When a truck rolls into the shop with an issue, maintenance technicians know their goal is always to fix that vehicle correctly and get it back to work in a timely and cost-effective manner. How to go about that isn’t always so clear, even with the power of modern diagnostic tools and streamlined triage processes.
“There’s a difference between identifying a problem with a vehicle and identifying the cause,” said Jake Schell, associate product manager, commercial vehicles, Mitchell 1. “Your diagnostics will be much more effective if you spend more time on the cause, treating the problem and not the symptoms. You’ll also spend less time overall, and you won’t have costly repeat repairs.”
Effective triage processes, or defining and addressing a truck’s severe issues in order to get it back on the asphalt battlefield, or escalate it to a more extensive repair, are the foundation of efficient maintenance service practices. By quickly determining a vehicle’s needs or the reason for an issue, shop throughput is enhanced and downtime is minimized. The key is in knowing all of the information that is available to service personnel.With any diagnostics, whether it’s an electronic or mechanical system, information and input from drivers and the fleet are the key, Schell noted. Active and historical codes aren’t the whole story; the questions are what conditions were present when the code was set and does it happen all the time?
“That goes a long way toward tracking and identifying the problem and to the success of triage and diagnostics processes,” Schell stated. “For example, say a vehicle has a fault code indicating a problem with a fuel injector that is not working or is working intermittently. You replace the injector and it runs fine for 25,000 miles, but then it needs to be replaced again.
“Now you need to ask if it was something else that was setting the code, such as a bad connector or the connection causing a voltage drop,” he continued. “It wasn’t a misdiagnosis that the injector was failing; it was why that wasn’t determined correctly.”
Incorrectly determining the cause of a problem has costly and time-consuming consequences. Not only does that ensure the truck ends up in the triage bay again, keeping it and the driver from making money—a shop’s reputation could be in jeopardy as well. To avoid repeat repairs, dedicated triage bays aim to promote uptime, but to do so they need to be set up and managed correctly.
The basics
The first thing to remember is that triage needs to be done quickly and efficiently, and that is accomplished by building a solid-yet-simple foundation. In the same way that first responders at an accident scene or field medics in the military can treat a host of issues out of a knapsack, a good triage technician can rely initially on a few basic tools.
“A battery tester and a diagnostic code reader are essential tools for any heavy-duty shop,” said Jennifer Grabowski, product manager, Bosch Automotive Service Solutions. “Before starting a diagnostic scan of the vehicle, a battery tester should be used to test the state of health and state of charge percentage of the battery. It’s important to make sure the battery is properly charged before using a diagnostic tool, as a low battery can generate erroneous trouble codes during a diagnostic scan.”
It is also crucial to complete a precise visual inspection and consider any details the driver or fleet shares about the vehicle, related Jason Hedman, product manager at Noregon. Then, an effective triage process combines a thorough vehicle scan with a diagnostic solution for all makes and models.
“Using a single application for triage, diagnosis, and troubleshooting makes the entire repair process more streamlined and efficient,” he explained further. “Rather than using countless component-based applications, a single application for all steps of maintenance simplifies training and gives technicians a holistic view, leading to a more effective triage process.”Effective triage includes knowing which fault codes exist, the status of those faults, and when they occurred. And to do that you need software that will look at the entire vehicle, noted Diesel Laptops CEO Tyler Robertson. The vast majority of the commercial trucks on the road today are not vertically integrated. They have various manufacturers of brake systems, engines, transmissions, collision warning systems, and cab/chassis controllers.
“You need to make sure you have the proper software that allows you to connect to the vehicle one time, read all the data on all the components, and easily retrieve that data both locally and from a web-based platform,” he added.
Grabowski agreed. “A heavy-duty code reader for Classes 4-8 vehicles that can read and clear standard trouble codes is a must-have for any shop,” she stated. “It’s a portable, handheld device that can diagnose ABS, transmission, and engine issues quickly, and it can help troubleshoot the complexity of the issue and help technicians determine if it is easily fixed or may require a fuller diagnostic scan.”
A portable tool can also be used to diagnose issues in the field and help identify quick fixes to keep trucks on the road and minimize downtime, she added. A heavy-duty code reader is not a replacement for a full function bidirectional heavy-duty diagnostic system, but it can quickly pull codes, as well as read, record, and playback live data streams for further analysis and diagnosis.
With diagnostic software tools, a roll call of all vehicle ECUs can be taken at startup, according to T.J. Thomas, director of marketing and customer solutions, Controls Group, at Bendix. “We recommend that technicians use a systems approach and review all diagnostic trouble codes (DTCs) before diving into any one active DTC, because many are interrelated,” he said. “For example, if a J1939 active DTC is reported by the vehicle controller and the forward-looking radar, we would recommend troubleshooting the vehicle DTC first; then rerun the software to see if that also addressed the radar DTC.
“Diagnostic software can generate very comprehensive reports that show important component information, active and inactive DTCs, and other event information,” Thomas continued. “The reports can be run before and after troubleshooting has been completed to enable a clear understanding of some of the critical information on the vehicle before and after it entered the shop. This can be very helpful when reviewing vehicle records for trends at a later time.”
Streamlining repair through remote diagnostics
With the advanced communication and internal diagnostics onboard modern trucks, the triage can technically start even before the truck gets to the repair facility.
“Remote diagnostics is the next evolution of where our industry is going,” Robertson said. “In the traditional model, everything is reactive and repair shops make the decisions on when trucks can be looked at, who looks at them, and what procedural steps should be done. While OEM dealerships can manage this for the brands they represent, it gets far more complicated for them when working on different makes, and at independent repair facilities.”
In any case, all vehicle repair operations face similar challenges, Robertson noted. This includes having access to repair information, proper diagnostic tools, knowledgeable technicians, and the needed repair parts. The diagnostic procedure and decision making process can start much earlier by moving the information gathering and diagnostic procedures to call centers. They are able to grab the data as the vehicle is driving down the road, which leads to better repair plans and more efficiency throughout the service process.
“By working with software providers that can monitor vehicle data remotely and help analyze the information, fleets can save a tremendous amount of downtime by getting ahead of the problem instead of being reactive or ignoring the problem until it becomes too late,” Robertson added.
Hedman agreed that remote diagnostics make it possible to begin triage before a truck ever arrives at the service center. The early start lets users download comprehensive diagnostic reports that can be sent to the shop to begin planning parts, bay, and technician needs ahead of the vehicle’s arrival.
“This approach generates major uptime improvements for fleets by helping to ensure they don’t route the truck to a facility unable to perform the work,” he added. “Remote diagnostics can also ease the burden on shops by empowering fleets to perform certain repairs over the air, such as sending bidirectional commands to correct an issue and avoid a roadside service call.”For Thomas, remote diagnostics are aimed at helping the fleet or repair shop understand what DTCs may be active, their priority, and where they can be fixed while the vehicle is on the road. He advised fleet operations to work closely with telematics suppliers to make sure they are taking full advantage of these more advanced features.
“Remote diagnostic technology can potentially help technicians and shop managers prepare for and schedule repairs in advance,” Grabowski added. “At the same time, portable scan tools can complement remote diagnostics, because they can easily provide a more detailed and more accurate view of a vehicle’s condition or potential issues in a shop or in the field, and that can triage vehicle issues more quickly.”
At Rush Truck Centers, remote diagnostics are used in multiple ways. “Knowing fault codes in advance can help the dealership schedule technician capacity, validate parts inventory, and better prepare to minimize customer downtime,” said Victor Cummings, vice president of service operations at Rush Enterprises. “That why we’re currently investing in remote diagnostics technology.”
Chase Bowman, vice president of operations at AM PM Diesel Services, a Houston-based firm that fields over 30 fully-outfitted service vehicles in ten major markets, said remote diagnostics are allowing a first look at what parts will be potentially needed for a repair and how fast they can be acquired. In addition, they are used to determine what skill level a technician needs to be assigned to repair the vehicle.
Dropping downtime and upping throughput
“Our service team’s goals are to initiate triage within two hours of arrival and provide an update within four hours,” said Cummings of Rush’s best practice target. “The intent is to perform a preliminary assessment of each vehicle as it arrives, with a triage technician determining the complexity of the issue.”
That first technician assigned to the vehicle can then jump into action or allocate the repair to a specialist.
“Simple repairs can then be completed by the triage technician or an accelerated repair technician,” Cummings said. “More complex repairs that require extensive diagnostics are reassigned to the appropriate technician with expert diagnostic and repair skill sets.”
At AM PM Diesel Services, noted Bowman, best practices are to first diagnose each unit using Fullbay software and a range of diagnostic tools, and then find out how fast parts can be available. That way, a service order can be created in Fullbay and a technician can be assigned based on the repair type.
From there, the service provider can organize repairs based on time and parts availability. “Of course, we also will move units up and down the repair priority list based on our customers’ needs,” he added.
At Rush Truck Centers dealerships, Cummings also pointed out that guides are available to all service personnel on the company intranet. New service employees also receive check-in process training as part of the company’s onboarding process, and supervisors may assign training as well. Additionally, Rush Enterprises conducts workshops with dealership personnel to provide guidance on the overall triage process.
“Technician training is the key to, and a huge advantage for, diagnosis and seeing what’s going on with the vehicle,” Schell noted. “Diagnostics is just data; it’s the knowledge to know what it means and having a strategic approach to interpreting that information that should be a focus of education for technicians. The more connected vehicles become, the smarter we need to be.”
“Any efficient shop operation requires an effective triage process,” said Hedman. “If triage is not performed correctly, labor or parts estimates can be inaccurate, causing longer downtime than expected and potentially depleting a shop’s resources that are needed to work on other vehicles.”
Finding fault with aftertreatment systems
Across the board, suppliers agree that many common faults on today’s highly advanced commercial vehicles originate from aftertreatment systems.
“We have over 30,000 clients running our diagnostic tools and using our web-based platforms for repair information,” said Tyler Robertson, CEO at Diesel Laptops. “Through them, we grab a lot of data, and every time we look at fault codes it is the same thing—derate fault codes occur the most. And then it comes down to failures that cause the derates, which are most often with emissions-related components.”
Jennifer Grabowski at Bosch Automotive Service Solutions also said DPF system fault codes tend to appear frequently in heavy-duty fleet vehicles. “Many heavy-duty code readers can validate the integrity of the DPF system and help determine if it is working properly,” she related. “It can also read the soot sensor to detect DPF failure, and it can be used to detect intermittent issues.”
Ideally, if the aftertreatment system is running correctly, a forced DPF regeneration should not be needed, but according to Jason Hedman at Noregon, it is most important for technicians to accurately diagnose these issues before unnecessarily forcing a regen in hope of correcting the problem.
“An unnecessary regen wastes time, puts undue stress on the truck, and renders the aftertreatment system too hot to repair, causing more downtime until it cools down,” he added. “Fortunately, however, when a forced regen is the solution to an aftertreatment issue, fleets can perform these over the air rather than calling a mobile repair service or routing the truck to a shop facility.”
It can be hard to say which codes are seen consistently, although regen problems and coolant temperature issues seem to appear in scan tools fairly often, noted Jake Schell, associate product manager, commercial vehicles, Mitchell 1. “[By tracking] codes over the long run,” he added, “fleets will see patterns and problems to address."
About the Author
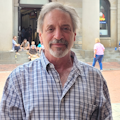
Seth Skydel
Seth Skydel, a veteran industry editor, has more than 36 years of experience in fleet management, trucking, and transportation and logistics publications. Today, in editorial and marketing roles, he writes about fleet, service, and transportation management, vehicle and information technology, and industry trends and issues.