers all the operations required to repair a vehicle based on the data received. It builds an optimized work package determined by the criticality of the issue, the parts needed, the skill levels of the technician required, and any additional information supporting material required. Fleets would be presented with scheduling options or an automatic selection based on their predefined criteria. The platform would orchestrate the coming together of resources to perform the repair.
If the technician encounters an unexpected issue, Arrival service engineers would be available on standby to provide remote support via chat and live sessions using smart glasses, or via in-person if needed. The platform also manages people by delivering training, certification, and technical support directly to the technicians and helping them stay up to date. Automatic warranty authorization and job documentation further support the technician through the entire process and minimize any paperwork required.
“Valvoline’s quick, easy, trusted approach to vehicle maintenance is the perfect complement to Arrival’s mission to create a ‘radical impact’ in cities across the nation,” said Heidi Matheys, chief marketing and transformation officer at Valvoline. “Our nearly 1,500 service centers across the U.S. offer exceptional service that will quickly and efficiently meet the needs of Arrival’s clients. We are thrilled to see the Valvoline-Arrival partnership come to fruition.”
This article originally appeared on FleetOwner.com.
About the Author
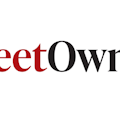
FleetOwner Staff
FleetOwner serves executives and maintenance management of commercial truck fleets that operate five or more vehicles, delivering business information about operations, vehicle maintenance, industry regulations and information-management technology. Engaging more than a half million commercial vehicle professionals every month, FleetOwner maintains the largest audience of commercial truck fleet executives available to the industry.