Since the early years of salt (sodium chloride) use for de-icing roadways in the 1930s, the chief challenge of winter maintenance, mobility and safety has been the never-ending quest of finding the ideal de-icer. As ice management chemicals change, so do the corrosion effects on vehicles and equipment.
In the late 1990s, the winter road maintenance strategy of anti-icing began to take hold in the U.S. and Canada as a way to prevent or minimize the bond between snow or ice and the pavement surface from forming. Anti-icing involves applying ice control chemicals before or at the very beginning of a storm. These typically are liquid chemical applications of salt, magnesium chloride, calcium chloride, calcium magnesium acetate and potassium acetate, with magnesium chloride and calcium chloride being the more popular choices.
Because anti-icing chemicals are applied prior to snow or ice fall, the probability of exposure to vehicles is increased. These materials are especially destructive because of their ability to cling to the underbody of a vehicle and re-crystallize as they slowly dry out. By their very nature, anti-icing chemicals attract and absorb moisture from the surrounding environment, keeping them in a semi-solution state for extended periods of time, which multiplies their corrosiveness.
De-icing chemicals and road salts don't melt snow or ice. Rather, they lower the freezing point of water by creating a brine solution.
Aggressive corrosion on vehicles caused by various formulations of road ice clearing chemicals has been a serious maintenance problem for many equipment users for more than 10 years, points out Robert Braswell, technical director of Technology & Maintenance Council (TMC), North America's premier technical society for truck equipment technology and maintenance professionals.
"It's widely known among fleet managers that use of magnesium chloride- and calcium chloride-based products by certain states is especially associated with increased incidence of corrosion on vehicles, causing damage in as little as a single winter season," he says. "As early as 1999, reports of this problem have manifested themselves through frame corrosion, brake table rust-jacking and excessive wheel and wheel fastener rust."
Corrosion of metals reduces the useful life of any vehicle, resulting in increased costs and decreased uptime. It is imperative to catch corrosion as soon as possible. Like a form of cancer, corrosion takes a certain period of time to manifest itself and can spread undetected until damage becomes significant. However, corrosion can be treated and repaired if caught early and the proper measures are taken.
DECOMPOSITION CHEMISTRY
In order to prevent vehicle corrosion, it is necessary to understand what corrosion is. Basically, corrosion is defined as the degradation of a material by reaction with its environment. Degradation implies deterioration of physical properties of the material.
Corrosion is derived from the Latin word "corrodere," meaning to eat away. The most common form of corrosion is called rust.
"Corrosion is an erosion or deterioration of a metal surface caused by an oxidation from a chemical reaction," says Matt Murray of Eastwood Company, a producer of auto repair and restoration supplies. "If you keep in mind how erosion comes into play with sand and the ocean at the beach, it is easier to understand. The chemical reaction actually makes the metal fall apart or ‘erode' away. This is especially an issue when it comes to structural points of a vehicle."
Road salt or de-icers can speed up the chemical reaction between iron and water, which causes rust or corrosion, thus making a bare metal area much more vulnerable to rust damage.
"Salt can promote corrosion on most any types of metal. The longer it is stuck on a metal surface - even if in a watered down film state, the quicker the surface will degenerate or corrode," says Murray.
Major causes of corrosion are accumulation of road salt, dirt, moisture or chemicals in hard-to-reach areas of the vehicle underbody or frame, and chipping, scratches and any damage to treated or painted metal surfaces resulting from minor accidents or abrasion by stone and gravel.
Once the protective coatings are abraded, even to a minor degree, these areas will be exposed to the caustic environment of road salts and other de-icing materials, as well as allow dirt and road debris to accumulate directly on the vulnerable substrate. Therefore, any damaged areas ought to be repaired as soon as possible to prevent spot corrosion from spreading.
Environmental conditions like dust control chemicals, sea air, industrial pollution and high humidity also play a role in accelerating the rate of corrosion. In addition, moisture and high temperature play an active role in corrosion to the parts of a vehicle which are not well ventilated to permit quick drying.
SOLUTIONS GUIDE
Many industry groups have done a good job identifying the problem of corrosion on vehicles, but a comprehensive guide for solutions has remained elusive, says TMC's Braswell.
In 2005, TMC's Future Truck Committee challenged industry manufacturers and suppliers to raise the bar when it comes to corrosion performance levels. In its position paper, "Recommendations for Corrosion Abatement," the Committee set the performance expectation that corrosion should not cause equipment users to replace any component during its useful life. Additionally, the Committee determined that commercial vehicle users should not need to perform any maintenance to prevent corrosion, other than normal, periodic washing.
TMC defined "useful" life as 10 years for a medium duty truck itself and 16 years for the truck cargo body. For heavy duty applications, useful life was defined as eight years for trucks and tractors; 16 years for trailers and converter dollies. In all cases, TMC recommended that manufacturers back up the corrosion performance expectations with a 100-percent parts and labor warranty.
In support of these expectations, TMC's Future Truck Committee called for improved laboratory tests that more accurately simulate today's operating environment, Braswell says. These tests also should feature provisions for testing electrical components while operating.
"TMC's report recognized that corrosion impacts the various zones of a vehicle differently," he says. "For example, the zone ‘from the road level to four feet above the road level' should have the greatest corrosion protection, as well as withstand impact by sand and stones that can compromise a coating's corrosion protection ability."
TMC's user expectations for corrosion durability were incorporated by the Society of Automotive Engineers (SAE) in its J2721, "Recommended Corrosion Test Methods for Commercial Vehicle Components," says Braswell. SAE 2721, now undergoing an update, offers improved test methods for assessing corrosion caused by the newer de-icing chemicals, as well as other impacts, such as drying, humidity, abrasive exposure and environmental variations.
Braswell notes that manufacturers and suppliers have developed new offerings and upgraded specs to help fleets fight corrosion, especially in the areas of brake rust-jacking, vehicle frames, wheels and fasteners and trailer and landing gear components.
In 2007, TMC created a new committee to carry on the fight against corrosion, the Corrosion Control Action Committee (CCAC). Earlier this year, the CCAC started gathering the work of several active TMC task forces and other materials, to develop a complaint, cause and correction manual for fleet managers and technicians to use in combating corrosion. The guide will feature three sections: identification and classification of corrosion types; means of preventing corrosion through specification; and corrosion-related maintenance and repair issues.
The effort is being lead by CCAC Chairman Todd Cotier, director of maintenance, Hartt Transportation. Plans are to have a well-developed draft for review, as well as an educational session on the complaint, cause and correction manual, at TMC's 2011 Annual Meeting in Tampa, Fla., February 8-11, 2011.
VEHICLE ELECTRICS
Corrosion is very damaging to vehicle lighting and wiring because it will compromise the electrical system by causing a larger voltage drop across the corroded wire, says Adam Bean, new product development manager for Phillips Industries, a leading supplier, innovator and manufacturer of advanced electrical and air brake interface equipment for the commercial vehicle industry.
Anywhere there is an exposed connection allows for corrosion, he says. For example, connectors underneath the trailer are exposed to water splash back from the tires. The seven-way socket/plug is particularly susceptible because it is plugged in and out, allowing for debris to get in and start eating away at the terminals from the inside. Plus, this connection/disconnection gets cycled regularly, allowing for the spreading of pins.
Corrosion is particularly detrimental to LED systems because it attacks a lamp's most venerable point - its electrical connections, notes John Grote, vice president sales and marketing for Grote Industries, a leading manufacturer and marketer of vehicle lighting and safety systems. Lamps that are not secure and that have not been properly maintained can be "killed" long before they serve their life expectancy of 10-plus years.
Today's LEDs are often designed to uses dielectric grease and modular connection designs to resist moisture at the connection point, but still must be inspected regularly and the grease replaced when needed.
Corrosion is most often caused by moisture intrusion within a vehicle's electrical and power delivery system, he explains. "An electrical and wiring system can be compromised via leaking lamp connections, cracked lamp lenses, wire and cable abrasion, grit and sand damage, extreme temperature fluctuations, extensive flexing and exposure to moving parts.
"The chemicals used to treat the roads can accumulate on the equipment via road spray and will eventually ‘eat' away the components on a piece of equipment, including the electrical system. Chemical-based corrosion is prevalent on trailers, as the harness system is typically exposed to the elements."
In an effort to prevent corrosion, Grote says fleets and OEMs are employing systems that can fight off corrosion, and are using connections that are more secure, and thus require less maintenance, reducing the chances of having to unplug a connection to diagnose a problem. They are also providing sealed solutions, die-electric greasing anything exposed that can't be sealed and using water-tight methodologies, molding over connections to protect the wires/pins from wicking water into the harnesses, adds Phillips Industries' Bean.
What's more, many fleets and OEMs are moving to modular electrical systems. These can expand easily through standardized wiring segments with connectors that snap together and are designed with reservoirs for dielectric grease to provide enhanced moisture barriers.
New modular nose boxes are also becoming popular and feature consolidated, multi-pin connectors and water-resistant modular plugs, Grote adds. These nose boxes incorporate mounting systems with gaskets that prevent the migration of moisture.
PREVENTION ACTION
The best way to prevent corrosion on a vehicle is to be proactive. Don't expect; inspect. Regular inspection of the equipment and proper preventative maintenance measures are not only more effective than corrective maintenance, they are usually less expensive and easier. The objective needs to be to attack corrosion before it becomes a serious problem.
In addition, Grote recommends a regular and thorough examination of the vehicle's electrical system and lighting. Light fixtures, wires and cables should be inspected for cracks, corrosion, excessive wear and punctures and should be replaced immediately as issues are identified. Even small surface cracks and holes in a wire or cable can cause moisture to wick into the system.
Foam/protect any exposed loose wires, says Bean of Phillips Industries. Loose wires that have the ability to wiggle around and chafe will eventually lead to a breach of the system, allowing dead shorts and corrosion to start. Cable ties, split loom, die-electric grease should be used where ever necessary. Coat or die-electric grease anything that will be exposed.
Including a regular washing and cleaning schedule with routine preventive maintenance will further contribute to extending the life of the investment in a vehicle equipment, as well as promote a company's image, according to Jim Hill, president of JIM Mfg., a manufacturer of mobile brush wash systems.
Regular fleet washing, especially in winter conditions, gets rid of the road grime, salt and dirt build-up that can contribute to premature wear on dozens of vehicle parts, along with wear on the exterior finish, he says. Plus, a dirty surface has more drag than a clean one, so keeping a vehicle clean will save money on fuel over time.
Beyond that, a clean vehicle makes a more positive impression than a dirty one. "A clean fleet directly reflects positively on an operator," says Hill. "The vehicles represent the company to the public and customers.
There's a reasonable assumption that if a company is committed to this level of maintenance, there's an equal commitment to overall maintenance. By extension, this contributes to an overall positive impression of the company."
Eastwood Company's Murray also recommends regularly washing vehicles and applying salt neutralizing chemicals to areas of the vehicles that are most susceptible to rust and corrosion – fender wells, floors, rocker panels, bottoms of doors, suspension components, etc.
"Also make a habit of periodically checking the fleet for any signs of rust or corrosion and treat the areas as soon as possible," Murray says. "Top coat the areas that are treated with a good sealing paint to keep the corrosion or rust from spreading."
Protective coatings are the most widely used corrosion control technique. Essentially, protective coatings are a means for separating the surfaces that are susceptible to corrosion from factors in the environment which causes corrosion to occur. It should be noted that protective coatings can never provide 100 percent protection of 100 percent of the surface.
Top 10 ways to fight corrosion
Here are some key suggestions for fighting electrical system corrosion from Adam Bean, new product development manager for Phillips Industries.
1. Use heavy duty, adhesive-lined heat shrink tubing or heat shrink terminals on all electrical connections. This ensures a water-tight seal, additional tensile strength and sealed connectors to prevent contaminants from corroding the wire while maintaining the integrity of the electrical system. Tip: Keep a terminal repair kit in each truck for on-the-go maintenance.
2. Use an anti-corrosive protector spray on battery posts and terminals. This actively seals the metal's surface, preventing condensation, chemicals and battery acid from corroding the battery.
3. Always make sure ground leads go directly to the negative battery post. Grounding to chassis or engine will lead to corrosion, poor contacts and faulty electrical systems.
4. Use stowage devices when electrical and air coils are not in use for extended periods of time. This ensures that they stay a safe distance from destruction chemicals and water on the road.
5. Keep an anti-corrosion repair kit in trailers for corrosion preventative maintenance. These kits help drivers stop wire corrosion and make permanent repairs on the road, minimizing downtime.
6. Never puncture a hole in the wiring jacketing. Holes create leak paths for contaminants to "wick" into the wiring system, ultimately rotting wires from the inside out.
7. Wash equipment frequently to significantly reduce magnesium and calcium chloride build-up during cold weather. Do not power wash as water can be forced into areas and cannot escape, leading to corrosion.
8. Clean connectors every six months using a plug and socket brush with water - not soap.
9. After every cleaning, re-apply dielectric grease on plug and socket pins. This prevents the moisture deposited during the cleaning process from collection and eventually corroding.
10. Inspect cables and wiring regularly for early detection of corrosion. This offers a head start at recognizing and combating possible corrosive damage.
About the Author
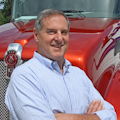