Mobile maintenance: Less downtime, more drive time
In this article, you'll learn about:
- The services mobile technicians can offer
- The advantages and disadvantages of mobile maintenance
- Criteria to understand if mobile maintenance is right for you
Proactive maintenance is essential for any fleet, especially those operating in demanding industries or rough road conditions. Meeting these maintenance needs means vehicles will have longer life spans, managers won’t have to worry about breaking the bank for repairs, and drivers can stay on top of their work.
However, that’s easier said than done. Many drivers don’t have time to handle upkeep. Besides, every minute a vehicle is in the shop is a minute it’s not working, negatively impacting your driver and customer satisfaction.
The alternative isn’t much better. By skipping preventative maintenance once or twice and ignoring check engine lights, safety recalls, or other warning signs, a simple fix can quickly become costly, causing more productivity losses.
This leaves fleet managers between the proverbial rock and a hard place. Many wonder if there is any way to handle maintenance without disrupting operations, leading to enhanced productivity and healthier vehicles.
Fortunately, there is. Mobile maintenance brings qualified technicians to your fleet via repair trucks or vans, performing preventive service basic upkeep, or minor repairs during off-hours or regular business hours. Like many fleet services, mobile maintenance has advantages and disadvantages; it may be ideal for some fleets but not for others. Let’s explore whether mobile maintenance suits your fleet team and drivers.
What can mobile maintenance do for you?
Vendors can perform various mobile services, including:
- Preventive maintenance like oil changes, brake inspections and replacements, fluid top-offs and flushes, and tire rotations.
- Diagnosing engine and transmission problems.
- Emergency services, both on-site and roadside.
- DOT inspections and compliance checks.
- Seasonal services, like installing snow tires, adding anti-freeze, AC checks, and coolant changes.
- Custom upfit repairs or PDR (paintless dent repairs).
- Industry-specific work for construction vehicles, refrigerated trucks, emergency services, and more.
The advantages and disadvantages of mobile maintenance
The biggest perk of mobile maintenance is its flexibility. Technicians service vehicles during off-hours, avoiding operational disruptions while ensuring vehicles are road-ready without a stop at the maintenance shop. Providers can follow a consistent maintenance schedule—ideal for large fleets—or work with your team on a more as-needed basis.
Another notable benefit is the cost savings. While mobile maintenance typically costs more upfront than going to a shop, there are long-term savings. These include extending the vehicle's lifespan, reducing vehicle downtime, and increasing efficiency.
Vendors are even making it easier to integrate mobile maintenance into existing technology. Most providers use digital tools to track service records and diagnostic reports, which can be added to your company’s telematics platform. Some even offer remote diagnostics to determine vehicle issues without physically being on-site.
Of course, mobile maintenance isn’t optimal for every situation. For example, if a vehicle needs complex engine work, a frame realignment, or a unique part, you would be better off sending it to a fully equipped, ASE-certified shop.
It’s also necessary to research mobile maintenance vendors. With the current technician shortage, mobile maintenance providers have varying degrees of expertise, potentially leading to inconsistent quality or compliance issues if a repair is done incorrectly.
Is mobile maintenance right for my fleet?
Mobile maintenance isn’t a one-size-fits-all solution. To determine if it fits your fleet’s needs, consider the following:
- What are my current maintenance practices? Do you already have a maintenance plan with a fleet management company (FMC)? Do you use telematics to track vehicle health? Are your drivers diligent about maintenance, or do they need constant reminders? How often does your fleet require significant repairs, and does your fleet have built-in downtime? Assessing your current setup helps determine if mobile maintenance adds value.
- What are my fleet characteristics? Fleet size, industry, fleet needs, vehicle types, usage patterns, and even location can affect whether it makes sense to engage in mobile maintenance.
- How much more efficient will my drivers become? How much time will your drivers save by avoiding runs to service centers? How many additional deliveries or services can be performed if breakdowns are reduced? Understanding these productivity gains clarifies the benefits.
- What costs should I consider? Compare the costs of mobile maintenance services to the expenses associated with downtime. Remember that downtime is broken down into hard, tangible costs, such as vehicle rental and lost revenue, and soft, variable costs, like lower productivity and delivery delays.
Consider changing the way you approach maintenance.
Mobile maintenance can be a game-changer for fleets looking to optimize operations and reduce downtime. By asking the right questions, thoroughly researching vendor options, and analyzing your fleet's maintenance requirements, you can determine if mobile maintenance is best for your team and what specific benefits it can provide.
About the Author
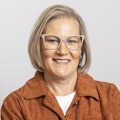
Jenny Baker-Ford
Fleet Maintenance Manager
Jenny Baker-Ford is the manager of fleet maintenance for Mike Albert Fleet Solutions. She has been with the company for six years. Before working at Mike Albert, Baker-Ford worked in retail automotive service for Performance Automotive Network’s Toyota, Honda, and Lexus stores for 25 years.