A maintenance guide to ADAS technologies
Federal efforts to improve commercial vehicle safety, along with the fear of nuclear verdicts, will likely expedite the voluntary adoption of more advanced driver assistance systems (ADAS) in trucking, particularly for Class 7 and 8 vehicles.
Touted as potentially lifesaving systems, ADAS technologies fall into four categories: active braking systems, active steering systems, active warning systems, and camera monitoring systems. Vehicles may use all or some of these features, which may provide a certain degree of autonomy for the vehicle.
Through Detroit Assurance 5.0, Daimler Trucks North America (DTNA) provides SAE Level 2 automation on the Freightliner Cascadia and Western Star 49X trucks. This includes active lane assist (ALA) technology that provides temporary automated steering and acceleration/deceleration, along with active brake assist and adaptive cruise control to 0 mph. Detroit has also added updated features such as active speed intervention to alert drivers with visual and auditory cues when the speed limit is exceeded and ALA with Auto Stop to gradually bring the truck to a halt.
Most manufacturers today are factory-installing ADAS, such as automatic emergency braking (AEB), lane-departure warning, lane-keeping assist, or blind-zone detection. These systems work through a series of cameras, radars, and other sensors that are responsible for capturing and transmitting information to the driver.The Bendix Wingman Fusion driver assistance system, for instance, is now standard safety equipment on the International Trucks LT and RH Series, and optional on the MV, HV, and HX Series trucks.
ADAS solutions also provide an increasing amount of complexity. For fleet maintenance operations to keep up, that will mean developing standardized training procedures for technicians working on these advanced systems.
“A few decades ago, the generalization and efficiency of the use of ADAS technology in commercial vehicles might have seemed uncertain,” noted Marcos Obispo, sales and training manager, diagnostic sales, Cojali USA. Cojali provides tools to detect and troubleshoot issues with ADAS.
Now that they are certain, Obispo said the next step is to accelerate industry learning and understanding to discover new insights, as opposed to being satisfied ADAS has entered the commercial vehicle space.
And that is what the industry is doing.
The Federal Motor Carrier Safety Administration (FMCSA) has teamed with the American Transportation Research Institute (ATRI), American Trucking Associations (ATA), ATA’s Technology & Maintenance Council (TMC), Owner-Operator Independent Drivers Association, Virginia Tech Transportation Institute (VTTI), and various suppliers on an initiative called Tech-Celerate Now. The overall intent of the program is to provide outreach materials for fleets to implement ADAS, as well as training materials for drivers and maintenance personnel related to ADAS operation, inspection, and troubleshooting.
VTTI has been studying heavy vehicle safety for more than 20 years now, and since safety technologies in trucking have become more prevalent and advanced, the organization has heavily focused on the vehicle technology side, explained Matt Camden, senior research associate for VTTI’s Center for Truck and Bus Safety. And ADAS has become one of VTTI’s main focal points today.
Over the course of a decade or more, ADAS technologies in the commercial trucking space have really begun to advance. Earlier generations of technologies had more limitations, Camden said. For example, the very first few generations of AEB would generate more false alerts. Lane-departure warning is another system where the technology is improving, Camden said.
As these technologies continue to advance, TMC is working on several recommended practice (RP) guidelines—many of which are still in draft form—under the Tech-Celerate Now program.
“Technicians must take a ‘whole truck approach’ when servicing ADAS-equipped vehicles,” TMC advised. “For example, all ADAS repair procedures are based off the assumption that the vehicle being serviced has a properly functioning antilock braking system (ABS).
“Keep in mind that small things can change ADAS operation or calibration,” TMC added. “ADAS can be affected by anything that can change sensor detection and/or location, cab ride height, etc.”
To properly train technicians on ADAS, TMC has identified four “critical areas”: onboarding new ADAS equipment training, performing preventive maintenance (PM), diagnosing driver complaints, and performing collision repair procedures.
Thorough technician training
ADAS technology is now commonly available from several manufacturers that offer an array of capabilities and functionality. These systems—known under several trade names such as Bendix Wingman, Daimler Assurance, Volvo Active Driver Assist, ZF OnGuard, and more—require equipment owners and users to follow correct maintenance and repair procedures to ensure proper operation, according to TMC.
“These technologies are moving targets, constantly evolving and improving,” explained Robert Braswell, TMC’s executive director. “Processors and sensors are challenged by limitations in processing speed and functionality; each generation gets better. Software algorithms need to handle extremely complex problems of dynamic traffic situations; these are constantly being improved. And when GPS is not available to the truck, better mapping systems can fill the gap. Standardization of nomenclature and design can also help in the specification and maintenance of ADAS.”
Because of all these moving parts, when onboarding new ADAS equipment training, TMC urges maintenance shops to train technicians in PM inspection procedures, ADAS service and repair information, warranty coverage, system part identification, part location, system function, and diagnostic system testing.
When it comes to parts, Fabio Mazzon, technical manager, TEXA USA, told Fleet Maintenance that it’s not easy to determinate the best way to handle the ADAS replacement parts.
“Cameras, radars, and sensors are more expensive than other spare parts already present in the shop,” he advised. “Also, electronic parts, such as cameras and radar, have to be stored in good condition away from dust, dirt, and humidity.
“But a small inventory is suggested,” Mazzon added. “A truck with a failure related to ADAS is a truck that can’t be on the road.”To reduce truck downtime, meticulous training to make the most of ADAS technologies comes into play. T.J. Thomas, Bendix director of marketing and customer solutions, stressed that both drivers and technicians need thorough training on the systems and their limitations.
“If that is covered with the driver and the technician before the vehicle is put into service, then a significant number of questions are answered,” Thomas said.
“If you’re a fleet that is just coming up to speed or your technicians are still ironing out details on how they incorporate that into your fleet, that could be a barrier,” he added. “Many dealerships have a lot of training and are up to speed, but a fleet may or may not be depending on how they maintain their vehicles.”
TMC urges fleet maintenance professionals to keep in mind that because there are several types of ADAS technologies, they should always be cognizant of the specific version being serviced. That also means checking OEM guidelines for any detailed repair, inspection, and warranty procedures.
Proper installation, calibration
Cojali’s Obispo pointed out that specific training will ensure that service providers are well placed to face this new market demand. Maintenance operations must understand the importance of the correct functioning and calibration of the ADAS solution, understand the different types of calibrations, and learn the use of calibration tools, he added.
For example, Bendix Wingman Fusion’s FLC20 camera and FLR21 radar require a specific tool to be calibrated. There are also many considerations to alert technicians to, even if they are not specifically addressing an ADAS maintenance issue.
“It’s important to understand that the position of windshield-mounted cameras might be disturbed by many factors: after the windshield replacement or installation, after vehicle body repairs that may have affected the windshield after a control unit replacement, after accidents, after a wheel alignment, after a tire size change, after suspension levels change, after the replacement of the camera or radar,” Obispo explained. “Therefore, fleets and service providers have the challenge to get ready for this new technological era, and make sure that they are able to work on the installation and calibration of ADAS systems in order to get trucks back on the road in optimum conditions.”
He emphasized that if repairers are unable to calibrate the safety systems, they should inform customers and drivers about the necessity and importance of getting the system calibrated somewhere else, as well as the risks of an incorrect or not completed calibration.In short, Obispo added, correct calibration will be key to guaranteeing the “perfect functioning” of the safety system and getting the most out of this technology. As far as fleets are concerned, he advised maintaining a control and record of the different systems incorporated or installed in vehicles (type, manufacturer, model, parts, or components that make it up).
“Based on our experience working closely with fleet managers, service managers, and technicians, we could say that now more than ever fleets and repair services are beginning to realize the need for and importance of calibration after repair work on the part,” Obispo said. “The reason is easy; they see that the number of commercial vehicles on the road and in workshops that incorporate these systems increases every day, and they want to remain competitive in the face of this new demand.”
TEXA’s Mazzon also emphasized that ADAS calibrations, alignment processes, suspensions calibration, and chassis/frame inspections must be part of the long-term maintenance plan for heavy-duty trucks.
Performing PM inspections
According to TMC, when performing PM procedures, technicians should connect the equipment to diagnostic computer to check for stored, inactive, or active fault codes, and check for any available software updates.
Technicians should also check for any driver vehicle inspection reports (DVIRs) that would indicate malfunctioning, as well as visually inspect all systems. For instance, check wiring and brackets, and inspect for signs of tampering—that might include high counts of inactive fault codes related to blocked sensors or switches that are related to safety systems like lane-departure warning.
High counts of inactive fault codes might be related to sensors and components that drivers unplug, such as cameras, displays, radars, and electronic stability program (ESP) sensors to disable ESP and collision mitigation.
Technicians should also inspect dash- or cab-mounted camera displays, including rearview displays, side mirror displays, blind spot displays, or bird's-eye view displays, TMC pointed out. That includes inspecting the surface of the display for cracks or scratches that will impair view and testing each type of installed camera display to check for clarity and function.
When installed, these systems do have a test mode. TMC urges using those instructions and abilities to test the full function of each system. “This is especially important to collision avoidance and automated emergency braking systems,” according to TMC. “It’s not safe to physically test all ADAS.”
Check for installed ADAS that include computer-guided checks while connected to a diagnostic computer. When they exist, TMC recommends performing these as a routine part of preventive maintenance.
TMC also advised that a professional driver should test drive the equipment—only if the systems can be tested safely. In addition, TMC recommends inspecting the function of ADAS technologies such as adaptive cruise, lane-change assist, and blind-spot assist. When test driving, see if any failures show up on the display screens.
After inspection, TMC recommends technicians make a post PM diagnostic scan to ensure any failure codes are cleared.System upgrades
Historically, commercial vehicle safety systems have typically relied on an individual radar or camera to identify valid objects and vehicles before issuing an alert or taking action. Supplier Bendix has taken its latest driver assistance system, Bendix Wingman Fusion, a step further. Wingman Fusion integrates next-generation advanced safety technologies like radar, camera, and brakes into one system.
Bendix built Wingman Fusion from technologies including Bendix ESP Electronic Stability Program full-stability system, Bendix Wingman Advanced collision mitigation technology, and AutoVue Lane Departure Warning System from Bendix CVS. New features for Wingman Fusion include stationary vehicle braking (SVB) and overspeed alert and action.
Bendix’s Thomas advised that because there is a significant amount of engineering that goes into these upgrades, installing ADAS technologies is not a one-size-fits-all for fleets. Upgrades, he noted, are designed for the specific make, model, and year of the vehicle.
“We are noticing that the OEs are applying that technology a bit differently from make to make,” Thomas said. “A feature that might be called the same feature by Bendix might operate just a little bit differently given a different OEM. We would encourage the fleets to get their dealership involved to make sure they fully understand from that specific OE point of view exactly what feature set is on that vehicle they are ordering and to understand how the dealership or OEM describes it as well.”
Bendix offers several troubleshooting tips to minimize downtime for these evolving systems. A Bendix Tech Tips series provides guidance on troubleshooting and diagnosing advanced safety technologies, from the foundational elements of antilock braking to the components that enable collision mitigation, and more.
“Sometimes the first response to an indicated electronics problem within collision mitigation systems may be to start removing and replacing components,” Thomas pointed out. “But there are plenty of times when a component isn’t the issue, so we recommend starting by running a diagnostic software tool that shows a system view of what’s on the vehicle that includes key vehicle components as well.”
This assessment can give the technician a quick overview of what’s going on, especially when more than one component shows similar active diagnostic trouble codes (DTCs), such as J1939 communication errors.
The technician can also look for frayed wires, corroded connectors, or blown fuses. Additionally, equipment such as cameras and radars should be checked to make sure they’re unobstructed by things like road debris, snow, and ice.
In addition, some DTCs are “self-clearing,” Thomas said. “This means that simply by fixing the situation—removing the obstructing debris, for instance—the indicator lights and associated fault codes will be deactivated.”
Service data sheets should call out these types of DTCs so the technician is more aware of what kinds of conditions generate them.
More than ever, the various systems across a commercial vehicle are intertwined, with multiple electronic control units sharing necessary information over the J1939 network, Bendix pointed out. For example, automated transmissions depend upon information from the engine to operate properly and at their highest efficiency.
A J1939 fault, for example, will impact several systems, so a technician should investigate that fault first, then re-run the diagnostic tool to see if the individual system faults are cleared up, according to Bendix.
Before assuming that an advanced safety system active DTC means something is wrong with that system, technicians should make sure they’re using a tool that gives them visibility to any active DTCs being broadcast on the vehicle’s J1939 network. Bendix ACom PRO is one such tool, but the important thing is having a diagnostic tool that shows DTCs of the full vehicle, the company advised.
When connected to a vehicle, the ACom PRO software automatically detects and gathers active and inactive DTCs from all Bendix electronic control units on the vehicle, as well as key vehicle ECUs, like the engine and transmission. This roll call shows what’s on the vehicle, eliminating the need for a technician to guess from a pre-populated list of components.
ADAS technologies that offer capabilities like adaptive cruise control and AEB are deeply integrated through their communications with systems like the brakes, engine, and transmission. They also include their own ECUs and sensors like camera and radar units—components that require an extra degree of caution.
Modern diagnostic tools can increasingly make changes to systems, from calibration to reconfiguration. Bendix recommends that any individual technician should confirm with maintenance or fleet management before making any performance changes.
As systems are upgraded and technologies continue to advance, the lingering question is whether FMCSA will eventually regulate ADAS industrywide. Dan Murray, ATRI’s SVP, believes that for the technologies that make sense, it will be an evolution.
“I think everyone is moving toward active safety systems and away from warning systems,” Murray said. “Regulatory agencies are going to probably cherry-pick those that make the most sense for regulatory consideration.”
And, as TEXA’s Mazzon pointed out, everything will be different when ADAS technologies are mandatory in trucking.
“There will be precise regulations as there are in the automotive industry,” he said. “For this reason, shops should embrace this new technology and be sure that they are ready for it.”
About the Author
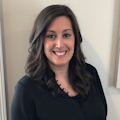
Cristina Commendatore
Cristina Commendatore is the Executive Editor of FleetOwner magazine. She has reported on the transportation industry since 2015, covering topics such as business operational challenges, driver and technician shortages, truck safety, and new vehicle technologies. She holds a master’s degree in journalism from Quinnipiac University in Hamden, Connecticut.