Vehicle maintenance operations are becoming more environmentally conscious. Along with using more fuel-efficient and less polluting vehicles, green initiatives are being instituted to embrace environmentally-friendlier architecture, supplies and attitudes. This includes all kinds of activities.
Shops are establishing green policies to change to the behavior and attitudes of workers; ensuring that hazardous materials are properly used, stored and disposed; using biodegradable cleaners for spills; keeping parking lots and service bays clean to prevent toxic waste from getting into storm drains; recycling fluids and wastes; taking extra precautions to prevent storage receptacles from leaking hazardous materials; making changes to save water and use energy more wisely; upgrading or building new facilities using green construction to create structures using processes that are more resource-efficient throughout a building’s lifecycle; and much more. Here is a look at what some organizations are doing.
Advanced Maintenance, Wilmington, NC — Since its founding in 2000, this full-service fleet maintenance company “has had a recycle and reuse effort that is taught from the top of our company down to our mechanics that are on the front line,” says chief operating officer Chris P. Holman. “We reclaim all fluids and dispose of them through a program with Safety-Kleen. We reuse uncontaminated antifreeze and refrigerant products.”
All aerosol products used are non-chlorinated. Any repair parts that don’t have a core are separated by type of metal and recycled. Oil mats are also recycled.
“We make a clean profit from our waste,” Holman says, “which helps us keep our costs down, allowing us to pass along lower pricing to our customers without sacrificing quality.
“Being green is a no brainer. Why throw out something when you can make money from it or use it again. The key is teaching all who come in contact with products, the benefits and the need to follow proper recycle and waste procedures.”
Arizona Department of Transportation (ADOT) — More than four year ago, environmental engineer Robert Trapani joined the ADOT and was charged with incorporating environmentally-friendly best management green shop measures into the agency’s fleet vehicle service and repair shops.
At the core of this green effort is the Equipment Services Best Management Practice (BMP) Manual, conceived to reduce pollution and improve and enhance operational capabilities in an environmentally-sensitive manner. The manual is readily accessible to all technicians on the shop floor and on desktop computers.
“Most regulations tell you what you have to do to be in compliance, but they don’t explain how to do it,” says Trapani. “ADOT’s best management practices are proven shop floor guidelines and methods that have helped us not only get into compliance and stay there, but moved our shops to the next level by changing from pollution-generating behaviors to pollution-prevention behaviors.”
Among the numerous matters addressed in the BMP Manual:
Prescribed methods for handling and disposing and recycling of waste materials such as used oil, oil filters, coolant, tires, scrap metal and batteries.
Using water-based parts cleaning and brake washers in place of spray solvents.
Having a fully enclosed waste transfer system for waste liquids.
Providing secondary containment for hazardous materials storage indoors and outdoors away from storm and sanitary sewer drains.
Making emergency spill kits available in service bays and chemical storage areas.
Using drip pans in outside areas to control fluid leakage under vehicles.
Having no open drains or sealed floor drains that lead to storm drains and sanitary sewers.
Prohibiting vehicle washing, or sending vehicles to a commercial washing facility with a closed loop water recycling system.
Posting “Do Not Discharge Chemicals Down Sink or Drain” warning signs above shop sinks.
Implementing a dry shop spill cleanup method that recycles spilled wastes.
Performing environmental awareness and pollution prevention training.
Recycling office paper.
Adjusting shop design, procedures and management practices.
Selecting less hazardous and toxic products.
Using refillable spray bottles instead of disposable aerosol cans.
Maintaining an electronic database of vehicle service and pollution prevention products and services,
Making no discharges to sanitary sewer systems
Performing regular maintenance on heating, ventilation and air conditioning systems.
Using an industrial launderer for shop towels.
Another practical tool Trapani developed was the Self-Audit Environmental Compliance Checklist. “We use this as a guide to find numerous opportunities through incremental environmental improvements as a basis for continuing progress for all our shops statewide,” he says.
Each shop completes the comprehensive checklist twice a year. It is reviewed by Trapani who then meets individually with each shop supervisor to discuss the results, assist with any emerging issues and go over a list of improvement areas and recommendations to reduce any environmental impacts associated with shop operations.
Another of his initiatives was creation of the annual Environmental Green Shop Award. Designed to improve and encourage better environmental performance in all ADOT shops, the honor “recognizes the shops that are best at environmental compliance and protecting and enhancing the environment.”
Averitt Express, Cookeville, TN — A provider of freight transportation and supply chain management, its shops are using low-viscosity lubricants and engine oils which lower the frequency of maintenance service intervals, therefore producing fewer waste products, says Christopher Asberry, the company’s communications coordinator.
The shops are also capturing 100 percent of the Freon when servicing vehicle A/C units and recycling accordingly; recycling all used oil and oil filters; recovering and reusing antifreeze whenever possible; using only non-hazardous waste parts cleaners; using salvaged/remanufactured parts whenever possible; recycling all scrap metal created from in-house vehicle maintenance and body work; and eliminating aerosols by purchasing bulk chemicals.
“Being ‘green’ is sometimes simply a byproduct of working to be more efficient and or cost-effective, which Averitt has always tried to do in its shops,” Asberry says. “We really started focusing on being green, though, when we became a charter member of the EPA SmartWay Transport Partnership in 2004. Since then, we’ve made environmental sustainability a top priority in everything we do.”
The SmartWay program’s goals are to reduce the impact of freight transport on the environment and to help EPA partners see the rewards to their business.
B-Line Lube Centers, Odessa, TX — With three shops in Texas that service more 150 Class 8 trucks each day, the company works to reduce its environmental footprint through a variety of measures, says owner Craig Freeman. Among other things, it uses waste oil to heat its shops, turns shop lights off during the day, recycles filters and oil, stores all invoices electronically, sends paperless statements via e-mail and accepts all forms of electronic payment. It is a registered waste oil collection site for do-it-yourself oil changes.
“The shops are designed specifically to do maintenance which allows us to contain most of the mess rather than have to clean it up off the floor with solvents and soaps which would then be washed into the drain,” he says.
The company is starting to replace lighting with much more efficient LED lamps that Freeman expects will cut electrical consumption by as much as 75 percent at a cost that will amortize in about 5 years.
Blaine Brothers, Minneapolis, MN — This provider of parts, service and towing to the transportation industry has found that “a big part of going green is using the latest technology to improve business operations,” says Michael Gray, controller. “There are economic benefits that go along with many of the environmental benefits.”
Some of its green processes “are a product of waste minimization efforts,” he says. “Many other areas are really a matter of economics.
“In-floor heat provides a better heat source for our shops when cold vehicles are pulled in all winter long. Retrofitting our shop lights to new fluorescent technology provides a brighter working environment with less energy consumption.”
Blaine Brothers, too, is retrofitting with new energy-conserving lights and will receive rebates from utility companies for installing them.
“Investment in computer technology allows us to be more efficient with resources too,” Gray says. “E-mailing invoices and statements saves paper and mailing costs. Customers also remit payment faster, increasing cash flow. Mechanics use a barcode gun to scan on and off of jobs. Their time is summarized by the computer system without needing time cards or manual entry.”
Parts flyers can be e-mailed instead of printed and mailed. The accounting system sends reports to PDF files for archiving instead of printing paper reports to put in boxes for storage.
The company recycles used oil, batteries, steal, aluminum, cardboard and paper. It privately labeled its own biodegradable truck wash soap. It reduced use of aerosol sprays by using refillable squirt bottles and uses parts washers with water and detergent instead of solvents that generate waste.
“Quite honestly, investing in these areas provides a cost savings that pays off in the long run,” notes Gray. He figures the greening efforts are producing monthly savings of $2,600 from recycling, $300 from in-floor heat; $150 from changed lighting; $300 from document archiving and $500 from barcode time entry.
Caledonia Haulers, Caledonia, MN — This food grade tanker carrier’s vehicle maintenance shops started recycling filters and recycling and burning waste oil for winter heat more than 10 years. It began a more concentrated greening effort a little more than a year ago. It joined the SmartWay Transport Partnership in April.
In addition to recycling and burning waste oil for winter heat, “the shop has moved to a virtually paperless computer system which saves huge on paper waste and printer inks - more than $1,900 annually,” says Linda Joy Vinson, maintenance manager. “We have started to take our damaged plastic bumpers and have them repaired to make good parts instead of scrapping them and adding them to landfill.”
Champaign-Urbana Mass Transit District (MDT), Urbana, IL — The district instituted green practices more than a decade ago, including beginning using soy biodiesel fuel and “stinger” system to keep air pressure up on its vehicles to reduce idle time by 5 to 7 minutes at start-up. Its maintenance facilities have been heated by a burner fueled by waste oil for more than 10 years and has been recycling for a dozen years.
“There is a systematic approach to environmentally-sensitive practices,” says MDT’s marketing director Jan Kijowski. “The maintenance team uses only green-certified cleaning supplies. There has been significant reduction in water use from the institution of a wash-only-as-needed policy for bus cleaning and installing low-flow water nozzles. There are plans to replace the wash bay with a unit that will employ water recycling.
Electrical consumption has been reduced by switching from fluorescent bulbs to LED lights and low-mercury bulbs, using motion detectors light switches and establishment of an if-not-needed-turn-it-off policy.
The MDT recycles virtually everything for which there is a recycling program: aluminum cans, plastic bottles, scrap metal, office paper, cardboard, antifreeze, Freon, printer cartridges, alkaline batteries, newspapers from incoming coaches and used oil filters. It recently purchased a fluorescent bulb crusher that captures and filters the mercury from these bulbs.
The district is in the process of upgrading its fleet with diesel-electric hybrid vehicles, Kijowski says. This summer its plans to install a geothermal heating and cooling system, a white roof which reflects sunlight and helps reduce energy use in hot, sunny weather and permeable pavers to reduce groundwater runoff.
City of Chubbuck, ID — When building a new maintenance shop in August 2008, the lights were wired so that they can turned on and off individually so lights can remain off in bays that are not being used, Dale Kinloch, shop foreman, says. The lighting is high-output low-amp draw.
The building’s numerous windows make turning the lights on unnecessary on sunny days, he adds. The air compressor is not turned on until needed and is always turned off at the end of the day so it doesn’t run overnight.
Con-way Freight, Ann Arbor, MI — A provider of regional, inter¬regional and nationwide LTL service, the company has undertaken a number of initiatives to reduce waste and increase energy savings. These include: converted all high-pressure sodium, metal halide and mercury vapor lighting utilized in 15 percent of its shops to more energy-efficient fluorescent lighting; doubled vehicle oil drain intervals; switched to more biodegradable, phosphate-free truck wash, pressure wash and floor cleaning chemicals; converted to single-type, self-cleaning parts cleaners; and implemented an oil recycling program. Total anticipated annual savings are $1 million to $1.5 million.
Con-way Freight initially began implementing green initiatives in its shops in late 2007 as part of parent company Con-way Inc.’s enterprise-wide sustainability roll-out, says Mike Grima, director of fleet maintenance for Con-way Freight. “In 2009, the division dedicated a research and development resource to begin testing and evaluating products that could further boost green efforts in the shops, which the company began implementing in 2010. We continue to evaluate new products on an ongoing basis to further reduce the shops’ environmental impact.”
He says by switching to fluorescent lighting, Con-way Freight anticipates savings of 114,240 kilowatts annually. Other yearly savings: reducing the frequency of oil changes by 50 percent, 164,244 gallons of oil and 17,000 oil filters; converting to non-phosphate cleaning products, an estimated 2,611 pounds of phosphates from the environment; and changing to self-cleaning parts machines will reduce its waste generation by an estimated 8,010 gallons of parts-cleaning solvent.
Last year, Con-way Freight’s waste haulers collected more than 297,193 gallons of used oil from its shops. Recycling this oil instead of disposing of it will result in annual savings of 2,419 metric tons of greenhouse gas emissions which, Grima points out, is equivalent to 44,800 propane cylinders used for home barbecues or 5,594 barrels of oil consumed.
Gordon Trucking, Pacific, WA — “Going green is a huge commitment,” says Kirk Altrichter, vice president of maintenance for this truckload carrier that is also a partner of the EPA SmartWay program. “This movement would not be possible if not for the widespread support by all Gordon trucking associates.”
From its environmental practices, not only is there a cleaner, healthier work environment for its technicians, he figures that per year, the company has oil savings of $190,000; oil filter savings of $30,000; savings from switching to rechargeable batteries in excess of $2,500; income from scrap metal in excess of $40,000; 3,000 kWh reduction in energy use per shop for a $725 savings per shop; and income from waste oil in excess of $10,000. The practices helping to achieve all of this:
New filtration technology reduced oil usage and waste oil by 27,000 gallons annually and has extended oil change intervals to 72,000 miles, reducing filter usage and waste by 4,000 filters annually.
Oil and antifreeze are sold to a reputable recycler.
Oil filters are crushed and recycled.
Fuel is saved from each fuel filter or fuel water separator change, then filtered and placed back into the company’s fuel tank.
Antifreeze not contaminated by oil is filtered and placed back into the radiator.
Parts washers are complete recycling systems that clean the dirty solvent to like new and only generate about 1 cup of waste every 3 months.
Brake clean and penetrating oil are dispensed by reusable sure-shot (air-pressurized) dispensers eliminating the use of aerosol cans.
Recycling all steel, aluminum, cardboard, acid and alkaline batteries, scrap tires and copper wire.
Steel wheels are reconditioned and reused.
Shop heating systems have been replaced with infrared heaters, improving heating efficiency by approximately 25 percent.
Reducing the use of paper by 80 percent by replacing paper work orders with real-time data entry.
Ryder System, Miami, FL — All of Ryder’s environmental efforts must first meet the litmus test of being good for business - driving bottom line savings, improving efficiencies or enhancing customer service, says Nanci Tellam, group director, environmental services and sustainability. “The energy conservation program, specifically, is where we are seeing measurable economic results. Upgrading facilities with energy efficient lighting, HVAC equipment and building materials can pay dividends for years, if done correctly.”
Electricity use, Ryder’s primary source of stationary emissions, is being tracked using a weather-compensated tracking platform that can compute energy demands at each facility and calculate various metrics, including per square foot usage as a benchmark, ranking similar sized locations and determining which shops are the most and least energy efficient. “This detailed analysis allows us to identify which conservation practices work the best and also helps us to then decide how to incorporate recommended upgrades to provide the best payback and return on investment,” Tellam says.
Ryder has developed several Energy Conservation Checklists for its facilities that include best practices for facility management, lighting and atmospheric controls. “‘These tools offer no-to-low cost tips for saving energy,” she notes. Some examples of actions on Ryder’s checklist, which can produce a 5 to 10 percent energy savings, include:
Replace manual thermostats with locking, programmable thermostats and set thermostats to 68 degrees for the winter and 76 degrees for the summer.
Install timers or sensing controls on all non-security lighting at the fuel island, wash bay and storage areas.
Routinely inspect and replace weather stripping on doors and caulking around windows every three years to prevent heating and cooling loss.
“One of the most frequently overlooked opportunities in shops today is establishing a routine, systematic maintenance program for heating and cooling equipment,” points out Tellam. “Simple things like inspecting air filters monthly and changing out filters when needed so that air flows freely, and cleaning drain pans, condensers and coils every 6 months or as needed to keep systems operating at peak performance can reduce kWh use by 5 percent.”
Ryder operates approximately 1,000 vehicle maintenance facilities throughout the U.S. and Canada. Last year, it recycled more than 2.7 million gallons of used oil, 961,000 gallons of oily water, 6,000 drums of used automotive oil filters and more than 28,000 gallons of used solvent.
Smithfield Packing
Transportation Company, Tar Heel, NC — The fleet maintenance facilities for Smithfield Foods Company’s fleet of refrigerated vehicles has implemented environmental management systems modeled after ISO 14001. Also a member of the EPA SmartWay Transport Partnership, it started its green shop movement in 2002 because “we felt that it was our social and moral responsibility, says Gary Bradshaw, service manager.
“We started with simple things, such as changing out lighting as bulbs and fixtures failed, and took advantage of green repairs and replacement as capital equipment aged out,” he explains. “Not only do we look at the immediate benefits, we also consider the long-term gains.”
The shops’ greening efforts include:
Heating the shop using waste oil which is safely stored onsite. “This has reduced our facilities’ LP gas usage by 86 percent or 11,236 gallons per year,” Bradshaw notes.
Extending oil drain intervals using bypass oil filtration. The fleet started testing bypass oil filtration 20 months ago and has extended drain intervals up to 4 times longer than standard filtration.
Recycling all plastic, cardboard, paper, aluminum and other metals “to reduce our landfill service by 31 percent, a reduction of 3,744 cubic feet per year.”
Monitoring drivers’ idle time and fuel mpg via monthly downloads and the use of APUs to reduce idle time by 40 percent, equating to reduced emissions, maintenance and fuel use.
Training shop staff to assist drivers with idle reduction and fuel-efficient driving techniques.
Establishing a diesel fuel stabilization program to burn fuel more efficiently at a lower temperature, without a cetane enhancement. Bradshaw says this has produced a fuel economy increase of around 20 percent with fewer emissions and a decrease in engine wear metals.
Upgrading all shop and office lighting to more energy-efficient lighting.
Upgrading the HVAC system to one with a SEER rating (a measure of how well air conditioning equipment works) almost double that of the old system.
University of Georgia, Athens, GA — “We didn’t decide to go green - green wasn’t a buzz word 20 years ago - when I started making changes to how things were done,” says the university’s fleet manager Bill Fox. “Protecting the environment we live in is common sense. As an institute of higher learning, we should use common sense and be a leader/experimenter in every area to go green. Plus, most all of our waste has value, so recycling made fiscal sense as well.”
The fleet runs on CNG and E85 that is made from expired coke syrup - a waste stream not a food stream, he notes, and has electric vehicles. All of the more than 1,600 vehicles - from transit buses to front load garbage trucks to Cushman carts and everything in between - is regularly and properly maintained. Other green practices include:
Using an antifreeze recycling system to recycle waste engine coolant.
Using a water-based parts washer.
Recycling all metals, plastic, office paper and cardboard, as well all waste oils, used filters, spill mats, Freon, batteries and tires.
Saving paper with web-based shop manuals, work orders and cost accounting reports.
Having all interior drains go through an oil separator before going to the sanitary sewer.
Using waterless urinals.
About the Author
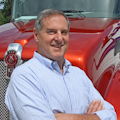