Even the most basic preventative maintenance tasks, when repeated over the course of 20 years, take a toll on the body and can result in a back or shoulder strain while performing an otherwise-innocuous task. But while the task may appear innocuous, the cost is not.
“If I strain a muscle in my shoulder or my arm, that’s at least six weeks of therapy, twice a week,” said Michael Renforth, VP of safety, health, and environmental for Dickinson Fleet Services. “And then that’s obviously light duty. So that means you can only lift five or 10 lbs., you can only push or pull up to five or 10 lbs., and usually there’s no climbing. Basically, this person is sorting paperclips.”
And if the injured technician in question runs a mobile truck, then the loss of manpower is even worse, as the idle truck becomes a sunk cost until another technician gets into the driver’s seat. But the impact of an injured tech does not simply begin and end with him or her, the hidden costs multiply throughout the shop.
Read more: Lifts raise bar for ergonomics in the shopAnd because technicians are a shops’ most valuable asset, management needs to consider not just what tools and technology can help workers perform more efficiently, but more ergonomically as well. One small strain can cascade into a litany of problem for a fleet, so preventing musculoskeletal disorders (MSDs) should be at the top of any shop’s list of priorities.
According to Kristi Hames, senior solutions strategist for VelocityEHS, an environmental, health, and safety software provider, here’s what happens when a worker suffers one of these injuries:
“You’re dealing with someone who’s out of work, so you’re short staffed, you’re dealing with the cost of an injury and having to pay for that,” Hames said. “You might have to pay overtime for someone to cover that job, and you might have to pay extra to have a temp come in and do that job.”
But even when someone is able to cover the missing technician’s work, they’ll still need to learn the rhythm of the job, which will decrease a shop’s efficiency.
If technician MSD injuries were a rare occurrence, these setbacks might not be so detrimental. But they are more common than you might think. The U.S. Bureau of Labor Statistics reported 272,780 incidents of worker injuries due to MSDs in 2018. On a granular level, 28% of injuries among general maintenance and repair workers involved an MSD in the same year, with the highest concentration of these injuries found in those aged 45-54. That’s right around the median age for diesel technicians in the U.S., according to Zippia.
So, what injuries must managers strive to prevent among their standing, crouching, and supine (lying face upward) technicians, and what tools can help them do so?
Standing sprains
According to the Centers for Disease Control and Prevention, precision production, craft, and repair workers accounted for 17% of back injury cases.
“The way these injuries happen is when you get into the peaks of exhaustion or strain, like if you’re picking up things repetitively,” explained Marvyn Rieger, key account manager for mobility accounts at Ottobock, a developer of industrial exoskeletons that reduce fatigue for workers by providing extra support for backs and shoulders. “You’re most likely going to get that pain in your back after you’ve picked up a heavy crate.”
Exoskeletons have been used in the automotive manufacturing space for several years to ease the repetitive motions of lifting power tools overhead to assemble chassis. As the technology matures and costs come down, they should also find a use in the shop, particularly where older workers find themselves performing several hours a day of overhead work.
But they aren’t the only solution to improve ergonomics. Even the most ubiquitous shop equipment, lifts, help prevent injuries during extended periods of standing.
According to Jason Matthews, product manager for automotive lifts with Vehicle Service Group, two-post lifts such as Rotary’s SPO16/20 Series symmetric lifts can be used to enhance technician comfort.
“Having the ability to raise the vehicle up to a comfortable height where you can walk underneath it, or you can lower it down so that you can grab the tires or the wheel assembly to remove those at a more natural position, is going to make it easier to do the work with less straining, and make you less prone to injury,” Matthews explained.
These lifts can also be outfitted with other accessories to avoid lifting and bending with heavy tires, such as Rotary’s Wheel Wing tire hanger, the B2000P Wheel Balancer from John Bean, or the ATD-7478 lifting table from ATD Tools Inc.
“Today, there’s a lot of 4x4 trucks, and all these guys like to put the big tires on them, so in some of our stores, we do have some extra lifting devices for that,” said Benjie Greene, commercial director, Black’s Tire and Auto Service. “When we’re balancing tires, especially on the truck side, we’ve got the lifts installed on the balancers. If we’re having to make a tire repair and we’ve got a spreader, we’ve got the air-assisted lift where our guys are not having to lift that heavy tire up on that spreader to facilitate the repair.”
Back pain
Technicians spend just as much time kneeling by vehicles as they do standing beneath them. This can invite back strain as well as injuries from repetitive repair movements, such as shoulder tendinitis and shoulder pain, as the National Institute for Occupational safety and Health (NIOSH) reported in a 1995 study.
The risks of this repetitive overhead work, especially with a tool in hand, remain as true today as in the ‘90s.
“For the shoulder, the most common injury we hear about in the advanced stages is rotator cuff tears,” explained Ottobock’s Rieger. “And then in the back, it’s anything with the spinal discs, really L5 or S1 type of strains—slipped discs, etc., that come from that repetitive strain.”
The L5 and S1 spinal sections refer to the lumbar vertebrae and sacrum, or lower back, which handles much of the strain involved in crouching and bending at the waist. This is where Ottobock’s exoskeletons come in.
Ottobock’s mechanical exoskeletons for the back or shoulder use spring-assisted mechanisms to help bear the weight of a tech’s torso or arm when they change their posture from bending or crouching and return to their normal position, taking the load of the body from one section and transferring it to another.
“We have folks that kneel and have to work in front of them on the floor, and they still have that support for their back,” noted Rieger, speaking of an aircraft maintenance use case. “The exoskeletons are more like a tool. They’re often kept in a tool crib where folks go and rent out different tools, because their work instructions may say ‘Consider using exoskeleton type: Ottobock Shoulder.’”
Ratcheting tools, when space allows, can also provide technicians some relief by avoiding awkward grips and positions, as well as utilizing anti-vibration gloves to lessen the impacts of using power tools.
“We try to use mechanized drivers, handles that can be held with a power grip that neutralizes your wrist posture,” said Dickinson’s Renforth. “We avoid pinch grips for forceful activities. We talk about the types of handles on tools; we don’t want them longer than four inches. If you get a longer handle, it can create an awkward type of position or more opportunity to strain an arm or an elbow when using it.”
Supine strains
Even lying down does not provide technicians much security from musculoskeletal injuries, especially when a technician is on their back for extended periods or levering themselves up and down multiple times a day.
As a result, shops need to be creative and make sure that their techs have the latest technology available to them.
“There are new devices coming on the market that we’re always looking at,” said Amy Lawson, assistant VP of EHS and security, Amerit Fleet Solutions. “There’s very interesting things out there that help employees lower their bodies under vehicles and then raise them back up.”
An example of these kinds of technology is Personal Positioning Technologies’ Human Hoist Power Shop Chair, an electric and mechanical chair that can be manipulated into an adjustable stool or a creeper with the technician in it, fully removing the supportive onus from the technician’s body. However, improving conditions in the shop does not always require the most expensive tech that money can buy.
“It may be as simple as using a pallet jack to move things rather than trying to shift it around with your own bodyweight,” Lawson mentioned. “Something that simple can make a huge difference.”
One example is an ergonomically designed creeper. These can cost about a hundred bucks and contour a worker’s body to ensure that work under the truck isn’t backbreaking.
“Where we work, we can we place ourselves in a lot of awkward positions, at times inside the cab or underneath vehicles,” Dickinson Fleet Services’ Renforth commented. As a result, technicians find themselves rolling underneath tractors and trailers on creepers in both indoor and outdoor environments, he continued.
But while a typical creeper might merely make wriggling beneath a vehicle easier, an ergonomically designed one, such as Lisle Corporation’s black plastic creeper, No. 97102, can provide better support.
“What that means is that we shaped the body a little bit to fit a person’s body better than the old, flat piece of wood that was always used,” noted Jon Bielfeldt, VP of sales and marketing, Lisle Corporation.
About the Author
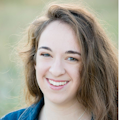
Alex Keenan
Alex Keenan is an Associate Editor for Fleet Maintenance magazine. She has written on a variety of topics for the past several years and recently joined the transportation industry, reviewing content covering technician challenges and breaking industry news. She holds a bachelor's degree in English from Colorado State University in Fort Collins, Colorado.