A total of 472 bus and truck technicians and diesel engine specialists died on the job between 2003 and 2020, according to the U.S. Bureau of Labor Statistics. Averaging 26 deaths per year, these workers died at the same annual average as ironworkers and precast concrete laborers, which are well-known highly hazardous occupations. Struck-by incidents, including vehicle rollaways, were the most common cause of technicians’ deaths.
The following details two such tragic events, where semi-truck technicians lost their lives. The investigation was done by the Washington State Fatality Assessment and Control Evaluation (WA FACE) program that is part of the Safety & Health Assessment & Research for Prevention (SHARP) program at the Washington State Department of Labor & Industries. Their deaths stress the need for using parking brakes and wheel chocks to make fleet maintenance operations safe.
#1: Technician crushed under chassis
In the first incident, a 47-year-old technician died when a rollaway semi-truck hit and caused a container chassis he was welding to crush him against a large steel bumper jack. The technician had worked for his employer for two months. The employer was a mobile commercial trailer repair contractor that operated at customer sites.
The technician was working in an outdoor repair area of a customer’s trailer leasing yard. He was welding a cross member at the rear end of a container chassis that was on jack stands. Behind him were a large steel bumper jack and a loading dock. A truck driver drove into the yard and parked his semi-truck directly behind another truck in front of the chassis the mechanic was welding. The driver then walked to the business office, where the driver of the first truck was talking with the manager.
The first driver soon left to drop off his trailer elsewhere in the yard. This opened up around 300 feet of space between the second truck and the chassis under repair. While the manager and second driver were in the office, the driver’s unattended truck rolled away and hit the chassis. The impact caused the chassis to fall off the jack stands and crush the technician behind it against the bumper jack. The technician died soon after first responders arrived.
Safety investigators found that the second truck rolled away because it was left unattended on a downgrade with its engine running, automatic transmission in neutral, and parking brake not set. The first truck may have briefly obstructed the second one from moving, but when it left, the second truck rolled forward at 5 mph toward the impacted chassis. The office manager told investigators drivers routinely dropped off trailers without stopping their engines and sometimes did not set their parking brakes.
#2: Technician crushed between wheels
In the second incident, a 62-year-old semi-truck mechanic was fatally crushed between the wheels of a rollaway container chassis. The day before the incident, he began repairs on the chassis, which was parked outside of the employer’s maintenance shop. He disconnected the air lines to its airbrake chambers, which engaged the parking brake. The truck was left outdoors for the night. The next day, he coupled a yard tractor to the chassis and tried towing it indoors to avoid the rain. The chassis would not move as its parking brake was still engaged.
The technician stopped and exited the tractor, leaving it parked on a downgrade with the engine running, parking brake released, and wheels unchocked. He told another technician to reconnect the chassis’ air lines so its parking brake could be released. He then knelt between the chassis’ wheels and waited while the other technician worked. When the air lines were reconnected, the restored air pressure released the chassis’ parking brake, allowing gravity to pull the tractor and chassis combo downhill. The mechanic was crushed by the wheels of the rolling chassis while the other mechanic, who was still under the chassis, was almost struck by the axles.
Investigators found that the yard tractor’s parking brake was disengaged and the chassis’ wheels were not chocked. The employer’s Accident Prevention Plan (APP) also lacked parking brake and wheel chocking requirements.
Rollaway Hazard Solutions
An effective way to prevent vehicle rollaways is by installing an electronic parking brake system. As a new safety technology, these systems automatically apply the truck’s parking brake if a driver has not set it before exiting the cab. The technology can be integrated with existing fleet telematics systems to notify managers when a rollaway occurred or almost happened so they can respond appropriately. Electronic parking brake systems do not replace the need to maintain safe driving and parking practices.
Employers should have parking brake and wheel chocking policies in their accident prevention plan that require vehicle operators to set the parking brake any time they park whether or not they exit the cab.
Operators who leave their truck unattended should be required to put their foot on the service brake, place the transmission in neutral, set the parking brake, stop the engine, lock the ignition, and remove the key and place it in their pocket. If parked on any grade, drivers must turn the truck’s front wheels to the curb or side of the road and chock at least one tractor drive wheel on each side.
An unattended truck parked on a very slight grade with its parking brake disengaged can easily roll away if it is bumped by another vehicle or equipment. Drivers should also check their dashboard parking brake indicator, if equipped with one, before exiting the cab. Supervisors should routinely check in-cab parking brake alert systems and take vehicles out of service when the systems are not working properly and need repair.
Parking brake and wheel chocking policies should also state that when the air supply lines to the tractor, chassis, or trailer parking brake or spring brake are disconnected during maintenance operations, technicians must chock the vehicle’s wheels until the lines are reconnected and the parking brake can be safely released.
The tractor to trailer air supply should not be restored before the air lines to the brake chambers are reconnected and the wheel chocks can be safely removed and parking brake released. The parking brakes should also never be manually released or caged before the wheels are chocked.
If a truck’s front or rear wheels are lifted or set on jack stands, then the wheels remaining on the ground must be chocked. Checkboxes on vehicle inspection and service forms can ensure mechanics set the parking brake before they inspect or work on a vehicle. Signage can be placed in maintenance shops, terminal yards, and loading docks to remind operators to set the parking brake, use wheel chocks, and engage trailer restraint locks if available.
With these strategies in place, facilities can better protect their workers, and ensure future deaths like these will be avoided.
Paul Karolczyk is a research investigator for the Washington State Fatality Assessment and Control Evaluation (WA FACE) program.
About the Author
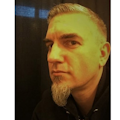
Paul Karolczyk
Paul Karolczyk is a research investigator for the Washington State Fatality Assessment and Control Evaluation (WA FACE) program that is part of the Safety & Health Assessment & Research for Prevention (SHARP) program at the Washington State Department of Labor & Industries. He was previously the technical safety expert for SHARP’s Trucking Injury Reduction Emphasis (TIRES) project.