Tired of tire service? Robot wheel changer is on the way
When you get too much wear and tear on your tires or brakes, you simply swap them out. And that requires a technician to physically remove up to four heavy wheel assemblies, and then replace them when they’re done. It’s one of the most common—and physically demanding—jobs in the shop, leading to plenty of wear and tear on your tech’s upper body. And those are not so easy to swap out. Even in the best-case scenario, low-value jobs like rotating all four tires take up precious shop space and your tech’s valuable time, while the repetitive, high-strain work slowly rips and pulls at their muscles and ligaments.
For more on tire technology and maintenance:
According to a startup called PitPro Automation, this is the perfect job for robots. Not the humanoid Optimus developed by Tesla, mind you, but an automated wheel changer that’s equal parts NASA and NASCAR, comprising a traditional off-the-shelf alignment lift with two gantry robots that can torque and untorque lug nuts with steely precision, and remove and replace the wheels without breaking a sweat. Pre-loaded new wheel assemblies are stocked on an attached carousel. A tech still manually controls the lift and positioning of jacks, but the robot drastically slashes repair time.
“We can access all four wheels, take them off, [and] put them back on in 15 minutes,” CEO and founder Jeremy Conrad told Fleet Maintenance. The MIT graduate tested laser-guided missile defense systems as an Air Force officer before starting a robotics venture capital fund.
The San Francisco-based company, which revealed the automated wheel changer in late June, estimates this is 80 to 90% faster than a human, ultimately savings fleets up to $300 in downtime costs per tire service.
“Managing service operations across 10,000+ Ford dealers, I saw how downtime and technician shortages cripple fleet profitability daily,” stated former Ford Pro CEO Ted Cannis, who previously worked with Conrad. “PitPro’s fleet-focused automation directly solves these operational challenges that impact customer deliveries while improving efficiency.”
The robotic technology can also sense tire tread depth and psi, as well as detect broken or stripped nuts. The shop also shouldn’t worry about wheel-offs, as the system torques within 1% of OEM specification and records the data.
The company is targeting fleet customers with Class 3 or lower pickups and vans, so under 14,000 lbs. GVWR. They can modify the design based on a customer’s needs, with the largest version for Sprinter vans (170-in. wheelbase) spanning about 15 ft. across and 35 ft. long, explained Gui Cavalcanti, PitPro’s head of engineering. It was designed to fit into your typical commercial vehicle bay, “hugging the sides of the vehicle with only a couple inches gap,” Cavalcanti explained, adding a laser curtain can be added as a safety measure to shut the machine off if a worker or foreign object breaks the plane. The lifts anchor into the ground with no infrastructure changes required.
Cavalcanti, who spent his formative years at Boston Dynamics developing what would become Atlas, then co-founded a short-lived-but-fascinating giant robot fight club called MegaBots, said the company’s future ambitions include bulking up to handle Classes 5-8 tires, and even balance tires and change brakes. (Coincidentally, NASA and NASCAR were actually involved in the development of MegaBot’s Eagle Prime, which Cavalcanti co-piloted in a battle of honor against a Gundam-style Japanese robot.)
Read more: USA Wins Giant Robot Brawl, Leaves People Wanting More
But for now the company is looking for service centers with 10-20 bays or fleet depots with 200+ light-duty assets to pilot the technology early next year. These scaled-down pilot versions “are basically a hydraulic robot that looks like a very fancy moving version of any other lift to their shop,” he said, noting the machine will use “the same basic tech shops are used to seeing, like cylinders, cables, and chains.” The system can run off 208V three-phase or 240V single-phase power.
And don’t let the high-tech gadgetry fool you; the automated platform exists to make technicians’ and shop managers’ lives much easier.
“If you have a de-scoped, constrained problem set, like for fleets working with lots of the same vehicles, you can actually make the robot really, really good at that thing,” Cavalcanti assured.
Lifting the burden
In preparation for inventing the wheel changer, both Conrad and Cavalcanti earned “higher level certification” from the Tire Industry Association and talked to several tire shops. The biggest advantage Conrad believes this machine offers them is “taking some of that heavy lifting away from the technicians, so they can focus on higher value work like working on an engine.”
Removing this burden also mitigates the risk for shop injuries related to mishandling commercial tires, such as a fractured foot or sprained wrist, as well as ones caused by repetitive lifting, such as a slipped disc or torn labrum.
“People just can’t stay in it very long without literally breaking their backs,” Cavalcanti added, noting wheel assemblies “are getting heavier and heavier,” with a Ford Transit’s assemblies each weighing nearly 80 lbs. “If you’re doing two cars an hour for a full workday, you’re done after two or three years.”
Conrad said one national chain considering becoming an early adopter admitted their turnover was around 120%.
“Even beyond the musculoskeletal stuff, it’s just a brutal profession,” Conrad asserted, citing anecdotes from shop managers like trying to handle frozen lug nuts in the winter or working in a sweltering Florida shop without climate control.
Finally, automation like this opens up roles for techs willing to join the trade but not built for the physical demands.
“If you can’t lift those big tires, male or female, whatever, it just means you can’t get to that next level—and so I certainly think that this is the technology that really can open it up,” Conrad said. “There are lots of different ways to adjust for the tech shortage, and I really think we’re going to have to try all of them, or this is a field that’s going to continue to struggle.”
About the Author
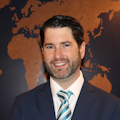
John Hitch
Editor-in-chief, Fleet Maintenance
John Hitch is the award-winning editor-in-chief of Fleet Maintenance, where his mission is to provide maintenance leaders and technicians with the the latest information on tools, strategies, and best practices to keep their fleets' commercial vehicles moving.
He is based out of Cleveland, Ohio, and has worked in the B2B journalism space for more than a decade. Hitch was previously senior editor for FleetOwner and before that was technology editor for IndustryWeek and and managing editor of New Equipment Digest.
Hitch graduated from Kent State University and was editor of the student magazine The Burr in 2009.
The former sonar technician served honorably aboard the fast-attack submarine USS Oklahoma City (SSN-723), where he participated in counter-drug ops, an under-ice expedition, and other missions he's not allowed to talk about for several more decades.