A way to improve maintenance practices is to learn and adapt best practices through cross-industry innovation. Looking at what other organizations have done and do has the potential to provide creative and adoptable ideas.
A recent issue of Mass Transit Magazine had the article, Improving Efficiencies in Your Maintenance Department. It shared what some mass transit agencies are doing to more effectively manage their maintenance operations.
Mass Transit and Fleet Maintenance are both part of Southcomm’s Transportation Group. Southcomm (www.southcomm.com) is a publishing and communications company.
Some of the techniques, excerpted from that article, can be adapted to fleet maintenance operations.
TOOLBOX TALKS
Palm Tran, the public transit bus system that serves Palm Beach County, Fla., hosts formal meetings at toolboxes at its two maintenance garage locations on all shifts every 30 to 45 days. All maintenance employees – including managers, mechanics, paint and body specialists and parts room specialists – are welcomed to participate.
Facilitated by a company training and technical specialist, topics include safety, upcoming training opportunities and current affairs at Palm Tran. Then, the meeting is opened up to maintenance staff to share information, concerns and knowledge.
Lasting anywhere from 10 to 20 minutes, these toolbox talks are intended to be quick and brief, so as not to disrupt employee workflow.
EMPOWERMENT
NEM Solutions, a company that offers management solutions to businesses responsible for the operation and maintenance of multi-system assets, recommends three things be at the top of a shop’s list of things to do:
1. Current situation assessment. What is the real level of efficiency? How capable, or performing, are your resources? Is information shared or are the operations organized in silos? Does everyone share goals and objectives?
These aspects are very important to assess how functional/dysfunctional an organization is. Only by understanding how bad the situation really is there will be real a chance of fixing it.
2. Maintenance program roadmap. The final destination needs to be clear to everyone in the organization. Outlining the reasons why things are done, explaining the process and detailing the goals and benefits at the end of the process is a great way of bringing all stakeholders onboard.
3. IT/Quality management. The support of IT tools and processes will be of great help to accomplish objectives and goals. Any organization needs to generate knowledge and put it to good use.
PFM
Huge efficiencies were be gained through the use of a paperless fleet management (PFM) system at Victor Valley Transit Authority, Hesperia, Calif. Switching to this system provides quick and easy access to real-time data on fleet information, current vehicle repairs and vehicle history.
The features of its PFM system saves significant man hours when reviewing work orders, preventive maintenance inspection (PMI) information, parts inventory and repair history. It also has a paperless PMI program that produces auto-generated work orders for failed line items, enhancing accountability by ensuring failed items are resolved.
Tablet technology is also used with its PFM system. This provides technicians with one-touch access to vehicle- and component-specific shop manuals and historical maintenance data while on the go. It is also used to easily perform PMIs, providing technicians access to all pertinent vehicle data.
About the Author
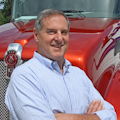