Failures are commonly the result of a cascade of events. This cascade will be slightly or grossly different for different failures. Preventive maintenance (PM) developed for failures, where there is an intervention, can interrupt the cascade.
PM is not a pancea and does not address all types of failures. Failures that are random cannot be predicted or even mitigated by PM.
Consider tires, for instance. While tire life can be impacted by a PM program that keeps tires filled with air and replaces them when required and matches duals, it has no, or little, impact on road hazards.
Bearings
Bearings serve as a good example of failures due to a cascade of events, because the details of their deterioration can be more easily seen than some other vehicle components.
As a bearing deteriorates, energy efficiency (increased friction) and performance (some horsepower tied up in driving a powertrain producing heat instead of rotation) also deteriorate. Other symptoms might be roughness, noises and heat.
The following is an example of a cascade of events caused by a bearing from a piece of agriculture equipment used on a farm in Saudi Arabia. There, sand is ever-present and the summer temperatures top out above 120 degrees Fahrenheit.
Here is the cascade for the bearing failure:
1. Dirt enters the bearing.
2. Dirt mixes with the grease.
3. The grease becomes less slippery and hones the balls and races.
4. Vibration is caused from the less than smooth surface.
5. Heat is generated.
6. The heat cooks the dirty grease, further degrading the grease. (In some cases, the heat may become hot enough to start a fire).
7. The bearing steel changes (maybe softens).
8. The bearing goes out of round or allows greater movement between races and balls.
9. The greater movement makes vibration, accelerates deterioration and loosens fasteners, producing a rough ride, noise, poor tracking, etc.
10. Eventually, the bearing fails.
In RCA (Root Cause Analysis) parlance, the whole picture of these events is called a cause tree. If you follow it through, one event causes the next event and the next event causes the event after that.
The Goal of PM
There are two main objectives of preventive maintenance:
1. Stop the initiating conditions that lead to a failure. In the case of the bearing example, this might include cleaning out the dirt before it becomes a problem, replacing or supplementing the lubricant, tightening the bolts loosened by vibration, etc.
2. Notice when the cause tree has started. This includes all types of inspections and the use of technology to detect physical manifestations of the cause tree.
If you interrupt the cause tree at any time, you will stop the natural deterioration leading to the failure.
In the bearing example, if you are slightly late in doing this, you still will have a corrective bearing replacement but no failure, and more importantly, no failure consequences.
PM is an organized attack on the cause tree.
Step in the Cause Tree |
What the PM is Doing |
Dirt enters bearing. |
Clean to get rid of dirt. No replacement needed. |
Dirt mixes with grease. |
Lubricate to replace grease that is deteriorated. No replacement needed. |
Grease becomes less slippery and hones balls and races. |
Lubricate to replace grease that is deteriorated. No replacement needed. |
Vibration. |
Inspect. Clean and replace grease to get adequate life. Otherwise, replace. (Vibration provides the longest interval between what is detectable and the failure.) |
Heat is generated producing added friction. |
Inspect and initiate corrective repair to lengthen interval before failure. |
Heat cooks the grease/dirt degrading grease even more. |
Inspect. Check for loss of oil film protecting the bearing. Replace soon. |
More heat (in some cases high enough to start a fire). |
Inspect. Replace very soon. |
Bearing steel changes (maybe softens). |
Inspect. Replace as catastrophic failure could occur at any time. |
Bearing goes out of round or allows greater movement between races and balls, making noise. |
Inspect. Replace as catastrophic failure could occur at any time. |
Greater movement makes vibration, accelerates deterioration and loosens fasteners. |
Inspect. Replace. If a wheel bearing, take unit off the road until the bearing can be replaced.
|
About the Author
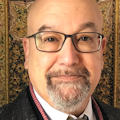
Joel Levitt
President, Springfield Resources
Joel Levitt has trained more than 17,000 maintenance leaders from more than 3,000 organizations in 24 countries. He is the president of Springfield Resources, a management consulting firm that services a variety of clients on a wide range of maintenance issues www.maintenancetraining.com. He is also the designer of Laser-Focused Training, a flexible training program that provides specific targeted training on your schedule, online to one to 250 people in maintenance management, asset management and reliability.