Outsourcing, maintenance software power efficiency at New England utility fleet
The word “sprawling” doesn’t even begin to describe the fleet and maintenance operation at Eversource, a diverse utility company that provides electric, gas, and water services to customers in Connecticut, Massachusetts, and New Hampshire.
For starters, the energy company’s fleet reflects the specialized requirements of all the departments within the organization. There are 6,802 pieces of equipment in total, including 5,765 motorized vehicles ranging from cars, pickup trucks, and vans to bucket trucks and tractor trailers. There are also 1,037 trailers and everything from small tools to large backhoes and excavators.
Across the three states it serves, the Eversource fleet is based at work centers where it is serviced by approximately 165 technicians at 29 maintenance facilities. The shops vary in size depending on the work centers supported, noted Michael Rorison, director of fleet operations.
“Our larger shops have 20 bays, while smaller locations may have only two or three bays,” Rorison explained further, “but all of the shops, regardless of size, have the capability to address any repairs required to support our fleet. Our team completes body work, including painting, welding, light machine work fabrication, tire balancing, state and federal inspections, engine overhauls, and in frames. They are also capable of conducting warranty repairs on select equipment.”
In some areas, maintenance and repair work are outsourced as well. For example, ARI services vehicles like pickup trucks and cars. Additionally, through a mounted tire program for tires 19.5” and above, carefully chosen vendors who go through a rigorous bid process handle tire replacement.
Taking a data driven approach
Everything that takes place within the Eversource fleet maintenance operation is managed and tracked using Chevin FleetWave software. That includes all assets, repairs, parts inventory, and usage.
“We have preferred vendors and that program is monitored using a monthly KPI setup in the Power BI business analytics service from Microsoft,” Rorison added. “All of our shops work to meet a monthly goal of purchasing 85% of all parts from a preferred vendor, and they usually achieve above 90% compliance.”
Eversource also uses Power BI to create KPIs to measure the performance of its maintenance program. Some of the key performance indicators it uses are PM Compliance and Door Traffic. A similar methodology is applied to shop staffing levels, which are based on MRUs (maintenance repair units).
“We use formulas supplied by Price Waterhouse Cooper,” Rorison explained. “Additionally, job standard times are evaluated using warranty tracking and reimbursement through OEM and third-party vendors. We also benchmark against similar repair organizations across the country, including the use of Utilimarc data.”
Training plays a role as well
Ongoing education is provided for all of the Eversource fleet maintenance operation’s 165 technicians. Newly hired technicians learn how to use the fleet management system during the onboarding process, how the shops work, and standards for repairs. Then they complete vehicle-specific training with manufacturers and other vendors. Eversource also works with Universal Technical Institute (UTI) for employee training and conducts frequent on-site training throughout the year.
“Training is important to remain current, and it results in a safe and effective workforce,” Rorison stated. “We are also proud that our entire approach is supported by a strong relationship and partnership with unions, which greatly enhances the professionalism of our organization and the quality of repairs that are completed.”
Everything that takes place throughout the Eversource fleet maintenance operation is based on standardized processes and procedures. A comprehensive Fleet Guide defines those standards and the Eversource Shop Playbook supports and guides supervisors in how they approach day-to-day operations at each of the shops.
“We use the 5S systematic workplace organization method—Set in Order, Shine, Standardize, Sort, and Sustain—to keep our shops in order and to ensure efficiency,” Rorison said. “Through the use of data analytics, standardization of work practices, preferred vendors, 5S, and training, we maintain a fleet that is reliable, safe, and ready to support our customers.”
About the Author
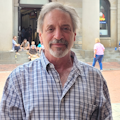
Seth Skydel
Seth Skydel, a veteran industry editor, has more than 36 years of experience in fleet management, trucking, and transportation and logistics publications. Today, in editorial and marketing roles, he writes about fleet, service, and transportation management, vehicle and information technology, and industry trends and issues.