Rising costs, lack of labor top fleet leader concerns, Motive survey finds
The trucking business has always been a volatile venture, but the recent confluence of bad economic times and battered supply chain paired with technological disruption and labor issues has tested the resolve of even the toughest fleet managers.
"Throughout the past year, leaders in the physical economy grappled with rising uncertainties, escalating costs, increasing fraud, and a scarcity of skilled labor," said Shoaib Makani, co-founder and CEO of Motive, a provider of telematics, safety solutions, and fleet management software
Rising costs and talent shortages are nothing new, but the COVID-19 pandemic did exacerbate the situation Ryan Plutnicki, Motive’s chief customer officer, explained.
“There was a big amount of chaos that was generated during the pandemic,” Plutnicki said. “Then, for the years that followed, there was, in some cases, a big boon and, in some cases, a lot of turmoil.”
Motive identified the biggest areas of concern in recent survey of 1,000 leaders and decision-makers across a wide swath of sectors, laid out in the recently released Physical Economy Outlook 2024 report.
Here were what respondents said were the most pressing threats in the industry over the last 12 months:
• 59%: Rising costs of insurance premiums, fuel, maintenance, accident-related expenses, etc.
• 51%: Economic instability with interest rates, inflation, lack of access to capital, and more
• 45%: Labor shortages and talent retention
• 42%: Supply chain issues as a top concern of 2023.
• 36%: Operational efficiencies, such as mismanaged assets, lack of visibility into operations, excess admin work, and more,
• 33%: Extreme weather events
• 32%: Regulatory issues and changes
• 31% Worker safety
• 27%: Theft and/or fraud
Motive found in trucking and logistics, these challenges have cost companies an average of $1 million in losses.
Half of the survey participants took an optimistic view of the future, believing the economy will improve in next 12 months. About a third predicted things to get worse. All that uncertainty has taken a toll. Ninety-three percent of leaders within physical economy businesses felt “at least a little underappreciated, stressed or anxious at work on a weekly basis.”
One respondent encapsulated the existential dread, noting, “Our workload is insane and we can’t retain workers at all. With the labor shortage everyone else has to work 60+ hour weeks.” On the bright side, 52% were more satisfied with their job this past year versus the previous one.
Fraudulent activity
Another interesting finding from the survey was that less than one-third of respondents (27%) listed theft or fraud as a top industry concern, but the mood changed when asked questions concerning fraud. Almost half of fleet managers and directors (44%) believe their business has been negatively affected by fraud, and even more respondents from the C-suite (57%) feel fraud has a "big financial impact" on their business.
Fraud and theft can take many forms, making it difficult to track and prove. Cargo theft is becoming more prominent, with incidents increasing by 59% year-over-year in Q3 of 2023. Additionally, employees can commit fuel fraud by filling up the tanks of their personal vehicles using company fuel cards.
"Fraud was an interesting (finding) for me," Plutnicki said. "When I dug into that a little bit, I kept getting this interesting theme, which is fraud that is intentional is a concern, but so is fraud that's unintentional."
An example of unintentional fraud Plutnicki offered is when an employee uses a fuel card, intended only for a fleet vehicle, in their personal vehicle when traveling from one job site to the next instead of using a company's standard personal mileage reimbursement.
"They have no idea that they're going against policy, but they just filled up a tank at $65 as opposed to the $12 they should have gotten in the mileage getting to the second site," Plutnicki said.
Enterprise fleets estimate an annual loss of 19% due to theft and fraud, whereas smaller fleets estimate an average annual loss of 16%. Technology, fuel cards, and asset tracking can help decrease those numbers.
Visibility is the key
Makani asserted that in a time of “limited visibility and data silos hampering profitability and heightening safety risks,” technology such as artificial intelligence can be a “game changer” in terms of offering new opportunities.
Introducing data into fleet operations can significantly impact efficiency, with Motive customers reporting 91% improvement in safety, 50% less time spent on manual paperwork and processes, and a 20% savings in insurance, fuel, and maintenance costs.
“I cannot imagine trying to manage the amount of data and the safety events the technology is pulling in,” Jared Whitson, director of safety at Bennett Family of Companies, shared in a Motive report. “The efficiencies that the platform has added, where it’s doing a lot of that work for us, that’s a huge deal.”
Fleets that aren’t using data analytics to make informed decisions—or those that aren’t capturing fleet data at all—put themselves at a disadvantage. But even those who collect data and use fleet management systems find it challenging to manage their fleet more effectively and efficiently.
One repeated theme in Motive’s report is visibility due to using multiple methods of data capture and fleet management. Simply having awareness and visibility can put fleet leaders at ease.
Unfortunately, one-third of respondents admitted not having the visibility they need to do their jobs effectively, and 42% said they lack a “single view” into their vehicles, workers, spend/payments, or equipment/assets.
This need for a “single view” could likely be attributed to fleet personnel using multiple tools to manage their operations. Survey results indicated that 46% of fleet leaders admit to using more than 10 different individual tools to help them manage their fleet. Another 30% said the tools used to manage their fleet are “too many to count.” One in five are still using pen and paper to manage their fleet. Using this amount of tools without a proper management system can lead to inefficiencies in time, reduce profitability, and increase safety risks.
What’s more, a lack of proper fleet management systems and processes can lead to lost assets. Of C-suite respondents, 63% admitted to losing track of vehicles monthly, and 34% of respondents in management/director roles admitted to losing vehicles monthly.
When properly tracked and analyzed, data has been proven to increase operational efficiency. More than 80% of respondents agreed that although industry challenges persist, data capture has helped them make better decisions.
Embracing technology
Fleets that have already integrated technology into their operations have an advantage over fleets that still use pen and paper to manage their systems, as stated previously. But that doesn’t mean technology comes without its challenges.
Many leaders (40%) find their current technology solutions unreliable and inaccurate, according to the survey. One of the top reasons these leaders aren’t pleased with their technology solutions is that, as with their operations, they “lack a single view” of the operations of their workers, vehicles, assets, and spend/payment (42%). Another aspect that fleet leaders find just as concerning is data security and privacy concerns with their technology solutions (42%). Additionally, 41% of respondents find technology solutions lacking because of their “data silos” or “lack of integration” within other fleet management systems.
But as technology evolves, Plutnicki thinks fleet management systems and data analytics will become more integrated and offer that “single pane of glass” visibility that fleet managers are looking for.
More than 50% of survey respondents indicated that they liked their jobs better this year than they did this time last year, and Plutnicki thinks that’s a “nod toward the optimism of where this technology is going.”
“It’s not 100% solved; this is a journey,” Plutnicki said. “Bit by bit, we’re bringing (these systems) all together. … Our goal is certainly to continue to put as much of it as possible into the ‘single pane of glass’ where it makes sense for us to be best in breed and then also integrate very deeply with the top partners that we have.”
A version of this article originally appeared on FleetOwner.com.
About the Author
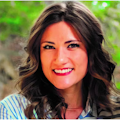
Jade Brasher
Senior Editor Jade Brasher has covered vocational trucking and fleets for the past five years. A graduate of The University of Alabama with a degree in journalism, Jade enjoys telling stories about the people behind the wheel and the intricate processes of the ever-evolving trucking industry.