The Best Reasons Yet To Get The Latest Smartphone
Smartphones transformed digital photography. Now, almost everyone has a decent camera in their pocket.
Think back just a decade or two. To transmit photographic images required that you take a photo, have the film processed (and get extra copies, if need be), put the photo in an envelope, write a note to go along it and mail it to the person you wanted to share that photo with. Now … just shoot and send.
Every generation of new smartphones has significantly improved its digital cameras. The current generation of smartphones take excellent photos easily, plus it’s simple and extremely quick to transmit the photo to others.
Your Camera On-The-Job
Why do we take photos? For a wide range of reasons. Among them, to:
- Help remember a job
- Show us a job that needs to be done
- Provide information to insurance companies
- Record what happened for an investigation or a RCA (Root Cause Analysis) effort
- Help with training
- Remind people of the proper steps or how something was done
- Record deterioration of an asset over time, or to show improvement
- Document construction before it is covered up
- Support a warranty claim
Good Practices
Photos help us remember a job so the next time we do it we have something to reference. Photos can also show the steps of taking something apart, setting up a machine, installing or commissioning a machine, etc.
In the maintenance world we may not do a large job but every 10 years or so. It’s great to have photos from the last time you did it to tell the story of what was done, as well as special setups, custom tooling, etc.
A good maintenance practice is to plan and then schedule jobs. One challenge to planning is establishing the scope of work. Good photos can show the planner the extent of the work, as well as any potential hazards that need to be dealt with in the job plan.
Contractors
It may be necessary on occasion to bring in a contractor to do a job. Frequently, a contractor can bid off of photographs or at least understand the basics of the job.
Obviously, on complex jobs, we would require the contractor to physically look things over and not just base their price on pictures. But for simple jobs, photos may suffice.
Moreover, photos can be sent to a vendor for identification of a part.
When we have an incident of any kind, we want to record visually as much of the story as can be captured. The information gathered might help us understand the causes for the incident.
Photos of accident scenes, damaged equipment and damaged parts can frequently explain what happened and support an insurance or warranty claim.
On the Shop Floor
One old-timer told me that 85 percent of all maintenance skills and knowledge are taught on the shop floor. Maintenance departments do almost as much teaching as a typical school.
Photos and videos – because they can compress enormous amounts of detail – are adjuncts to on-the-job training.
Documentation
Some deterioration is quite subtle. Slight changes in an asset are difficult to detect without something to compare it to.
Photographing an asset over time, from the same or similar vantage point, can make it much easier to detect deterioration. The same goes for documenting the effects of improvements over time.
Sometimes when we make an improvement, modification or rehabilitation of an asset, we want to document the story via photos for people who are not on the shop floor but might appreciate the work that’s going on. Gantt charts and network diagrams only go so far to show what you’re doing, but photos can really tell the story.
Joel Levitt is director of projects for Reliabilityweb.com’s Reliability Leadership Institute. Reliabilityweb.com provides the latest reliability and uptime maintenance news and educational information to help make asset managers, reliability leaders and maintenance professionals safer and more successful. The Reliability Leadership Institute is a community of practice to improve how organizations deliver asset performance through the use of Uptime Elements, a reliability framework.
About the Author
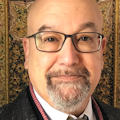
Joel Levitt
President, Springfield Resources
Joel Levitt has trained more than 17,000 maintenance leaders from more than 3,000 organizations in 24 countries. He is the president of Springfield Resources, a management consulting firm that services a variety of clients on a wide range of maintenance issues www.maintenancetraining.com. He is also the designer of Laser-Focused Training, a flexible training program that provides specific targeted training on your schedule, online to one to 250 people in maintenance management, asset management and reliability.