There are many technology investments out there to improve fleet uptime, but dollar for dollar, none can transform your operation from reactive to proactive as much as the right telematics solution. And a proactive approach is absolutely critical right now, as effectively managing and anticipating vehicle maintenance needs avoids unnecessary equipment failures and costly emergency repairs.
Without telematics, fleets are usually reacting in triage mode after a vehicle has already broken down. Paperwork is often handled manually, preventing fleet managers from focusing on monitoring operations and analyzing data in real time. The result is a maintenance program that is highly unpredictable, extremely costly, and imposes a safety risk to its drivers.
Conversely, properly leveraging telematics can help ensure vehicles are operating at their peak performance. That translates into less downtime, higher fuel economy, and generally more efficient performance fleetwide. This also leads to better safety ratings, lower insurance costs, and more on-time deliveries.
Reactive vs. predictive maintenance
Looking into the future, the goal of telematics is to identify the tractor-trailers that will need replacement parts or maintenance work before any actual problem materializes. Advances in predictive maintenance are slowly being accomplished through artificial intelligence (AI) and the better analysis of existing data. At ISAAC Instruments, there is a team focused on the enhancement of artificial intelligence capabilities, including predictive maintenance. But it would be a mistake to wait until some future date to invest in maintenance technology. Every truck on the road today generates large amounts of data and diagnostic codes.
Telematics solutions immediately notify maintenance managers to problems and help prioritize fault codes to minimize downtime. Besides more rapidly uncovering emerging vehicle problems, leveraging telematics can help fleets make data-driven decisions when it comes to scheduling maintenance. You can target the vehicles most in need of service, which minimizes unplanned maintenance events and catastrophic failures.
Telematics can also help create maintenance schedules for your fleet based on the utilization of vehicles. These solutions help prevent the over-maintenance of lightly used vehicles.
Utilizing a Smart DVIR
While the maintenance staff may be responsible for keeping equipment in optimal condition, drivers also have a critical role to play in identifying potential maintenance problems during pre- or post-trip inspections. Electronic driver vehicle inspection reports (DVIRs) sync to a fleet’s backend and alert managers to any and all problems in real time. This ensures minor issues are caught and fixed before they turn into far more significant problems.
One safety executive shared during a recent webinar that ISAAC’s customizable Smart DVIR has resulted in a more than 50% increase in notifications from drivers of possible equipment issues. Drivers are able to transmit photos directly to the home office with the ISAAC tablet to show the maintenance team exactly what is going on. The team can immediately begin to diagnose the severity of the problem, and management can decide whether to tell the driver to pull into the nearest truck stop or complete the delivery and then return to a terminal for a closer look.
Savings over the long term
Research from the Technology & Maintenance Council and FleetNet America show that fleets with best-in-class maintenance practices have lower costs than competitors. By performing regular maintenance—and catching small problems before they grow larger—they are able to cut the frequency of emergency repairs and prolong the life of vehicles.
This is of growing importance to the many fleets holding their equipment longer, which a recent Fleet Advantage study attributed to lingering supply shortages related to the COVID-19 pandemic. Maintenance costs tend to increase during a vehicle’s lifetime as parts begin to break down more frequently. But vehicles that receive consistent and high-quality maintenance, guided by telematics, are sure to have a lower total cost of ownership.
Even telematics devices need maintenance
Even the best maintained equipment will inevitably break down or sustain damage. That includes not only tractor-trailers but electronic logging devices, too. When choosing a provider, fleets should consider hardware maintenance as well and how they will perform long term in harsh environments. How well that provider supplies replacement parts is also vital, as ELDs are federally mandated and a broken one will keep a truck off the road. ISAAC Instruments ensures 95% of spare parts orders or replacements reach their destination the next day after shipping. To minimize downtime, fleets should also keep several spare tablets, additional cables, antennas, power supplies, and other accessories such as tie wraps at their most critical locations. That way, they are better prepared for any unexpected problems.
No matter how safety-conscious a truck driver or fleet is, it is impossible to avoid equipment maintenance and repair issues. However, with advanced planning and the aid of technology, fleets can limit the impact these inevitable problems have on their bottom lines.
Melanie Simard is director of compliance, client service & technical support at ISAAC Instruments. She brings these groups together to ensure ISAAC clients receive best-in-class service and support, and to demystify all questions relating to regulatory compliance. She has over 20 years in the trucking industry, including stints as a driver, dispatcher and compliance manager.
About the Author
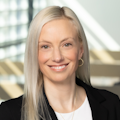
Melanie Simard
Director of Compliance, Client Service & Technical Support
Melanie Simard is director of compliance, client service & technical support at ISAAC Instruments. She brings these groups together to ensure ISAAC clients receive best-in-class service and support, and to demystify all questions relating to regulatory compliance. She has over 20 years in the trucking industry, including stints as a driver, dispatcher and compliance manager.