The benefits of paperless processes in your maintenance department
Construction firms have lots of equipment to track and manage. Typical firms have everything from excavators and backhoes to pavers and dump trucks. This equipment is expensive and needs to be maintained. On top of these giant machines, many jobsites require a plethora of small equipment and power tools. This equipment also needs to be tracked as the tools can easily get lost or walked off the site.
Many contractors still use paper-based systems to track tools and jobsite machines manually. They write down the piece of equipment in an equipment log, enter the person's name and location, and the time the equipment is checked out. When workers finish with the equipment, they check it back into management. But papers can get lost. Logbooks get misplaced. Plus, if you enter information into a paper log, your admin person must re-enter the information into a computer system for billing purposes. Reentry of data often leads to mistakes and errors.
Most importantly, equipment needs to be maintained. When a piece of equipment goes down, it takes time to figure out what is wrong and then time to repair it. Digitizing your maintenance operations increases equipment reliability, streamlines maintenance operations workflows, increases labor productivity, and keeps costs contained. Using a digital maintenance management system optimizes workforce efficiency with digitized workflows.
Optimize workforce efficiency with digitized workflows
For decades, machine maintenance throughout the industry was primarily reactive. When a piece of equipment broke down, a shop manager would locate or order parts and assign a mechanic to repair it, and the mechanic would keep track of the hours spent on the fix using a paper ticket. Then paperwork orders and tickets made their way back to the office for manual entry, allowing payroll to cut checks and managers to assign repair costs against equipment.
With manual methods, unless the mechanic had personal experience with the equipment, there was no way to know its history, if other items on the machine were up for repair, or if the fix was a warranty issue. But now, each piece of equipment's entire work and repair history is stored within the maintenance management system, giving the technician a complete picture of the equipment being maintained.
When equipment specs, warranty information, and insurance data are input into a fleet maintenance system, mechanics in the shop and the field enjoy greater efficiency because they have the information they need at their fingertips. Work orders are created, and alerts are set for preventive maintenance and services. As a mechanic prepares to work on a piece of equipment, they have immediate access to part numbers, diagrams, and technical specifications. They can look up warranty information to see if a piece of equipment is under warranty, saving costs.
Mechanics enter repair data into the system rather than submitting paperwork, which can get lost or must be deciphered by someone else later. Mechanics see all work orders before they head out to a jobsite, so they know what needs to be done and can have the tools and parts they need for the repairs. Jobs are prioritized and assigned to available workers. The system ensures that workers have the right parts for the work they need to do. If inventory for a particular part is low, the system can reorder and replenish parts, ensuring work can continue as needed.
Mechanics enter timesheets via an iPad. Times are combined with personnel data to pay workers for their work. If mechanics are in the field, the system empowers workers to document their hours across various jobs. Crew members clock in and out and submit information about what they worked on. Inputting data from the field with a simple, digital interface saves supervisors about 30 minutes daily. Over a year, that's $5,000 per foreman when assuming a fully burdened foreman hourly rate of $45.
Preventive maintenance avoids breakdowns in the field
Maintenance management systems can configure preventive maintenance alerts to track when a piece of equipment needs to undergo routine maintenance. When a piece of equipment is coming in for an oil change, management can schedule time in advance to handle any other issues identified through reports from the field.
Preventive maintenance can be hard to track and lead to poor equipment utilization. Maintenance management systems easily keep track of maintenance schedules, so equipment is appropriately maintained. Properly maintained equipment reduces downtime. If a piece of equipment goes into the shop for repair, mechanics follow work orders directing them what to do. Plus, if a piece of equipment has a scheduled maintenance plan, management can order rental equipment to replace it so that crews can continue working.
Preventive maintenance schedules can have alerts set by calendar days, runtime hours, and equipment odometers. Cost codes can be charged, and damages assigned to specific jobs, so you know whether a piece of equipment lost you money on the jobsite.
Integrate maintenance operations with other software for greater value
Integrate equipment maintenance software with other solutions within your construction operations to maximize value and further improve your business. Integrating your maintenance software with field operations streamlines the maintenance request process from start to finish. The crew can spot issues with equipment while out in the field and create maintenance requests, which can turn into work orders in the maintenance system.
Telematics devices on equipment send real-time meter readings and detailed equipment location history to the maintenance system to help the shop keep track of asset usage. Mechanics can see live locations where their services are needed when telematics devices are used on equipment.
Integrate your maintenance software with your safety management system to speed communications from the field to the shop. Have workers enter notes, take pictures, and perform equipment inspections, sending any alerts to shop managers using the maintenance software. These shop managers can add alerts to the work orders, backlog the work, or dismiss the alert so that nothing slips through the cracks and prevents equipment downtime.
Utilize equipment hours from project management timecards can be sent to the maintenance solution to compare runtime hours versus charged hours better. Expenses can be directly integrated into accounting software to streamline payroll. Managers can view asset reports to see a snapshot at the fleet level for how much everything costs you by the mile or how much you spend on specific work.
Improve future bidding accuracy by sending actual fuel consumption rates to your bidding software so estimators don’t have to guess when budgeting for equipment. Better estimates mean more money for your business. Integration with other solutions provides excellent value for your maintenance operations.
Hayden Price is technical product manager at Heavy Construction Systems Specialists LLC (HCSS). HCSS Equipment360 is a heavy equipment maintenance solution for heavy civil construction companies. It helps companies stay on top of preventive maintenance and offers real-time issue reporting and work order management.
About the Author
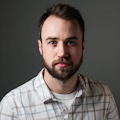
Hayden Price
Technical Product Manager | HCSS
Hayden Price is technical product manager at Heavy Construction Systems Specialists LLC (HCSS). HCSS Equipment360 is a heavy equipment maintenance solution for heavy civil construction companies. It helps companies stay on top of preventive maintenance and offers real-time issue reporting and work order management.