Breaking down heavy-duty air brake maintenance
Electromagnetic braking systems likely represent the future of heavy-duty trucking, but air brakes continue to represent the present. Manufacturers of both drum and air disc brakes (ADBs) have continued making design enhancements, giving fleets plenty of options to improve longevity while simplifying maintenance.
When selecting a brake system, fleets should consider the benefits of each style. Generally speaking, drum brakes are known for their durability, parts availability, and lower purchase price. While a bit more expensive up front, ADBs are known for their reduced stopping distance and fade.
“Fleets should evaluate duty cycles and lifecycle costs,” said Joe Kay, director of engineering at Meritor, a supplier of drivetrain, mobility, braking, and electric powertrain solutions. “One key consideration is routine maintenance. Overall, disc brake maintenance is simpler and takes less time.”
With ADBs, Kay said Meritor has seen consistent performance and feel regardless of duty cycle. That said, the benefits of ADBs really shine through on vehicles with brakes that run hotter, such as city delivery, transit buses, and refuse collection. “The rotor is exposed, so heat is easily released into the atmosphere, which helps lengthen service intervals and improve stopping performance,” Kay explained.
“Disc brakes actually perform better when they get hotter,” added Kevin Rose, director of fleet sales for the Commercial Vehicle Solutions (CVS) division of ZF Group. “If a truck is operating in an environment with a lot of hills or mountain grades, for instance, spec’ing disc brakes is a good idea.” CVS is the result of ZF’s recent integration of its Commercial Vehicle Technology division and Commercial Vehicle Control Systems division, formerly WABCO, which ZF acquired in May 2020.
Adoption drives ADB innovation
“Now that disc brakes have been capturing a larger piece of the overall equipment rate, we are optimizing ours to fit particular applications,” said Keith McComsey, director of air disc brake and systems product group at Bendix Commercial Vehicle Systems, a provider of safety technologies, energy management solutions, and air brake systems and components. “We are taking weight out of the brake for some of the lighter-duty applications such as linehaul. For applications with a higher braking duty cycle, such as school bus and refuse, we’ve optimized the pad friction, so it wears at a much slower rate at a higher temperature range where those applications tend to operate at more frequently.”
See also: The ABCs of ADBs
Haldex, a supplier of brake systems and air suspension systems for heavy-duty trucks, has made improvements to its air disc brake caliper, the ModulT. “This second-generation caliper is as durable as its predecessor and has the same braking performance yet is lighter at the same time,” said Daniel Ślimakowski, Europe, Middle East, and Africa fleet sales manager at Haldex. According to Ślimakowski, disc brakes should balance durability and weight for a fleet to reap maximum benefit.
ZF has made some improvements to its WABCO MAXXUS 2.0 Air Disc Brake, including enhancements to the internal adjustment mechanism. “There is a significantly reduced opportunity to have a hot brake or hot runner situation,” Rose said.
Fleets are also benefiting from improved seal protection.
“We’ve done a tremendous amount of field testing and have found that in some extreme climates such as northern Canada, having redundant seals that prevent water ingression and foreign particles from getting into the adjuster mechanism, slide pins, and throughout the braking system helps eliminate the potential for downtime,” Rose said.
Meritor has taken steps to further guard against debris and heat exposure. The EX+ LS Air Disc Brake has several unique design features, including an advanced seal protection that protects the piston boot until the pads are significantly worn and need to be replaced.
Manufacturers have also made advancements that make disc brakes even easier to inspect and maintain. Many disc brakes include built-in wear indicators that are integrated into the caliper/carrier. This provides a relatively easy way for technicians to monitor pad and rotor wear in the lead-up to performing a wheels-off inspection or pad replacement.
Technology is helping improve the monitoring process even more. For instance, pad wear sensor devices are available as an option on the Bendix ADB22X Air Disc Brake for tractors and trailers. Sensors are installed on the pads. When friction thickness reaches approximately 3.5mm, the system triggers a signal. A diagnostic code or message is then created and made available to the telematics system.
The WABCO MAXXUS 2.0 has also incorporated pad wear sensors. OEs can incorporate the sensor data into their telematics system. Meritor’s EX+ LS Air Disc Brake offers an electronic pad wear warning indicator as optional equipment.
Disc brake maintenance
As manufacturers have made design enhancements to improve disc brake life, technicians should not take that as a cue to relax preventive maintenance.
“One of the myths out there is that air disc brakes don’t need to be inspected as much,” Bendix’s McComsey said. “But it’s still a brake, and it needs to be inspected just as often as a drum brake. Refer to our service data sheet that provides recommended inspection intervals, which vary slightly by application.”
Generally speaking, wheels-on inspections should happen at least every four months for OTR applications and every three months for buses, vocational trucks, and delivery vehicles. Technicians can check pad thickness by monitoring the mechanical wear indicators. Additionally, rotors can be checked for cracks. McComsey said tools like mirrors and borescopes can improve the visual inspection process.
If any issues are observed during a wheels-on inspection, a more thorough wheels-off inspection should be scheduled promptly. And even when no issues are detected, a more thorough wheels-off inspection should happen at least once a year. Technicians should inspect the pads and entire rotor surface for cracks, as well as running clearances, adjuster operation, and caliper travel. Tappet and boot assemblies should also be inspected along with all related caps and hoses.
It is important to regularly check the condition of the caliper. “Every year, a technician should check the condition of the various parts of the caliper, such as plugs, protective cups, thrust plate guide pins, adjustment spindle bellows, and slide function,” Haldex’s Ślimakowski said.
Drum brake developments
Manufacturers have also been making design improvements to extend drum brake life.
“One of the most recent changes we’ve made has been the move to improved coatings and assembly processing to counter the impact of corrosion on the overall brake system,” said Pat McNamara, VP of sales and marketing at TSE Brakes, a provider of brake chambers, slack adjusters, and brake-sensing technologies.
“Frictions are now lasting 300,000 to 400,000 miles in some cases,” said Frank Gilboy, director of foundation drum brake and actuators at Bendix. “The period in between disassembling the system to make repairs or replacements is a lot longer. The risk is that things aren’t being looked at as often. So, in reality, longer-lasting components actually reinforce the importance of understanding the preventive maintenance intervals recommended by the manufacturer.”
Technicians should regularly inspect the friction for abnormal wear and cracks. Additionally, it’s important to measure the free play to ensure that it remains within the allowable 3/8” to 5/8” range. If the free play falls outside of this range, look for any signs of damage. Brake stroke should also be checked and compared to the specification for that chamber. The S-cam and slack adjusters should always maintain proper lubrication.
McNamara said there are key maintenance aspects with respect to brake chambers as well.
- Look for worn, loose, or missing chamber mounting nuts.
- Ensure proper chamber mounting and alignment.
- Ensure that breather caps aren’t damaged or missing.
Just like with disc brakes, technology is beginning to provide some assistance to technicians working on drum brakes. For instance, TSE Brakes has introduced TSE-Sense. Currently available for trailers, TSE-Sense continuously monitors brake stroke and transmits the data to a data integration box mounted on the sliding tandem frame. The box communicates with the trailer’s telematics system to alert technicians to stroke issues.
Cut that slack adjuster some slack
When it comes to drum brakes, automatic slack adjusters continue to frustrate many technicians. But those frustrations are often a matter of misinterpretation.
According to Bendix’s Gilboy, it is amazing how many slack adjuster problems go away when technicians take the time to grease the slack adjuster, cam tube, and other areas so everything can move freely. “This can really be a problem on trailers because they can get ignored a little more, leading to more slack-related problems over time,” Gilboy explained.
If excessive brake stroke is ever suspected, ZF’s Rose said the first thing a technician should do is conduct the CVSA applied stroke test to confirm that there is a brake adjustment issue. From there, it’s important to follow manufacturer test procedures to ensure that the slack is working properly.
One procedure that must be avoided is manually adjusting an automatic slack adjuster. If brake stroke is excessive, it is usually a sign that either the slack adjuster is worn out and needs to be replaced or that something else is going on. Excessive wear of the cam head, bushings, or rollers could cause brakes to fall out of adjustment, but many times, the problem simply lies with a lack of lubrication.
If it’s concluded that the slack adjuster doesn’t need to be replaced, Rose said the next step is to simply begin doing visual checks of the various components throughout the system. One thing to look for is worn components. For various reasons, a technician will sometimes reuse certain hardware and other components when doing a brake job. That same thing could have happened when a slack adjuster was replaced in the past, and the same mounting hardware was reused.
Sometimes a slack adjuster simply needs to be replaced. When that is the case, Meritor’s Kay said that it is best practice to replace slack adjusters in axle sets or pairs to maintain balanced braking performance.
When it comes to any braking system, safety is always the number one consideration—and balance, stopping distance, longevity, and ease of maintenance all play into that.
About the Author
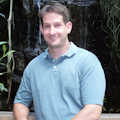
Gregg Wartgow
Gregg Wartgow is a freelancer who Fleet Maintenance has relied upon for many years, writing about virtually any trucking topic. He lives in Brodhead, Wisconsin.