When a “check engine” light illuminates, a truck driver has to hit the brakes and get out the code scanner. If the problem detected doesn’t require immediate attention, the driver can get back on the road and deal with the problem once the job is done and the load is delivered. But if the problem requires immediate attention, the driver will have to make a trip to the mechanic. The lost time and the amount of money spent on repairs and maintenance add up, but luckily for Volvo truck owners, there’s a way to reduce the number of faults experienced.
Volvo Trucks recently conducted a one-year study that followed a group of about 10,000 trucks that were model year 2019 and newer. The study sought to provide data by the numbers of the impact of Remote Programming (over-the-air updates) on Volvo trucks. At the end of the study, Volvo discovered a 51% reduction in faults for trucks that received OTA updates, indicating that updating a truck significantly reduces faults and that reduction in faults led to other benefits as well.
See also: Volvo Trucks introduces Turnkey Solutions for full-service EV infrastructure
Volvo Trucks has offered over-the-air updates for its trucks equipped with Remote Diagnostics hardware since 2018. Now as trucks across the industry become more connected, these updates are getting more advanced and provide benefits to fleet owners and drivers.
Volvo Trucks’ Remote Programming service allows drivers to connect to the Volvo Uptime Center and perform OTA parameter and software updates within 15 minutes while pulled over for a break or even at the jobsite. Remote Programming updates are available for the engine, aftertreatment, and transmission modules (ECUs). These updates can fix or improve code, optimizing vehicle performance and thereby reducing the number of faults experienced. Remote diagnostics can also remove false positives from previous versions, another hassle-saving benefit of OTA updates.
“Basically, what a fault means is that a driver will have to stop… and get the truck fixed,” Cheyene De Souza, product marketing manager for safety services at Volvo Trucks, told FleetOwner. “So, we can translate a fault in dealer visits. When you have less faults, you have less dealer visits.”
By the numbers
For this test, Volvo analyzed engine modules, of which Volvo releases updates either one or two times per year. Of the 10,000 trucks in the test group—a group of fleet trucks in various applications—Volvo recorded the faults that occurred six months prior to the OTA software update and six months after the update.
Before the updates, the 10,000 trucks experienced 10.9 million total faults. After the updates, the trucks experienced 5.3 million total faults—a 51% reduction in faults. That’s more than half the number of faults experienced by implementing OTA updates alone. But not only do OTA updates reduce faults, they also reduce trips to and time spent at the dealer.
Fortunately, not every fault code warrants a trip to the dealer, but when it does, the truck must be taken out of service. Of the trucks that were part of the study, those that received OTA updates through Volvo’s Remote Programming took 25% fewer visits to the dealer than trucks that didn’t receive OTA updates.
See also: Hype is real with predictive maintenance
“You can translate that 25% to around one dealer visit per year, which is a very representative number,” De Souza said. “If I go a little bit further, it's not just less faults, meaning less visits, it's also less time at the dealer. That dwell time is also reduced. If you think about it, when you have your truck updated and it’s running to its optimal performance, when you get to the dealer, it will be easier to diagnose— and will be easier to repair.”
For those that like numbers, De Souza said that equals out to about 24% less dwell time for trucks that receive OTA updates. Based on the numbers, that’s about 32 hours saved per year.
A benefit to drivers and technicians
Time savings and savings on the costs of repairs is possibly the biggest advantage of OTA updates, but Volvo truck drivers and technicians experience benefits as well.
According to WorkHound’s 2023 Driver Perspectives Report, driving trucks that are in need of maintenance is a significantly negative theme among truck drivers. One driver in the report said, “If you really want to know how to crush a driver’s spirit, they do that by not fixing his/her trucks.”
In this competitive market, it’s even more necessary that a driver’s truck is operational and ready to roll as often as possible.
“The one thing that a driver doesn’t want is an unplanned stop,” De Souza said. “By keeping the truck updated, you have less faults … but also you have less risk of an unplanned stop.”
When drivers do have to take their trucks to the shop, as De Souza mentioned, if they’re updated, typically, they are more quickly repaired. This benefits the driver in terms of time savings as well as the technician working on the truck. On an updated truck, De Souza said the diagnostic process will be quicker because “a healthier truck is easier to repair.”
“Even for a technician that's not from Volvo, he will go to the instrument cluster of the truck, and probably, one of the first things they would do is check for updates on the software,” De Souza said.
A technician will have to perform a software update if the truck isn’t up to date. Technicians working on updated Volvo trucks will be able to skip that step.
De Souza said that Volvo strives to “give the best tools for drivers and for fleets to have the best of those trucks, have their best performance, and the best driver productivity they can have.”
And having OTA updates helps them do just that, because the Volvo truck receiving OTA updates becomes better and better each time an update is performed, which results in better performance, reduced dwell time, and improved productivity.
About the Author
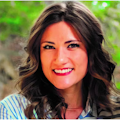
Jade Brasher
Senior Editor Jade Brasher has covered vocational trucking and fleets for the past five years. A graduate of The University of Alabama with a degree in journalism, Jade enjoys telling stories about the people behind the wheel and the intricate processes of the ever-evolving trucking industry.