Gerry Mead, VP of truck service at TravelCenters of America, has worked in the commercial vehicle maintenance industry since the mid-’90s, leading maintenance efforts for some of the largest fleets in the country. At this point, he’s regarded as a top fleet maintenance expert who can spot problems in the shop from a mile away. It wasn’t always this way. Early in his career, one oversight nearly cost him an eye.
“While replacing the decking on a gooseneck trailer, I was drilling out fasteners from underneath when a metal shaving ended up lodging in my eye,” Mead recalled. “I initially didn’t realize it, but it led to an emergency eye irrigation, followed by surgical removal of the shaving and a buffing procedure.”
Mead said he was wearing safety glasses at the time, though he admits sealed safety goggles would have prevented the injury. Looking back, he said this incident was a “tough but important reminder that working safely means you should “match the right PPE to the specific hazard, not just check the box.”
Mead’s pain penance was relatively light, considering he kept his vision. But accidents like this are far too common in the shop, despite OSHA mandates regarding the use of proper personal protective equipment, such as face shields for welding and gloves for handling lubricants. And it’s the duty of shop leadership to ensure that the right type of PPE is always used for specific work.
“Technicians work in high-risk environments every day,” Mead offered. “Hands and eyes are two of the most vulnerable parts of the body in a shop—and injuries aren't just painful; they can be permanently disabling. Protecting these areas is critical not just for safety but also for the long-term sustainability of operations because safe technicians are also productive technicians.”
Kyle Anderson, group manager of product marketing at Milwaukee Tool, agreed, noting, “Statistics show that hand injuries account for a significant portion of nonfatal workplace incidents, leading to lost workdays, while eye injuries remain a daily concern."
“Where there are hazards such as flying debris, chemical splashes, and sharp objects, without proper protective gear, technicians face serious injuries that can impact both their safety and productivity,” he continued.
John Kelly, safety sales specialist at Brass Knuckle Protection, noted there is not a one-size-fits-all approach to PPE. Each task should be evaluated individually based on adequate protection and performance.
“For example, for hand protection, it’s important to remember that meeting dexterity needs is as critical as cut protection,” Kelly continued. “A glove that has a high level of cut protection could reduce dexterity. If technicians use rotational tools like impact hammers and screw guns, polyurethane will be a better choice because it has good grip but isn’t as sticky as foam nitrile, so it reduces the risk of a glove becoming wrapped around the rotating tool.”
The important thing to remember is that the PPE should shield your workers from the worst-case scenario.
“Sometimes glasses aren’t enough,” Kelly stated. “There’s potential for stored energy in many vehicle maintenance applications. There are belts that have a tensioner, which can suddenly break free. Antifreeze is under pressure at high temperatures, so you may need full-face protection to reduce the risk of catastrophic injury, whether from an extreme burn or object impact.”
That may seem like an overabundance of caution as your techs likely perform the same type of jobs hundreds of times without incident, but the managers’ job is to mitigate risk. As the saying goes, “Accidents happen.”
That’s why at Fleet Fast, an Akron, Ohio-based commercial vehicle body shop, using the proper hand and eye protection is non-negotiable, noted Brian Joseph, the company’s operations manager. There’s rarely a moment when someone isn’t using power tools to grind, cut, weld, or paint.
“It's not just about compliance; it’s about making sure our team gets home safely every day,” Joseph said. “We’ve seen firsthand how a small mistake can turn into a serious injury if the right PPE isn’t being used.”
What is the cost?
The cost of not having hand and eye protection programs or non-compliance by technicians is staggering on multiple levels, Mead noted. “From a human standpoint, one serious eye injury or hand laceration can change someone’s life,” he said, “and from a business perspective, OSHA fines, workers' compensation claims, and lost productivity due to injuries add up quickly.
“But beyond dollars and cents, non-compliance erodes the safety culture,” Mead added. “When one technician cuts corners, it can set a precedent, and soon others follow. That’s why we don’t treat PPE as optional.”
Kevin Botosan, production manager at Fleet Fast, pointed out that injuries lead to lost time and unnecessary liability. “One eye injury or deep hand laceration can put a technician out for weeks,” he said. “That affects not just the employee, but the entire flow of the shop. We run on quick turnarounds and tight deadlines, so keeping our people protected keeps the business running smoothly, too.”
Failing to implement proper hand and eye protection programs can result in costly consequences for both workers and businesses, including medical expenses, lost productivity, and potential legal liabilities, Anderson pointed out. “Safety investments are a necessary precaution that not only comply with regulations but also foster a culture of protection, ensuring technicians can work confidently without the fear of injury,” he said.
“There are a number of ways to consider costs,” said Kelly. “You need to factor in medical care, lost time and productivity, and workers’ comp claims. There’s also the possibility of increases in insurance costs and the loss of reputation or even loss of business due to negative publicity.
“According to an OSHA calculator, the average cost of a laceration injury is $46,000 and for vision loss, the cost exceeds $200,000,” Kelly continued. “It seems clear that a little prevention goes a long way.”
About the Author
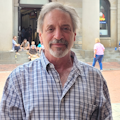
Seth Skydel
Seth Skydel, a veteran industry editor, has more than 36 years of experience in fleet management, trucking, and transportation and logistics publications. Today, in editorial and marketing roles, he writes about fleet, service, and transportation management, vehicle and information technology, and industry trends and issues.