Best practices to avoid ADAS maintenance mishaps
Trucks outfitted with safety systems, such as advanced driver assistance systems (ADAS), which include active braking, steering, warning, and camera monitoring systems, are becoming increasingly common. Safety, after all, is every fleet’s top priority. This often means ensuring brakes and tires are in working order and changing them out when they aren’t.
It is equally important that fleet maintenance providers are up to the task of making sure each ADAS component, such as the various sensors and cameras, works at all times and their maintenance is a top priority.
“Fleets and shops must realize this will be a part of standard maintenance; it cannot be overlooked,” noted Fabio Mazzon, technical manager at TEXA USA, a provider of ADAS diagnostic and calibration solutions. “Soon most trucks will be equipped with ADAS systems as a standard. This means that technicians in the shop, whether they like it or not, will have to get familiar with the ADAS systems, and how to do calibrations and diagnostics.”
Some basic tips Mazzon offered include physically inspecting the systems and making sure the radar is clean and the truck is properly aligned. Spare parts should also be stored away from dust or humidity.
Being unprepared when an ADAS component isn’t working properly will lead to “significant downtime,” Mazzon warned.
Failure to do so will not only lead to more downtime but possibly accidents as well.
Mazzon noted that a malfunctioning lane departure system can cause the truck to drift into other lanes, while an uncalibrated or improperly installed radar connected to the emergency braking system can prevent it from sensing the vehicle up ahead and may not mitigate a potential collision in time.
It’s all connected
One thing to first note is that the more advanced ADAS technologies become, the more interconnected they are with each other. That can create a challenge for maintenance operations, noted Chuck Brodie, field service team leader, Commercial Vehicle Systems, ZF Group.
For example, an issue with an antilock braking system (ABS) wheel speed sensor can affect a collision mitigation system.
“A failed sensor can trigger a fault code, but it may not be an issue with that system,” Brodie explained further. “To accurately diagnose a problem, technicians can use software to follow a very logical step-by-step procedure. They can determine the description of the problem and, in our diagnostic software, double-click on fault code readings to see recommendations about what to check and in what order.”
While there are not recommended maintenance procedures for many of these systems, Brodie did say that fleets should be asking how they can make sure things are working properly. The answer often has to do with when and where modifications are made. For example, certain procedures could misalign the radar system, and replacing a windshield could move a camera out of position.
Brodie also stressed that while fault codes vary from system to system, drivers should report all codes.
“Drivers are not inclined to report issues if the truck is running correctly, but in the case of things like cruise control not working, it will get their attention,” Brodie said. “Drivers may also notice a service need when the issue is simply blocked radar caused by the buildup of sticky snow or ice.”
Training up technicians
Brodie added that technicians need to have a strong understanding of the electrical and data link aspects of ADAS technologies. “With that basic training, they are able to use diagnostic software and check simple things like power, ground, and data link connections. Not having that knowledge can lead to higher costs and not fixing the system.”
Main ADAS issues that are seen in the shop at Fyda Freightliner Columbus in Ohio are related to wiring, noted Jamie Denton, assistant service manager at the 30-bay shop, one of seven service department locations operated by the Elite Support Certified dealership network.
“Basic electrical is one of the skills we need to work on,” Denton said. “Training technicians to load test a wire to make sure it will carry the necessary current or to see if it fails goes a long way. We tell our technicians that a simple voltmeter is their best friend.”
Those issues can arise when aftermarket components are added to vehicles. For example, Denton related that an aftermarket bumper might impact the operation of a forward-facing radar.
“We had a vehicle in with an intermittent problem that was hard to diagnose,” Denton continued. “It turned out that when a camera was added to the windshield, the wiring wasn’t run through a grommet and the bare metal edge of the hole rubbed through the insulation. In that case, we had to start at the frame and didn’t find it until we reached the headliner. It took all that labor time for a problem that could have been avoided with a small, inexpensive part.”
For Denton, the biggest obstacle to effective ADAS diagnostics is learning how OEM and aftermarket systems communicate with the truck. “The use of these technologies is growing fast,” he said. “We started training a few years ago when the systems began to become more popular, and we’re always interested in refresher courses, especially about how the systems interact.”
Sensing sensor issues
It’s important to think of an indication that there’s a problem with a safety system as a chassis issue, noted Brian Screeton, supervisor, technical service training at Bendix Commercial Vehicle Systems: “Sensors are where we see the most issues with these solutions, and it’s generally related to moisture.”
Screeton provided two examples. In one case, you might try to calibrate a system without any luck, but taking the connector apart, cleaning it out with contact cleaner, and then putting compatible grease in might resolve the problem simply. Another issue might be with wiring pins that get corroded, even if they’re in the cab. “We did one where there was actually ice in the cab that had melted once it warmed up,” he said.
Voltage issues can be the culprit as well. With the key on, for instance, the ECU will send voltage to the sensor but if there is an open circuit or short in the wiring, it will shut off. There is a tendency, Screeton noted, to confuse that with a bad ECU when it’s actually a harness going from the ECU to the central bank. In reality, it didn’t see the sensors, so it cut the power.
“When it comes to voltage issues, typically, what you’ll see is a timeout fault,” Screeton added. “What you really have is a circuit issue in a chassis wiring, which means it’s not getting any data from the sensors. Most of the time with sensors, we haven’t seen any systemic issues with the components. Other than calibration issues, it’s mostly chassis wiring issues, not sensor issues.”
Listening to drivers
Daryl Bear, lead engineer and COO of MVT Solutions (MVTS), a subsidiary of Mesilla Valley Transportation that provides technology testing services for fleets and manufacturers, has seen an increasing number of issues with malfunctioning ADAS technologies. He raised his concerns at a recent TMC meeting and was not surprised to hear other fleets were having the same issues.
“We have seen a variety of problems with forward-facing radar that have to do with reliability and interference,” Bear explained. “The least extreme consequence is inoperative cruise control; the worst case is brake lock-up.
“We’ve also seen issues with steering-assist systems designed to keep vehicles in the lane,” Bear continued. “Drivers complained they were fighting the system, and during one of our fuel economy evaluations involving trucks from three different OEMs, we saw it firsthand. It was a windy day and the next day the driver in the truck equipped with that technology was exceptionally tired and had very sore shoulders, and this was someone who was used to hard work.”
For its part, MVTS is using its advanced data acquisition equipment to provide OEMs with information they can use to make these systems more reliable and eliminate issues that lead to costly time in the shop. “We understand that many of these systems are still relatively new and are getting better every year,” Bear added. “But we also believe that driver complaints and issues are worth listening to.”
With nearly 9,000 tractors equipped with some of the latest ADAS technologies, Werner Enterprises finds that keeping the devices calibrated is one of its biggest service challenges.
“Many of these systems have radar-based sensors in the bumper and cameras in the cab,” said Ben Murphy, associate VP of equipment resources at Werner. “They need to be rugged and rigid to withstand the stress associated with rolling down the highway.
“Understanding how to react if one of the systems is out of sync is essential,” Murphy continued. “Buy-in from drivers and including them during the testing and validation processes is important when you decide to start using ADAS technologies. At the same time, they need to understand the importance, from a service perspective, to provide feedback about notifications they receive in the cab.”
A key part of the service process for Werner is an alert system that is based on exceptions. “It is unrealistic to scroll through data for all these trucks daily to find unique examples of notifications, so we look to manufacturers to provide exception-based reports,” Murphy said.
Stocking up on parts
One of the biggest challenges Werner currently faces is the need to have inventory on hand, and in the right locations, for repairs. To address supply chain issues, the fleet works ahead with its providers to understand their needs and have the necessary parts available. This mutually beneficial partnership with manufacturers also allows the ability to make regular upgrades to diagnostic software over the life of the technology.
A solid vendor network is important as well. “We can’t solely rely on our network of company shops because some of our trucks may not reach one of those facilities when a service event or repair is needed,” Murphy pointed out. “A partnership between our shops, third-party service providers, and manufacturers enables the accurate diagnosis and repair of technology issues in the least amount of time and with fewer obstacles.”
Simplification and consistency also play a significant role. “We are focused on step-by-step troubleshooting that starts with basic electrical and communication issues,” Murphy said. “We also take a cradle-to-grave approach in order to effectively maintain these technologies over their life span and strive for uniformity by not specifying many variations.
“As ADAS and other safety technologies become increasingly integrated, we are continually laying the groundwork for upcoming enhancements,” he added.
There’s a general underestimation about the level of activity necessary to maintain technology, according to Deryk Powell, president and COO of Velociti. “If you ask most fleets, they’d think the numbers are low but in 2021, among the more than 700,000 systems we monitor through our VeloCare technology health monitoring and repair service, 19.4% required some level of support.”
In 2021, 24.4% of the service calls for onboard cameras made by Velociti were due to accidental damage or tampering. Among those, broken windshields accounted for a significant percentage of the repairs. Another 20% resulted from needing to remove the devices from retired or wrecked trucks. Next on the list were the rapidly growing number of user devices and driver apps, which accounted for 9.6% of service needs. That number, Powell noted, doubled from 2020.
Most important is a proactive system that monitors connected devices on vehicles and uses that information to maximize uptime of technology solutions. Introduced in 2012, Velociti’s VeloCare Program combines technology health monitoring, field repair services, a tech support call center, and inventory management services for electronic logging devices, vehicle telematics systems, and in-cab video safety solutions.
“Fleets invest in ADAS and other technologies to improve productivity, efficiency, safety, fuel economy, driver satisfaction, and customer service,” Powell stated. “When you have a reactive approach, there’s an undetermined amount of time between a failure, its discovery, and then repair. When a technology is offline, it negatively impacts your return on investment, which can also be compounded if your in-house service operation doesn’t have the resources it needs to work on those systems, especially when the market for technicians is tight and keeping up with core maintenance needs is a big challenge.”
Another thing that can erode the value of a technology and extend an ROI is the current uncertainty with the supply chain for parts, especially electronic items. Centralizing that effort with a service provider can eliminate the need to purchase and store more inventory than in the past, Powell noted. That maintenance partner can also supply repair kits.
Setting up a PM schedule
Measurable value can also be realized when you address speed of service.
“It starts with proactive monitoring, which leads to more effective troubleshooting, but also includes the need to take a look at bringing the repair to the vehicle when it comes to onboard technology,” Powell said. “The cost of waiting until the driver reaches a shop can be ridiculously expensive. Taking advantage of opportunities to have the technician go to the truck can lead to the lowest cost.”
A preventive approach to onboard safety technology works well for getting the most out of an investment and for getting the output you need, noted Adam Kahn, president of Netradyne, a provider of vision-based safety camera solutions.
“In some cases, it can be as simple as putting camera lens cleaning on a set schedule,” Kahn said. “Most people routinely make sure their cell phone camera is clean, but fleets don’t always stop to think that their in-cab devices aren’t always operating in a clean environment.”
Kahn also points to the value of over-the-air software upgrades that can keep electronics-based systems functioning properly. Unlike the traditional practice of finding vehicles and installing updates when they can be accessed, often during other service intervals, connectivity through 4G and now 5G modems can speed up the process significantly.
“There is also a need for training in basic electrical, data, and communications systems,” Kahn added.
Maintenance management software can play a role in preventive and predictive service practices for ADAS and other safety technologies.
“You can use asset management systems like our TMT Fleet Maintenance and TMT Service Center software to track repetitive repairs and find causes and solutions,” said Dave Walters, senior solutions engineer at Trimble. “Analyzing data by component, system, and even location can be considered a part of normal maintenance today.
“You can eliminate issues with these technologies by adding to DVIR and inspection checklists to validate their proper function,” Walters continued. “Especially when it comes to components like sensors and cameras that live outside the cab and need to operate in severe conditions, you need to be sure they are properly protected and positioned.”
Walters went on to say that if onboard technologies are connected to a vehicle’s electronics and telematics systems, there are mobility products that can be configured to send alerts with early notifications. From there, diagnostic steps in a maintenance management system are a logical source for identifying problems.
“Effective technology maintenance begins with not being reactionary,” Walters stated. “The goal is to not have issues occur by catching things that could have been prevented, especially if they cause a breakdown. In those cases, you have unnecessary downtime and lost revenue that you can’t recover.”
About the Author
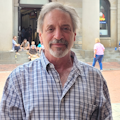
Seth Skydel
Seth Skydel, a veteran industry editor, has more than 36 years of experience in fleet management, trucking, and transportation and logistics publications. Today, in editorial and marketing roles, he writes about fleet, service, and transportation management, vehicle and information technology, and industry trends and issues.