Aftertreatment systems (ATS) have been mandated on diesel trucks for about 15 years, yet diesel particulate filter maintenance continues to be a complex issue for the trucking industry and a big source of downtime. Shops have admirably acquired the knowledge to service the ever-evolving DPFs, but it’s an ongoing process. And lately, the parts shortage has made ATS components harder to come by. Spotting signs of trouble and damage will help their fleet better manage DPF issues, making inspections so important.
First, some DPF maintenance basics. The active and passive regeneration process routinely burns off soot collected in the filter during the engine combustion process, which keeps clogging at bay. But the system may also require a forced regen while parked. That causes a truck to become inoperable for about 45 minutes while the regeneration takes place.
According to RoadWarrior Inc., a provider of aftermarket DPFs, if a regen goes for an hour or longer and/or a truck undergoes unusually frequent forced regens, it could indicate that the filter isn’t heating up enough to burn off the soot. This leads to a clogged filter.
“It’s important to deal with this quickly, or the pressure buildup can crack the DPF,” the company noted.
And regens won’t burn off ash. At some point, the DPF will need to be cleaned or replaced.
“There are a few different factors when determining when a DPF should be replaced,” said Dustin Carnes, training/SME manager of product development at Diesel Laptops. “Some manufacturers recommend replacing the DPF around the half-million-mile mark. Others say the DPF should last the life of the vehicle, but that is only under the most ideal scenario.”
In between, the DPF can be cleaned, which can cost $250 to $650, according to Diesel Emissions Service, an operator of four truck repair and DPF cleaning facilities on the West Coast. A new DPF costs several thousand dollars. OEMs set these intervals based on mileage and/or fuel consumption. DPFs can last 300,000-500,000 miles. A fleet should not rely on those intervals alone. Engine data will also give fleets a good start on detecting if DPF service is needed.
“Engine manufacturers use strategies within the aftertreatment or engine control module to calculate the percentage of ash in the DPF and to recommend when the filter should be removed and cleaned,” Carnes explained.
He noted that “most DPF replacements are the result of other upstream issues or a lack of maintenance.” Those issues could include oil, fuel, or coolant contamination, or could be a result of other uncorrected engine problems. These issues in turn may cause catastrophic damage to the DPF, Carnes warned.
“Every part of the engine works in conjunction with the exhaust aftertreatment system in maintaining a working vehicle,” he added. “If any part upstream fails, it has the potential to create problems in the aftertreatment system. Because the DPF is utilized to catch what’s in the exhaust, it can become the casualty of many other root cause issues.”
Inspection process
When determining whether to clean the DPF or replace the centerbody, specific processes and proven methods need to be applied when inspecting the filters to identify damage.
Velocity Truck Centers, a dealership network that sells and services Freightliner, Western Star, Mitsubishi Fuso, Hino, Autocar, Ford, FCCC, and other truck brands, provided a video demonstration on how to inspect the DPF core and identify damage. Velocity’s outlined criteria can be applied to all generations of exhaust aftertreatment, and the inspection process is purely visual, so no special tools are required.
It should be noted that the exhaust side of the DPF provides the most detail for determining the condition of the core. Good lighting will aid in the inspection process, Velocity advised. The dealer also detailed a number of specific areas to inspect when assessing a DPF for damage. According to Velocity, these include:
Surface damage: Gouges or scrapes
Scrapes and gouges on the surface of the core cannot exceed 1/2” in length and 1/4” in width and can be no deeper than 1/8”.
Surface damage: Loss of substrate plugs
The loss of substrate plugs across the surface is considered surface damage. Open cells along the outer edges cannot exceed three rows in from the edge. Surfaces with numerous gouges that do not exceed the tolerance criteria cannot exceed a total of five blemishes across the entire surface area.Vertical cracks
Vertical cracks are visible at the surface and may be seen on one or both sides. Vertical cracks may propagate in different patterns that may spider across the surface or around uniformly, parallel, or perpendicular with the cell walls.
Horizontal cracks
To identify filters that have experienced horizontal cracks internally, turn the filter to the exhaust or outlet side for inspection. The exhaust side of the filter can be identified by an embossed arrow on the can showing flow that points to the exhaust side of the filter or by careful consideration of the mounting flange characteristics. The exhaust side of the filter should have no signs or evidence of soot. Horizontal cracks run laterally through the brick. Cracking begins around the outer area of the substrate brick and propagates to the center but cannot be seen at the surface of the brick.
Internal horizontal cracks
Internal horizontal cracks in early stages leave traces of soot in a ring around the outer edge of the outlet side of the filter. More severe internal cracks that have propagated across the entire brick allow soot to accumulate in the outlet across the entire surface in a uniform pattern.
Foreign matter
Foreign matter blocking the surface pores of the substrate cause damage through the cells and during removal. Contamination could be any substance that adheres to the surface of the substrate and restricts flow.
Fusion or melding
Internal fusion breakdown allows soot accumulation on the exhaust side of the filter and can be identified as spots of soot or evidence of soot in non-conforming patches on the outlet surface. Fusion or melding of the substrate brick and the severity of the failure can be localized internal hot spots known as fusion or as extensive as a complete exothermal breakdown that can be seen by massive deterioration of the cell walls extending to the surface of the brick.
Brick slippage
Slipping of the brick can be identified by a reduction of clearance from the outlet surface area to the outlet flange of the filter can.
Can damage
Dents that exceed 1/2” into the can constitute can damage. Witness marks from clamps are acceptable unless the damage is so severe as to allow rust to penetrate through the can.
Flange damage
Flange damage is a distortion of the mating surface of the filter can at either the inlet or outlet clamping area. Bracket damage is a distortion of the bracket.Key points such as direction of exhaust flow, specific characteristics, and substrate brick damage and soot patterns are important when inspecting the particulate filter core for potential damage.
Similarly, Diesel Forward Inc., a distributor of new and remanufactured diesel engine components through its Alliant Power brand, details visual DPF core inspection criteria.
The Diesel Forward process includes steps for visually inspecting the DPF core housing and substrate inlet and outlet faces for the following damage:
- Cracked filter substrate
- Gouged filter substrate
- Melted filter substrate
- Soot accumulation on the DPF outlet face
DPF diagnostic considerations
Diesel Laptop’s Carnes explained that DPF diagnostics can be as simple as removing the inlet and checking for contamination or damage—or as complicated as running multiple on-board diagnostic tests with a scan tool to monitor the rise and fall of DPF pressures and the differential. Additionally, soot accumulation on the back or outlet side of the DPF is a telltale sign that the filter is internally cracked.
“When a DPF is replaced or cleaned, a technician must go into the diagnostic software and program a reset or replacement command so the control module knows that the DPF is now clean,” Carnes said. “One problem that arises is when technicians perform the resets when they are not needed, which can throw off the calculations inside the control module. That leads to technicians having to perform more diagnostics than necessary when ash has accumulated in the DPF, but the control module may not be aware of it.”
Diagnostic scan tools offer a solution to that challenge. Scan tools are needed for performing a DPF service for a number of reasons, noted Victor Rivilla, marketing director at CanDo International, maker of a wide range of diagnostic scan tools for commercial vehicles. For example, they give forced regenerations the ability to override soot levels logged in the engine ECM, which occurs when soot loads are too high for a passive or active regeneration. The tools are also needed to scan for trouble codes prior to performing a forced regeneration.
“It is also important to use a scan tool to view live data on soot levels, soot concentration, and DPF load before, during, and after the forced regeneration,” Rivilla said. “Finally, after performing the forced regeneration, the scan tool is used to reset or turn off the DPF light.”
Steve Hoke, president of Diesel Emissions Service, said that a sound approach to evaluating DPFs is to use several tools to get the whole picture on aftertreatment problems. At the same time, he was quick to point out that DPFs are serviceable units and should be cleaned every 75,000 to 100,000 miles.
“This keeps the volumetric efficiency of the DPF where the manufacturer intended it to be,” Hoke explained. “Barring no engine upset conditions and yearly cleanings, the DPF should last for many years. In fact, we have customers that have had the same DPF for more than ten years.”
When it comes to sourcing replacement DPFs, Hoke noted that current supply chain issues have led to some lack of OEM ATS components, but there has been steady availability of aftermarket parts. “Fleets could assume that a branded part meets or exceeds all OEM parameters,” he explained. “Brand reputation should help with this decision, and warranty length and what’s actually covered should also be included when making a choice.
“In all cases, fleets should look to their local truck parts supplier or specialist in the DPF cleaning business,” Hoke added. “Most truck parts distributors have chosen reputable companies to partner with for aftertreatment parts.”
The importance of proper DPF inspections cannot be understated. Beyond cleaning and maintaining the filters, however, it is important to recognize that a DPF will eventually need to be replaced. In those cases, there are several OEMs and aftermarket providers that offer new and remanufactured replacements.
About the Author
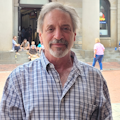
Seth Skydel
Seth Skydel, a veteran industry editor, has more than 36 years of experience in fleet management, trucking, and transportation and logistics publications. Today, in editorial and marketing roles, he writes about fleet, service, and transportation management, vehicle and information technology, and industry trends and issues.