The old adage, “an ounce of prevention is worth a pound of cure,” is especially true when considering the value of the billions of pounds of perishable goods hauled in trucks trailers chilled by transport refrigeration units (TRUs) every day in North America. Maintaining those TRUs to help ensure proper operation is the key to satisfactory on-time deliveries and avoiding equipment issues that could lead to a costly load loss.
Fortunately, the built-in analytical and diagnostic features on many TRUs make it easier than ever to troubleshoot and stay on top of unit performance. Many of today’s TRUs are more reliable and durable than their predecessors, thanks to design improvements that decrease demands on unit engines.
What’s more, many modern TRUs’ preventive maintenance (PM) service intervals have been stretched out by as much as 15 percent compared to earlier models, owing to improved system efficiencies resulting in reduced engine run-time hours when operating in the start/stop mode.
Pre-Trip Inspections
One of the handiest maintenance practices of all is the pre-trip inspection routine, which truly amounts to that proverbial “ounce of prevention,” especially considering how little operator effort it takes to do: a simple button push.
“The pre-trip doesn’t replace the need for scheduled service and preventive maintenance, but what it does is rather extraordinary,” says John Jameson, comprehensive maintenance and repair agreements (CMRA) program manager, Carrier Transicold (www.carrier.com/truck-trailer/en/north-america), a company that helps improve transport and shipping of temperature controlled cargoes with a complete line of equipment and services for refrigerated transport and cold chain visibility.
“A pre-trip should be done prior to loading the refrigerated compartment,” he says. “In the time it takes to grab a cup of coffee – 10 to 15 minutes – the control system on a Carrier Transicold trailer unit, for example, will run 13 to 17 tests covering hundreds of potential alarm conditions, including about 75 that are specific to the pre-trip routines.”
To name a few, the pre-trip routines examine:
- Electrical system continuity.
- Engine high and low speeds.
- Fan motor operation.
- Refrigeration system valve operation.
On Carrier trailer units, the APX Control System display module will indicate pass/fail results for all tests. Alarm conditions, if detected during the scan, can then be viewed by the operator.
Regular Schedule
Beyond taking advantage of the pre-trip routine, Jameson advises that the regular preventive service schedule per the manufacturer’s recommendation be maintained.
“Performing regular preventive maintenance per original equipment manufacturer (OEM) recommendations will help ensure the diesel engine and refrigeration system mechanical components, including the compressor, are running true, and will assure that fluid and filter changes are done at appropriate intervals,” he says.
Variances in TRU platform design make significant differences in the amount and frequency of maintenance required in the PM schedule. For example, notes Jameson, Carrier Transicold has both a traditional belt-driven platform and a hybrid diesel-electric platform, each with different maintenance needs.
Vector hybrid units were purposely designed to require less maintenance than traditional units, he explains. The refrigeration system is all-electric, powered by a generator connected to the diesel engine.
Thus, many of the routine maintenance components found in conventional belt-driven refrigeration systems are gone. Examples include the mechanical clutch, gearbox, alternator, mechanical fan shaft, some of the refrigeration valves and most of the belts and pulleys.
“Since many of those serviceable parts are not required, concerns about mechanical failures are reduced,” Jameson says. “A part that’s not there is one less part to maintain.”
“As a result of fewer serviceable parts, lifecycle costs are reduced with hybrid designs,” he adds. “If operators take advantage of electric standby and run the hybrid units off an electric power source when stationary, engine hours are reduced even more, thus extending service intervals further.”
Items To Check
There are items for which OEMs generally recommend an annual PM inspection, while other maintenance procedures have been extended through the years, Carrier Transicold’s Jameson says. For example, oil changes may now be performed at 3,000 hours or two years –whichever comes first, and extended-life antifreeze coolant replacement intervals are now 12,000 hours or five years.
He notes here again, the APX the control module simplifies things by keeping track of engine hours to help determine when it’s time to do a PM check.
During preventive maintenance, Jameson says the following items should always be checked:
- Engine oil (add as necessary).
- Battery cables and clamps.
- Lift pump screen.
- Belt condition (tightening as necessary).
- Coolant level (adding more if needed).
- Exhaust system and mounting hardware.
- Air filter (changed, if needed).
With conventional units, the gearbox and compressor seal should also be visually checked for leaks, he adds, keeping in mind that the presence of a small amount of oil in the compressor shaft seal area is normal.
“The engine should be checked for proper operation and the pre-trip routine should be initiated with all active and inactive alarms noted,” advises Jameson. “Technicians should observe fuel lines, oil lines, filters and the exhaust system for leaks, and should listen for unusual bearing noise from components, such as belt idlers or fan shafts. Water should be drained from the fuel tank and debris should be cleared from defrost drains.”
Additional adjustments, such as battery checks, coolant flush and fill and belt changes come at longer intervals, he adds.
“To summarize, a solid equipment maintenance program is essential to running a cool refrigerated transport operation,” Jameson says. “Running trailer units through the automated pre-trip routine before loading and following the preventive maintenance schedule will help assure reliability and uptime for the long haul.”
About the Author
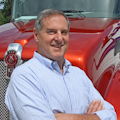