In a short time, telematics and connectivity have experienced an astronomical evolution, and fleet uptime will be the greatest beneficiary. The advancement in technology empowers fleets with vast new abilities—from sorting and analyzing asset data to scheduling maintenance and addressing issues smarter and faster than ever before.
What started with simple location data has transformed into the future fleet managers have long awaited. Now, they have tools that can predict when equipment may fail, supply a host of locations to send the truck for repairs, or schedule maintenance for less pressing matters.
It all started with fleets adding GPS sensors to understand where trucks are on the road. Things kicked into high gear following federal electronic logging device (ELD) mandates to track driver hours of service (HOS). Fleets were now required to have some form of telematics, allowing developers a larger customer base and a wider array of solutions.
This has led to the new revolution in uptime, as data can shoot right from equipment on the trucks—such as from engines and tire pressure monitoring systems—to management, who can now make more informed decisions.
The uptime advantage
Mike Keus, VP of the asset maintenance division at telematics provider Trimble Transportation, explained that uptime, a fleet’s main concern, impacts everything from asset utilization to driver satisfaction. Fleets can handle this when the trucks are near home base and have the bandwidth to tackle repairs, but trucks are always on the move—and technicians usually have their hands full with scheduled preventive maintenance. This creates major uptime problems.
“There’s a lot of inefficiency in the process when fleets are looking for outside repair,” Keus told Fleet Maintenance at American Trucking Associations’ Technology & Maintenance Council 2022 Annual Meeting & Transportation Technology Exhibition.
In a common scenario, Keus explained, once a driver notifies the office of an issue, the fleet manager or road call team will try to find a vendor and make a dozen phone calls to find parts. Then someone must fill out vendor repair orders in the fleet maintenance system and add service requests in the vendor system. Dwell time for unplanned repairs can average four to six days, at a cost of about $700 a day, he added.
“How do you reduce that communication between your fleet maintenance system?” Keus asked.
The company spent a lot of time during the show discussing their answer with attendees, and how the Trimble Connected Maintenance ecosystem and TMT Fleet Maintenance have undergone their own evolution. It has completed integrations with both TravelCenters of America and Navistar’s International 360 to allow drivers to automatically find a haven for quick repairs. Dwell time can be cut by two days, Keus revealed.
Now, he pointed out, when drivers use this telematics solution if the truck’s alternator is about to fail, the system alerts how long they can travel and then suggests the nearest vendor location. Enabled by connecting with TA and International 360, management can set priorities and preferred locations. Everything is streamlined and automated, where work orders are populated in multiple systems.
Fleets are leveraging these maturing technologies to reallocate road-call employees and other employees where they are needed.
Origins of telematics
Willie Reeves, director of maintenance at PacLease, recalled the humble beginnings of telematics, when it was used to track only the location of a specific unit, and noted how that compares to the technology of today.
“This was one of the first benefits of telematics, and it helped pave the way for the advances that we see today,” Reeves said. “In today’s ever-changing and expanding environment, we are not only able to simply track the location of a specific unit; we are able to see diagnostic information, fault codes, engine mileage, idle time, and even perform over-the-air software updates.”
Telematics and connectivity provide an easy-to-use solution for most fleets, Reeves said.“Fleet managers can now better understand maintenance requirements, truck conditions, and even predict potential areas to address,” he said. “The days of simple telematics—that only provide asset location—are long behind us.”
Fleets with thousands of assets know about these abilities, how they provide transparency, and more importantly, how they help plan scheduled downtime and decrease unplanned maintenance. But with this evolution of connectivity and telematics solutions, changes are happening so rapidly, there are now several strategies and options for all fleets.
Low-hanging fruit
Every organization has its own preference on what fleet management software and hardware is used to optimize operations. Minneapolis-based carrier Dart Transit’s fleet, which comprises about 1,100 trucks from three OEMs, has embraced several telematics provider solutions and uses them in their daily operations, according to Paul Pettit, Dart’s VP of maintenance.
This has enabled Dart to find connectivity solutions for both the truck and trailer sides, he said.
“There are several suppliers that have given fleets the ability to take what was a pretty simple trailer in years past and now have as much data sent to you as you want,” Pettit explained.
Sensors are included to address tire concerns, potential bearing failures, and inoperable lights, as well as cargo monitoring.
“Trucks can be even more detailed, with data coming from the engine, transmission, and tires, to name just a few,” he added.
These features are now standard on engines. For example, Detroit Diesel’s DD13 Gen 5 comes with the Detroit Connect suite of connected vehicle services. These inform fleets of vehicle health, fuel efficiency, and safety data. Specifically, the Detroit Connect Virtual Technician remote diagnostics service allows fleet managers to see within minutes if a fault event occurs, along with severity, and when, where, and how to best resolve the issue.
Daimler Truck North America took this a step further by partnering with Platform Science to offer Virtual Vehicle, an open OEM platform that lets fleets access telematics, software solutions, real-time vehicle data, and third-party applications right from the truck.
“With Virtual Vehicle, we offer our customers an open digital solutions and services platform that allows them to choose fleet applications that best meet their needs,” said Sanjiv Khurana, head of the connected services group at Daimler Truck. “The system is seamlessly enabled in our trucks without the need for installing any additional telematics hardware or the associated costs and loss of uptime.”
Navistar offers OnCommand Connection, an all-makes remote diagnostics platform, which for the OEM’s customers integrates with the International 360 solution, while Mack uses GuardDog Connect, Volvo has Remote Diagnostics, and Paccar relies on Paccar Solutions. There are numerous third-party providers as well.
Pettit identified spot-checking assets’ fuel efficiency as a major advantage.
“We use our telematics to review them on a truck-by-truck basis versus looking at one specific make model year and seeing how that entire model year is looking,” Pettit said. “From there, we look at what kind of outliers we are having, and if that idle percentage is driving down fuel economy or anything like that, and try to work toward educating drivers where we can on how to reduce idle.”
When it’s done right, these solutions can lead to a faster ROI, improve uptime, and increase vehicle total cost of ownership.
“If the fleet is able to act on the data and avoid costly repairs, the initial charge and possible monthly charge is not as painful,” Pettit said.
Data management
As maintenance VP, Pettit has many more responsibilities other than tracking asset data, so he does his best to avoid data overload–the point at which all that data becomes white noise.
“The challenge is having the systems in place to act on the data and take advantage of the technology chosen for your fleet,” he explained. “The amount of data incoming can be overwhelming, and it is too easy for maintenance teams to simply not act on any of the issues. You have to be able to choose strategically what data you want, and then work with it once you have received it.”
For Dart, this meant picking out what alerts to prioritize, such as those that would signal a breakdown.
“Those would be acted on quickly to help get the driver into a safer situation, expedite the breakdown, and still service the customer at the same time,” Pettit said. “By being proactive, we are able to help steer the course of action, which works for us much better than being reactive and working with a situation completely out of your control.”
Martin Günsberg, Ford Motor Company’s director of connectivity and new business communications, agreed.
“Access to real-time vehicle health helps fleet managers proactively service a vehicle to help avoid more costly repairs or worse, unplanned downtime,” he said.
Ford is newer to the telematics game but has picked up momentum with the creation of a new commercial vehicle-centric business, Ford Pro, and the launch of Ford Pro Telematics. With it, the light- and medium-duty segment now has a free option to gather data to improve performance, efficiency, and total cost of ownership.
It works with gas, diesel, hybrid, and electric vehicles, and comprises several cost-saving features such as instant odometer readings, diagnostic trouble codes, recall notifications, trackable maintenance alerts, and information around engine hours and oil life.
As customers transition to electric vehicles, Ford Pro Intelligence will link the services they need, including electric vehicle data such as live range, optimal time to charge, and charging products and services across depot, home, and public.
Günsberg reiterated the importance of collecting real-time data from your fleets’ operations.
“Vehicle health insights are critical to maintaining uptime,” he said. “A fleet manager no longer has to rely on a driver to inform them of a vehicle health issue. Vehicle health information is available in the dashboard to help make immediate decisions about a vehicle to maximize uptime.”Empowering predictive maintenance
The latest way to avoid data overload is by letting the cloud-based platforms do the heavy lifting through predictive maintenance.
One example is sending sensor data from the powertrain to an electronic control unit. From there, the data is transferred to connectivity devices that send the information off to the cloud. The platform then cleans and analyzes the numerous points of data to distill them into actionable insights for fleet management.
And it’s becoming more available for fleets big and small.
“Combining artificial intelligence and data off the trucks and from the shop, fleet maintenance platforms can filter oceans of data and find pearls of wisdom to help you make smart decisions,” explained Jessica Kim, head of marketing at Pitstop, a Canadian provider of vehicle predictive maintenance. “Alongside telematics, they use data to provide new opportunities across various business functions. But beyond impacting a company’s bottom line, the right fleet technology can effectively streamline and increase efficiencies on the day-to-day operations of fleets of many sizes.”
Pitstop reported its fleet customers have experienced a more than 20% reduction in downtime, saving up to $2,000 per vehicle, annually.
Predictive maintenance also helps eliminate some of the issues that will lead to breakdowns on the side of the highway.
“There is a huge safety concern with drivers broken down on the side of the road, so if we can identify a potential breakdown in advance, it helps keep our driver from an unsafe situation,” Pettit said.
Remote diagnostics are another advantage.
“If we look at just the telematics coming to us from our trucks’ engines, for example, we can quickly determine what the fault codes are, what dealers are closest, and the level of urgency related to the engine fault code,” Dart’s Pettit said. “Before telematics, we would have to attempt to troubleshoot with the driver, and we had limited visibility until the truck arrived at a dealer or company shop.”
Some fleets still operate with that minimal to nonexistent visibility.
“I can’t believe how many customers still work off of Excel and a war board,” said Brian Mulshine, Navistar’s director of digital service delivery. He said even smaller customers can leverage predictive maintenance with International 360 and the Advanced Preventive Maintenance feature. This can help fleets more efficiently manage preventive maintenance.
“We have the fuel economy for up to about 30 telematics providers and based on the fuel economy, we can suggest adjusting the maintenance interval,” Mulshine said, “because now you can stretch that oil change interval when you get better fuel economy.”
PacLease’s Reeves said advances in technology have made predictive maintenance an essential part of keeping their trucks and shops running smoothly.
“All of this ever-advancing connectivity and technology allows fleet and individual asset owners to have a better view and understanding of how to manage their equipment to increase uptime while driving driver and customer satisfaction,” he said.
With shops focusing on quality as well as speed of maintenance, predictive analytics offers insights in advance of potential failures that will occur, allowing ample time to notify the repair shop. It also helps avoid missing parts or increased shipping fees for a shorter turnaround.
A fleet can also customize what data the AI looks at and from there identifies trends and issues. For instance, they can query the system to check how many trucks in a fleet of 1,000 may have transmission issues based on similarities they share with a truck with a known transmission problem.
“You can send that data out and make loT of the dealerships aware of what’s going on and what to be on the lookout for,” Reeves explained. “It gets them involved, and that way they can take a look at things themselves.”Loading up with trailer telematics
Putting GPS-tracking sensors, cargo sensors, TPMS sensors, wheel-end sensors, lighting alerts, and more onboard and linking that to the tractor telematics is just the start of the next evolution of telematics: the smart trailer.
“It is a trailer that knows its current state. It knows its systems and its operation, health, and status at any given point in time,” said Nada Jiddou, EVP of Clarience Technologies and general manager of Road Ready. “It is also able to communicate that to the fleet—or the operator—comprehensively with a complete data set.”
Orbcomm’s Smart Truck array of solutions include a cargo camera sensor and Tractor ID sensor to ensure the correct tractor-trailer pairing, as well as integrations with Bendix to leverage safety and video data, and Noregon TripVision for maintenance insights.
Chris MacDonald, Orbcomm SVP of North America Sales, noted 70% of CSA violations are from maintenance or service problems, and data can help identify issues before a CVSA inspector does, which leads to more downtime.
“By providing real-time visibility into lighting, brakes, tires, and other components that are known to be usual suspects during roadside stops, telematics identifies many issues that are easily preventable with proactive trailer maintenance programs in place,” MacDonald said.
Several other telematics solutions already exist and are rapidly becoming more sophisticated. These include the PetersonPULSE trailer telematics system, DrŌv Technologies’ AirBoxOne comprehensive smart trailer solution, and ZF’s TrailerCAST.
ZF has advanced even faster after acquiring Wabco in 2020. The two sides have integrated their connectivity and safety technology to form ZF’s Commercial Vehicle Solutions Division. ZF customers are now able to see detailed histograms on tire pressure and temperature, as well as speed and load. Diagnostics provide alerts on if an axle load sensor fails, then provides management with service center information.
This requires some installation and maintenance considerations. That is also getting easier. At the recent TMC meeting, Phillips Connect announced a partnership with Utility Trailers to develop the Utility Connect solution. This combines Utility’s proprietary wiring harness with Phillips’ Smart7 nosebox, a smart trailer solution that can monitor ABS bulbs, ABS fault codes, automatic tire inflation system (ATIS) bulbs, air tank, tractor/trailer pairing, cargo status, door status, light-out status, regulator, TPMS, internal camera, wheel end, and more.
Because the evolution never stops, this technology has built-in expansion to allow for over-the-air communication updates that will integrate with advanced tire pressure monitoring systems and Bendix’s roll-stability system, trailer weight, air tank pressure, and optional brake pad wear sensors for disc brakes, Phillips explained.
“We’re not just in the GPS tracking business. There’s so much more than that,” commented Phillips Connect CEO Rob Phillips at the TMC Annual Meeting. “We’re talking smart trailers and adding a lot more than just ‘where’s my trailer.’”
About the Author
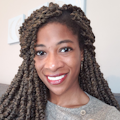
Faith Boone
Faith Boone has more than 15 years of experience as a journalist, public relations professional, strategic marketer, and entrepreneur. She has held several positions within the communications industry, and also enjoys giving back to the community through her work with various non-profit organizations. She is the founder of Boone Logic, a Cleveland-based content development and marketing consultancy.