To thrive, a company must hold on to its best assets, and in the modern transportation industry, which is filled with ever-evolving, highly complex equipment, technicians with diagnostic expertise are among a fleet’s most valuable resources. Who else can troubleshoot those phantom engine fault codes and get commercial vehicles back on the road?
But holding onto techs may become an issue. According to a 2022 survey by WrenchWay, a company dedicated to promoting technical schools and connecting technicians with shops, 80% of technicians have considered leaving the industry, with 70% of them experiencing job burnout, and more than 50% considering leaving due to problems with a manager.
These are grim statistics, but your fleet doesn’t have to add to them. To find out how to prevent your diagnostic techs from reconsidering their employment, you need to know how to troubleshoot their on-the-job issues. That’s why we spoke to Talon Thomas, product management technical engineer for diagnostic tool provider Noregon Systems and a former diesel technician.
Fleet Maintenance: What’s a day in the life of an average diagnostic technician look like?
Talon Thomas: Often, places I worked had 7 a.m. to 10 p.m. operating hours where the first shift worked until 3:30 p.m., then the second shift came in at 1:30 p.m. to 10 p.m. Some shops offer 10-hour days so they only have to work four days a week, which would have workers coming in at 7:30 a.m., then clocking out at 5:30 p.m.
Typically, you’d have a selected set of work orders curated by the shop foreman and the other supervisors. Once you get those, the first step is to verify the customer complaint. Sometimes that’s a straightforward ordeal; other times it requires getting ahold of the customer and talking either with the customer directly or with the driver to try to get a better understanding of what may be going on with the vehicle. Verifying the customer concern is very important because you don’t want to waste your time and you don’t want to waste the customer’s time, either.
Getting any kind of tips or tricks that the driver is aware of that may not be mentioned on the work order could also go a long way to duplicating a concern. And then, using the resources that you have available to the shop as well as inside your own mental toolbox, you typically have two to four hours to try to connect the dots to take the root issue and repair it, whether that be physically repairing it or presenting a case of why you may need to replace certain components.
FM: You’ve told us before when you were a diagnostician, it was really hard to find a laptop becaue there were not enough in the shop. What kind of tools today do techs really need to do their job and to get the best uptime?
Thomas: Resources are absolutely critical. There are certain resources that technicians are expected to have, like hard tools, and certain diagnostic tools, like multimeters and even oscilloscopes. The things that a diagnostic tech may not have are usually furnished by the shop, like scan tools, service tools, diagnostic tools, access to work orders, and reporting systems’ data to look at repair histories. If you’re a dealer, having all of the dealer-level uptime resources available to the tech right when they need access to it is critical.
See also: Three ways to train and retain quality entry-level technicians
FM: Is it more important to have enough tools to outfit the technicians in the shop or have enough technicians to address the labor shortage?
Thomas: You obviously need technicians to handle the work, but at the same time, as far as management is concerned, you really need to be aware of which technicians are going to become resource-constrained first. So, out of all of your technicians that are currently in your shop, who are the ones responsible for triage and are really good with diagnostics?
You really don’t want to constrain the resources that they need to get their jobs done because they can usually diagnose something efficiently and correctly if they have the time and they have the resources in front of them. And at that point, once the diagnosis is made, and a part needs to be replaced, it can get passed down the line to somebody that’s more in their wheelhouse replacing components.
So, yes, there is a technician shortage, but you should be aware of the capabilities of the techs who you have in your shop, the ones that are going to bring the trucks in and initially address their concerns. They need as many resources as they can possibly get their hands on so they can get the truck from diagnosed to moving into the repair phase.
FM: Would you say that the growth of integrated electrical systems is making it more or less difficult to diagnose problems? Even with diagnostic telematics, is it now easier to confuse symptoms with the cause?
Thomas: It is, but at the same time, it isn’t. To the trained diagnostic tech, he or she should not feel an increase in pressure or difficulty in diagnosing. Part of the diagnostic tech’s responsibility is to not just know that certain components exist, but part of what makes them effective is understanding the root of how certain things work. If you understand what the engineering team has developed for this vehicle, even if you’re not involved at the OEM level, and if you understand fundamentally how certain components are designed to get along and do their jobs together, then as long as you have that understanding, diagnostics are relatively straightforward.
Regardless of how many more additional ECUs are on the truck or how or many different types of networks there may be, it all comes down to the same thing. The components themselves have a job to do. And whether the component is directly responsible for a task or it has to talk to some other controller to say, “Hey, I need you to do this,” as long as the tech understands those differences, then his or her job stays relatively the same.
FM: What are some ways that technicians can keep pace with the speed of technological development?
Thomas: Training, training, and training. And beyond that, good diagnostic techs, even outside of work, will continue to research, dive into things, and try to understand how certain things work. And training is usually the first place that you get exposed to new systems or new concepts that have been created or that are coming out on certain vehicle lines. A good diagnostic tech will anticipate those things, so when they see them coming into their shop and their bays, they’ll be able to say, “Oh, yeah, I remember this.” And they’ll go and look at the materials they have available and all the resources that they might have.
FM: Is it important for even the most experienced technicians to have a path for career development?
Thomas: In my experience, as a technician, there will be a point where you, as a tech, know all the diagnostic tricks of the trade for all the particular vehicles that you come across on a day-to-day basis; you’re very familiar with all the pattern failures, and there’s not much that can come into the shop that will surprise you. There are certain folks, once they get to that point, who are completely comfortable, and they will continue to work that way until they retire. But then you also have certain techs who are always looking at different avenues. The last thing management in a shop wants to hear about is providing ways and paths to have their top technicians find someplace else to work. But it is a valid point, because if those techs at the top of their chain reach a point where there really isn’t much new challenge, that may be something to watch out for as a manager.
FM: To keep those long-term technicians engaged, would diagnosing new technologies such as electric vehicles or hydrogen fuel cell trucks be something that management could offer to provide education and enrichment?
Thomas: From a management perspective, absolutely offer that opportunity to those top techs, because it’s one more skill set under their belt if they come to master it. Most diagnostic techs are looking for things like that. If they’re not familiar with electric vehicles, alternative fuel vehicles, or hydrogen vehicles, but then all of a sudden you’re saying, “Hey, we’re going to start seeing more of these in the shop, and we want you to be the guy to triage these or diagnose or repair these,” that’s new and exciting. And being the guy to oversee that, that keeps interest in employment as well.
FM: Would you say that there’s a way to track that interest and productivity as you’re keeping an eye on both your new and advanced techs?
Thomas: Having management come down to [the technicians’] level, even if it was just for weekly one-on-ones. Just give them 30 minutes of personal time; it makes it less evident that this is a system of productivity. That can hurt morale in the shop, especially if technicians start feeling like they’re just a number on some spreadsheet. Just bring yourself down to the tech level every once in a while and talk shop with them. It makes the day go by so much easier and brings so much more respect to you as a manager.
About the Author
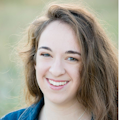
Alex Keenan
Alex Keenan is an Associate Editor for Fleet Maintenance magazine. She has written on a variety of topics for the past several years and recently joined the transportation industry, reviewing content covering technician challenges and breaking industry news. She holds a bachelor's degree in English from Colorado State University in Fort Collins, Colorado.