The growing number of aftermarket technologies being deployed by trucking operations today, including onboard communications and telematics solutions that connect technicians and drivers, bring with them the need for an efficient communication strategy about maintenance and support needs.
“Maintaining aftermarket technology products effectively is just as important to a fleet’s bottom line as scheduled preventive maintenance for trucks,” says Deryk Powell, president and COO of technology deployment services provider Velociti (www.velociti.com). “Upfront costs to deploy onboard technology range from 10 percent to 50 percent of hardware costs, and maintaining the long-term health and performance of the technology is a cost that must be accounted for as well.”
Cost effective turnkey aftermarket technology deployment and support incorporates everything from planning through the entire lifecycle of the solution, he says. “While focusing on making the right hardware and software choices is necessary, too often not enough consideration is given to developing a detailed plan for managing how aftermarket technologies for vehicles will be maintained, and how technicians and drivers should communicate about those needs.”
COMPOUND CHALLENGES
While aftermarket technologies can deliver transformational and measurable benefits to trucking operations, many fleets are also facing technician shortages. That challenge is compounded as well by the need for staff that is trained to maintain and repair more complex vehicle systems, Powell notes, causing the use of internal resources for maintaining even the simplest of technologies to have an impact on shop productivity.
“The focus for technology providers and fleets should be to properly plan and implement maintenance and support programs and solutions quickly and efficiently,” he advises. “It is also important to have a means of communication so everyone involved is informed of schedules and plans, and can access installation guidelines and reference materials, as well as updates when changes occur.
EASY COMMUNICATION
Allowing for transparent and easy communication between technicians, drivers and project managers, whether those are in-house or third party, is vital for the success of a technology maintenance program as well, Velociti’s Powell says.
In many cases, fleets approach technology project management internally by naming a point person and by using spreadsheets to track maintenance programs. “Those tools can be inadequate,” he observes. “A comprehensive solution for maintenance of aftermarket technologies can be more productive and lead to cost savings.”
As the adoption of aftermarket technologies continues to grow, Powell says that using an outside service for maintenance and support “can help fleets continually leverage their technology solutions and maximize their return on investment.”
About the Author
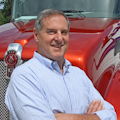