What does your dream shop look like? That is a question asked by Fullbay, providers of a heavy duty repair shop management platform. Whatever it looks like, the company advised, fleets and service providers need to address a number of key practices to achieve that goal.
To start, you should not only have some idea of where you want things to be in your shop, but also how long it will take technicians to reach them. You do not want them hiking back and forth all day between places like bays and the parts room, so seeing how much time that will take and organizing the facility to cut it down as much as possible will pay off in productivity.
Second, invest in equipment storage. Large tools especially can get in the way when they are not in use, but technicians need them nearby so they do not waste time looking for items or trekking across the shop to retrieve them. Keeping equipment stored close to the service bays in a space that is organized but both out of the way and accessible, is a sure time saver.
“Fleets want to minimize the distance a technician has to travel to perform routine tasks,” said Dave Shedlock, BendPak’s director of national accounts, North America. “Take wheel service, for example. By putting wheel balancers, tire changers, and inflation cages near each other and close to a bay where that work is done, technicians don’t have to move heavy wheels and tires all over the shop.”
How technicians move heavy vehicle components is another important consideration, Shedlock pointed out. Service carts, vehicle dollies, and other equipment can take the strain of lifting and moving vehicle parts off the technician, reducing risk of injury and improving efficiency, he noted. In some cases, labor-saving shop equipment can even let a single technician perform tasks that would otherwise require two people.
“Service and parts departments should be considered profit centers, and storage solutions should be looked at as a means of increasing efficiency and productivity,” said Ricky Johnson, vice president of sales at Borroughs LLC. “It’s important to work with a manufacturer to address efficiency and ergonomics. The supplier should be able to survey current and future workspace needs and use design software to provide a suggested storage layout.
“Parts inventory is the backbone of a shop’s support for technicians,” Johnson continued. “A proper layout for the parts department creates a ‘Fast Zone’ that places the fastest moving parts close to the counter. When a technician stands and waits for a part, a dealership can lose an average of a $1.50 a minute in revenue. Creating a fast zone will resolve this issue.”
Tool storage and equipment organization can help keep shops running efficiently, Johnson also noted. Features of well-designed workstations can include drawers that extend far enough so technicians can find tools in the back easily, and they should have the ability to open upper cabinets with one hand.
Shop size and layout can dictate equipment choices, noted BendPak’s Shedlock.
“Fleets with facilities that have less square footage will want to look at more compact equipment,” he said. “And don’t forget about the HVAC system’s role in technician safety and productivity. When temperatures get high, technicians can overheat, lose focus, and even become ill.
“Proper lift selection leads to greater shop efficiency and productivity as well, but the process must take into account many factors,” Shedlock also related. “Understand the types and weights of vehicles to be lifted, clearances above and around the lift, and access to vehicle lifting points. Before choosing a lift, get accurate bay measurements, including ceiling height, and check to make sure the service bay can accommodate the fully raised height of the lift when it’s loaded with the vehicles you’ll be working on.”
When it comes to two-post lifts, Shedlock pointed out, overhead cross bars can sometimes limit how high a vehicle can be raised, so make sure to account for that in your calculations. Turning radius is also a factor in lift selection. The vehicles a fleet is planning to service need to be driven into the bay without a lot of time spent maneuvering.
For ultimate flexibility, Shedlock added, consider a portable lift. For heavy duty vehicles, mobile column lifts can be stored out of the way until they are needed, and then conveniently moved from bay to bay as jobs require their use. A single set of mobile columns can be used to lift multiple vehicles throughout the day and lower them onto support stands. The lift columns can then be moved to the bay where they are needed next.
Fleets relate best practices
With more than 44,000 units of trailering capacity and over 4,000 power units in its asset-based fleet requiring routine service and repairs, Gerry Mead, executive vice president, maintenance & equipment, noted Hub Group’s five shops have to operate as efficiently as possible.
“If you look at how a well-run dealership’s shop is organized – with things like express lanes that improve throughput – you realize they do that to generate revenue,” Mead said. “The same concept applies to fleets. Moving equipment efficiently through shops reduces costs and downtime so assets can cover more revenue-producing miles.
“The simplest approach to an efficient shop layout is to make sure everything is placed so technicians aren’t wasting time,” Mead continued. “COVID has forced everyone to focus more closely on non-essential movement, but a layout that limits the need for our 60 technicians to walk across shops eliminates wasted time under any circumstances. Simple things like making sure that PM tools are by the PM bay, or tire tools are readily available, turn unnecessary travel time into asset uptime.”
To further limit the need for technicians to leave their work bays, Mead is focused on the time that is associated with getting parts. As a result, Hub Group shops are organized by job type. For example, bays used for preventive maintenance (PM) and faster repairs are closer to the parts room. In addition, the shops use carts to deliver parts to bays rather than requiring technicians to pick them up.
“The carts help with social distancing because technicians are not crossing back and forth across facilities, but just as importantly the time that saves adds up,” Mead stated. “We’re seeing that improvement in efficiency in direct labor costs and quicker turn times for repairs. It was an opportunity that was always there but until recently we didn’t look at it closely.
“Another thing we’re doing to improve shop efficiency is organizing parts rooms by VMRS code,” Mead added. “It saves a lot of time when things are sorted correctly. Otherwise, you will lose time you can never recover.”
“Incorporating best practices for shop efficiency starts by looking outside your office door to see the workload for each day,” said Jeff Harris, vice president, maintenance at USA Truck. “We’ve established staging areas for tractors and trailers that immediately identify where they are in the service process. That better way to organize vehicles eliminates wasted time and energy searching for or moving units to be able to bring one into the shop. And a quick three second look makes it easier to tell our dispatch and operations staff which vehicles are ready for service.”
Tool storage and equipment organization has also been addressed in USA Truck shops to eliminate wasted footsteps and time.
“We use rolling shadow boards with common and associated tools, which are staged at specific locations,” Harris explained. “A board, for example, can have tire and wheel-end tools or other high usage items. The boards are stored in painted blocks on the shop floor and are rolled to a bay as needed. That way they still have a home, but the tools are closer to the technician because they’re not all in one central location.”
Other organization practices at USA Truck shops, according to Harris, include painting boxes on shop floors for garbage cans and establishing locations for items like refrigerant recovery units.
“We’ve focused on parts storage as well, especially high usage items” he added. “For example, we keep a supply of mud flaps for quick replacement at our Maintenance Quick repair lanes, and we installed shelves for filters in our PM pits.”
Quantifying time savings has also yielded efficiency benefits at USA Truck shops. To evaluate the time spent on a routine PM, for example, the fleet outfitted a technician with a pedometer to count footsteps and created a diagram of the technician’s path around the truck. By analyzing the information, a change in procedure to reduce steps resulted in cutting a four-hour PM down to one hour and 45 minutes.
That kind of time savings can add up quickly for a fleet that has 115 technicians at seven shops, including four new facilities that were opened in the past three and half years. The maintenance staff at USA Truck services over 1,600 company tractors, 450 owner-operator vehicles, and 5,500 trailers.
“We see the benefit of all this activity in SRT efficiency on the thousands of routine jobs we perform every year,” Harris stated. “By measuring efficiency, we know why things take certain amounts of time and whether we can improve on it with better organization.”
Technology contributes to shop efficiency
For productivity, related Jason Hedman, product manager at Noregon, it is important for shops to equip their technicians with tools that facilitate quick and accurate diagnosis and repairs.
“When a truck is held up in a bay because no one can figure out what’s wrong, fleets experience unnecessary downtime and service centers decrease their profit margins,” he said.
“The tools must both assist entry-level technicians with diagnostics, so they don’t have to pull away more experienced team members from their work, and at the same time offer advanced capabilities that experienced technicians need to complete more intensive jobs,” Hedman continued. “By equipping locations with tools that assist technicians of all skill levels, fleet shops will experience fewer comebacks and better bay-turn rates.”
Hedman also noted that benchmarking is essential for measuring improvements from upgrading shop tools.
“Keep records of average repair times, dwell time, average repair order values, or whatever other metrics you wish to improve,” he advised. “Fleets should also consider maintenance intervals, breakdown rates, or other measurable items that affect uptime. Then, once you implement a new tool and use it for a sufficient amount of time, return to these figures and take note of how they have changed.”
Management technology can streamline processes and make shops more efficient, noted Fullbay CEO Jacob Findlay.
“We’ve seen the results across different operations,” he stated. “Locations with shop management platforms that can transfer information in real time by using tablets or laptops at each bay so technicians and service managers can be in constant communication are steadily improving their efficiency. By taking paper out of the equation, for everything from repair orders to parts ordering, work can progress faster.
“We recently spoke to a truck dealer who had done the research and found out that every time a technician leaves a bay for whatever reason, they could write off 30 minutes that time was not spent turning wrenches,” Findlay continued. “Our data benchmarks have also shown that management solutions can improve shop efficiency by an average of 10 percent to 15 percent.”
With the right shop layout, tools, technologies, and practices, fleets can have a major and positive impact on technician and facility efficiency and productivity across their operations.
About the Author
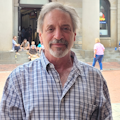
Seth Skydel
Seth Skydel, a veteran industry editor, has more than 36 years of experience in fleet management, trucking, and transportation and logistics publications. Today, in editorial and marketing roles, he writes about fleet, service, and transportation management, vehicle and information technology, and industry trends and issues.