Corrosion resistance testing on galvanized steel trailer components
In recent years, some trailer OEMs have been touting the use of galvanized steel components as a solution to corrosion.
“Though the use of galvanized steel in trailer construction has been gaining in popularity, little if any scientific research has been done to support its efficacy,” says Mike Duncan, Ph.D., vice president technology, Daubert Chemical Company (www.daubertchemical.com), a leader in the formulation of cavity wax and wax-based underbody coatings.
The company recently announced the results of comparative corrosion resistance testing that reveal the limitations of galvanized steel and demonstrate its inability to withstand exposure to the most common corrosive agent, sodium chloride.
In salt spray exposure tests following American Section of the International Association for Testing and Materials (ASTM) B117 standards, Daubert Chemical compared galvanized steel I-beams to I-beams coated with its Nox-Rust 1210HP wax-based coating, an industry leading corrosion-inhibiting solution for medium and heavy duty truck and trailer manufacturers.
Formalized Testing
“Questions about the use of galvanized steel chassis components have arisen among truck and trailer OEMs in recent years,” Duncan says. “As we discussed the topic with our customers, we realized that nobody had done a definitive study on the subject, and that’s when we decided to undertake formalized testing.”
The test results showed that after 1,000 hours of exposure to the saline spray, the galvanized steel I-beam underperformed in comparison to the I-beam coated with Nox-Rust 1210HP, he says. “The continuous salt spray exposure caused the galvanized sample to begin visibly shedding its protective zinc coating in the form of zinc oxide, also known as white rust.”
Galvanized steel is even more vulnerable to corrosion wherever connection points are made, he adds. The assembly process inevitably causes portions of a component’s zinc coating to be dislodged, often breaking off where fasteners are applied, or where grinding, drilling or welding takes place. Once the zinc coating has been disturbed, corrosion will inevitably follow.
“The idea that corrosion can be avoided by building a trailer using paint applications, two-step zinc and paint combinations, epoxy coatings or galvanized components is a myth,” says Duncan. “You simply can’t take corrosion out of the equation with these other products, but you can successfully manage corrosion on all exposed metals, including galvanized, cost-effectively with hot-melt wax-based corrosion-inhibiting solutions like Nox-Rust 1210HP and Nox-Rust X-121B.”
About the Author
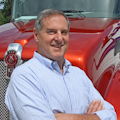