Some of the most critical concepts in our lives are concepts that call on us to be better people. World-class maintenance is an important concept, not for what it is, but for what it can do.
World-class maintenance asks us to answer the question, “How can we support the mission, vision, and values of our organization in the best way possible?” At its most powerful, this is a cultural conversation, not an operational conversation.
Some attributes a world-class maintenance environment may include:
- A “do no harm” approach to employees, communities, and the environment
- Active management of risk
- Operation of assets only if they continue to provide value
- Achieving a “waste nothing” operation
Assess asset management
The best companies today are dedicating themselves to the triple bottom line of profit, people, and planet. They are taking a hard look at their processes and procedures to deliver their mission with fewer inputs of material, energy, and people.
A new view of maintenance activity might look something like:
- Maintenance is a part of asset management.
- Asset management is managing assets from “lust to dust.”
- When working on or operating an asset, use precision techniques.
- Reduce all cost inputs. The fewer resources used, the better.
- Focus on the ongoing need to improve output, yield, and quality.
- All activity is accurately accounted for and detailed in work orders.
Maintenance is part of a larger conversation. This conversation starts with understanding an organization's need, then finding an asset to provide that need, and learning how to maintain and operate that asset. Maintenance ends with the asset’s disposal and managing any residual liability. Maintenance activity is something to be thought about and planned, but it is not the goal. The goal is getting the value the asset provides and limiting the risk.
One way to do this is to view challenges in new ways. Approach a problem as if you need to solve it permanently. What would it take to never have that problem again? Have a willingness to run controlled experiments within your organization and consider spending at least 1 percent of your effort improving things, not just fixing things in the short term.
Measure the impact of changes
Say goodbye to “seat of the pants” maintenance and hello to analysis-driven maintenance. Benchmarking allows fleets to use hard numbers and data to measure continuous improvement. To do this, fleets must have a willingness to use sophisticated tools of statistics, finance, and accounting in maintenance analysis, as well as be open to trying artificial intelligence (AI) and advanced analytics for maintenance analysis.
We must use all the tools we can adopt to achieve our mission. I have never met a tradesperson who wouldn’t try a new tool. In management, we must lay down our fear of new tools (especially ones we don’t completely understand), embrace our ignorance, and learn.
Focus on the people
Always focus on service, or adding value, to the customer and encourage the customer to participate in the maintenance.
There is one reason to have an asset to maintain and that is to provide some value to the organization. In general, the customer actually drives the mission, and we provide our customer with the means whereby they can drive that mission.
Beyond that, look at internal staff as well. Have the right people in the right jobs with the right competencies. When assessing this, consider:
- Teams with different points of view can see defects and solutions from different angles.
- Fade traditional barriers to information. Find new ways of reaching and communicating with these employees.
- Offer continual training and cross-training.
- Have an attachment to people rather than to technology.
- Look at every option before a layoff.That every other option is looked at before a layoff.
This is a people business. As you rise in the hierarchy of the business, you are dealing with fewer technical issues and more people problems.
The ultimate goal is to have a powerful, self-motivated workforce and excellent execution of maintenance, with well-supported customers.
Joel Levitt is the president of Springfield Resources, a management consulting firm that services a variety of clients on a wide range of maintenance issues. Levitt has trained more than 17,000 maintenance leaders from more than 3,000 organizations in 38 countries. He is also the creator of Laser-Focused Training, a flexible training program that provides specific, targeted training on your schedule, online to one to 250 people in maintenance management, asset management, and reliability.
About the Author
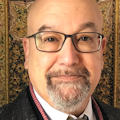
Joel Levitt
President, Springfield Resources
Joel Levitt has trained more than 17,000 maintenance leaders from more than 3,000 organizations in 24 countries. He is the president of Springfield Resources, a management consulting firm that services a variety of clients on a wide range of maintenance issues www.maintenancetraining.com. He is also the designer of Laser-Focused Training, a flexible training program that provides specific targeted training on your schedule, online to one to 250 people in maintenance management, asset management and reliability.