Maintenance productivity is very important, especially since vehicle maintenance creates added value to a fleet’s business process.
Simply put, productivity is the ratio of output to input. The more effective and efficient a maintenance operation is, the greater its productivity.
While there are a variety of methods for measuring shop productivity, a best practice for this has been developed by Technology & Maintenance Council (TMC), North America’s premier technical society for truck equipment technology and maintenance professionals (www.trucking.org).
Its Recommended Practice 804A, Labor Productivity Measurement, provides a basic set of standard forms, instructions and guidelines to measure labor productivity. Plus, it discusses how technician productivity is the end result of their skills, supervision and work environment.
“Labor accounts for approximately 60 percent of the dollars spent by a company to repair and service equipment,” note TMC officials. “The size of this expenditure demands that labor be used to the best advantage.”
Recommended Practice 804A is included in TMC’s updated Recommended Practices Manual 2014-2015 – a comprehensive guide to equipment maintenance and maintenance shop management that includes more than 3,100 pages of technical information.
For more information about the manual, contact ATA Business Solutions online at www.atabusinesssolutions.com or phone 866-821-3468.
About the Author
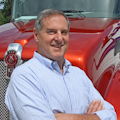