UPS is in business to synchronize the world of global commerce. To that end, they deliver more than 15 million packages a day to more than 7 million customers traveling 3 billion miles per year. It’s a logistical ballet that relies heavily on an automotive fleet that numbers more than 100,000 vehicles.
Those vehicles range from what UPS calls “package cars,” the ubiquitous brown stepvans, to tractor trailers, with a very wide variety of vehicle types, brands and models. UPS also operates one of the nation’s largest fleets of alternative fuel and hybrid vehicles.
Properly maintaining its massive fleet is critical to the company’s success, and it has recognized this since it plied the streets of Seattle with Model T’s in the early 1900s. Globally, UPS has some 5,000 technicians stationed at nearly 1,800 maintenance facilities.
Just as it has with its army of iconic brown-clad drivers, UPS has developed its own methods and procedures for the maintenance of its fleet. The company is increasingly using technology to capture vehicle data which is analyzed in order to make improvements in fleet maintenance and repair processes.
TECHNICIAN RECRUITMENT
Regardless of how good any maintenance program is, it will not produce results if there are not capable and qualified technicians to do the work.
When recruiting technicians, there are specific things UPS looks for. Once hired, UPS has a highly structured methodology for training and development.
UPS has found that certain key criteria improves its success rate in hiring and retaining technicians, says Vic Mariano, the company’s corporate automotive training manager.
It looks for technicians who have most, if not all, of the following qualifications:
- A minimum of five years of heavy truck experience.
- Are experienced with computers, scan tools and diagnostic equipment.
- Are able to work various shifts, especially nights, because that is when repair and maintenance of much of the company’s fleet takes place.
- Have a commercial driver’s license and a clean driving record.
Technician certifications, such as ASE, are not required, but are a plus. So are college degrees and continuing studies. “Because we often promote from within at UPS, there are opportunities to move into management,” Mariano says, and notes that he started his career with the company 32 years ago as a technician.
Like others companies, UPS uses a host of methods to recruit technicians. All can be effective depending on each situation, he says. Most often, the strongest candidates have come from referrals from technicians who work at UPS.
CONTROLLED PROCESS
The vehicle technician job at UPS is very structured, with assigned fleets and weekly work schedules that are planned by the supervisor and technician to ensure the work is prioritized properly to make the most efficient use of the technician’s time.
The foundation of UPS’s technician training is what it calls the Pre-Seniority Training Period - essentially a “try-out” for a technician to make the UPS team. It’s an extensive program that averages 45 days.
The Pre-Seniority Training Period is a well-defined process aimed at taking a new hire through several distinct elements of training. It begins with an “introduction” to the company and its history, then covers business conduct, procedures and policies at UPS.
Next comes safety training and regulatory compliance, which includes all applicable OSHA, DOT and EPA rules and regulations. “Safety and safety training is paramount and ongoing at UPS,” Mariano says.
When safety and regulatory compliance training are complete, managers start to evaluate a new technician’s skills and qualifications. Progress reviews are done weekly throughout the training period.
These reviews are very important to let the technician know how they are progressing, as well as to review positive points and areas the technician may need to focus on.
“Our Pre-Seniority Training gives the new technician a feel for what it’s like to work for UPS,” he says. “Just because we hire a person as a technician, the position may not be a good fit for him or her so it works both ways. We get a chance to evaluate the individual, and they get a chance to evaluate the job.”
PMI METHOD
The next element of the Pre-Seniority Training Period is preventive maintenance inspection (PMI) training. “The preventive maintenance program at UPS is the backbone of our whole operation,” emphasizes Mariano. “With effective preventive maintenance, we’re able to have minimal vehicle breakdowns on the road. That means we deliver our customers’ goods on time, and that means we’ve kept our promise.”
For UPS’ PMIs, in addition to checking components required by the DOT, there is a prescribed method for completing them, he explains. “The level of detail we go into for our PMIs, which require several hours to conduct, is key to our vehicle reliability and helps keep our operational costs manageable.”
Regardless of their experience, all new technicians at UPS are trained and certified on the UPS PMI process during the Pre-Seniority Training Period.
Just as it does with its drivers, UPS assigns its technicians the same vehicles to work on. By doing this, the technicians “get more familiar with the vehicles and take ownership of their fleet,” says Mariano. “It becomes a matter of pride in keeping their fleet in top shape.”
As with everything at UPS, vehicle reliability, maintenance expense and technician performance are constantly measured.
DIAGNOSTIC SKILLS
Evaluating a new technician’s ability to diagnose the source of a problem quickly and accurately, along with their mastery of repair skills, is another aspect of the Pre-Seniority Training Period. Technicians are observed by their supervisor as they diagnose a problem, set up for the job and then make the repair. This is done on the shop floor, rather than in a classroom with mock-ups or training displays.
“The problems are real-life and done on active fleet vehicles,” Mariano says. “When we hire a technician, it’s not as if they are an extra person on the shop floor. We need them to contribute quickly to keep the maintenance program on track. After the safety and PMI training and certification, we get them going right away and observe how they do.”
There are a handful of key repairs - brakes repairs, replacing a clutch or transmission, diagnosing vehicle electrical problems, for example - on which technicians are evaluated to make certain they have the required skill level to properly and effectively complete the repair.
In addition, new technicians receive training on the emerging technology of telematics and condition-based maintenance. Condition-based maintenance offers proactive notification of impending vehicle component failure.
Once a new technician successfully moves through the Pre-Seniority Training Period they gain their seniority and join the UPS team. Technicians at UPS are union employees.
GOOD START
UPS works hard to get technicians off to a good start. The technicians know early on what is expected of them. Plus, they are given all the procedures and policies they need to follow, along with the necessary beginning training.
“With all this, they can have a long, productive career at UPS,” says Mariano.
He notes that technicians tend to stay a long time at UPS. “There is very little technician turnover. We offer a competitive pay and benefits package, and we work hard to make UPS a good place to work.”
CONTINUAL EDUCATION
Recurrent training is done annually at UPS, which includes safety training and all training required by regulatory agencies.
“Continual education and training is very important in order to stay current on what is happening in the industry, on the regulatory front and with new vehicles and technology,” Mariano says.
Company-wide, about half of all the training at UPS is devoted to safety. That amounts to $175 million every year.
UPS also provides web-based training for its technicians. UPS maintains a large online library of training materials for its technicians through its own Learning Management System.
UPS also takes advantage of manufacturer-supplied training and uses outside trainers as well.
TARGETED TRAINING
“Because some of our vehicles are used for 20-plus years, there is the challenge of keeping technicians up-to-date on new vehicles and vehicle technology,” says Mariano. “When we buy new equipment, part of our process is to have suppliers include training with the purchase.
“Our new vehicles often get spread out nationwide, so it’s difficult to get everybody trained on every new piece of equipment. But our goal is to make sure all technicians are at least familiarized with the main features and differences, and understand the key things they need to know to maintain any new vehicle.”
Because trucks in general have become more reliable, UPS can delay the roll-out of some in-depth new vehicle training until the trucks have been in use for a while. “Otherwise, technicians could forget the course content since it may take a year or so for some repairs to be necessary,” he says.
However, targeted training is done when and where needed, say when a facility gets new hybrid or electric vehicles.
UPS also does initiative-based skills training when the company deems it necessary. This could be when a company-wide issue arises with electrical systems, or if a new diagnostic tool is rolled out, or if there is the need to implement some business initiative.
In such instances, UPS will develop training sessions that address the concern or initiative. This could be online, hands-on or a blended solution - whatever is the most effective way to deliver the training is done.
In addition to training on vehicle repairs and maintenance, UPS also provides training on shop test equipment. “Because we have such a diverse fleet, our technicians need to be proficient on all types of scan and diagnostics equipment,” he says.
TRAINING ROI
“Our goal is to get immediate feedback on training course content and delivery,” says Mariano. “From there we measure application of learning in different ways, including testing or observation. The measure of effectiveness of any training program is how it contributes to the bottom line results.
“It may not always be a purely financial measurement,” he notes. “It may be vehicle reliability, technician safety or cost per mile.
“However, we know without a doubt, training contributes to helping us reach our goals. We couldn’t be where we are today as a company without an effective training component.”
Mariano points out that the technicians at UPS “know they’re an integral part of the on-time delivery of packages. We’re in the business of satisfying customers. The ultimate goal of everyone at UPS is perfect service.
“The job of the UPS technician is to keep our vehicles in service, keep our drivers’ wheels moving and help us keep our promise to our customers. That’s how we roll.”
A commitment to technician training
Penske Truck Leasing, one of the largest transportation services companies in North America, continually trains its maintenance personnel because “we need to keep pace with state-of-the-art technology, government regulations and the advanced techniques required to keep a fleet of 210,000 vehicles operating optimally,” says Holly Gerke, the company’s manager of technical training.
The training - a mix of in-house, third party and OEM initiatives - focuses on preventive maintenance, technical and diagnostic skills and the customer experience.
Penske features two types of maintenance technician training: a standard mandatory program, and the voluntary Continuing Automotive Service Education (CASE) program.
“With the mandatory training, the goal is for each technician to receive 40 hours of annual training,” she says. “The Penske CASE program was just re-certified by ASE, after we first obtained the certification in 2008.”
Gerke notes that one of the benefits of going through ASE’s application process was uncovering areas of needed improvement within Penske’s technical programs, as well as the processes to support these programs.
CAREER ADVANCEMENT
For those pursuing career advancement, Penske offers a voluntary certification program: the Technician Certification Program (TCP).
“It is designed to provide further education and training for critical job skills, matching each service classification in a blended learning approach,” explains Gerke. “The TCP’s requirements include self-paced hard copy and online activities, OEM instructor led classes and courses focusing on Penske’s internal maintenance procedures.
“A number of our senior maintenance leaders started with our company as technicians, so career advancement opportunities are always a part of the big picture planning,” she says. “It is important for Penske associates they are provided with the necessary tools to keep up with changes in technology and product advancements, and to increase the customer’s uptime.”
TEAM BUILDING
Several years ago, Penske realized that at the rate its fleet was growing, it would also need to continue to build its team of maintenance personnel in order to maintain customer service satisfaction.
“Young professionals in our business are interested in career development opportunities,” Gerke says. “The TCP program provides a clear path. We envisioned that it would improve our ability to recruit, and retain, qualified technicians.
“We also wanted to demonstrate to our customers that we invest in the education of our maintenance workforce. A highly educated team of technicians lends itself to the best customer experience.”
CONTINUOUS DEVELOPMENT
In addition to the multiple training programs Penske Truck Leasing operates on an ongoing basis, it has formed an internal Technical Training Advisory Board “to ensure that voices across all levels of the maintenance organization can be heard,” says Gerke. “The board plays a vital role in allowing Penske to drive continuous improvement.
“The board’s vision is to improve upon a world-class technical training program that instills motivation at all levels, and consistently demonstrates value to Penske and our customers.”
Hands-on diagnostic education
Fault codes are but one element in the process of determining an issue with a vehicle.
“Once you identify the code, you then have to know how to effectively diagnose what exactly caused the fault,” says John Arndt of Advocate Fleet Services and Associates, a company specializing in vehicle maintenance and repair issues. “Otherwise, you may not get to root of the problem and the issue will continue.”
Advocate Fleet Services has been retained by UPS to help its technicians master the company’s Service Bay Diagnostic Tool (SBDT). SBDT is used to help troubleshoot problems on UPS’ diverse fleet of various vehicle models and brands.
Arndt, who prior to starting his own company, was International’s manager of customer training, conducts SBDT training throughout the UPS system. SBDT training is a six-hour course that begins with a classroom session on the necessary steps to use the tool to diagnose fault codes.
He makes each session interactive because “training is always more effective when technicians are engaged and involved,” he says.
Arndt constantly challenges his students to make sure they have a clear understanding of what is being discussed.
Following the classroom session, the class moves to the shop floor where theory is put into practice. The technicians use the SBDT to actually diagnose different fault codes.
After completing this element of the training, the students return to the classroom for training on I-gate, UPS’ web-based enterprise-wide portal.
Among other things, I-gate contains an automotive component that includes OEM information and links to manufacturers’ technical websites, vehicle owner’s manuals, technician self-study program, training materials and much more.
Technicians appreciate the training because it helps them keep their diagnostic skills sharp, says Jack Hardt, fleet manager for the UPS facility in Addison, IL.
Managers and supervisors also take advantage of the SBDT training, adds Mark Collins, UPS’s Illinois district area automotive manager, because they need to stay current on new service technologies as well to better manage maintenance operations.
How to drill down to the type of technician required
There are numerous functions a technician plays within a lift truck dealership, as there are shop-based jobs and field-based (road technician) jobs for maintaining or repairing equipment, Jonathan Dawley, vice president of marketing for NACCO Materials Handling Group (NMHG) explains.
The company manufactures and distributes two separate brands of lift trucks: Yale and Hyster. Each brand is distributed through independent dealer networks.
“Field-based technicians have added responsibilities of maintaining inventory on vans, travel safety, time management, paperwork, jobsite safety, remote communications, customer interface, selling of required repairs, etc.,” he says. “As a result, dealerships must evaluate shop and road technicians with different criteria.”
NMHG provides its dealers with a technician assessment that can be utilized to evaluate readiness of a technician to perform the hard or soft skills required for shop or field work. Many dealers customize the assessments further for their specific needs.
ADDITIONAL SKILLS
“With lift trucks becoming so automotive-like in their electronics and functionality, dealers need technicians that have more than just traditional electronics, hydraulics or powertrain diagnostic skills,” says Dawley. “Technicians now have to be technology savvy with the ability to troubleshoot through use of computers.”
Communication with the manufacturer many times happens electronically, so technicians must be further versed in using computer applications and have strong writing skills, he adds. “Having not only a strong back but a strong mind is becoming essential for technicians in many equipment industries, and lift trucks are no different.”
CERTIFICATION PROGRAM
NMHG helps to make sure technicians perform their duties accurately by mandating that each technician enter its Technical Certification Program. For Yale, this program is called ProTech; for Hyster, it is CerTech.
“The five levels of the NMHG curriculum ensure that each technician has a process of career-long learning and growth regardless of their tenure,” says Dawley.
Starting at Maintenance Level (Level 1), new technicians learn about the basics of safety, customer care, product maintenance, basic electronics and basic hydraulics.
Once this entry-level learning path is completed, technicians enter the main body of the certification program which contains three levels: Certified, Master and Elite. Each level contains a specific amount of product-specific training and general systems training.
As technicians progress through each level, which can take one to three years depending on the technician’s aggressiveness, additional product and systems knowledge is gained. The curriculum contains both online and live training courses, as well as on-the-job training and evaluation.
“As seasoned technicians maintain the Elite level certification status, it is important that their knowledge be passed down to their peers, Dawley says.
To enable this action, NMHG has a fifth level of certification called Trainer. This is mostly live training in which factory trainers educate technicians on adult education principles, communication practices and course management.
CUSTOMER UPTIME
NMHG expects its dealers to field a specific number of trainers to technicians to ensure a ratio that will support knowledge growth locally, notes Dawley.
“Customer satisfaction is important to NMHG and both of its leading dealer networks, so we collectively agreed to make Technical Certification a mandated part of our relationship in which dealers do not get paid for warranty work unless their technician is certified to repair the piece of equipment in question,” he says.
“We believe this provides the appropriate check and balance to drive first-time fix and customer uptime.”
Ohio Technical College: A technician training ground
By Eric R. Brothers, Business Journalist
Technicians often begin their careers at a vocational training school. One such school is the Ohio Technical College (OTC) in Cleveland, OH. Founded as the Ohio Diesel Mechanics School in 1969, it has been training students in diesel equipment technology and a lot more.
OTC now offers programs in automotive, diesel, auto-diesel, CDL truck driver training, collision repair, classic car restoration, high performance and racing, alternative fuel vehicles, custom paint and graphics, power generator systems, welding, motorcycle/power sport technology and BMW service technician education. Courses, which run 12 to 18 months, feature a balance of classroom learning and real-world shop skills using the latest technology and equipment.
The school draws applicants from all over the U.S. Currently, more than 1,000 students attend classes at OTC, which employs 190 full-time staff. Maximum class size is limited to 25, but averages less, with a focus on personalized, small-group, hands-on training.
OTC’s downtown campus occupies more than a full city block. The sprawling main building can claim a unique heavy duty heritage. It once was the factory of the legendary truck maker, White Motor Co. Now, the brick structure boasts eight classrooms, numerous dedicated lab and large workshop spaces, a library, computer stations, cafeteria and a Matco Tools store that offers student discounts.
DIESEL TECHNOLOGY
While OTC’s range of automotive specialties is impressive, the foundation from which all of the current course offerings spring remains the Diesel Equipment Technology program. The 72-week course of instruction includes 1,800 hours of training; 2,100 hours to earn an Associates Degree of Applied Science.
Students learn about diesel engine performance and repair, electrical systems, drivetrains, automatic transmissions, suspension and steering systems, brake and hydraulic systems, transport refrigeration, off-road and industrial equipment maintenance.
Teaching aids include some 60 engines, ranging in size from an antique single-cylinder 2-stroke farm model to a mammoth V-16 tugboat diesel. There are Caterpillar, Detroit Diesel, International, Mack, Paccar and other on-highway engines, and even the latest Cummins ISX fitted with a diesel particulate filter.
The school has more than 22 Class 8 tractors, light and medium duty straight trucks, plus five dry vans, to provide real-world repair experience.
Ben Maddox, the director of diesel at OTC for 22 years, oversees all diesel instruction. During a recent tour given exclusively to Fleet Maintenance, he pointed out some showcase features of the shop. One is the Roadranger Academy - a dedicated classroom equipped with an assortment of 20 Eaton Fuller transmissions, ranging from older manual models up through today’s automatic manuals, that serve as training aids.
In three weeks of intensive training at the Academy, students practice disassembly, reassembly and diagnostics on these transmissions. Perfect attendance and grades averaging 85 percent are required to earn certification, said Maddox.
Another distinctive area is set aside for transport refrigeration unit (TRU) maintenance and repair. More than a dozen units provided by OTC’s partners Carrier Transicold and Thermo King give students experience working on a variety of TRU models.
Instruction at OTC is not always about classroom study and working on vehicles and components, noted Mike Manocchio, advanced diesel instructor. “Students also learn life skills, such as the discipline of the workplace, punching a time clock, managing their time, the importance of teamwork and working from actual repair orders.”
FULL ACCREDITATION
Recognized by the Accrediting Commission of Career Schools and Colleges of Technology (ACCSCT), OTC is certified by the National Institute for Automotive Service Excellence/National Automotive Technicians Education Foundation, American Trucking Associations, Automotive Service Association (ASA) and National Alternative Fuel Training Consortium. As such, all financial aid - grants, loans, scholarships and even the GI Bill - can be applied to the school.
Depending on which program a student graduates from, OTC boasts job placement between 80 and 95 percent.
The goal of OTC - family-owned by the third-generation descendants of its founder, Julius Brenner - is to remain on the cutting edge of future technology and deliver the necessary technical and career skills to keep its graduates well equipped for the industry, said Jordan Brenner, the school’s director of enrollment.
About the Author
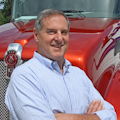