The importance of documenting ‘institutional memory’
If your business was given a memory test, it might fail pretty badly (at least the ones I’ve visited). When it comes to keeping track of previous processes and projects, many operations don’t build on their own histories in a format to make it easily searchable or even easy to locate.
But, is it something important to consider doing? Absolutely.
Past and present
One company I worked with told me they kept all the files from a big construction project. I found them in the warehouse just like they said. They were stored in 27 boxes (picture boxes stacked three-by-three-by-three on a pallet covered with plastic wrap). The boxes were stored with no index, no table of contents, no organizational system; just boxes stuffed with papers.
Organizations can save significant money when they know where pipes and wires are routed. It may be useful to have access to documentation on past projects and plans. Many things that were considered for the business in the past and discarded may now become good ideas in present day because of changed circumstances or new technology.
There were two examples that came to mind. One actually happened recently, and one a few years ago.
Forgotten, then found
A few years ago, I had a municipal fleet manager from a large town in Long Island, N.Y., attend one of my classes. He seemed to get a lot from the class and was intent on building a great fleet organization. He was looking for the “best” computerized maintenance management system (CMMS) for municipal fleet operations. He told the class that his organization had been looking for only a short time but had seen some great systems. At the time, that level system, for that size of client would have cost more than $100,000.
Unknown to him, I had previously been a consultant for a CMMS vendor. This particular CMMS was a high-end system used by FedEx for their truck fleet, along with municipal fleets like the City of Philadelphia. Coincidentally, this same CMMS had already previously been purchased by the town on Long Island.
When it had been purchased previously, I had been involved in the delivery. The municipal fleet had hired us to set up the equipment list and basic files, but no one from the town was tasked to work with us. This meant the CMMS vendor set up the system, but no one from the fleet was actually trained on how to use it.
I thought it was a disaster that could have been avoided. They ended up with a system that was not used; not even a single work order was ever entered. The person driving the effort moved on and the software was eventually removed.
Getting back to the class, I mentioned the name of the IT manager and asked the fleet manager if he was still there. He was. I advised the fleet manager to ask where the archives for the system were. He was shocked that he had potentially won a $100,000 lottery for his town.
More importantly, why had the purchase been forgotten?
It is extremely common for organizations to buy software or hardware and abandon it before it even has a chance to prove itself. In fact, I would visit maintenance departments and ask if they had ever bought any fancy predictive maintenance equipment. Inevitability they had, and it was stuck in some drawer someplace. A few too many thousands of dollars wasted. Not to mention, the next group of leaders might benefit from that information.
Back to school
I recently visited the elementary school my kids had attended. It is located in a beautiful valley full of trees and a creek. The classrooms were all one-room schoolhouses. There was a science room, library, art room and a music room, all separate or in pairs. When the kids were there, I was a member of the school board and head of the Buildings and Grounds committee. We had completed a massive capital campaign and reconstructed two of the school buildings. We also did a project to manage the rainwater and runoff. This all happened about 15 years ago.
The new principal said that they were starting a new capital campaign and were going to rebuild and reconfigure several buildings, rework the rainwater management and a few other things. I started talking about what I remembered from those projects and she was surprised that we went as far as we did. I told her some stories about some of the issues we had and some of the plans we had but didn’t carry out. This was all news to her.
She found some of the discarded “good” ideas we had back then (mostly because of limited funding) would be even better now.
When I left the board 15 or so years ago, all the drawings, meeting minutes and reports were at the school. In the years since, however, everyone on the leadership team changed (in some cases a few times). The knowledge was lost except what I could remember years later, during a coincidental conversation with the current leadership.
What fleets can do
These examples should resonate. How much of this is going on at companies? And how much of this information will survive once management retires? What can fleets do to ensure history isn’t repeated?
Today, scan-and-store document management systems with optical character recognition (OCR) are inexpensive, robust and can survive migration to the cloud or other digital storage options.
Having access to a systematic and organized archive of previous processes, plans and projects can provide current management a wealth of information.
Joel Levitt is the president of the Springfield Resources, a management consulting firm that services a variety of clients on a wide range of maintenance issues. Levitt has trained more than 17,000 maintenance leaders from more than 3,000 organizations in 38 countries. He is also the creator of Laser-Focused Training, a flexible training program that provides specific targeted training on your schedule, online to one to 250 people in maintenance management, asset management and reliability.
About the Author
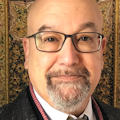
Joel Levitt
President, Springfield Resources
Joel Levitt has trained more than 17,000 maintenance leaders from more than 3,000 organizations in 24 countries. He is the president of Springfield Resources, a management consulting firm that services a variety of clients on a wide range of maintenance issues www.maintenancetraining.com. He is also the designer of Laser-Focused Training, a flexible training program that provides specific targeted training on your schedule, online to one to 250 people in maintenance management, asset management and reliability.