Hydraulic monitoring solution enables uptime, maintenance transparency
HydraForce, a manufacturer of hydraulic components for mobile equipment, is collaborating with Elevāt, a provider of IoT connected machine applications, and Tan Delta, an equipment monitoring solution provider, to improve maintenance of hydraulic systems in mobile equipment. Elevāt's telematics solution will be integrated into hydraulic systems utilizing HydraForce technology, allowing the monitoring of system performance.
In October, the company announced a partnership with Tan Delta Systems — a manufacturer of real-time oil quality monitoring sensors. Through this partnership, Tan Delta's oil conditioning sensor can be integrated into manifold assemblies equipped with HydraForce's cartridge valves. This enables continuous monitoring of hydraulic oil conditions.
Adding Elevāt's technology to the mix will help machine users be more proactive with their maintenance practices. Its telematics solution provides a centralized portal through which hydraulic system information can be collected, analyzed and sent to machine owners and maintenance personnel as necessary. Email and text alerts can be sent, helping to ensure timely action for any hydraulic system maintenance needs.
"We started working with HydraForce on their telematics strategy early this year, late last year," said Adam Livesay, co-founder of Elevāt. "They take a unique approach in which they provide more of their subject matter expertise to their components and the applications their components power. They have a lot of history, data and information to give customers.
"The Internet of Things (IoT) accelerates that because now they can share what they as a supplier know about the way their components are operating with the OEM or channel partner and ultimately the end user," he continued. "Five years ago, that was not really the case with fluid power suppliers. That was kept internal. We’ve seen this change with our [various] partnerships."
Livesay also explained how the real-time motioning through the Tan Delta oil quality sensor, which measures current hydraulic oil condition and temperature, can enable predictive maintenance.
"It will [provide this information] and the rate that those things are changing over time," Livesay said. "This gives the fleet owner or machine operator immediate visibility into the current state of the oil within the hydraulic system. They can take immediate action if the oil condition starts to deteriorate because that is a major leading indicator of wear and component failure."
The solution should ensure expensive heavy equipment and work trucks stay on the jobsite and not in the shop.
"The reported information will prevent excessive wear of hydraulic components and catastrophic failures that can occur when machines are in operation, thus, leading to increased productivity, and reductions in machine downtimes and maintenance costs,” said Russ Schneidewind, Director of Business Development, HydraForce.
The data also helps on the preventive maintenance side.
“Through accurate monitoring of oil health, maintenance scheduling can also be optimized as equipment is serviced only when required, and operators can rest assured that any unexpected changes in the oil condition will be immediately detected and reported," explained Chris Greenwood, Managing Director, Tan Delta Systems. "This can also extend the operational life of equipment and overall machine health, as optimal oil conditions prevent unnecessary wear and tear."
Read more: Cummins, Elevāt collaborate to deliver next gen IoT connected services
About the Author
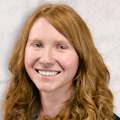
Sara Jensen
Sara Jensen is technical editor of Power & Motion, directing expanded coverage into the modern fluid power space, as well as mechatronic and smart technologies.
She has over 15 years of publishing experience, which includes working at her college newspaper as a copy editor and then an editor, as well as at a supply catalog company as a copy writer. Prior to Power & Motion she spent 11 years with a trade publication for engineers of heavy-duty equipment, the last 3 of which were as the editor and brand lead.
Over the course of her time in the B2B industry, Sara has gained an extensive knowledge of various heavy-duty equipment industries — including construction, agriculture, mining and on-road trucks —along with the systems and market trends which impact them. She looks forward to continuing to expand that knowledge to now include a deeper dive into fluid power and motion control technologies and the various markets in which they're utilized including heavy equipment and manufacturing.