There comes the time when it makes sense to modernize a maintenance facility and make improvements in safety, productivity and the environment. Shop equipment wears out, the equipment needs to change and new, improved equipment is constantly coming to market. Vehicle mix changes, and that results in adjustments to vehicle service and repair requirements. Not having enough space for all shop activities can severely impact productivity.
A shop update is the ideal time to consider all of the things that will increase both shop and technician productivity. This includes designing proper space allocation of tools, supplies, equipment, fluids, monitors and support services.
A maintenance facility requires order and discipline, says John Dolce, fleet specialist for Wendel, a nationally recognized architectural and engineering firm well known for its Transit Oriented Development initiatives, bus maintenance and multimodal facility designs. Almost every act needs to be sequenced for efficiency and to maximize productivity.
With good planning, a shop can also be “greened” by embracing environmentally-friendly architecture and reducing energy consumption and carbon dioxide emissions, he adds.
Because of funding limitations and priorities, organizations tend to make do with their mature facility by adapting staff and space to meet the immediate needs, but that can come at the cost of productivity and energy loss, Dolce says. With stimulus money now available for emissions reductions and a heightened focus on environmental stewardship, organizations should begin to look for opportunities to fund, build, expand or upgrade their facilities.
VITAL CONSIDERATIONS
The first step is to decide whether to expand a present shop, reduce its size, relocate to another facility or build a new shop. Architect and engineering firms are experienced to efficiently and cost-effectively assist with these efforts, says Dolce.
Among the chief considerations are space and technician requirements. Not having enough space or technicians can be just as bad as having too much space and too many technicians because these are capital expenses, he points out.
Energy use is another key consideration in greening a shop, says Dolce. One way to reduce energy consumption is to, as shop equipment wears out, replace it with newer, more energy-efficient units that use less energy. This will result in a savings on utilities and fuels and will reduce carbon dioxide emissions which benefits the environment.
By shop equipment, he means not just tools and machinery like lifts, cranes, washers, lathes, steamers, generator, welding equipment, parts cleaners and electronic test equipment. There is also facility management equipment and systems, such as heating, ventilating and air conditioning equipment, fans, ventilators, pumps, transformers and lighting.
ENERGY COSTS
An effective energy management plan begins with data collection and analysis, after which energy savings measures can be put in place, then monitored and controlled.
Dolce advises shops to perform an energy audit. Basically, an energy audit is an assessment of a company's energy use throughout its operations. The audit will identify opportunities for energy savings, energy efficiency improvements and possible alternative energy sources.
An energy audit shows a shop how to reduce carbon emissions by reducing its electrical draw, he says. This in turn will reduce utility generation, and that reduces fossil and gas usage. Changes can be as simple as replacing light bulbs with more efficient ones or as complex as replacing electrical needs with solar or wind technology by rehabbing present facilities with cost-saving technologies.
“It is a complex process but not overwhelming,” says Dolce.
ENERGY EFFICIENCY
Immediate energy savings can be achieved by simple practices. For example, moderating summer and winter thermostat settings can make a real difference. Heating, ventilating and air conditioning are usually a building’s biggest energy costs.
Energy conservation can also be accomplished by automating and controlling building equipment and systems, which promotes more active energy management.
Using good-quality, insulating windows and place windows to allow daylight to reduce lighting use, while providing solar warmth in cool weather. Studies have shown that natural lighting has a positive impact on productivity and well-being.
OTHER MEASURES
“Green roofs,” where a vegetative layer is grown on a rooftop, provide shade and remove heat from the air through evapotranspiration, reducing temperatures of the roof surface and the surrounding air. According to the U.S. EPA, on hot summer days, the surface temperature of a green roof can be cooler than the air temperature, whereas the surface of a conventional rooftop can be up to 90 degrees F warmer.
In-floor heating systems reduce utility costs and help improve employee comfort. Solar photovoltaic arrays on the roof can provide on-site renewable energy.
There are also a number of things than can be done for water efficiency. Dual plumbing can be designed to use recycled water for toilet flushing. Wastewater can be minimized by using ultra low-flush toilets, low-flow shower heads and other water-conserving fixtures.
For building construction, passive design strategies can dramatically affect building energy performance. These measures include the building shape and orientation, passive solar design and the use of natural lighting. Using sustainable construction promotes resource conservation and energy efficiency.
ASSORTED BENEFITS
U.S. Green Building Council (USGBC) has developed the LEED (Leadership in Energy and Environmental Design) green building certification program. It provides third-party verification that a building was designed and built using strategies aimed at improving performance across all the metrics that matter most. These are energy savings, water efficiency, CO2 emissions reduction, improved indoor environmental quality and stewardship of resources and sensitivity to their impacts.
The USGBC is a non-profit organization dedicated to sustainable building design and construction.
While a green maintenance facility may cost more up front, a number of economic benefits come from shop greening. Among them: lower operating costs, improved productivity and optimized life cycle economic performance.
Other paybacks of green buildings are not easily quantified. Things such as improving occupant health and comfort, and reducing pollution and landfill waste are less tangible green building benefits.
VARIOUS PATHS
The greening of vehicle maintenance facilities can be approached from three angles: maintaining green shops, maintaining green fleets and maintaining alternative fuel/advanced technology equipment, says Suzanne Seivright, manager of regulatory affairs and compliance at Valley Power Systems, a member of the WheelTime Network. “All three offer benefits in future opportunity and new revenue streams, while also requiring investment of resources and time.”
WheelTime is a professional truck care and service network that offers service support through more than 30 training facilities and nearly 200 service centers located across the U.S. and Canada.
She offers the following considerations for those shops getting ready to go “green.”
- Maintaining green shops - Green fleets will want to align with green shops and knowledgeable resources, says Seivright, who has extensive experience in the environmental field, working in both the public and private sectors.
“Technicians with experience in hybrid-electric, natural gas and advanced diesel engine and emissions systems may be hard to come by at these early stages of technology adoption,” she says. “Training and retaining factory-trained technicians that specialize in alternative fuel and advanced technology equipment will be key. Once you have them trained, you may find demand for onsite training of customer shop personnel adds extra value to your relationship and extra revenue for your shop.”
Technologies are coming on strong, she notes. In some cases, these are being mandated for use in certain states like California, and those policies are expected to spread to other states in the near future.
- Maintaining green fleets - Longevity and functionality of emissions control technologies post installation is directly related to proper engine maintenance, says Seivright. Operations and maintenance personnel need to be trained so they are prepared for their role in maintaining after-treatment systems. “U.S. EPA SmartWay Approved idle reduction technologies will be a mainstay of green fleets going forward,” she says.
- Working with alternative fuel fleets - In addition to tracking performance and benefits of extended life treatments and green additives such as oil, ethanol and biodiesel, green shops will be called upon to help fleets navigate federal, state and local funding opportunities that promote the purchase of alternative fuel vehicles, Seivright says.
“Gearing up for this demand takes a new expertise in grant writing, as well as knowledge on compliance procedures and air district regulations related to new vehicle purchases, retrofits and repowers. While facilitating workshops and local air quality board collaborations takes time, resources and investment, we (Valley Power Systems) find the commitment aligns our business with the needs of fleet customers that are going green.”
10 steps to energy savings in compressed air systems
1. Turn off compressors when not needed. A 100-hp compressor can cost $75,000 per year in energy costs (based on 8,760 hours at 0.10 per kWh).
2. Identify and fix air leaks. Studies show that anywhere from 25 to 50 percent of all compressed air generated is wasted to leaks.
3. Eliminate inappropriate uses of compressed air. Using compressed air for blow-off is not only wasteful, it can be dangerous as well. Using air over 30 psi for blow-off is an OSHA violation.
4. Apply proper controls to multiple-compressor systems. Master system controls maintain a stable system pressure, ensure only the needed compressor units are brought online and that they are operating at peak efficiency.
5. Ensure piping and storage are adequately sized. Undersized piping will increase pressure drop in the system.
6. Change your filters routinely to eliminate pressure drop. Every 2 psi in pressure drop costs 1 percent in compressor horsepower efficiency.
7. Use automatic, zero-loss condensate drains. Capacitance sensor operated drain traps don't need to be monitored. They discharge only condensate, not valuable compressed air.
8. Apply variable speed drive compressors where appropriate. Variable speed drive is not a one-size fits all solution. But if you have varying demand, it can save thousands of dollars on electricity costs each year.
9. Reduce operating pressure to lowest possible setting. For every 2 psi reduction in system operating pressure, 1 percent in compressor efficiency is saved.
10. Recover waste heat from coolers. A 50-hp compressor rejects heat at approximately 126,000 Btu per hour.
Source: Kaeser Compressors
?
Considered trying biobased products?
The myth among many fleet maintenance managers is that non-hazardous performance fluid alternatives can’t work in their tough environments.
“In reality, today’s biobased cleaners, degreasers and lubricants are formulated for high-performance and designed to work alongside traditional, petroleum-based products without compromise,” says Mike Guggenheimer, vice president of business development, RSC Bio Solutions, a company focused on providing high-performance chemistries that are safe, non-hazardous and environmentally responsible.
As fleet maintenance shops choose to “go green” with environmentally safe fluids, shops can become safer for employees and reduce many of the risks associated with using harsh chemicals and acids, he adds.
Biobased products, designated by the Secretary of Agriculture, are commercial or industrial products (other than food or feed) that are composed in whole, or in significant part, of biological products or renewable domestic agricultural materials (including plant, animal and marine materials) or forestry materials.
“Biobased maintenance fluids work at the same high level as traditional maintenance fluids,” says Guggenheimer, “but offer a greater level of safety to the people handling them.” If spilled, biobased products are less likely to irritate an employee’s skin, and they are safer to breathe in during use.
While biobased products add value by reducing the risk of on-the-job safety hazards, they can also reduce risk in other areas. In many shops, a hazardous spill puts a company at risk for incurring fines or an expensive clean-up job.
For example, Guggenheimer says if workers are using petroleum-based cleaners in a truck bay and chemical runoff goes down the drain or enters nearby soil and groundwater[e1] , the company could be fined for ecological damage. “This risk is dramatically reduced when a shop chooses readily biodegradable and non-hazardous solutions.”
COST SAVINGS
Another positive effect of biobased products is improved endurance.
“Using a solution such as Gunk Powered by SafeCare Universal Parts Washing Fluid in a parts washer with a waste oil skimming system allows the product to perform longer in the equipment because the fluid stays cleaner longer,” says Guggenheimer.
“In addition, many oil recycling programs will examine the content of waste oil for hazardous materials that might contaminate its process, and using non-hazardous cleaners can help these oils be approved for recycling.”
It’s also important to consider that many costs associated with using traditional cleaners and degreasers are eliminated when a maintenance shop switches to biobased alternatives, he says. Chemicals labeled as “hazardous” require special vessel storage, while biobased products don’t have the same storage requirements. Plus, ordering biobased products offers more shipping options since they can be shipped by air and the cost to ship non-hazardous fluids is lower.
“Biobased solutions have become an effective alternative to the typical acids and harsh chemicals commonly used by the fleet industry’s maintenance teams every day,” Guggenheimer says. “These new products can provide benefits in the areas of safety enhancement and risk reduction without sacrificing performance or cost.”
[e1]One word
?
How to conserve shop resources
Incorporating green processes is not only good for the environment. It can be good for a shop’s bottom line. Conserving resources and cutting down on waste saves money.
No matter the size of a maintenance shop, there are simple things that can be done to go green.
One green method is to better manage high-use shop supplies, says Jerad Tuxen, a fleet industry sales specialist for industrial supplier Fastenal. By way of example, he cites industrial vending systems that dispense items such as gloves, safety glasses, ear plugs, rags, grease, tape, etc.
Along with providing a lean, controlled flow of product to the point-of-use, such systems also provide a number of green benefits, Tuxen says. Among them is automated reordering. This not only requires no paper, ink or toner, it also eliminates stock-outs and rush orders, resulting in fewer deliveries and, thus, less fuel consumption and lower carbon emissions.
Industrial vending systems can also reduce technician “energy use,” he adds. By placing the machines near the point of use, and with product immediately available, walking and waiting time at the parts window is minimized.
An added benefit is that some systems, like Fastenal’s FAST 5000, track vending usage via employee ID card or key code, allowing limits to be set on what, and how much, employees can access. This reduces product consumption so that less material ends up in landfills.
Reduced consumption also means reduced spending, notes Tuxen, so it’s an opportunity to be green and save green.
?
Shop requirements for natural gas vehicle maintenance
In April 2010, the San Bernardino Associated Governments (SANBAG) Board selected Ryder as its fleet partner in a groundbreaking heavy duty natural gas truck rental and leasing project in Southern California. Ryder will use $19.3 million in state and federal American Recovery and Reinvestment Act of 2009 (ARRA) funding secured by SANBAG to implement the project.
This is the first time that natural gas trucks will be deployed into a large commercial truck rental and leasing operation, says Scott Perry, group director, vehicle supply management, Ryder System.
As part of the project, Ryder is introducing more than 200 heavy duty natural gas powered trucks that will be deployed into Ryder’s Southern California operations network, where Ryder’s customers will be able to access them through short-term rentals, long-term leases or through Ryder’s dedicated logistics services. When fully implemented, the project will displace more than 1.51 million gallons of diesel annually with 100 percent domestically produced low-carbon natural gas, Perry notes.
To support the project, Ryder will construct two new natural gas refueling stations and will maintain the vehicles at three strategically located maintenance shops within the region. Modifications are being made to each existing Ryder maintenance shop to ensure the facilities meets stringent industry and government safety standards for natural gas vehicle maintenance.
CERTAIN REQUIREMENTS
One of the first steps to ensure a shop is equipped to service heavy duty natural gas vehicles includes a number of upgrades to the facility’s electrical system, says Perry. For example, electrical systems must be 18 inches above the floor and 18 inches below the roof. All fixed electrical equipment and wiring must be changed to comply with a Class 1, Group D, Division 2 area classification per Article 500 of National Fire Protection Association 70: National Electrical Code.
Gas fire heaters must be replaced with indirect heaters to prevent ignition in the event of a gas release, he says. Gas detection systems must also be installed at floor and roof levels and arranged to provide an audible and visual high level (HL) alarm at 25 percent of the Lower Flammable Limit (LFL) and an audible and visual high-high level (HHL) alarm with emergency shut down of non-emergency electrical equipment at 60 percent of the LFL.
Alarm settings are determined according to national standards, as well as by the local authority having jurisdiction - normally the local fire department - which may require the alarms to be set slightly lower.
In addition to physical and system upgrades, Perry says several protocols must also be put in place in the facility. Rolling (overhead) doors must be left open when natural gas vehicles are inside the building. It can also be arranged to have doors open upon activation of a high-high level alarm.
Office doors, or other doors into the shop, should remain closed when natural gas vehicles are inside. It’s also important to maintain a slight positive pressure in offices which open into the shop to prevent vapors from traveling from the shop area, he says.
Ventilation systems must be set to arrange for ventilation to achieve 12 air changes per hour continuously, or at a high level alarm in the event of a gas release with air supply and exhaust points at the roof level and the floor level. He notes that in cold climate areas it is often necessary to have two-stage ventilation levels so that building temperatures in winter can be maintained at comfortable levels for employees, except during a release.
Automatic sprinkler protection may be required and should be considered for buildings which are not already equipped, Perry adds.
Ryder’s professional maintenance technicians are also receiving extensive, specialized training on the maintenance and repair of heavy duty natural gas vehicles, as well as the safety protocols that must be followed when natural gas vehicles are in the shops.
?
About the Author
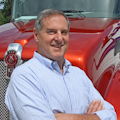