Computerization is changing commercial vehicles in ways many fleets never thought possible. One of the emerging technologies is remote diagnostics, which allows fleets to analyze vehicle data from anywhere without having to physically touch the truck. In a growing number of instances, a fleet can even remotely fix the problem.
“The ultimate benefit of remote diagnostics is that it allows a fleet to take an unplanned vehicle failure and turn it into a planned maintenance event,” says Joe Edmonds, project manager - connected services for Navistar, a holding company whose brands include International trucks. “Many of the issues we see are progressive and don’t start out urgent. If the problem can be addressed before it becomes urgent, it keeps the vehicle on the road and reduces expenses.”
This is where remote programming is now coming into play. As Edmonds explains, many of the potential failures can be avoided by correcting issues with a software update. “OTA (over-the-air) updates will help avoid issues altogether before a problem may occur,” Edmonds says.
Remote diagnostics identify problems
Where remote programming uses two-way communication between a vehicle and remote online interface to fix a problem, remote diagnostics use vehicle data to determine the cause of a problem.
In the case of Volvo, for instance, a truck’s advanced telematics system collects data through a device mounted on the truck and delivers it to a central server at the Volvo Uptime Center.
“Once delivered, Volvo’s uptime specialists determine maintenance needs and communicates their diagnosis directly to the customer, presenting them with the information needed to maintain efficiency in their operation and avoid downtime,” says Ash Makki, product marketing manager at Volvo Trucks North America, which offers a full range of medium to heavy duty trucks.
In some instances, the remote diagnostic process allows data to be shared with the fleet manager, technicians, or external service partners.
“A remote diagnostics system, using telematics technology, makes it easier to understand different vehicle fault codes and prioritize repairs by providing alerts,” says Scott Sutarik, vice president of commercial vehicle solutions at Geotab, a provider of GPS fleet tracking devices and fleet management software. “These can be sent to technicians with different levels of severity, the fault description, and recommendations for action. The technician can then be prepared for what’s wrong with the vehicle and ensure that the right parts are in stock, decreasing vehicle downtime.”
In addition to the built-in data systems on a truck, third parties are also developing telematics devices to monitor various vehicle components. One example is ROI (Road-Optimized Intelligence) technology recently unveiled by Link Mfg., a developer and manufacturer of suspension systems for commercial vehicles.
ROI uses sensors in the axle that provide real-time feedback, allowing a vehicle to continuously react to changing conditions. There is also a remote diagnostics component. Sensor data helps provide a picture of overall system integrity, including early warning of component problems such as low pressure in airbags or issues with lift actuators.
“We have the capability to publish information on the vehicle CAN bus for use by any number of third-party telematics solutions,” says Tye Davis, senior engineer for Link Mfg. “Parameters and settings will also be modifiable through a tablet or smartphone with a Bluetooth connection, or through the vehicle diagnostic connector.”
Having the ability to work with all makes and models of trucks is a big plus for a fleet. Some third-party telematics systems, such as Cojali’s Jaltest ODF, connect to a truck’s CAN bus to read data. This helps alleviate the challenges fleets face when operating trucks with numerous brands of components and data streams.
“The core of our software is the same used on our diagnostic equipment that has 20 years of development under its belt,” says Bruno Gattamorta, vice president of diagnostic sales for Cojali USA, a manufacturer of technology and diagnostic tools for the commercial vehicle industry. “We follow the full integration model from our diagnostic tools and scan all the systems present. We then provide proprietary fault information and allow fleets to analyze a vehicle as a complete system — all in real time.”
Adoption of remote diagnostics platforms is still relatively low among fleets, though some momentum has been gained over the last year. Some truck manufacturers and telematics providers expect momentum to continue as fleets turn their attention to remote diagnostics after completing efforts to meet electronic logging device (ELD) requirements.
“We believe a lot of fleets were introduced to remote diagnostics before the technology was ready to meet their needs, which left a bad taste in their mouth by being overloaded with data they couldn’t manage or understand in a lot of cases,” says Dave Covington, chief technology officer for Noregon Systems, a provider of commercial vehicle diagnostic, repair, and data analytic solutions.
As remote diagnostics has evolved to include more descriptive fault codes and actionable alerts, the benefit for fleets has only become greater.
“Simply put, remote diagnostics should facilitate uptime in a glance,” Covington says. “Fleets should be able to rely on a single system for all makes and models with built-in features that help avoid breakdowns, such as the ability to force a DPF (diesel particulate filter) regen or view predictive maintenance alerts.”
Remote programming fixes problems
Remote programming is the next step beyond remote diagnostics. Remote programming is commonly referred to as over-the-air (OTA) updating. Truck manufacturers began introducing the technology a couple of years ago.
OTA updates fall into two general categories:
- Firmware (software) updates to things like the powertrain, engine, or aftertreatment controllers
- Parameter adjustments to things like a road speed limiter or idle shutdown ambient temperature
In the case of Volvo, OTA updates are implemented using a telematics device that comes standard on all Volvo Trucks. “In order for updates to be installed remotely, the truck needs to be in a stationary position with cellular service to connect with the Volvo Uptime Center,” Makki explains.
In the case of International trucks, any fleet that purchases a new LT or RH Series truck will have OTA capabilities. “All they need to do is start an OnCommand Connection account and they will be ablec1 to deploy calibrations from the portal,” Edmonds explains. “Alternatively, a user could log into the portal and turn on Auto Updates so their vehicles will always get the latest calibration right away.”
With International’s remote programming capability, fleets are able to upgrade the engine control module (ECM) software, as well as modify programmable parameters. “The parameters that can be changed are max(imum) vehicle speed (cruise and pedal), predictive cruise control settings, if equipped, and idle shutdown time and associated settings,” Edmonds says.
For truck manufacturer Peterbilt, a subsidiary of Paccar, remote programming focuses on engine and aftertreatment software updates for Paccar MX-11 and MX-13 engines. The process is designed to be thorough, yet flexible.
- The customer, such as a fleet technician thousands of miles away from truck, uses the Paccar OTA phone app to enable a specific chassis update for OTA.
- To confirm connection, the driver presses the cruise control button for five seconds.
- The software status is then updated on the Paccar Solutions Remote Diagnostic web portal via the cloud.
- After downloading the software to the onboard truck telematics gateway, the technician uses the phone app to initiate a software install onto the engine and aftertreatment electronic control units (ECUs). The app walks the technician through the process.
- The phone app provides a status update while also providing the option to roll back to the previous version, if necessary.
In addition to remote “repairs” such as a forced DPF regen, OTA updates enable customers to switch between operating modes to maximize performance and fuel efficiency.
“A real-world example that our customers run into all the time is crossing the border from the U.S. to Canada,” Navistar’s Edmonds says. “The U.S. allows for truck speeds up to 85 mph in some cases, but Canada requires the vehicle to have a speed limiter of 105 kph (about 65 mph). Many customers stop at a shop near the border to have the max speed changed. With OTA updates, that can now be done passively to the driver prior to them entering Canada and can be done at no cost.”
Changes in topography can also be a factor. For example, a driver may have finished a long, flat stretch during which the truck’s transmission and engine were programmed and optimized for fuel efficiency, but the next stretch of the route is more mountainous. “With remote programming, the driver could pull over, connect to the Volvo Uptime Center, initiate an update to optimize for performance, and be back on the road in a matter of minutes,” Volvo’s Makki says.
Jason Krajewski, director of truck connectivity for Daimler Trucks North America, says some fleets have gotten pretty creative with how they are leveraging OTA technology. Daimler is a manufacturer of several commercial truck brands including Freightliner.
In one example, a truck’s front radar system was reporting a blockage. The truck continued to leave the depot every day before the fleet manager decided to take control of the situation. The fleet manager used an OTA update to remotely reduce the truck’s maximum allowable speed to 25 mph, forcing the driver to come back to the shop to have the radar system repaired. In this case, safety was the reason for the remote update.
Idle shutdown is another good example, Krajewski points out. This can be seasonally driven based on location and time of year. For instance, a fleet might want to remotely lower the ambient temperature for a truck in Arizona in the middle of August to help maintain a comfortable cab for the driver.
Telematics providers move toward remote programming
Dario Peruch, general manager of TEXA USA, points out that many of today’s telematics devices are read-only, meaning that they can only provide some degree of remote diagnostics capabilities but no remote programming. That is beginning to change.
For instance, the TEXA eTRUCK can remotely perform emissions resets and speed limiters. TEXA USA offers a complete range of products and services for diagnostic repair and maintenance. “The driver needs an app on a [smartphone] and the ability to communicate (via regular phone call or data transfer) to the workshop that uses an online portal to see what’s happening to the truck,” says Peruch. “Downtime is often caused by emissions-related issues such as a clogged filter. Connecting remotely and performing a regen would solve the issue and put the truck back on the road as soon as possible.”
Other telematics and diagnostics companies are also taking steps to provide remote programming capability. For instance, through its 19.3 update, Cojali’s software has the ability to run OTA updates for a majority of Cummins engines.
To complement its TripVision remote diagnostics product, Noregon introduced TripVision Uptime earlier this year. “Fleets can easily view vehicles to improve their current condition through a driver action, such as adding more coolant or pulling over somewhere safe to force a DPF regen,” Covington explains. TripVision Uptime also allows fleets to clear faults, change parameters, and initiate bidirectional controls — regardless of make or model.
OTA adoption on the rise
More fleets seem to be taking advantage of OTA updates on a more regular basis.
“We’re seeing 800 to 1,000 updates every month now,” Daimler’s Krajewski relates. That is a noticeable increase from when the technology was first rolled out a couple of years ago.
“Acceptance is absolutely increasing across the industry,” Volvo’s Makki adds. “Usage of vehicle data and connected data is becoming more a part of our customers’ day-to-day business. Almost every vehicle has some connectivity component to it now and we believe over-the-air updates will continue to progress in the same manner.”
Telematics systems of the future will analyze and optimize a vehicle’s performance based on what users expect out of their truck.
“Volvo Trucks predicts there will be more intelligence both onboard and offboard that will be working together to create alerts, exceptions, recommendations, et cetera, on how the truck can be tuned to increase performance,” Makki explains. “That may be changing some of the specs of the truck, such as changing the power or shifting patterns to get the best performance out of the truck without having to bring it into a shop. It could also enable fleets to adapt geofencing technology with parameter updates, which is something that Volvo Trucks is exploring as well.”
“We started down this road around 2011 with our remote diagnostics platform, Virtual Technician,” Daimler’s Krajewski says. “As we’ve evolved our own connectivity platform and work more with telematics providers to move more data off of vehicles, the capability of remote diagnostics has grown quite a bit.”
“Over the past three or four years, we and other OEMs have embraced the concept of data collection to begin building it into a more robust diagnostics scheme for commercial vehicles,” Krajewski continues. “Plus, beyond what the OEMs are doing, there are third-parties starting to get involved that often have expertise in things like data science. That is moving the industry even faster in the direction of more responsive and in-depth remote diagnostics, which is of great value to a fleet.”
Freightliner has a suite of services under the Detroit Connect brand. Virtual Technician is the remote diagnostics service. Also offered is an OTA update platform referred to as Detroit Connect Remote Updates.
“In our latest platform of trucks, we have our proprietary connectivity hardware onboard the vehicle, so we don’t have to rely on a third-party telematics device anymore,” Krajewski says. “This provides the architecture in the background for the most secure OTA potential you can provide.”
While numerous telematics providers remain entrenched in the industry, the move toward more truck-embedded connectivity is a general industry trend Krajewski says is starting to take shape. That said, third-party telematics solutions continue to provide value and are an option for fleets looking to begin leveraging remote vehicle management technologies.
How fleets can begin embracing OTA technology
First things first, a fleet needs some sort of telematics device to interface with a truck’s engine and other components, whether that device is embedded on the truck or provided by a third party. A fleet also needs some sort of web interface to remotely communicate with the vehicle in a highly secure fashion.
When looking at third-party telematics solutions, Noregon’s Covington says fleets need to be aware of potential firmware limitations that can reduce the available features and access to datapoints on a truck.
“Noregon has designed its own hardware called the ND2, which does not interfere with other hardware such as a telematics device, to ensure that the necessary levels of data are reached and that advanced functions like remote bi-directional controls are accessible and reliable,” Covington points out.
Another thing fleets need to do is create a plan for implementing OTA technology. Again, there are different options. For instance, some OEMs prefer that a call center connect to a truck and perform the remote update. Krajewski says Daimler prefers to leave it up to the fleet to decide who performs the updates.
Regardless of the method a fleet chooses to use, there is a noticeable uptick in the volume of OTA updates being conducted. Furthermore, there is an uptick in the variety of things fleets are asking OEMs to make capable of being remotely updated.
“In a Freightliner truck, for instance, you can already update your engine, transmission, common powertrain, and aftertreatment controllers,” Krajewski says. “In the future you’ll be able to update quite a bit more — things like safety controllers and in-cab controllers, as well as the information that is displayed to drivers. As an industry, we are just starting to crack this nut open and expose some of these things to our customers. The underlying challenge is helping fleets understand how to use this technology and where it fits into their organization.”
This can vary based on fleet size and structure. As Krajewski points out, someone could easily send out updates to 12,000 trucks when they meant to send out to a mere 1,200. In many instances, the fleet manager can be in control, along with a few designated technicians. The main idea is that a fleet needs to think about where this technology will live within the organization, defining and assigning roles in the process.
Fleets also need to understand how OTA technology works. Much like any mobile device or computer, fleets don’t need to know the intricate ins and outs of every little component. But fleets should understand what the technology is designed to do — along with its limitations.
“It’s also important to understand not only how to push out remote adjustments, but also how to roll them back if necessary,” Daimler’s Krajewski says. It’s also essential to be able to keep track of all of the updates as time goes on.
“This will become even more important going forward as more automated systems come into play on trucks,” Krajewski says. “A truck manufacturer could become more like a software company that is rolling out more and more updates to various controllers based on performance needs and insights the manufacturer is learning.”
Seeing as how this technology is only a couple of years old, the full potential hasn’t even been close to realized yet. As Krajewski says, OTA technology has already quickly evolved from introduction to adoption in a very short time. Next up is growth and expansion — and that will likely happen sooner than later.
About the Author
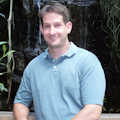
Gregg Wartgow
Gregg Wartgow is a freelancer who Fleet Maintenance has relied upon for many years, writing about virtually any trucking topic. He lives in Brodhead, Wisconsin.