Along with taking up space, oil, lubricant and fluid storage, handling and dispensing can have a considerable impact on any maintenance or repair shop’s productivity, says Joe Murphy, president and general manager of Fireball Equipment Ltd., an industrial contractor, service center and wholesale distributor of fluid and lubrication handling equipment whose expertise includes lubrication and maintenance fluid systems.
For many shops, the traditional solution is to dispense lubricants and fluids right out of jugs, pails, kegs or drums, however, these methods present some issues, he says. “For one thing, with drum storage, accurate inventory control is very difficult. Too often, the drum runs dry before a technician has dispensed the necessary amount of lubricant.
“Another frequent occurrence is that empty containers and drums often have residual product left in them. Over time, that amounts to a lot of wasted product.”
Drums take up a lot of valuable floor space and can be messy, Murphy says. There is also the chance that shop employees might hurt themselves when handling the drums.
There are alternatives to traditional packaged lubricants that “can provide an easier, safer, cleaner and more accurate and efficient way to handle all kinds of lubricants and other maintenance fluids,” he points out. These include centralized lubrication systems where lubricants can be stored in bulk containers and dispensed through hose reels right into the unit being serviced.
MANAGEMENT SYSTEMS
“Without a fluid management system, it is difficult and time consuming for shops to track fluid changes in vehicles,” says Scott Hill, worldwide product marketing manager for Graco’s Petroleum Management Group. “These systems help record the date, technician, fluid type and amount dispensed into vehicles with relative ease.”
Graco is a world leader in fluid handling systems and components.
“Systems can dispense fluids, such as petroleum and synthetic oil products, transmission lube and antifreeze,” he says. “The systems provide access to data throughout the facility for automated tracking and monitoring, plus state-of-the-art dispensing for complete control of the fluid inventory.”
Fluid management technologies are evolving, notes Hill. “Older, wired systems can accurately meter oil and other fluids, but require technicians to walk to the parts counter where they make a request for the amount of fluids they need to dispense in their service bay. If the parts desk is busy with other orders or personnel are away from the desk, the technician must wait or come back later.
“In addition, many older systems only dispense fluids to one meter at a time. The technician might return to his workstation and have to wait his turn to dispense fluid.
“Neither one of these scenarios is an efficient use of the technicians time.”
Newer, wireless systems optimize technician time with systems that can provide accurate fluid inventory control, permit multiple fluids to be dispensed at the same time and allow the technicians to control the dispensing process at the service bay,” Hill says. These systems can also:
- Track vehicle fluids for more accurate and reliable metering and reporting.
- Track and maintain the correct level of fluid changeovers, from top-offs to complete fluid drains, and tie them back to the manufacturer’s recommended intervals.
- Support warranty claims with a complete history of fluid changes.
In addition, “wireless systems offer system installation and setup costs that are much less with far superior capabilities and flexibility over wired systems, he points out.
ELIMINATE WASTE
Len Badal, commercial sector manager, Chevron Lubricants, a leading supplier of lubricants worldwide, says “maintenance facilities can benefit greatly from an optimized storage and dispensing system for lubricants by preventing contamination, improving efficiency to deliver key lubricants at the right place, time and quantities and also help eliminate waste.”
Using programming dispensing equipment with meters can help manage the amount of lubricant that is dispensed to the working equipment, he says. “This helps eliminate waste from overfilling, and in the case of some products, such as grease, can help prevent damage.
“Overfilling cavities can lead to increased friction and heat or failed seals, which would then leak out grease causing lubrication starvation.”
STARTING POINT
When deciding upon the appropriate storage, handling and dispensing equipment and system, a shop must first know what lubricants and fluids it uses, the amount of each being consumed and how much of each type is used in any given area, says Fireball Equipment’s Murphy. The shop also needs to consider the different fluid monitoring and inventory management and control systems available to manage and record the usage.
Typically, bulk storage tanks or tote setups can be used for high usage type lubricants - usually 200 gallons or more per month, Badal of Chevron Lubricants says. With lower usage type lubricants, packaging such as drums, kegs, pails, gallon jugs, etc., can be used based on a shop’s monthly or periodic requirements.
“However, some areas for low volume usage can be in mini-bulk systems or with the direction towards environmentally packaging offerings,” he notes. “Bag-in-the-box concepts are taking off for lower volume liquid lubricants.
“The bag-in-the-box concept has primarily been focused on passenger car engine oils and smaller volume items, such as automatic transmission fluid and gear oils, but can be extended to industrial and commercial lubricants to help lessen the impact of steel or plastic containers in the environment.”
BULK PRODUCTS
When working with a shop to design and provide equipment configurations, one important piece of information Fireball Equipment gathers upfront is whether or not there is an advantage to using bulk lubricants delivered right to the vehicle rather than using packaged products.
“The answer falls into three categories: reduced product purchase costs, greater shop efficiency and less waste,” Murphy explains. “The savings from bulk products varies significantly between suppliers and packaging types, and shop operations vary, so each fleet maintenance manager needs to do the math on their own.”
To assist in this undertaking, he offers this sample worksheet. While the example is for oil, the worksheet can be used for any fluid.
Bulk Product Worksheet
Volume of product bought annually:
Savings per gallon:
Annual purchasing cost savings:
Number of oil changes per year:
Time saved per oil change (include time to get the packaged product, installation time and container disposal time):
Value of annual time saved (hours per year x value per hour of bay time):
Annual handling and disposal cost of packaging:
Annual value of retained fluid in packages:
Saving of prepaid disposal fees included in package purchase (typically $0.25/gallon):
Total handling, waste and disposal costs:
Total annual saving from buying and handling in bulk:
SYSTEM STRATEGY
When determining oil, lubricant and fluid storage, handling and dispensing needs, it is best to follow the fluid as it flows through the system and eventually gets recorded, advises Murphy of Fireball Equipment.
- Storage - Product can be stored in kegs (15 gallons), drums (55 gallon), totes (portable tanks, typically 250 gallons in size) or tanks (typically 250 gallons and up).
“Our recommendation is to size the tank to a minimum of two months usage, keeping in mind minimum delivery sizes and price breaks,” he says. “Tanks are relatively cheap compared to what you might be able to save by buying quantities on sale.”
Lubricants have very high flash points - typically well over 400 degrees F - so they are not classified as “combustible” or “flammable” products, he points out. “As such, there are typically no fire code requirements for the tanks, including requirements for certification, venting or containment, but you should verify this with your local authority.”
Oil storage tanks have traditionally been steel, often the “oval” furnace oil tanks, but increasingly “we are seeing plastic because of aesthetics, cleanliness and product visibility. Larger steel tanks can be epoxy-lined to minimize contamination and rust.”
According to Murphy, if volumes don’t justify it, kegs or drums can be used instead of tanks. Kegs are typically put on a dolly and rolled right to the vehicle. “This works well for low-volume, high-value lubricants, such as synthetic gear oils, especially now that the new wireless control systems can record the dispensing of rolling kegs.”
Drums are usually stationary and require an operator to switch over when empty. “This can be minimized by using a low-level cut-off to stop the pump when the drum is empty, and wall-mounting the pump so that a technician just has to move a stinger, and not the whole pump assembly,” he says.
“If the product that you need is not available in bulk, our suggestion is to install a tank anyway and transfer the product into the tank from the drum or tote. That way, you are not tying up space for containers and not changing drums partway through dispenses.
- Pumps - Oil systems use air-powered pumps almost exclusively because they are simple, inexpensive and they can produce a variable flow rate and “stall out” under pressure, says Murphy. Automotive shops require about 2 gpm; heavy truck shops usually 3 to 4 gpm.
“In order to generate the pressure to deliver these flows, these pumps need to be a minimum of 5:1 ratio,” he explains. “That means that 100 psi of air pressure gets multiplied to 500 psi of fluid pressure."
- Hose Reels - “The ideal layout is to have one set of hose reels for every two bays,” Murphy recommends. Typically, hose reels are spring rewind and usually need to be 50 feet long to reach from the ceiling to the floor and then to the vehicle.
“Spring rewind reels can be as long as 75 feet if the bay layout permits it and you are willing to have hoses stretched out on the floor. Theoretically, a single 75-foot reel can cover a 17,000-square-foot shop.”
- Dispense Valves - The “gun” on the end of the hose is available in a variety of configurations. These can range from an unmetered trigger, a metered valve to count the oil, a presettable metered valve that shuts off at a predetermined amount or a wireless controller that communicates back to a computer in the parts room that puts the dispense job on the work order.
- Grease - Grease can be distributed to hose reels or supplied in one or two rolling kegs that supply the shop. Either way, Murphy says, they use a 50:1 ratio pump that delivers 5,000 psi pressure or more to the dispense valve.
“For this reason, it is critical that all hoses, especially the flex extension on the dispense valve, be rated for high pressure. Underrated grease flex extensions that fail after they get worn can cause serious grease injection injuries and are a significant safety issue in the industry.
“It takes less than 100 psi to inject a substance through human skin.”
He notes that there are systems, like the Graco Topper-Inductor grease pump system, that ensure all the grease is removed from a drum or keg, and include an air-elevator to help swap out drums without damaging the pump. “These are not practical for portables but we highly recommend them for stationary applications.”
- Used Oil - Most fire codes classify used oil as a “combustible” product because it can contain amounts of fuel. For that reason, the typical tank needs to follow the local fire code, says Murphy.
“This likely will require a contained, certified, steel tank vented and equipped with an evacuation connection. It may also require mechanical protection from vehicle damage.”
Used oil is best transferred with a 1-inch air-powered double diaphragm pump, he says. This will evacuate from containers and drain trays at 5 to 10 gpm and will transfer it from the evacuation station to the storage tank.
“We do not recommend having a splash-fill location on the tank itself since this inevitably ends up as a cosmetic and environmental problem. Fill it with a pump and make sure you have some type of overfill protection to prevent spills.”
The size of tank is a function of how often the pick-up company needs to come and collect the used oil and what volume is generated.
- Control Systems - Fluid monitoring and inventory management and control systems have evolved from the traditional console at the parts counter to hard-wired options and wireless systems that can put the dispense right on the work order, observes Murphy.
Traditional consoles sit at the part counter and require the technician to go there to order product, costing productivity, he says. Second generation systems have a keypad out in the shop to allow a technician to enter dispensing requests which increases efficiency. The keypad controls fluid using solenoid valves installed at the fluid outlets.
Third generation equipment is totally wireless and can tie into the shop’s in-house computer system, he says. There are systems than can simultaneously control, dispense and monitor numerous locations, are able to create reports by product, user, customer or location and monitor fluid stock levels.
Because they are not hard-wired, wireless control systems are a good option for retrofitting existing shops, plus they can handle portable dispensing equipment that wired systems cannot, he notes.
PRODUCT CLEANLINESS
Proper storage, handling and dispensing guidelines are critical to ensure product cleanliness and performance in all types of equipment and all types of storage units, stresses Chevron’s Badal. “Improperly stored and handled lubricants can cause cleanliness issues and contamination, and that impacts equipment performance and useful life.”
Always ensure that dispensing lines and equipment are clean and that lines are periodically checked, and even purged, to make certain contaminants are not built up over time, or in the case of grease, that the thickeners don’t “harden” and block appropriate dispensing, he advises. Furthermore, in the case of changing lubricants, always clean storage and dispensing equipment to eliminate contamination or incompatibility, which will lead to equipment performance issues or damage.
The proper care and use of grease guns or keg/pail top dispensing units, is also important, as is keeping them clean and free of dirt or old grease to ensure correct application, he adds.
Frequently, the dispensing nozzle can end up on the floor or ground where it can pick up contaminants that could get inputted to a grease cavity, and causes problem. “Always be sure to store these nozzles properly and wipe them off before pumping in grease to the lubricated parts.”
It is best to “deal with lubricant suppliers that provide consistent quality of product and blending process to ensure all OEM specifications are maintained and product integrity is not compromised,” says Badal. “This becomes critical when any failures occur to ensure that warranties are covered and support is required for customer claims.
“Typically customers don’t realize the amount of testing required to maintain OEM approvals for quality products and some of the detriments to performance when short cuts are taken by less quality oriented suppliers. This can lead to costly failures and rejection of claims that can offset any savings in product prices.”
SELECTION CRITERIA
To see if a fluid management system is right for your shop, Graco’s Hill suggests contacting other shops using systems to get feedback on how their systems perform.
“Do some research to find out what the system features and benefits are so you can be certain it fits the needs of your maintenance department,” he suggests. “Contact a distributor to get an idea on cost, and realize that many systems can pay for themselves in less than one year.”
Regardless of the type of fluid storage, handling and dispensing equipment and system a shop decides upon, there are a variety of control systems available to ensure you have a record of the maintenance done on vehicles and all your fluids get billed out,” Murphy says. “From the tank to the control system, a well-designed lubrication system can make your technician’s work easier, save you money and increase the productivity of your maintenance shop.”
Air or manually operated grease pumps?
Air operated grease pumps are a big investment when compared to a manually operated grease cartridge guns, says Matt Weems, vice president in charge of marketing at Legacy Manufacturing Company. “But for those in the market for greasing equipment, air operated systems provide many advantages for shops where a lot of grease is used.”
Legacy Manufacturing offers a wide range of professional-grade service and maintenance equipment for automotive, industrial, contractor, agricultural and marine markets.
“First and foremost, air operated grease pumps are designed to fit on top of bulk - 35-pound pail or 120-pound drum - grease containers, which are more economical to buy over time than buying an equal amount of grease in the much smaller 14-ounce cartridges, he explains. “The larger container sizes also help to reduce the grease from being contaminated, as the grease is always covered after installing the pump and lid assembly on top of the container.”
In comparison, grease guns have to be reloaded more often, increasing the opportunity for the grease to be contaminated when changing cartridges or during the bulk loading process, he notes. What’s more, because the larger containers do not need to be changed as often as cartridges, productivity increases.
“Larger containers allow the shop to maintain better control of its grease inventory, and these containers can be stored away from the shop floor, preventing potential grease messes that are caused when cartridges are dropped.”
CUSTOMIZED SYSTEMS
Air operated grease pumps can be combined with hose reels and booster guns allowing for a customized greasing system, Weems says. Hose reels mounted above the service bay keep the hose off the floor for safety, as well as provide unconstrained access to wherever grease is needed.
Booster guns, such as those included with Legacy Manufacturing’s Performance Series, allows greasing pressures over 10,000 psi on demand, he says. “That means fresh grease is being delivered to bearings under load, or that clogged grease fittings are being cleared with confidence.
“The continuous flow of an air operated grease pump requires little effort when dispensing grease compared to manual grease guns.”
Are there benefits to oil, lubricant and fluid management systems?
Oil, lubricant and fluid management system can increase the quality of maintenance service and allow a shop to handle its lubrication needs quickly and accurately, as well as improve efficiencies and enhance profitability, says Scott Hill of Graco, a world leader in fluid handling systems and components. Such management systems can be used to a shop’s advantage and will pay for themselves for years to come.
Graco’s wireless fluid management system, by way of example, includes management software, dispense meters, tank level monitors, pump air controls and transceivers. Together, these components wirelessly talk to each other through an RF (radio frequency) signal to collect data from fluid dispenses and levels in bulk oil and waste tanks.
Wireless systems have easy-to-install bolt-on components with no special tools required, he says. Management software options are available to configure a system to the specific needs of a shop. If shop requirements change, the system can be upgraded or easily expanded with minimal investment.
Management software options include an e-mail function that automatically advises oil distributors and recyclers that service is needed, says Hill. Customized reports can be created and exported as Microsoft Excel files. System parameters can be customized to each application with security controlled passwords for the persons who will administer the system to ensure that inventory is completely controlled.
WIRELESS TECHNOLOGY
Graco’s wireless fluid management system’s dispense meters accurately supply high and low fluid flow to accommodate different dispensing requirements for different vehicles, says Hill. Meters can be set through the meter’s keypad to input service technician or work order information.
The tank level monitor provides the convenience of wirelessly transmitting tank level information, says Hill. An ultrasonic signal measures the fluid level in each tank and communicates this information wirelessly to the PC, keeping the shop informed as to when fluids need to be ordered.
“Once installed, everything is automatic, allowing for easy viewing and management of all tank levels without additional labor costs. The tank level monitor eliminates the task of manually checking the volume of each tank. Reporting on usage and ordering need are easy to gather from the database to be used as a planning tool for estimating and budgeting.
Transceivers receive an RF signal allowing the shop’s PC to communicate with dispense meters, pump air controls and tank level monitors, he explains. Units can be mounted to walls, ceilings, or any convenient surface in the main portion of the shop. The size of the shop will depend on how many transceivers will be needed.
The pump air control opens to supply air to the pump only when an authorization to dispense the fluid is received by the system. After the dispense ends, the pump air control closes the air supply to the pump.
“This adds another level of security to the fluid inventory, plus turning off the air supply protects from environmental spills in case of a line break and helps to avoid expensive clean up costs. Hill says.
How to choose hose reels
For years, overhead hose reels have been a staple of vehicle service garages.
“The main reason for using hose reels is to keep hoses off the garage floor,” observes Bill Parker, director of petroleum equipment service distributor sales at Lincoln Industrial, a manufacturer of lubrication equipment, fluid control systems, pumping products and technical service. “With technicians and customers walking around the bays, lubricant and air hoses on the floor could present a major tripping hazard.
“In addition to safety benefits, using hose reels allows a shop to buy lubricant products in bulk, yet still deliver fluid to each bay as needed.”
He says there are a number of advantages of buying in bulk, including lower cost of fluids, no empty bottles or drums to dispose of or recycle and more productive technicians with convenient access to lubricant products.
CHIEF CONCERNS
When purchasing reels, there are several points to consider, says Parker. Firstly, all reels look the same when they are new with an attractive coat of paint on steel. However, the strength of a reel is what is inside.”
Of all the equipment in a maintenance shop, he says reels may receive the most abuse, as they continually are extended and retracted. “Many times the retraction is without control. Each extension and retraction wears on the main spring which, if not properly chosen for the lubricant - high, medium or low pressures - will suffer premature wear and possibly breakage.
“The lever and spring that lock the reel spool in place during use also are susceptible to wear,” he says. “Be certain both of these items are sufficient in strength and design to handle the application.
“Look for a spool or sheave that is solid, not just pins that the hose wraps around. Without a solid base, the small pins that some manufacturers use will put a kink in the hose, restricting flow and causing premature wear.
“Confirm that the inlet and outlet swivels are appropriate for your fluids and pressures, and look for swivels that have unions that do not kink the hose as you install it.”
HOSE ISSUES
The hose that comes with the reel is critical, emphasizes Parker. “Be certain the hose cover is compatible with the fluids to which it will be exposed. Verify that the hose cover is smooth and wraps easily around the reel spool.
“Do not be deceived about the reel’s strength based upon the outlet arms. The actual strength of the reel is in the design, not the appearance. A single-arm reel can be just as strong as a dual-arm reel if properly designed.
“Consider a skyscraper when the wind blows. The structure sways ever so slightly to keep it from breaking. A single-arm reel does the same, giving slightly as you extend the hose to allow dissipation of the pressure on the reel.”
Single-arm reels allow for hose replacement or tension adjustment without removing the valve – a time saver when action is required, Parker points out. Many shops choose a dual-arm reel, preferring the appearance and extra stability it provides at the hose outlet.
“When properly selected, both single-arm and dual-arm reels will work comparably.”
“Reels, when properly positioned and chosen, provide a safer, more profitable and more productive workplace,” says Parker. “Select your reel based upon your actual requirements and its cost of ownership - not by its looks and price tag.
Product guide
A listing of companies that offer lubricant storage and dispensing equipment and systems:
Alemite, www.alemite.com
Balcrank Corporation, www.balcrank.com
Coxreels, www.coxreels.com
Dyna-Power, www.dyna-power.com
Fireball Equipment, www.fireballequipment.com
Fluidall, www.fluidall.com
Graco, www.graco.com
Hannay Reels, www.hannay.com
IFH Group, www.ifhgroup.com
JohnDow Industries, www.johndow.com
Legacy Manufacturing, www.legacymfg.com
Lincoln Industrial, www.lincolnindustrial.com
Liquidynamics, www.liquidynamics.com
Morsco Lubrication, www.morscoinc.com
National Spencer, www.zeeline.com
Reelcraft Introduces, www.reelcraft.com
Samson Corporation, www.samsoncorporation.com
About the Author
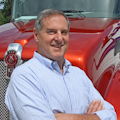