Some of those dents, scratches, and rust spots you notice in the service bay might seem like more of a nuisance than anything. But ignoring even minor cosmetic damage can hurt a fleet’s image—and may lead to more problematic issues down the road.
Today’s fleet technicians are also dealing with a wider variety of construction materials, including steel, aluminum, and composites. Because of this, it’s beneficial to have a strategy in place to streamline workflows and tackle exterior repairs with the right knowledge, tools, and processes to ensure as quick a turnaround as possible.
Even within the same make, materials can differ. For instance, Ford’s Transit, Transit Connect, and E-Series vans have steel bodies, while Ford’s F-Series trucks have bodies made of high-strength, military-grade aluminum alloy panels.
Shops should be aware of this and should think about in which bay these vehicles are placed.
“To prevent cross-metal contamination that could lead to vehicle corrosion, aluminum vehicles undergoing repairs should be separated from vehicles undergoing steel repairs,” said Gerry Bonanni, senior engineer for paint and body repair at Ford Motor Company. “Furthermore, equipment used to repair aluminum body panels must be maintained separately from steel repair equipment.”
Regardless of vehicle or material type, Bonanni stressed the importance of making sure any collision repair, whether a minor ding or major body damage, is performed by a trained technician and to OE workshop manual procedures, along with industry guidelines and training for collision repair.
“There are naturally different processes needed to repair steel or aluminum, including welding, riveting, dent extraction, and other techniques,” Bonanni said. “Our manuals show the vehicle’s structure, what it is made of, and repair procedures. We expect professional technicians to know how to carry out these procedures and to understand what the collision repair industry mandates.”How coatings can cause confusion
“On the coatings side, all of your Class 8 trucks in the USMCA (United States, Mexico, and Canada) space are now painted basecoat/clearcoat,” said Joe Wood, VP of global commercial vehicle coatings at Axalta, a supplier of automotive paints and coatings. “That is much different than in the past when there was a mixed bag of basecoat/clearcoat and monocoat.”
This trend plays to a paint technician’s advantage. The monocoats of the past were single-stage paints with no clearcoat layer. Thus, they were not as durable with respect to color and gloss retention.
“Furthermore, repairing with basecoat/clearcoat gives the technician a wider operating window for blending the basecoat followed by a clearcoat application,” Wood explained. “The technician can better provide an invisible repair and also has the ability to buff minor imperfections without sacrificing durability, as would be the case when polishing a monocoat.”
That said, non-LTL commercial trucks can present some challenges for paint technicians. “The truck itself might be a basecoat/clearcoat, but an accessory such as a box or wrecker could be monocoat or powdercoat,” Wood said. “If a truck comes in with damage in multiple areas, the technician could have some challenges in getting to the right solution from both a color and gloss perspective.”Dan Olsen, who has been in the collision repair industry for 27 years, knows all about these challenges. He went straight for the heavy-duty segment, bypassing the glitz and glamour of hot rods and luxury automobiles. Over the past five years, however, a bit of glitz has made its way to the Class 8 segment, said the collision manager at Premier Truck Group’s Salt Lake City location.
Premier Truck Group, part of the Penske family of brands, is a full-service Freightliner, Western Star, and Isuzu dealership across North America—and the trend is happening across makes and models.
“The days of nothing but solid white, black, or red tractors are long gone,” Olsen said. “We’re seeing many more colors and more metallics, so our technicians are having to learn new spray patterns. For example, a certain color and finish may require the air pressure on the spray gun to be adjusted.”
The paint manufacturers have also noticed the trend of trucks veering into the flashy colors of the consumer vehicle space.
“The stylists at the OEMs are now looking at automotive colors to build their color pallets from,” added Scott Colvin, brand manager for fleet segments at PPG, a supplier of automotive paints and coatings. “That means more metallics, pearls, and special-effect colors.”
Colvin and Olsen concur that the expanding range of colors is driven by customer demand. It’s all about improving fleet image and standing out. “We have one fleet customer who is running seven or eight different pastels,” Olsen said. “He definitely keeps us on our toes.”
With deeper, richer colors and even some tri-colors, Olsen said the same traditional basecoat isn’t always the default solution in the paint booth anymore. “A white primer sealer is often needed nowadays on some of these lighter colors. If you’re not using the right sealer, there’s a good chance you’ll end up fighting a complete color shift,” Olsen explained.
The end result could be a final repair that is anything but “invisible.” And that can have an adverse effect on the truck’s appearance and fleet’s overall image—just like all of those dents, scratches, and faded paint that are left unattended.
Matching colors, maximizing efficiency
Maintaining quality and efficiency in the paint booth requires unprecedented collaboration with a good paint vendor. As Axalta’s Wood pointed out, the goal is to always make a repair look invisible while also ensuring that it wears and looks the same as the truck continues down its lifecycle.
“A heavy-duty paint shop really needs a complete layering system, irrelevant of where assets are in their lifecycle,” Wood emphasized. For example, premium-quality paints, such as Axalta’s Imron line, are desirable when repairing trucks that are just a couple of years old. For older vehicles, that might require a complete reimaging. In that case, an economy coating, such as Axalta’s Rival, could be the ideal solution.
“When it comes to selecting a paint vendor, look at how broad the product offering is,” Wood suggested. “Additionally, scrutinize the color capability. Axalta has roughly 96% of the Class 8 truck market at the OEM level. We tell the OEMs, ‘You can have any color you want because we have around 18,000 colors and are creating more every year.’”
Premier’s Olsen said his shop is constantly updating its color library to accommodate new colors and formula changes at the factory that are leading to color shifts in the field.
“For instance, an Imron Elite Productive EY formula is still basically a basecoat/clearcoat like Imron Elite EB, but the factory cure time is faster,” Olsen said. “So with that, we are still dealing with the same toners, but the activators and reducers have changed, which can result in some color shifts. Our technicians just need to be on top of those things.”Colvin said PPG has focused on making its color-matching process as easy to use as possible. PPG’s Fleet Color Selector systems consist of chips that are actually sprayed, as opposed to printed or being ink drawdowns. “This gives the painter a better representation of the colors they’ll encounter on a truck,” Colvin said. PPG’s system is roughly 4,000 colors strong and growing. “We launched an additional 300 chips last year,” Colvin pointed out.
A well-designed paint-matching light with a CRI (color rendering index) over 90 does a good job of replicating sunlight to help illuminate colors and imperfections to aid in paint-matching.
Milwaukee Tool recently introduced its M12 Color Match Light. It provides five different color temperatures and three modes generating up to 1,000 lm of light output. The CRI is 98+, giving technicians a near-perfect replication of natural sunlight. Technicians report that the brightness of high mode is helpful in identifying pearls and coarse metallics.
Olsen said his go-to color-matching tool is a camera. Thanks to recent improvements in technology, his shop is seeing a nice lift in efficiency. “We’re now about 75% successful in getting matches without having to ask for help from our vendor (PPG),” Olsen said.
PPG’s RapidMatch XI spectrophotometer is another useful tool to match colors.
“The software includes proprietary mathematical equations that work specifically with our colors,” Colvin explained. “We recommend that the technician capture five images in the area being painted. But first and foremost, it’s important to make sure the surface is clean. And if it’s scraped up, we recommend buffing out a spot because the camera is very sensitive and will pick up scratches and dirt. PPG’s color science team builds formulas and mathematical equations to point the camera system to the color with the closest possible match.”
Developing those matches is also a science. When doing a body repair, Olsen said a technician cuts out a piece of the panel that needs to be repaired. That piece is sent to PPG’s lab for analysis. Data from the analysis is uploaded into the software. The next time that same make, model, and color rolls into the shop, the technician can get a head start on color matching.
“In a perfect world, every blue truck coated with a certain paint code should be exactly the same,” Colvin said. “In reality, there are variations of color. When we get these samples from the shops, we are able to look at how closely they match the standards we have created. From there, we can create variants to that standard. That way, the painter can look it up in the computer and see that there is a standard but also a variant with certain characteristics. For example, if a technician is looking at a truck and thinks it is bluer than the standard blue, the technician can look to a variant to begin the matching process.”
Automating exterior inspections
The opportunity to automate different steps of the repair process is growing. Color-matching cameras are one example. Additionally, AI (artificial intelligence) and machine learning have the potential to expedite and improve the visual inspection process, giving technicians another tool to stay on top of exterior repairs.
A software developer in Toronto is already showcasing the possibilities. PAVE is a browser-based app that works with any smartphone to automate the inspection process. The app guides a user through a series of photos that need to be taken. Those photos are then analyzed by PAVE’s built-in intelligence. A vehicle-condition report is generated within seconds, which includes itemized details of any damages detected along with suggested repair types. The whole process reportedly takes no more than five minutes.
“Our goal is to replicate that same 360-degree visual inspection like you’d get with a professional inspector,” said Steve Southin, co-founder and co-CEO of Discovery Loft, the developer of PAVE. “A lot of decision-making has to happen when managing a fleet. Is a given vehicle in a condition that can easily be cleaned up and put back on the road within days, or is it getting to that point where it’s going to need some serious maintenance, reconditioning, or even disposal? When you’re moving the visual inspection process more upstream, ideally when the person is the actual user of the vehicle, decision-making becomes much more streamlined.”
PAVE recognizes not only paint irregularities, scratches, and dents but also things like worn tires, broken taillights, and even signs of corrosion and leaks—all important insights that can help technicians better prepare for what needs to be done when a vehicle makes its way to the service bay. And because PAVE is an open API (application programming interface), it is accessible to other software developers. In other words, PAVE’s damage detection and analysis capabilities could be integrated with existing fleet management or shop management software, giving fleet maintenance teams another tool to help manage workflows.UVeye is another automated vehicle inspection system. The deep-learning AI platform of the system analyzes high-quality, multi-angle images to identify hard-to-detect issues such as scratches, dents, and corrosion. The vehicle scan takes a few seconds, and a high-resolution image of the vehicle marked with potential trouble spots pops up on the technician’s monitor.
Technology is also helping to automate the collision repair estimating process. PPG’s AdjustRight draws on a robust database of parts and repair information to produce detailed, accurate estimates. The secret is the back-end “logic” that helps estimators select the correct parts and determine the necessary repair and refinish labor. A tool like this helps standardize the estimating process, reducing the time needed to create estimates while virtually eliminating the possibility of errors.
Fleets can benefit from automated inspections when their assets are dispersed throughout a broader region. “Having that initial visual inspection done ahead of time helps the fleet manager determine which shop to send the vehicle to,” PAVE’s Southin explained. “The fleet manager doesn’t have to worry about sending a vehicle to Shop A, only to find out later that it also has to be sent to Shop B to get a fender repaired, for instance.”
PAVE’s initial focus is on the passenger vehicle segment, along with select segments of the commercial sector, including delivery vehicles such as pickups and cargo vans. That is because a tremendous amount of upfront work goes into gathering all of the vehicle data so PAVE’s AI can do its work. “We can run analysis on every passenger vehicle sold in North America for the past 15 years,” Southin pointed out. “The next frontier is additional segments of the commercial vehicle market, including heavy-duty.”
Reducing a collision repair shop’s carbon footprint
The next frontier for fleets also includes increased environmental consciousness.
For a paint shop, the first step toward reducing its carbon footprint is using the most environmentally friendly coatings possible. “In North America, that is typically a high-solid, two-part urethane,” Axalta’s Wood explained. “But it’s also about how much energy the shop uses. Is the shop using a highly efficient paint that can drive the cure cycle down by 50%?”
PPG has taken its premium heavy-duty paint offering in a more environmentally sensitive direction. The Delfleet One system is replacing the company’s paint system of more than 20 years. Delfleet One gives heavy-duty shops a complete product offering in the 1.5 to 1.9 VOC range, which is lower than most traditional products.
“You get to a lower-VOC paint by looking at the chemicals that go into it,” Colvin explained. “Some solvents and activators have a lower VOC than others. Our chemists looked at those options on the lower end to determine if they could create a lower-VOC formula that retained all of the back-end qualities we also need, such as durability, gloss, and ease of use.”
Aside from using the right coatings, Wood said there are other things a shop can do to reduce its carbon footprint. Is the curing equipment well-maintained so time and energy aren’t wasted when curing? Are air hoses leaking all over the place that cause the compressor to run nonstop? Not only can these play into a paint shop’s carbon footprint but also its bottom line.
About the Author
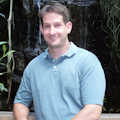
Gregg Wartgow
Gregg Wartgow is a freelancer who Fleet Maintenance has relied upon for many years, writing about virtually any trucking topic. He lives in Brodhead, Wisconsin.