How to rightsize your fleet maintenance management system
Jamie Hagen is the proud owner of a small fleet called Hell Bent Xpress. Not only does he run the South Dakota-based fleet, but he’s also dispatcher, light maintenance technician, fleet manager, and, sometimes, even driver. He’s a quite capable social media manager, too, and often shares his trials and tribulations, along with fuel efficiency wins, on Twitter and LinkedIn. He’s known to post updates whenever he purchases a new truck, and these posts have been more frequent the last few years. He’s a Mack guy through and through and his fleet just hit a dozen in January with their latest purchase of a 2023 Anthem with the Super Econodyne package and Bahama Blue Metallic paint job.
“Certainly it’s not much, but for a guy who is nobody special and grew up with welfare on a small farm, it feels like a milestone every time we are able to add and grow,” he posted on LinkedIn after obtaining that newest Mack Anthem.
Since 2021, Hell Bent Xpress has tripled its fleet size. It’s still obviously a very small fleet, but with all the roles Hagen fills for his company, his workload likely surpasses most fleet managers in the business.
To ease that workload, Hell Bent Xpress hit another big milestone in the fall of last year: purchasing a fleet maintenance platform. Hellbent went with Samsara’s platform because they also handle the fleet’s electronic logging devices (ELDs) and cameras.
“They sold me on the whole platform because we could not only have our ELD, but we could also have cameras, dispatching, and maintenance tracking,” Hagen recalled. “It sounded better than me writing everything down.”
Hagen noted in the earliest days of his freight shipping business that “everything was on a notebook, and then we switched to a little form, and then in a file. And then it seemed way easier and quicker to look up [fleet data].”
Read more: How to unlock more uptime with eDVIRs and CMMSFor Hagen, organizational necessity was the tipping point for investing in a fleet management system, especially with his burgeoning fleet growing to a dozen trucks.
“It saves time, but the biggest thing was just getting lost in the sauce,” Hagen clarified. “It’s starting to become apparent that I need more organization, [and] if I’m not going to hire somebody to do these roles, which when you’re this small you really can’t afford to do, it’s cheaper to digitize than to bring another human being onboard.”
But finding the right fleet maintenance management system can be an investment in and of itself, and one that a busy fleet or shop might hesitate to allocate time to. However, the investment is often well worth it, as the benefits can drastically improve uptime, reduce costs, and overall give managers more peace of mind. And the best part is, there’s an option for every fleet out there, big or small. The only question is which is the right size for your fleet?
Visibility and transparency
One of the main benefits of a maintenance management systems is the ability to have a constant, real-time data feed monitoring a fleet’s performance. But while smaller fleets question the need to monitor a low number of assets, having an immediate view of every vehicle’s health and status can provide immediate investment returns.
“We find that people who run a number of assets, there’s lots of overhead—lots of costs associated with running those assets. And sometimes they don’t need all of them,” said Will Wycks, chief marketing and product officer, Chevin Fleet Solutions, which offers the FleetWave platform.
The platform includes a code-free report builder called KPI Wizard that allows users to quickly add or remove items from a list of best practice fleet industry key performance indicators.
“FleetWave analyzes lots of data to provide clear insight in order to say ‘What is the right size of the fleet that you need to run?’” Wycks noted.
The data analytics aspect is something every fleet can take advantage of, as every vehicle and shop is generating data all the time.
“I would encourage anybody trying to understand their fleet costs or compliance to consider fleet management systems, because if you can’t measure it, then you can’t manage it,” Wycks said.
For specific example, one of the maintenance platform Fleetio’s customers was a small landscaping company called ProQual Landscaping. As their business grew, they realized that they needed more insight in managing their maintenance operations.
“As they expanded, they were spending too much time on repairs and experiencing high vehicle downtime,” said Daniel Simpson, product marketing manager at Fleetio. “When ProQual became a Fleetio customer, they immediately adopted our custom digital inspection forms. This gave them insight into the state of their fleet and allowed them to set up unique maintenance schedules for each type of asset they had.”
After adopting the fleet maintenance system that helped them “create proactive maintenance plans,” the Tempe, Arizona-based fleet cut costs by 33% in the first half of the year versus the previous timespan without one, according to Jeremy Bader, ProQual Landscaping’s Implementation Manager. This is because the platform combines OEMs’ maintenance recommendations with fleet inspection data.
“It takes the guessing game out of maintenance,” Bader said. “Everyone knows when a vehicle will be out for service and everyone knows when it’s supposed to be back.”
But managing fleet costs isn’t just limited to maintenance schedules. It can also help smaller fleets decide when it’s time to grow their business or how they can stretch the vehicles they already have.
Meanwhile, this transparency into fleet efficiency is even more important for fleets with several hundred trucks at their disposal. Like the differing KPIs any one fleet might choose to monitor, management solutions also vary in their applicability for each business.
There’s no one-size-fits-all solution, noted Matt Wiedmeyer, CTP, director of fleet services at Fleet Advantage, which provides fleet lifecycle management solutions. What’s good for a grocery chain’s fleet might not work as well for a heavy hauler.
“An entirely different system may be better because their units work on an entirely different dispatch system and aren’t home every night,” Wiedmeyer said.
So, how does Fleet Advantage help its customers?
“We’ll sit down and we’ll talk with them,” Wiedmeyer continued. “We will look at what their highest costs are, whether it’s tires, brakes, or the aftertreatment system, the things that can sometimes kill a fleet.”
Identifying these pain points are particularly critical for large fleets, when each minute issue a smaller fleet might be able to postpone is multiplied across hundreds of vehicles, leading to marked financial losses.
This is especially true in the years following the COVID-19 pandemic, which have been rife with vacillating costs, inflation, and supply chain difficulties that hindered expenditure management for fleets.
“In [these] times, it’s important that you ground yourself,” said Brian Antonellis, SVP of Fleet Operations at Fleet Advantage. “If a customer came to us and said, ‘Hey, [my fleet] feels kind of erratic; I’m having trouble getting trucks,’ we would say, ‘Okay, let’s start from the beginning. Let’s understand your data.’”
This prompts Fleet Advantage to drill down into the fleet’s components, financial costs, and miles per gallon to create a plan that leads the customer to their intended stability.
“And it’s not just about a one-year strategy, but it’s about a three- or five-year strategy around making sure we set them up on a lifecycle [where] we’re going to understand what the cost is,” Antonellis explained. “We’re going to understand how it’s going to change over time and then help them get back to a place where they feel comfortable.”
Compliance and inspections
Nowhere is this transparency and visibility more critical than in vehicle inspections, a topic that all fleets large and small must address. Whether it’s via Fleetio’s GPS tracking a driver’s path around a vehicle during an inspection or Zonar’s Electronic Verified Inspection Reporting (EVIR) solution, which requires operators to scan specific tags in each inspection zone before they can move on, federal compliance is a key asset of many fleet management systems.
“The primary constraint that we all need to comply to is [Department of Transportation] compliance,” said Dave Walters, senior solutions engineer, Trimble. “So, we always start there. We have to have a PM system that supports DOT compliance. Are we inspecting the vehicles at the proper time? Are we maintaining compliance when we go to California? Do we have a current California BIT inspection on file?”
These granular questions are particularly impactful for smaller fleets, where the consequences of a violation are less easily absorbed than by a larger organization. But even so, a bigger transportation company may be more vulnerable to insufficient pre- and post-trip inspections, or pencil-whipping, simply for their size making accountability and enforcement more difficult.
“If you look at safety overall, the violations that are found at roadside inspections are typically tires, mirrors, and brakes,” said Fred Fakkema, VP of Safety and Compliance, Zonar, and former commander of the Commercial Vehicle Division of the Washington State Patrol. “Those are all critical components of your pre-trip [inspection]. So, we set it so it’s done right, and done right the first time to ensure vehicle checks are up to code.”
Killpack Trucking experienced this inspection verification firsthand as well as the resulting maintenance and communication benefits.
“Before switching to Zonar, they were doing inspections on the honor system, kind of like what some fleets still do on paper,” Fakkema recalled. “Drivers come in after completing the trip, they leave a piece of paper on the dashboard to indicate what needs to be fixed. Well, when you think about that, and the maintenance person reading the writing, you realize this may not be the clearest way to share information about necessary safety and compliance updates for the vehicle.”
Communication and efficiency
Communication issues such as these between drivers, technicians in the shop, and back-office management are another frequently mentioned benefit of fleet management systems for organizations large and small.
“I don’t have to wait for a check engine light come on, [for] a driver to see it [and] evaluate whether or not he wants to call me,” Hagen said. “[Samsara] automatically sends me a notification, whether they like it or not; it’s completely autonomous.”
Additionally, fleet management systems provide their users with constant access to their fleets, regardless of where they are or what they’re doing–at least, as long as they have a solid internet connection.
“I don’t have to be at my desk to access information; I can just hit the app,” Hagen continued. “I can find my loads, I can dispatch, I can look at my maintenance, I can look at the live feed of the video going down the road.”
But this efficiency extends beyond real-time asset information. For maintenance shops, management platforms can organize technical information as well.
“Over the years and even to this day, we see a lot of platforms out there that have a telephone book of information, or it used to be the CD ROM [in the shop],” said Chris O’Brien, chief operating officer, Fullbay. “It was overwhelming; there were three-ring binders that were bigger than the accounting department… We have all of that baked into our software.”
Meanwhile, larger fleets need streamlined communication more than ever.
“For fleets with 500 to 600 trucks and multiple depots in multiple locations, that digitized communication makes life a lot easier given the volume of repair that’s taking place in a big fleet,” said Mark Wasilko, Decisiv VP of marketing. “It certainly improves that fleet manager’s ability to oversee and better control the process.”
Sometimes this digital communication translates directly into time savings, as it did for a large linen service delivery operation using Shell Fleet Solutions’ Fleet Maintenance Hub.
“Their pain point was the amount of time one of their divisions was spending on consolidating invoices when it came to maintenance,” said Jim Perkins, director of fleet solutions, Shell. “So, we introduced the product to them, [and] they wanted to trial it at this one particular distribution center. If they could just save 10% of the time they were spending on maintenance administration, they were sold.”
According to Perkins, the company signed up for the solutions platform within two weeks thanks to their administrative efficiency.
When a fleet maintenance system is right for you
Having considered the various benefits of maintenance management systems for various sizes of fleets, then comes decision time. Ultimately, fleet management must calculate the cost/benefit analysis and whether the price of a platform outweighs the savings they gain from it or not.
“If you think about the small fleet, somebody that only has a handful of vehicles, costs and savings are almost critical to their survival at the time,” Perkins reasoned. “When you put it on the other side when you have 1,000 vehicles, now you’re talking huge scale. And small changes can make huge improvements to your bottom line and to your time-saving.”
Additionally, there is the argument to be made that beyond cost savings, the maintenance visibility offered by various platforms is more critical than ever, especially as fleets need to stretch the viability of their vehicles due to the delay in getting new parts and components.
“[For] a fleet that doesn’t even have its own shop to do PM work or is relying on local ISPs to do the PM work, that portal access to the network, so they can track the work being done, is every bit as important to a small fleet as it is to a midsize fleet or a large fleet,” Wasilko agreed.
O’Brien distilled down fleet considerations for a management platform even further.
“Should I have a fleet management platform?” O’Brien asked. “I go back to some questions to ask [fleets], starting with ‘Do you repair your own equipment?’ And that would be the first indication of should you have management: Absolutely.”
O’Brien argued that when a fleet provides its own repairs, it takes on a measure of legal responsibility for any accidents or repairs due to accidents for the vehicle, making maintenance management not just a question of convenience, but one of public safety.
In the end, whether or not a fleet procures a fleet maintenance management platform and which one they select is entirely driven by the fleet manager and the KPIs they want to achieve for their business. The decision will be different for each fleet, with the common goal of greater ease for managers, technicians, and drivers alike.
“[A maintenance management system] simplifies the day-to-day responsibilities for fleet owners by automating maintenance workflows,” Simpson said. “It allows them to reduce fleet costs and focus on running their primary business.”
And ultimately, being able to focus on what they do best–getting necessary goods, parts, and supplies from one end of the country to the other–without worrying about downtime for maintenance is all that any fleet needs for smooth operation.
“On the maintenance side, it’s a no-brainer when they put the whole package together,” Hagen concluded.
The only question that then remains is what fleet managers and owners will do with their newfound time and peace of mind.
“Before, things would slip through the cracks,” Hagen explained. “Now, it’s freed me up to add more equipment.”
About the Author
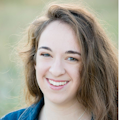
Alex Keenan
Alex Keenan is an Associate Editor for Fleet Maintenance magazine. She has written on a variety of topics for the past several years and recently joined the transportation industry, reviewing content covering technician challenges and breaking industry news. She holds a bachelor's degree in English from Colorado State University in Fort Collins, Colorado.