There’s a lot for fleets to focus on as spring rolls around, from trade shows to prepping trucks for warmer weather, but they should be especially aware of the Commercial Vehicle Safety Alliance’s International Roadcheck. The 2025 safety inspection event is set to take place from May 13-15, which means technicians should pay special attention to the various elements that can earn fleets out-of-service (OOS) violations. Lighting is always at the top of the list.
Over the past six years, lighting issues have been responsible for an average of 1,783 OOS violations on trucks in North America, at an average share of total vehicle violations of 12.4% per year. This rate has put lighting among the top five issues for vehicles every year since 2019.
Lighting violations tend to persist for many reasons. One is how flexible the definition of an “operable light” is, according to Al Anderson, VP of sales and marketing at lighting and harness manufacturer Peterson Manufacturing.
“There are as many different opinions about what is legal [in the eyes of] the inspectors,” Anderson said. While some might think having one LED lamp out is grounds for a ticket, another might forego penalties as long as a certain number of diodes are lit on a lamp.
And lighting is an easy catch for inspectors—as they either work or they don’t—noted Kaleb Osborn, product design engineer at Optronics. Also, it’s an issue that can be hard for drivers to catch while on the road, especially if a light goes out on a 53’ trailer.
“Drivers typically only inspect trailer lights during pre- or post-trip checks,” said Matt Zidek, sales engineer for Grote Industries. “Unlike issues such as a stuck brake or a damaged tire, there’s no immediate feedback alerting the driver to a problem that might require attention during a trip.”
While smart trailer solutions and the increasing flow of telematics data and fault notifications from a truck to the shop are helping to address the problem, this still makes lighting maintenance critical for both fleet safety and regulatory compliance. To help, here’s some of the most common issues for vehicle lamps, why they happen, and the tools a technician needs to keep their fleet bright.
Good equipment is a bright idea
Having proper equipment is key to the troubleshooting tests a technician needs to do to diagnose a lighting issue. Luckily, multimeters and load testers are common tools in the shop.
“Your standard automotive multimeter [is great],” Diesel Laptops’ Scott Meek said. “As long as it has the capability to measure amperage through an external amperage clamp, and as long as it measures voltage and ground, you’re pretty good. Most of your standard meters that technicians would have access to would give the capability to measure voltage and amperage.”
Some options include Electronic Specialties’ LOADpro tool and Back Probe Kit, Mac Tools’ EM823 digital multimeter, and the CAT IV Digital Multimeter.
The LOADpro tool and kit includes LOADpro test leads, tip adapters, two types of probes, and two types of alligator clips, with the test leads able to work with almost any digital multimeter. Meanwhile, the CAT IV multimeter can measure up to 1,000V AC/DC voltage and 10A AC/DC current as well as resistance, diode, continuity, and mx-Pulse/duty cycle. The EM823 features a pulse width of 0.5 to 240.00 ms and can run diode and continuity tests as well, and also features some new features like Bluetooth and USB connectivity.
Corrosion
According to Anderson, corrosion is the number-one reason that lights fail on trucks today, especially due to water and de-icing chemicals entering lighting systems at the connector between the lamp and the wiring harness or through a cracked lens. These contaminants can then short out internal components on the circuit board, he warned.
Additionally, corrosion can physically stop electricity from traveling through the system by increasing resistance along the wire harness.
“Once inside, moisture can travel through the wire via capillary action, spreading corrosion throughout the system,” Zidek said.
Also, while de-icing chemicals are a problem during the colder months, the corrosion they cause isn’t the only issue winter brings for lights.
“Snow and ice accumulation on lamps—both on tractors and trailers— pose significant visibility risks,” Zidek continued. “While LED lamps are excellent for their durability and energy efficiency, their low heat output makes them less effective at melting ice or snow.”
Cold weather can also freeze the moisture that creeps into the housing, and ice can also make wires more brittle. This means maintenance teams for fleets that operate up north should be on the lookout for degraded arrays and, when feasible, preventatively replace them ahead of Roadcheck.
Vibration and physical damage
Corrosion isn’t the only culprit for electrical system woes. Given how delicate the wiring system can be and the punishment a heavy-duty truck takes on the road, physical damage can be a problem, too.
“Shorts in wiring can be caused by something as simple as a screw being placed in the trailer too far when it was being built, causing the screw to catch the harness, which eventually works its way to a wire, shorting it out,” noted Chuck Ralston, manager of the Truck Care Academy and mechanical services at Love’s Travel Stops.
This makes checking for what Anderson calls “clipping” or “routing” critical for technicians. This just means making sure no other sharp edges are going to rub against a truck’s wiring harness and potentially chafe a wire, especially at points where a wire goes across a cross member or through a channel. It’s also critical to ensure that a truck’s wire harness has convoluted tubing wherever it may wear against another component.
The connecting cord between the truck and trailer can be an issue, too, Anderson said. The connecting pins can wear out as the vehicle travels, causing them to lose their connection. Wear on both ends of that cord can sometimes even cause it to become disconnected entirely, cutting off power between the truck and trailer.
Power delivery and voltage
Beyond physical damage to a wiring harness that can put out lamps in a truck or trailer, power delivery issues from the truck can also cause problems, Optronics’ Osborn said.
“One thing that’s unique about the lighting and trailer world is you can’t control the power source because the power source comes from the truck,” Osborn explained. “So different trucks have different mechanisms for controlling the power output of the alternator for when they’re charging the battery, which then ultimately feeds the whole trailer system.”
The transition from incandescent bulbs to LEDs
Part of the reason that the power draw to a lamp can cause issues is due to how trucks have been transitioning from incandescent bulbs to light-emitting diodes (LEDs) over the past several years. The benefits of LEDs are many, as their solid state eliminates filament breakage from shock and vibration, said Paul Sniegocki, EVP of Engineering and CTO at Clarience Technologies.
LEDs also burn with less heat and create less amp draw on the electrical system, making them last longer overall. According to Dustin Smith, VP of sales at Optronics, an LED light will last 50 times longer than an incandescent bulb.
“The light emitting part of [an LED] rarely has a failure,” said Al Anderson, VP of sales and marketing, Peterson. “Those are very, very reliable components.”
But while LEDs can produce a lot of benefits for a vehicle, if a controller is programmed to anticipate the power draw of an LED bulb and incandescent lamps are put in instead, this can cause issues. For example, Scott Meek, director of diesel training for Diesel Laptops, said if a driver experienced a bulb failure and put a few incandescent bulbs in their truck as a replacement, “now you’re drawing more current than that module allows, because it’s programmed for the wrong style of bulb, which means it’s not going to allow that much current to pass through it to power the incandescent.”
This can cause lights to only work for a moment when turned on or can speed up or slow down the cycle of a turn signal. Reprogramming a vehicle module to resolve the issue can vary depending on the manufacturer. Some might have different cab controller settings based on the bulbs used by each circuit, while others might only have settings for how much current a particular circuit can handle.
According to Osborn, that power output from the truck should be around 13.75V. But depending on a truck’s alternator, voltage can spike up to double that and fall as low as 12V, especially if a driver is turning on or off equipment with a heavy power draw. A big enough voltage spike can even burst through a lamp’s resistor, damaging the light or making them work improperly, especially in older vehicles.
“If you’re running an older vehicle, you’ll have to put some inline resistors in there, because the vehicle won’t recognize the amp pull from the lights, so they’ll either flicker or they won’t come on at all,” said Michael Wittman, director of product management at Optronics.
And if one of those resistors cracks at a circuit board, that could also cause it to fail.
“If you’re going down the road behind a truck or a trailer, and you see a light with only part of the LEDs lit, it’s probably got a problem on the circuit board,” Peterson’s Anderson added.
Similar to the alternator issue, vehicle modules can also cause lamps to function improperly due to how they regulate the power that goes to a lamp.
“The problem with newer vehicles is a lot of [them] use cab control modules or body controllers, and those have internal integrated fuses that are virtual,” said Scott Meek, a former diesel technician and current director of diesel training for Diesel Laptops, a provider of diagnostic tools and training. These fuses provide internal circuit protection, but if a body controller finds a shorted wire is damaged, it can turn off that leg of a circuit, which can make lighting issues harder to identify.
“For an example, one weird lighting problem that I’ve had in the past is when you turn the headlight switch on, the box lights would come on for a second, and then they’d turn off,” Meek explained. Thinking this could be due to a virtual fuse, Meek tested the light’s voltage and amperage with a multimeter. He found that there was too much current draw to the lighting circuit, causing the body control module to think there was too much current in the circuit and stopping current flow to it, shutting the lights off.
The lighting diagnostic process
Now that we’ve discussed how lighting can go wrong, how can a tech approach all of this information in an orderly manner during troubleshooting? Starting with the basics helps, Meek said.
“The first thing that any technician should really be doing when a vehicle comes into a shop for maintenance or repair is a visual inspection,” he said. “It’s not uncommon for a technician to get tunnel vision and say, ‘Okay, here’s my problem. I’m going to pull the truck in, I’m going to hook up my computer, I’m going to look for codes.’”
Instead, technicians should look for the simple answer first and check if a lighting system isn’t working due to physical damage, as if you damage one light, the entire circuit can be affected, Meek explained. For instance, if a front right box light is hit by a branch and ripped from the trailer, it may pinch the voltage supply wire on its way.
“Now you’ve increased your current draw because now you have a short to ground, so your flow and max available current flow and everything on that circuit will be affected because of that,” Meek noted.
Technicians should also make sure to use their visual inspections for a corrosion check, said Paul Sniegocki, EVP of engineering and CTO for Clarience Technologies. This means making sure that their connections don’t have a buildup of a white or green corrosive substance. This is also a great time to make sure a truck’s connections are in place and that everything’s plugged in correctly and there’s no rubbing, Osborn added.
But a visual inspection can also give clues for a technician’s later troubleshooting steps, too.
“If there is only one light out, the issue should be fairly close to the inoperative light,” Love’s Ralston added. “If multiple lights are out, the issue could be further away.” This could mean a technician will need to assess a trailer by sections and circuits to avoid getting overwhelmed.
With a visual inspection done, “common sense is the rule of the day,” said Peterson’s Anderson.
This means starting at the source of a vehicle’s power: The truck itself. Make sure that the vehicle is starting well and charging the system properly.
“If the vehicle starts up just fine, that’s generally an indication that we have sufficient voltage, but we’d still want to verify that using a multimeter with electrical troubleshooting,” Meek noted. “You should always verify your voltage source, that it’s adequate.”
Checking that source voltage means testing “the only trustworthy ground on the vehicle, which is the battery negative post,” added Love’s Ralston.
Sniegocki also said that checking the circuit of a trailer’s nose box is a great place to start for troubleshooting, since it has seven-pin connectors that distribute power to standardized circuits.
“If all the lights are out on the circuit, that is a good indication that there’s an issue in that nose box, which in many cases is the factor for failure of electrical systems,” Sniegocki said.
If only one light is out, then it’s time to test the lamp that’s struggling, instead of immediately replacing it. If there’s no easy visual verification that a light is damaged, then you can use a multimeter to check if there’s sufficient voltage (at least 12 volts) and ground at the lamp itself. If the 12 volts are present at the connection and the light still isn’t working, the light is probably the issue. If the light works but it’s dim, there could be some resistance in the harness. But if a technician tries adding an external power or ground supply to the light and it works, there could be another issue.
“That could be due to a damaged wire,” Meek said. “It could be a corroded connection. It could even be something as far as virtual fuses inside the control modules could be the cause of that.”
Anderson added that there’s right and wrong ways to check a light for current, with the latter risking damaging the lamp and the entire electrical system. To check a light correctly, take the wiring harness out of the back of the lamp and check for current at the harness, he said, warning against sticking a test probe into the conductor or the coating of the wiring harness. This can leave a wound for corrosion to enter.
“If you stick a test light into the coating of the wiring harness, that hole’s there forever. It’s not like if you prick your finger, your skin heals it up,” Anderson said. “That will lead to corrosion and can go through a complete wiring harness system in a matter of hours if it’s powered up.”
About the Author
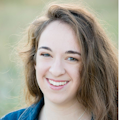
Alex Keenan
Alex Keenan is an Associate Editor for Fleet Maintenance magazine. She has written on a variety of topics for the past several years and recently joined the transportation industry, reviewing content covering technician challenges and breaking industry news. She holds a bachelor's degree in English from Colorado State University in Fort Collins, Colorado.