Most of us in the maintenance field think in terms of our CMMS (computerized maintenance management systems) primarily being a WEM (Work Execution Management) tool. CMMS helps us manage things like planning and scheduling, stockrooms, preventive maintenance (PM), driver inspection and trouble tickets, etc.
In fact, CMMS are the hub of the whole reliability program. Beyond that, they anchor any notions of operational excellence we might have.
A good computerized maintenance management system has complete and accurate data about acquisition cost and specifications, all maintenance activity, fuel consumption, tire data, PM and spare parts. It may have operational data also – or at least access to it.
When we view Reliability through the lens of the Reliabilityweb.com’s Uptime Elements – a system for asset reliability and performance management, we realize that WEM is only one domain that is open to us. There is also AM (Asset Management), REM (Reliability Engineering for Maintenance), ACM (Asset Condition Monitoring) and LER (Leadership for Reliability).
I want to briefly review each domain and highlight one or two opportunities from each.
AM
The field of Asset Management has gone viral with the adoption of ISO (International Organization for Standardization) 55,000 – the first set of International Standards for Asset Management.
What is frankly weird about the standard is that Asset Management is not really about managing assets. It is about managing the value or potential value that you get from the asset, as well as managing risk, from wherever it comes from.
Asset Management is looking at every step of the asset’s life – from conception (business case), specification, acquisition, operation, maintenance and disposal. Most computerized maintenance management systems can be used to manage the information to optimize the whole process.
In some cases, we make acquisitions based on personal prejudices. In others, we decide based on the latest catastrophe. In any case, on average, a data-driven decision will produce low costs and higher value to the organization.
Guess where to look for this information and guess where I say to store your analysis? In your CMMS.
This goes for every step through disposal. Do people ask: What was our operating assumption when we bought the asset and how did we do? Did we guess high or low on disposal?
It all feeds into providing value to our organization and managing the risk to provide that value.
REM
Our field, due to history an d inclination, is weak in the area of Reliability Engineering for Maintenance. How many fleets have a qualified engineer looking at its data and making recommendations for improvements to lower costs, improve safety or extend life?
There are many opportunities for REM, and once again, the data can be found in the CMMS.
REM can be used to get the most use and life out of a piece of equipment. Once again, the data can be found in the CMMS.
ACM
One big area of action is dealing with the data output from the unit itself.
A modern Caterpillar haul truck in a mine operation has 145 sensors and an onboard system that scans them every second. This information, along with the equipment’s Masterfile information, can give us a real-time look inside the equipment to predict problems.
Even last year’s computers would choke at that amount of data for a whole fleet that comes from the field of big data analysis using cloud-based tools for deep analysis.
This is happening right now and will become a hotbed of innovation in the next few years.
LER
All this leads to having Leadership for Reliability that can make intelligent decisions based on facts, data and analysis.
Joel Levitt is director of projects for Reliabilityweb.com’s Reliability Leadership Institute. Reliabilityweb.com provides the latest reliability and uptime maintenance news and educational information. He remains president of Springfield Resources (www.maintenancetraining.com), a management consulting firm.
About the Author
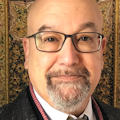
Joel Levitt
President, Springfield Resources
Joel Levitt has trained more than 17,000 maintenance leaders from more than 3,000 organizations in 24 countries. He is the president of Springfield Resources, a management consulting firm that services a variety of clients on a wide range of maintenance issues www.maintenancetraining.com. He is also the designer of Laser-Focused Training, a flexible training program that provides specific targeted training on your schedule, online to one to 250 people in maintenance management, asset management and reliability.