There was a book written in 1978 that transformed maintenance. It was called Reliability-Centered Maintenance (now known as RCM) by F. Stanley Nowland and Howard H. Heap. Both worked for United Airlines – Nowland as the director of maintenance analysis, and Heap as manager of maintenance program planning – conducting a study and subsequent report on airline maintenance practices.
Sponsored by the Office of the Assistant Secretary of Defense, the results of the study were printed as a book in order to share insights with other disciplines, such as the U.S. military, on scheduled-maintenance programs.
This work was the result of the techniques used to design and maintain aircraft. The first jet that used RCM with was the Boeing 747 (which originally rolled off the line in 1969). The 747 was more reliable and needed less maintenance then the prior generation Boeing 707, and was quite a bit bigger and more complex.
Addressing random failures
The notable thing about this study, among others, was when they looked at failures they found that most of them were not caused by wear and tear, or age. Most failures were random. An example of a random failure might be when a vehicle is driving down the road and a rock cracks or breaks the windshield.
No amount of preventative maintenance (PM) would help to anticipate or mitigate that kind of failure. Other random events like road hazard tire failures, gunk in the diesel, (some) brake failures and (a few) transmission failures can be somewhat managed, but not eliminated, by good PM service.
Their study found that more than 75 percent of the failures were random in nature. The problem with this is that the focus of a PM program seems to manage only a small percentage of potential failures. The same holds true for commercial vehicle fleets.
They grappled with how you manage these random failures. Think about it: an aircraft flying at 36,000’ with 200 souls on board. The consequences of a failure were even more critical. So how did Nowland and Heap help to address this issue?
Defense in depth
They decided to look first at the consequences of a breakdown (broken into categories such as fatalities, environmental catastrophes, airplane downtime and cost of repairs, etc.) to see if it was worth it spending the time to reduce the chance of failure to as close to zero as possible.
The solution was known as “defense in depth.”
Defense in depth is a concept that is used in mission-critical applications to address how you manage your efforts. It starts with a failure mode.
For example, let’s say loss of engine power is the failure mode. What are all the things that could cause this loss of power? Some are typical maintenance issues such as bearing failure, a crank breaking, a clog in fuel line, broken cam shaft, etc.
However, many causes to the loss of power may not be maintenance-related at all, like a bird strike, running out of fuel, bad fuel, driver reducing the throttle, etc.
Defense in depth considers the causes and seeks to eliminate all of them. This makes the vehicle system (truck, airplane, submarine) more robust.
First, for fleets, it means looking first at the consequences of different failures.
Secondly, it means applying all the tools and resources available to the fleet to help eliminate or reduce the chance of the critical non-maintenance related occurrences from happening.
Tools can include, but are not limited to, reengineering, refining pre-trip checklists, changes to training, enrolling the driver in run-time inspection, finding new aftermarket products, adopting new procedures, ensuring procedures are followed and many more.
All of this will be aided by specific discussions with all the participants (technicians, drivers, washers, fuelers, parts room people, etc). PM alone will never get you there.
Joel Levitt has trained more than 17,000 maintenance leaders from more than 3,000 organizations in 24 countries. He is the president of Springfield Resources, a management consulting firm that services a variety of clients on a wide range of maintenance issues maintenancetraining.com. He is also the designer of Laser-Focused Training, a flexible training program that provides specific targeted training on your schedule, online to one to 250 people in maintenance management, asset management and reliability.
About the Author
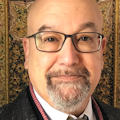
Joel Levitt
President, Springfield Resources
Joel Levitt has trained more than 17,000 maintenance leaders from more than 3,000 organizations in 24 countries. He is the president of Springfield Resources, a management consulting firm that services a variety of clients on a wide range of maintenance issues www.maintenancetraining.com. He is also the designer of Laser-Focused Training, a flexible training program that provides specific targeted training on your schedule, online to one to 250 people in maintenance management, asset management and reliability.