Averted disaster highlights importance of fifth wheel and kingpin maintenance
Just how important is the coupling between a tractor-trailer’s fifth wheel and kingpin? Last March, Sydney Thomas, a 26-year-old driver for Sysco, found out it’s the difference between life and death. As she was driving northbound on the narrow Clark Memorial Bridge that connects Louisville, Kentucky to Jeffersonville, Indiana, a driver going southbound wildly swerved his pickup into Thomas’ lane. The pickup crashed into her semi’s front end and disabled the steering. In an instant, she lost control, and her semi careened over the oncoming lane and through the guardrail. The steel bridge’s truss beams caught the back end of the reefer trailer, suspending the battered day cab over the Ohio River.
All that seemed to keep the truck, and Thomas, from plummeting around 60 ft. to the cold waters below was the trailer kingpin nestled firmly into the truck’s fifth wheel.
Thomas recalled the harrowing event to Louisville news station WBIR: “Well, this is it…I really thought I was about to die,” she thought in the moments immediately after the collision.
But the kingpin held onto the fifth wheel (specifically, the Fontaine Fifth Wheel No-Slack 6000 Series top plate) for another 45 minutes until firefighter Bryce Carden rappelled down, grabbed her through the window, and pulled her to safety.
“Sometimes I pray, and I don’t think God is listening…but he was that day,” Thomas said.
Sysco CEO Kevin Hourican agreed, surmising “a higher power” must have been involved to keep the kingpin from popping out.
“The fact that the pin stayed engaged inside that fifth wheel is a miracle,” he said to another local news outlet, WAVE.
The feel-good story went viral, and rightly so. For some, the fire department’s heroics restored their faith in humanity, and for others, it confirmed their faith that a higher power watched over them. But for anyone involved in trucking, it should provide one additional thing.
“It just goes to show the importance of that connection,” remarked Troy Widtfeldt, director of sales and marketing at Badger Product Group, a manufacturer of fifth wheels. “You never know when the strength of that locking mechanism between the truck and the trailer might save your life.”
This is why spec’ing the right components is so important.
In the case of Thomas’ truck, the connection was fortified by the 6000 Series’ self-adjusting lock technology, which includes an adjustment rod that is in constant contact with the locking wedge during operation. It also reduces wear and tear on the kingpin to ensure a reliably snug fit for many years.
Paige Petroni, president of Fontaine Fifth Wheel, noted that although the 6000 Series “was not designed for the extraordinary forces involved in this type of accident,” how it performed on that March day over the Ohio River is a testament to the engineering and manufacturing teams’ prowess.
But it doesn’t end there, as the fleet’s technicians probably deserve some praise, too.
“Even the best engineered product needs to be properly maintained to OEM specifications,” Petroni noted.
While Thomas’ scary situation is the most extreme example of this, every day drivers head out with fully loaded trailers—all stuck together by the fifth wheel and kingpin. And it’s management’s responsibility to their drivers, customers, and everyone on the road to get it right when spec’ing, maintaining, and inspecting these coupling devices.
After all, emergency responders and miracles aren’t always around when you need them. That means fleet managers must be the connector to bridge it all together. You’ll also see some uptime and cost reduction benefits, which aren’t life or death, but the key to success.
With these tips, we’ll help make sure you won’t need divine intervention to stay connected.
Greasing done right
The fifth wheel not only has to keep the tractor and trailer together, but do so in a way that doesn’t impact other parts and increase wear and tear on systems such as the steering system or steer tires, Widtfeldt said. Plus, failure to keep your fifth wheel slick is “one of the main causes of semi-truck trailer jackknifes in the winter,” he added.
Many of these issues stem from simple neglect of proper fifth wheel maintenance, and sometimes, all you need is a little grease.
“The number one maintenance item is just making sure it’s properly lubricated, because obviously it’s metal-on-metal contact and you’ve got a lot of weight, upwards of 40,000 lbs., sitting on a plate that’s connected to the truck,” Widtfeldt explained. “That’s a rotational point, so the friction forces are pretty high if it’s completely dry or it’s not sufficiently lubricated.”
Coincidentally, perhaps the most common mistake when it comes to fifth wheel maintenance is a lack of proper greasing technique, and as Widtfeldt points out, everybody has different opinions on how fifth wheels should be properly greased. There are some methods, however, that are downright ineffective.
“A lot of times there’ll be guys that essentially ‘silly string’ grease on the top of the fifth wheel plate, and then once the driver backs under the fifth wheel, it just gets scraped right off,” he explained, “so there’s a lot of waste.”
Tony Ryan, technical services manager with SAF-Holland, discussed a similar pattern.
“A lot of customers that we see now in the industry will grease the top of the fifth wheel, but that’s only the contact patch between the upper coupler and the fifth wheel itself,” he said. “Where the magic happens is the mechanism underneath, and they forget to lubricate that.”
The lack of lubrication in the mechanism underneath can result in a few different issues, as it “slows down the reaction time of the mechanism and can lead to miscouples, or, more importantly, it makes the handle a lot harder to pull, which can lead to driver injuries,” Ryan added.
The most important areas to lubricate are any contact points or movable parts, like the two jaws and locking mechanism, the yoke tips, and the handle. The most critical point, however, is the cam plate, which contains rollers and a pivot point. According to Ryan, this is the area where problems occur most often.
“Countless times throughout the year, lots of customers say, ‘I’ve got a fifth wheel and it’s not working; we took it off, we need warranty, or I bought another one to replace it,’” the technical services manager detailed. “And we’ll come up and lubricate it, cycle it three or four times just to make sure the lubrication gets through all the points, and it suddenly works 100% every time.”
This may be a nuisance for the OE technicians, but costly to the fleets.
“There are a lot of customers out there affecting their own ROI by not doing proper maintenance,” he said.
And while insufficient lubricant might be the main issue, overdoing it can be just as problematic.
“We do see a lot of over-greasing of fifth wheels, especially in winter months when it’s really cold outside,” noted Robert Marsh, VP of truck product sales, OEM and fleet, Jost. “That can cause problems with the locking mechanism on the fifth wheel.”
And worst of all, sometimes it just doesn’t get done at all.
“It’s a messy job, and nobody wants to do it,” Widtfeldt remarked.
Maintenance missteps
Despite their importance in everyday truck operation and their solid construction, fifth wheels are
not immune to problems, and many of the issues that could arise are due to common misconceptions and mistakes many technicians make while maintaining fifth wheels and their components.
“They are generally very robust,” Ryan said. “They don’t have a lot of wear and tear on the mechanism and the components on it. They last for a very, very long time.”
While made to last, fifth wheels don’t often ‘fail’ on their own. Improper practices and bad habits are to blame for most fifth wheel issues encountered by drivers and technicians.
“It’s more a case of the drivers thinking they have failed because they dropped the trailer,” Ryan reiterated.
And if a trailer is dropped, there are sometimes clear indicators of what may have caused it. A frequent culprit is improper coupling.
“If they haven’t coupled correctly, quite often, you’ll see telltale signs of marks over the top of the fifth wheel, and the kingpin’s gone over the front skirt,” Ryan explained.
He noted that drivers will often perform a tug test, which entails engaging the trailer brake and easing forward slightly after coupling to put tension on the connection. This can sometimes catch an improperly coupled or locked kingpin. But not always.
“They’ll do a tug test. The kingpin will be up against the front of the fifth wheel, and it will pass the tug test,” he detailed, “but they’ll literally go out the driveway and the first turn they hit, it sweeps around the front skirt and you can see there’s a telltale mark.”
Another issue is lack of adjustment.
“We recommend you don’t adjust the fifth wheel on a trailer,” the technical services manager cautioned. “You should adjust it on a lock tester, because a trailer can have a worn kingpin, then suddenly you get a brand new kingpin on a different trailer and it becomes over-adjusted.”
Another common error technicians make is over-repair, Marsh pointed out.
“I think that a lot of times, fifth wheels are able to be repaired by replacing a few components instead of replacing an entire top plate or all the components in it,” he said.
Ryan agreed that the solution is often simpler than it may seem.
“The main thing that we recommend is ‘clean, lubricate, and adjust,’” Ryan concluded. “That fixes the vast majority of any issues that we’ve seen.”
Inspections and PM
Proper greasing and repair of the fifth wheel is crucial, but these skills only go so far without regular inspections and preventative maintenance. Keeping an eye on fifth wheel components—and knowing what to look for when checking for wear—can help catch issues before they get worse.
According to Bruno Scuracchio, VP of OEM sales and engineering at Sampa USA, “the two main durability issues that you can have with a fifth wheel are basically wear and oxidation,” or corrosion.
Luckily, both of these issues can be mitigated, or at least identified, through preventative maintenance and inspection. While most fifth wheels have a similar timeline for regular preventative
maintenance, inspecting and maintaining as per service manuals for the fifth wheel in operation is always a best practice.
For example, with SAF’s FW35 fifth wheels, the recommended preventative maintenance inspection interval is an initial check for operation at 30,000 miles or three months, and then a more in-depth inspection every 60,000 miles or six months.
“Every six months we recommend a thorough clean, check for any damage, broken or missing components, cracks, whatever,” explained Ryan, “and then a complete brand-new lubrication across it.”
This lines up with six-month seasonal maintenance in spring and fall, which he emphasized is especially important for northern states, in that a thorough spring PM can get rid of salt and other build-up from the winter months that could corrode fifth wheel components.
Brian Bowen, aftermarket sales manager for Fontaine Fifth Wheel, outlined a similar PM schedule for their fifth wheels, explaining that the two most important times to clean them are going into and coming out of winter.
Coming out of winter and “into the spring, you want to fully clean your fifth wheel off and do a re-lubrication, so it gets all the dirt and grime off the top of the fifth wheel and where the bushings are. And then going into winter, you want to winterize your fifth wheel,” he detailed.
One of the most effective ways to prevent serious fifth wheel issues, however, is to simply give them a once-over. Awareness and proper inspections can often reveal any potential problems before hitting the road.
Key areas of inspection are the main wear points, said Troy Widtfeldt, director of sales and marketing at Badger Product Group, a manufacturer of fifth wheels. He highlighted the throat and jaw area, or point of contact between the kingpin and the fifth wheel itself, along with the locks that go around the kingpin. He recommended including these points in a pre-trip checklist.
The kingpin should also be inspected every three months or 30,000 miles, according to SAF-Holland. Check for any bumps, valleys, or warping, as these can result in damage to the top plate and reduce lock life.
The good news is that indicators of wear can usually be detected before they become more
serious—both through visual inspections and listening for unusual sounds on the road—given that a driver or technician knows what to look for.
Widtfeldt offered an example: “A clunking noise on braking or acceleration can signify that there is play in the locking jaws that hold the kingpin to the fifth wheel. Either the lock jaws need to be adjusted, or the jaws or fifth wheel itself need to be rebuilt.”
About the Author
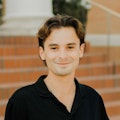
Lucas Roberto
Lucas Roberto is an Associate Editor for Fleet Maintenance magazine. He has written and produced multimedia content over the past few years and is a newcomer to the commercial vehicle industry. He holds a bachelor's in media production and a master's in communication from High Point University in North Carolina.