Absent the protection provided by corrosion-inhibiting technologies, the critical metal structural and ancillary components in any heavy duty trailer would quickly begin to oxidize and corrode. Today, all trailers being manufactured have some type of corrosion protection applied to their metallic surfaces, and anti-corrosion coatings are the most common.
The simple combination of moisture and the sodium chloride from road salts combine to create the corrosive one-two punch that will continuously assail a commercial fleet, if maintenance professionals don’t assume a defensive posture. It often starts as stones and other road debris cause chips and abrasions to paint epoxy-based and galvanized coatings, but maintenance activities can degrade coatings as well.
If even a small area of a coating is dislodged, the unprotected metal will begin to react and oxidation begins. Left unattended, the corrosion that started with a small chip in a protective coating can expand by allowing water and salts to migrate and begin corrosive activities between the coating and the metallic surface it was meant to guard.
Fleet maintenance professionals will often see osmotic blistering as a sign that corrosion has begun. The blisters actually create microenvironments consisting of high humidity and levels of chloride that promote rust development.
“Many people associate cold weather with corrosion, but actually, every rise in temperature of 10°C Celsius doubles the rate of corrosion, even if no humidity is present,” says Mike Duncan, Ph.D., vice president technology, Daubert Chemical Company (www.daubertchemical.com), a leader in the formulation of cavity wax and wax-based underbody coatings. “Iron oxide corrosion caused by moisture alone has limited solubility and is relatively slow acting, but iron chloride corrosion, accelerated by moisture, combined with the sodium chloride in road salt, has almost unlimited solubility and can spread very rapidly.”
Many trailer components are also vulnerable to galvanic corrosion caused by dissimilar metals making contact. A simple maintenance repair that pairs the wrong nut, bolt or washer can create a corrosive response.
Problems can also occur as a result of fasteners being tightened, which can dislodge surface coatings, exposing reactive metals to one another and to the elements.
If they are taught what to look for and to look for it constantly, Duncan says fleet maintenance professionals can often locate corrosion and remediate it before it does real damage. Corrosion detection should be a part of every formal preventive maintenance (PM) protocol.
Likely Locations
Left unattended, corrosion can flourish virtually anywhere a metallic component is found on a trailer. Some areas on a vehicle are more susceptible than others, but high exposure to road-born moisture and debris strikes are the keys factors in determining where corrosion is most likely to dwell.
“As trailer refurbishment specialists, we have a unique perspective on trailer corrosion and we see situations and trends that others in the industry might not be aware of,” says Dave Letts, president, Transport Finishes (www.transportfinishes.com). “We see corrosive activity occurring most often on forward facing surfaces under the trailer. We also observe that the closer a surface is to a tire, the higher the probability that this surface will show signs of corrosion.”
Letts notes that forward-facing crossbars on trailer landing gear are particularly susceptible to rock strikes and the road spray kicked up by tires. Bogie assemblies are equally at risk, along with structural crossmembers above and behind them.
Anything below an 8’ to 10’ feet “spray line” should be considered the prime corrosion inspection zone, he adds, and identifies upper couplers, landing gear K-members attachment points on wing plates, crossmember end clips and the butt welds on lower hinges of door frames as key areas to watch for signs of corrosion.
“Ledges, flanges and areas forming pockets often allow debris to collect and remain moist, and these create the perfect environment for rust,” notes Letts. “Electrolysis can be a self-inflicted problem for fleets, and we often see it around fasteners, resulting from ill-informed maintenance practices.”
Maintenance inspections should also include areas around welds. Heat from the welding process changes the composition of base metals and regardless of the quality the welding materials, there will always be some disparities in their makeup, presenting the opportunity for electrolysis to take place.
Silicate concentrations also form around welded areas. The silicate is not only difficult for paints and hard coatings to bond with, but its salty composition means that moisture can easily activate it and cause corrosion to begin.
Problems
How can maintenance professionals promote safety and save their fleets money, while increasing trailer longevity and resale value?
“We see the results of effective PMs on a daily basis, as well as the results of a lack of preventive maintenance,” Letts of Transport Finishes says. “You can tell a lot about a fleet by the way maintains its trailers, and that ultimately impacts both safety and asset utilization.”
He says a poorly maintained trailer will deteriorate steadily and that this is a recipe for a Compliance, Safety, Accountability (CSA) infraction. He proposes a scenario where a corroded mudflap bracket has come loose and falls off a trailer.
“A loose or missing mudflap bracket is a formal invitation for authorities to conduct a roadside inspection,” he says, “and an out-of-service vehicle generates no revenue.”
Letts observes that a vehicle with active corrosion is also far more difficult to work on. It can be costly and time consuming to have to heat, cut or break off corroded fasteners. Wiring can also become contaminated, lamp holes can become misshaped and sometimes patch panels have to be added to keep equipment functional.
“Maintenance crews can spend more time on preliminary corrosion-related repairs before they can even address the original problem,” he says.
Letts is adamant that an active corrosion prevention PM plan will pay dividends when it’s time to sell a used trailer. He insists that poorly maintained trailers often sell for 50 to 75 percent less than even reasonably maintained trailers, and some poorly maintained trailers often must be sold as scrap.
“If corrosion is allowed to gain a foothold and remain active on a trailer’s structural members, you are going to regret it,” says Letts. “Once the structural integrity of vehicle is compromised, you’re looking at repair costs that may make it virtually impossible to salvage.”
Prevention Measures
Fleet maintenance professionals have a number of tools to inhibit trailer corrosion on in-service vehicles. Today’s trailer manufacturers use a range of methods to prevent corrosion on new vehicles, and fleets have varying options available to them for corrosion prevention on in-service vehicles. In the process of original construction, vehicle components are often treated inside and out with corrosion resisting substances. After the assembly process is complete however, interior access can be limited.
Trailer OEMs fight corrosion on a trailer’s structural crossmembers with paint applications, two-step zinc and paint combinations, epoxy coatings and construction using costly galvanized, stainless steel or aluminum components. The technique used by the vast majority of trailer manufactures is hot-melt wax-based coatings.
Maintenance professionals must take into consideration what type of corrosion-fighting method was originally used on a vehicle when making repairs, and some coatings and materials are harder and more costly than others to work with, says Duncan of Daubert Chemical. He also notes that the company’s Nox-Rust corrosion-inhibiting solutions are compatible with virtually all commonly used anti-corrosion coatings.
Fleet maintenance crews can use its Nox-Rust X-121B as part of an effective PM protocol that stops active corrosion in the field, he says. It is a thixotropic wax gel rust-proofing compound designed to provide a long-term protective film for primed and unprimed steel.
Nox-Rust X-121B shares the performance characteristics of Nox-Rust 1210HP, a hot melt corrosion preventive coating designed to be applied to various trailer structural members from a heated dip coating tank.
Both solutions, which contain rust-inhibiting chemicals, are hydrophobic, literally excluding water molecules from contact with the metal they cover, Duncan explains. “The products’ ability to protect metal from salt, humidity, dirt and debris makes them one of the most effective direct-to-metal protective coatings around.”
Wax-Based Technologies
“With the exception of stainless steel and aluminum crossmembers, which are cost prohibitive, other anti-corrosion methods, such as galvanized steel, rely on the application of a coating, and in all cases except wax-based coatings, those coatings are prone to chipping,” Duncan says. “In contrast, wax-based coatings are soft, pliable and self-healing even when struck by rocks or abrased.
“Due to its malleability, the material won’t chip and essentially encapsulates a metal substrate in a protective coating that is much better suited to the wet abrasive environments found under a heavy duty commercial trailer.”
About the Author
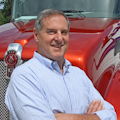