This is Part Two of a three-part series.
With tires as one of the highest operating costs for fleets, having a solid program to manage tire monitoring and maintenance can make a big difference in keeping fleet costs in check and fuel efficiency at a maximum. In Part One of this story, we discussed how tire pressure and duty cycle can impact tire life for a fleet.
But to keep track of that life, fleets also have to establish best practices for inspections and tracking their tire efficacy. Whether a fleet uses digital software or excel sheets, thorough and consistent record-keeping can help maximize tire life cycles and lower maintenance costs.
Best practices
Valentino Faraone III, regional vice president, new product development manager, Double Coin said the best place to start when it comes to keeping tire costs in check is to conduct pre-trip and weekly yard inspections.
“The weekly yard checks are so important that having someone from maintenance or your commercial service tire provider conduct them will pay off, regardless of what it costs to provide this service,” he stated. “Although this is a fixed weekly expense, it’s a better investment than dealing with costly tire failures on the road.”
During these checks, Faraone related, tires should be either inflated or deflated to the proper psi, and dual assemblies should be inspected to ensure air pressures are correct and treads are wearing evenly. Typically, he added, a service provider will have additional tires on hand and can replace any tires that are a maintenance concern.
“It’s critical for fleets to conduct efficient tire checks and digitally capture crucial tire data to streamline maintenance and management,” said Chris Garcia, head of U.S. automotive business, Anyline. “This allows for accurate tracking of tire conditions, usage patterns, and maintenance history, and provides insights that help optimize tire life and reduce costs.
“By analyzing this data, fleets can make informed decisions on tire maintenance schedules, retreading timing, and inventory management, ensuring the right tires are used and maintained effectively,” Garcia added. “The integration of mobile data capture and analysis drives down tire-related expenses by pinpointing areas for improvement specific to each fleet’s needs.”
Read more: Tire makers discuss spec'ing commercial tires by duty cycle
Jim Garrett, product category manager, Michelin North America, pointed out that sophisticated on-board tracking and monitoring systems can also be used to process and understand data and recognize ways to generate a quick payback from improved and effective tire maintenance.
Measuring up
Tire performance can be measured by continuously gathering feedback from drivers, maintenance personnel, and fleet managers regarding tire performance and durability, related Dave Johnston, division head, product & pricing, CV at Apollo Tires. “Use this feedback to make adjustments to tire specifications and maintenance practices to further optimize performance and cost-effectiveness,” he said.
Garret said that type of analysis can validate the various approaches fleets take to ensure the lowest tire costs. In order of cost of investment, he added, the payback can be determined for driver training; maintenance personnel training for things like tire mounting best practices; pre-trip checklists with pressure checks; preventive maintenance pressure checks; new valve stems every time a tire is replaced; digital tire gauges for maintenance personnel, and even pressure stickers on the vehicle for each wheel position.
“Some fleets are using Excel-based spreadsheets to monitor tire performance, constantly evaluating and benchmarking,” Faraone said. “Even this simple procedure can allow a maintenance manager to see irregularities and investigate further to find and address the root cause of high tire costs. Today as well, many new state-of-the-art software programs make this task even easier and present data more concisely.”
Shaun Uys, vice president, Truck Tires U.S., Continental, said routine cost-per-mile analyses should include tires to pinpoint where expenses may be higher than expected. “Fleets can measure tire costs per mile every day, the same way they track all expenses,” he said.
“While fleets do typically measure expenses on a cost-per-mile basis, when it comes to tire assets it can be helpful to evaluate costs and performance from a total cost of ownership perspective,” Garcia explained. “Assessing tire lifespan and evaluating utilization is critical for being able to extract maximum value from each tire.
“It’s also helpful for fleets to measure their retread utilization rate and the savings that result from keeping tire casings in service longer,” Garcia continued. “These metrics offer a holistic understanding of tire-related expenditures, guiding fleets toward optimized cost efficiency.”
For more information on digital tire management solutions and other savings to be reaped from a fleet's tires, see Part Three of this story.
About the Author
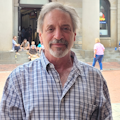
Seth Skydel
Seth Skydel, a veteran industry editor, has more than 36 years of experience in fleet management, trucking, and transportation and logistics publications. Today, in editorial and marketing roles, he writes about fleet, service, and transportation management, vehicle and information technology, and industry trends and issues.